Manufacturing is a complex dance of machines, people, and processes working together to create the products we use every day. In this intricate dance, there are moments when the music stops – these are called downtimes. Downtimes can be planned, like when a factory takes a breather for maintenance, or they can be surprises, such as a machine deciding to take an unplanned break.
Now, why does it matter if machines take a break? Well, that's what we're here to unravel. In this blog post, we'll explore planned and unplanned downtime in manufacturing and how these interruptions can significantly impact factories' results.
Imagine you're baking your favourite cake, and suddenly the oven stops working – that's a bit like unplanned downtime. Or, think about when you plan a day off to clean and organise your house – that's more like planned downtime. In manufacturing, these pauses in production can affect not only the quantity of products made but also the quality and the overall success of the business.
So, grab a cup of coffee or tea. Let's journey into the world of manufacturing downtime, exploring why it matters, how it happens, and what manufacturers can do to keep the music playing smoothly in their production dance.
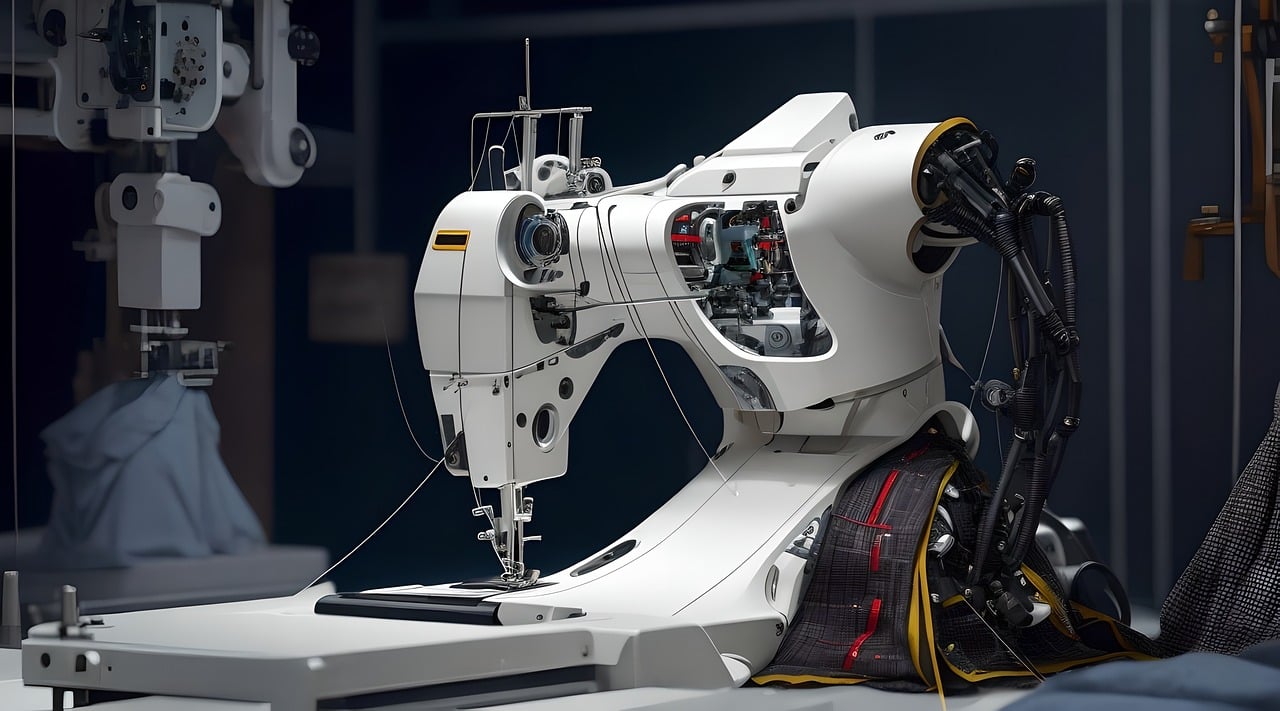
The Difference Between Planned and Unplanned Downtime
Okay, let's break it down – planned downtime is like when you schedule a break for your favourite TV show, and unplanned downtime is when your internet suddenly decides to go on vacation in the middle of that exciting episode.
Planned Downtime: Taking a Scheduled Breather
Scheduled Maintenance and Upgrades |
Just like your car needs a check-up, machines and equipment in factories need some tender loving care, too. Planned downtime happens when factories pause scheduled maintenance and upgrades. |
Picture this: you plan a day to give your car a tune-up to keep it running smoothly. Factories do the same—they schedule breaks to ensure all their machines are in top-notch shape. |
|
Production Line Adjustments and Retooling |
Imagine you're an artist switching from drawing to painting – you need a bit of time to set up your paints and brushes. Similarly, factories might pause to adjust their production lines or change tools to make new and exciting products. |
Planned downtime here is like the intermission in a play – a deliberate pause to set the stage for the next act. |
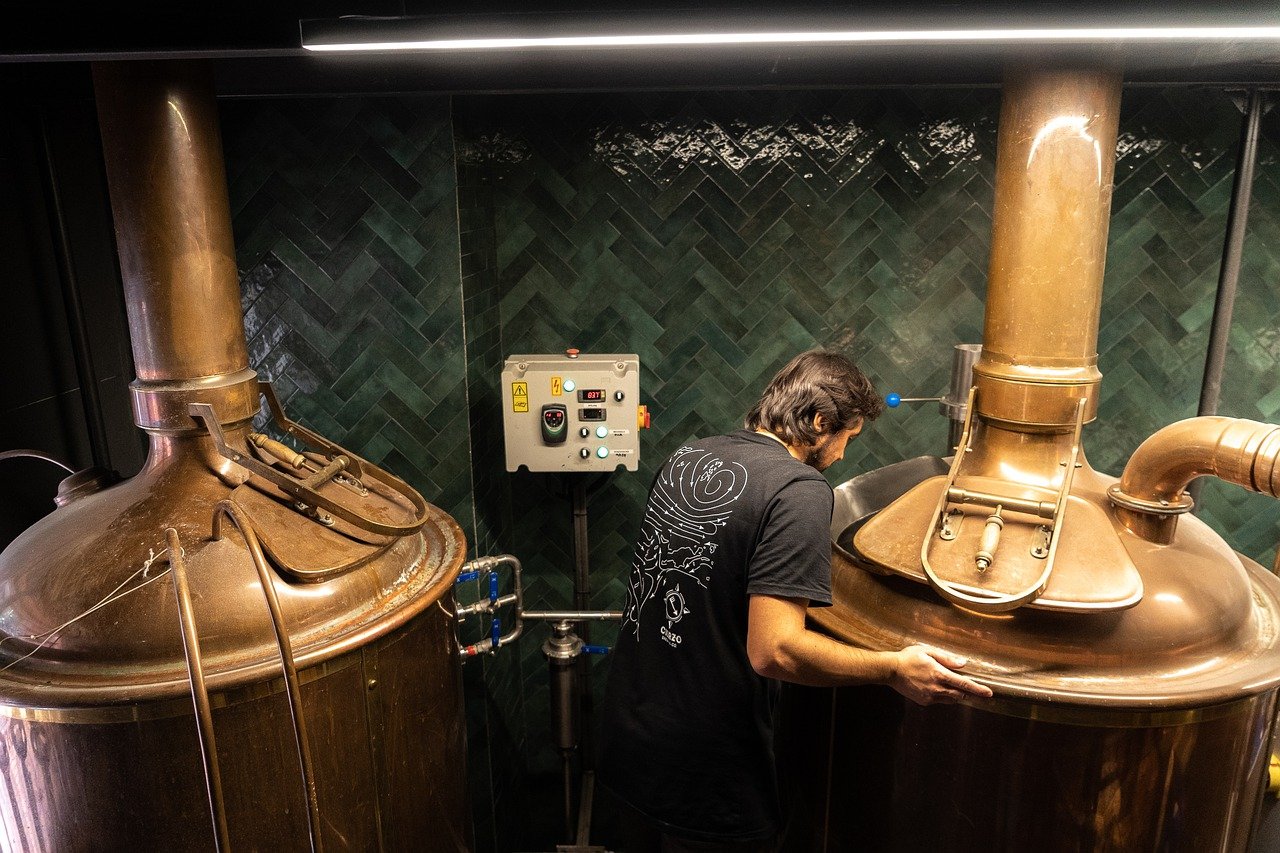
Unplanned Downtime: Unexpected Interruptions
Equipment Failures and Breakdowns |
Now, think about your computer suddenly freezing when you're in the middle of something important. Unplanned downtime in manufacturing is a bit like that—unexpected equipment failures and breakdowns that bring production to a sudden halt. |
It's like when your favourite pen stops working, leaving you in the middle of a sentence. In a factory, a machine deciding to take an unscheduled break can be a showstopper. |
|
Supply Chain Disruptions |
Imagine planning a surprise party, but the cake delivery gets delayed. Unplanned downtime in manufacturing can be caused by disruptions in the supply chain – like when the ingredients for your favourite recipe don't arrive on time. |
It's a bit like expecting a package on a certain day, and it doesn't show up. In manufacturing, delays in getting the necessary materials can lead to unexpected pauses in production. |
Plan downtime is like pressing pause on purpose, while unplanned downtime is when the pause button is hit unexpectedly. Both can impact the manufacturing stage, and we'll soon explore why managing these pauses is crucial for keeping the production dance in full swing.
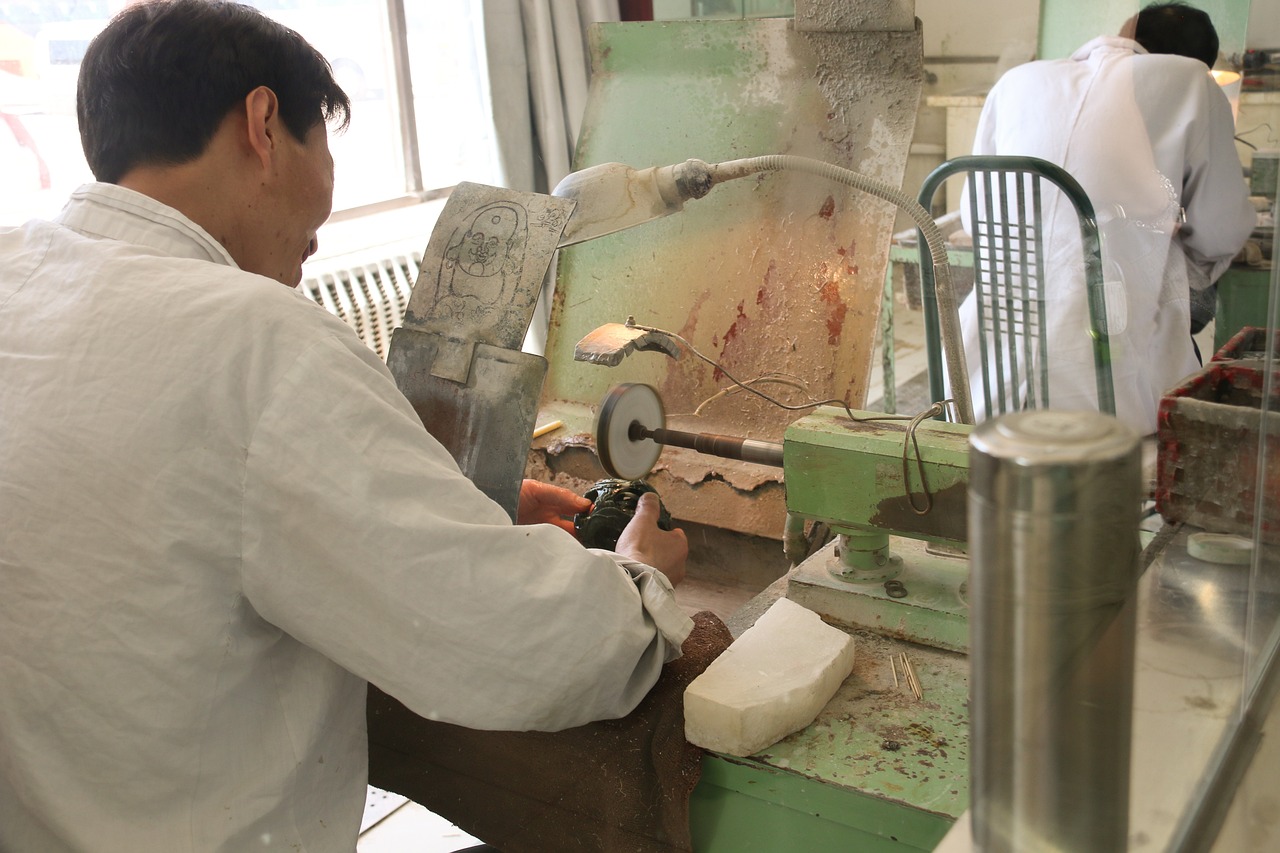
The Cost of Downtime
Alright, let's talk about the price tag that comes with those unplanned pauses and scheduled breaks in the manufacturing world. It's a bit like when your favourite ice cream melts – not so sweet. So, why does downtime cost so much?
Financial Implications of Downtime
Lost Production and Revenue |
Imagine a lemonade stand on a hot day, but suddenly, the lemon squeezer decides to take a break. That's a bit like what happens in manufacturing when machines stop – no products get made, and the money-making slows down. |
Lost production means lost money. When factories can't make things, they can't sell them either, and that hits them right in the wallet. |
|
Increased Maintenance and Repair Costs |
Think about your bike – if you ignore that strange noise, it might lead to a bigger problem. In factories, ignoring maintenance needs during downtime can result in bigger and more expensive issues later. |
Just like a stitch in time saves nine, spending a little on maintenance during planned downtime can prevent hefty repair bills later on. |

Non-Financial Consequences
Damage to Brand Reputation |
Imagine telling your friends about a cool new gadget, but it breaks down the first time they use it. In manufacturing, if products have issues due to downtime, it can damage the company's reputation. |
Customers want products that work like they're supposed to. If downtime leads to faulty goods, people might start looking elsewhere for their favourite stuff. |
|
Negative Effects on Customer Relationships |
Think about waiting for a pizza delivery that never arrives – frustrating, right? In manufacturing, delayed deliveries due to unplanned downtime can upset customers and strain relationships. |
Businesses rely on happy customers. If they can deliver on time, it can lead to satisfied customers who might not choose their products in the future. |
In summary, downtime isn't just a pause in production – it's a costly intermission. It affects both the money in the bank and the way people see and trust a company. Now that we've peeked into the wallet-wincing side of downtime let's explore how manufacturers can take steps to keep the production stage well-lit and the cash register ringing.
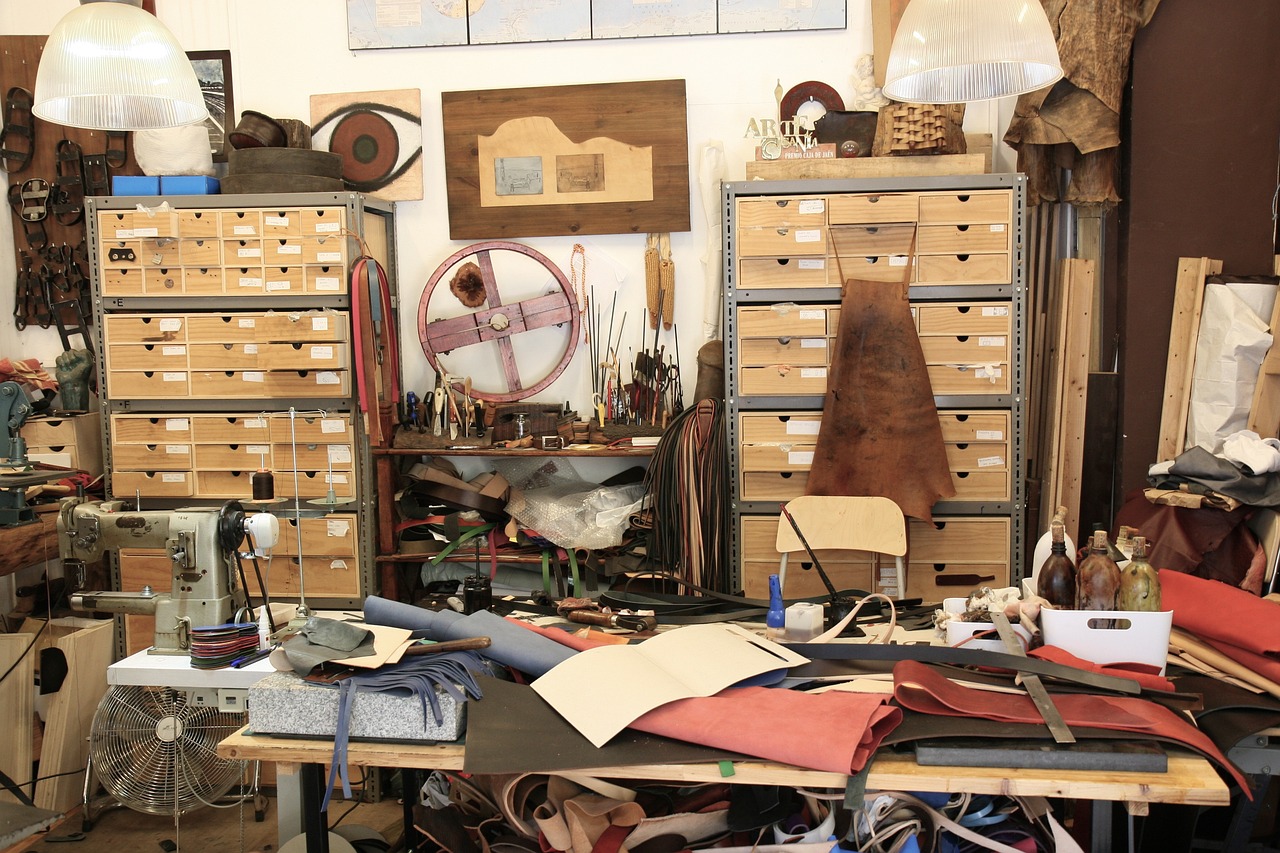
Strategies for Minimizing Downtime
Alright, now that we've seen the not-so-fun side of downtime, let's dive into the game plan to keep those interruptions to a minimum. It's a bit like preparing for a smooth road trip – you check your car, have a spare tyre, and maybe even a GPS. Similarly, factories have strategies to navigate the bumpy terrain of downtime.
Proactive Maintenance Practices
Predictive Maintenance Using Technology |
Imagine your phone telling you it's time for an update before it starts acting weird. In factories, technology can predict when machines might need a break for maintenance before they cause trouble. |
Predictive maintenance is like having a crystal ball that helps factories fix things before they break, keeping the production line flowing smoothly. |
|
Routine Inspections and Preventive Measures |
Think about going to the doctor for a check-up – it's to catch potential issues before they become big problems. In manufacturing, routine inspections and preventive measures help catch glitches before they turn into full-blown breakdowns. |
It's a bit like tightening a loose screw before it falls out. Regular check-ups keep everything in working order. |
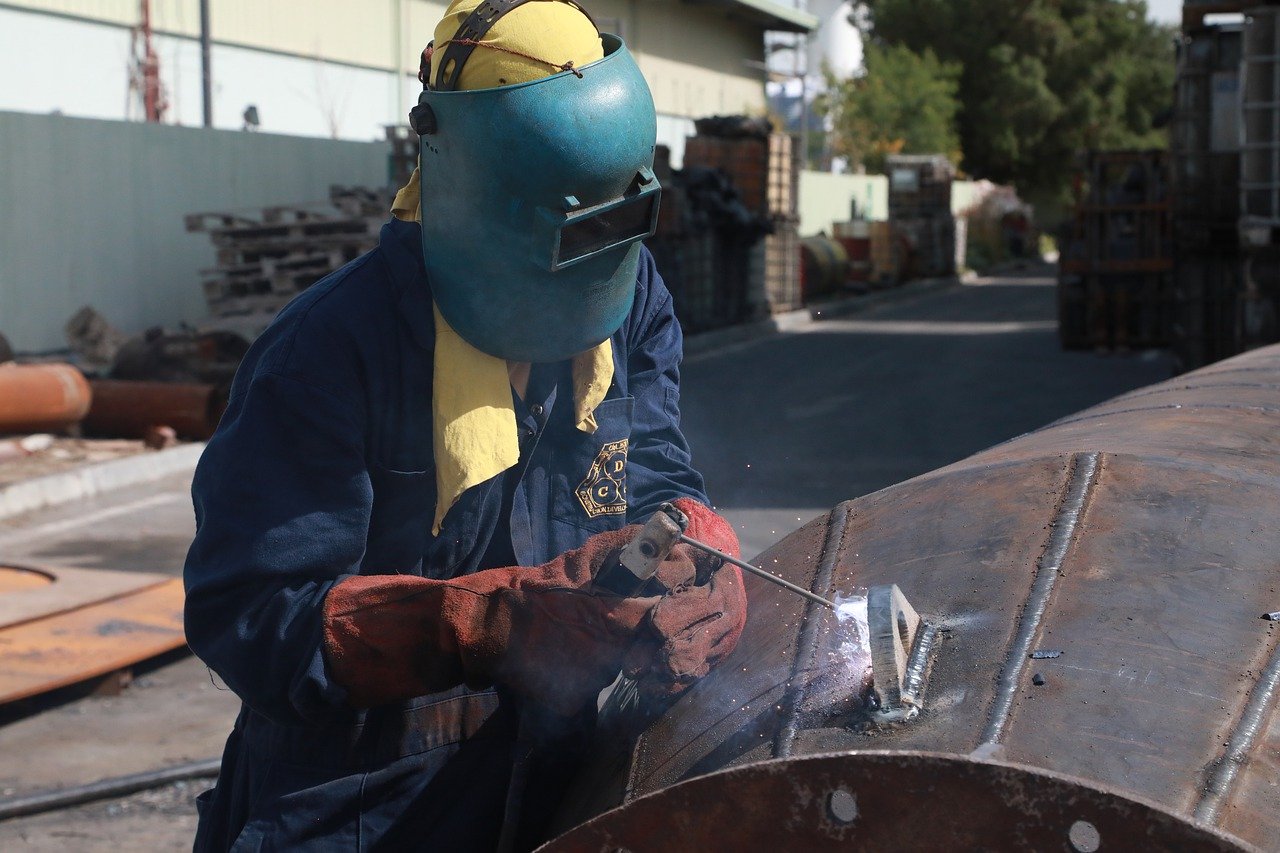
Efficient Supply Chain Management
Inventory Optimization |
Picture this: you're making a sandwich, and you realise you're out of cheese. In manufacturing, having a well-managed inventory is like making sure you always have enough cheese – or materials – to keep the production sandwich going. |
By optimising inventory, factories can avoid unplanned downtime caused by running out of essential materials. |
|
Supplier Relationship Management |
Imagine having a reliable friend who always shares their snacks with you. In manufacturing, having good relationships with suppliers is like having dependable friends who deliver materials on time. |
Strong connections with suppliers mean a steady flow of materials, reducing the risk of unexpected pauses in production. |
Employee Training and Engagement
Empowering Staff to Identify and Address Issues Promptly |
Think about being the superhero of your own story – employees in manufacturing can be the heroes, too. By empowering them to spot and address issues early, they become the first line of defence against downtime villains. |
It's like giving everyone a superhero cape to keep an eye on the production city. |
|
Continuous Improvement Culture |
Imagine a garden that's always growing and getting better. In manufacturing, fostering a culture of constant improvement means always looking for ways to do things better and more efficiently. |
It's about learning from past experiences and finding ways to make the production process smoother each time. |
In essence, minimising downtime is like preparing for a smooth journey – it takes planning, technology, good relationships, and a team that's always ready to tackle challenges. By implementing these strategies, factories can aim for a production stage that's more like a well-choreographed dance and less like a series of unexpected pauses.
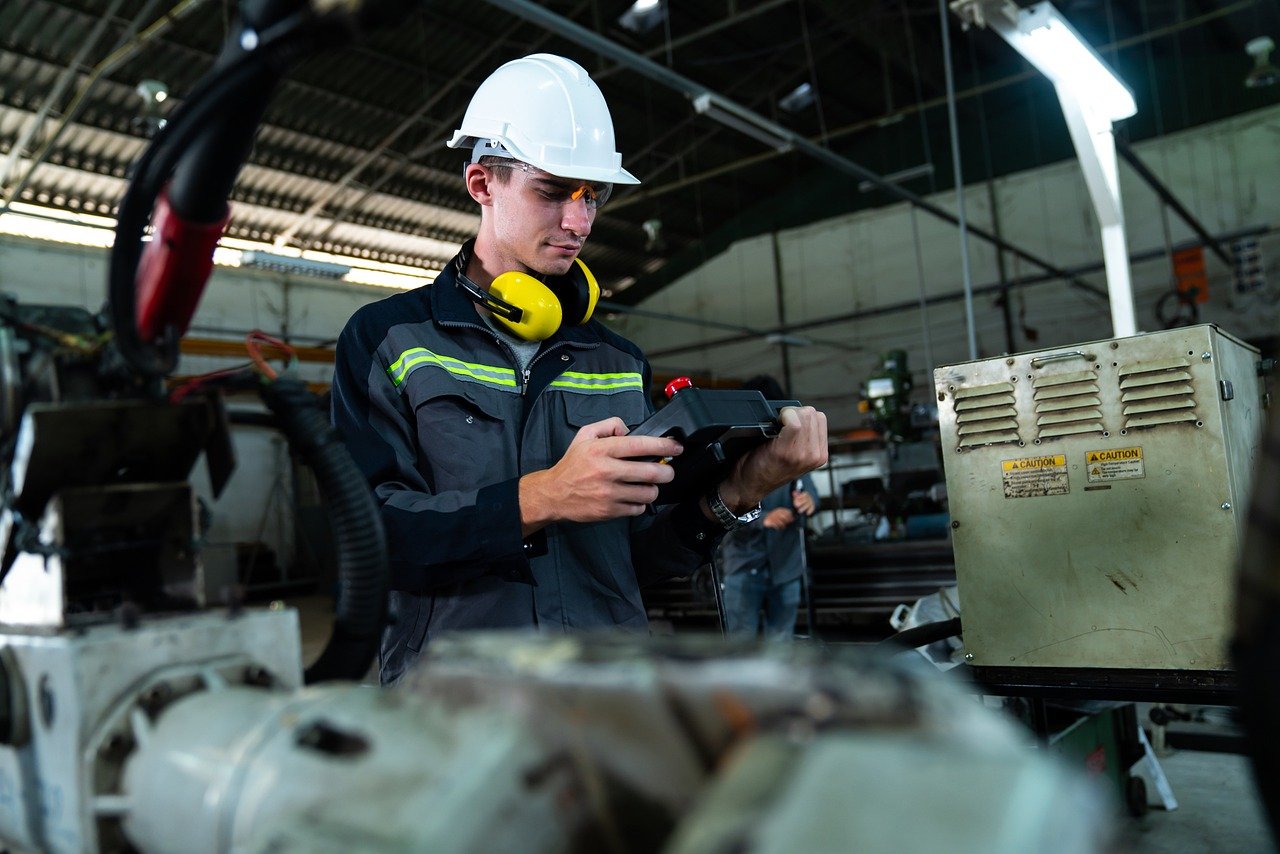
Technology and Innovation in Downtime Reduction
Now, let's explore the superhero gadgets and magic spells that technology brings to the world of minimising downtime. It's a bit like upgrading from an old flip phone to a fancy smartphone – suddenly, you have tools that can do amazing things. In manufacturing, technology plays a crucial role in keeping the production party going smoothly.
Role of Industry 4.0 in Minimizing Downtime
IoT Sensors for Real-Time Monitoring |
Imagine having tiny detectives on your machines, constantly monitoring everything. In manufacturing, Internet of Things (IoT) sensors act like detectives, providing real-time data on machines' health and performance. |
With these sensors, factories can detect issues before they become big problems, ensuring a production line that runs like a well-oiled machine. |
|
Predictive Analytics for Proactive Decision-Making |
Think about a weather forecast telling you it might rain tomorrow – in manufacturing, predictive analytics is like having a forecast for machine health. By analysing past data, factories can predict when a machine might need a break for maintenance. |
It's a bit like being prepared with an umbrella before the rain starts. Predictive analytics helps factories make decisions before issues pour in. |
Integration of Artificial Intelligence and Machine Learning
Predictive Maintenance Algorithms |
Picture this: a smart assistant that knows when your favourite show is about to air and reminds you to grab your popcorn. In manufacturing, predictive maintenance algorithms are like smart assistants, predicting when machines might need attention. |
These algorithms learn from patterns, making them smarter over time and helping factories plan maintenance breaks when it makes the most sense. |
|
Advanced Production Planning and Scheduling Systems |
Imagine planning a big family dinner with multiple dishes – you need a schedule to make sure everything is ready at the same time. In manufacturing, advanced production planning and scheduling systems create efficient schedules for machines and workers. |
It's like having a well-organized recipe for success, ensuring that different parts of the production process work together seamlessly. |
In a nutshell, technology is the superhero cape that factories wear to battle downtime monsters. With real-time monitoring, predictive analytics, and smart algorithms, manufacturers can transform their production process into a high-tech dance where every move is carefully orchestrated. The integration of Industry 4.0 technologies not only reduces downtime but also opens doors to a more efficient and futuristic manufacturing world.
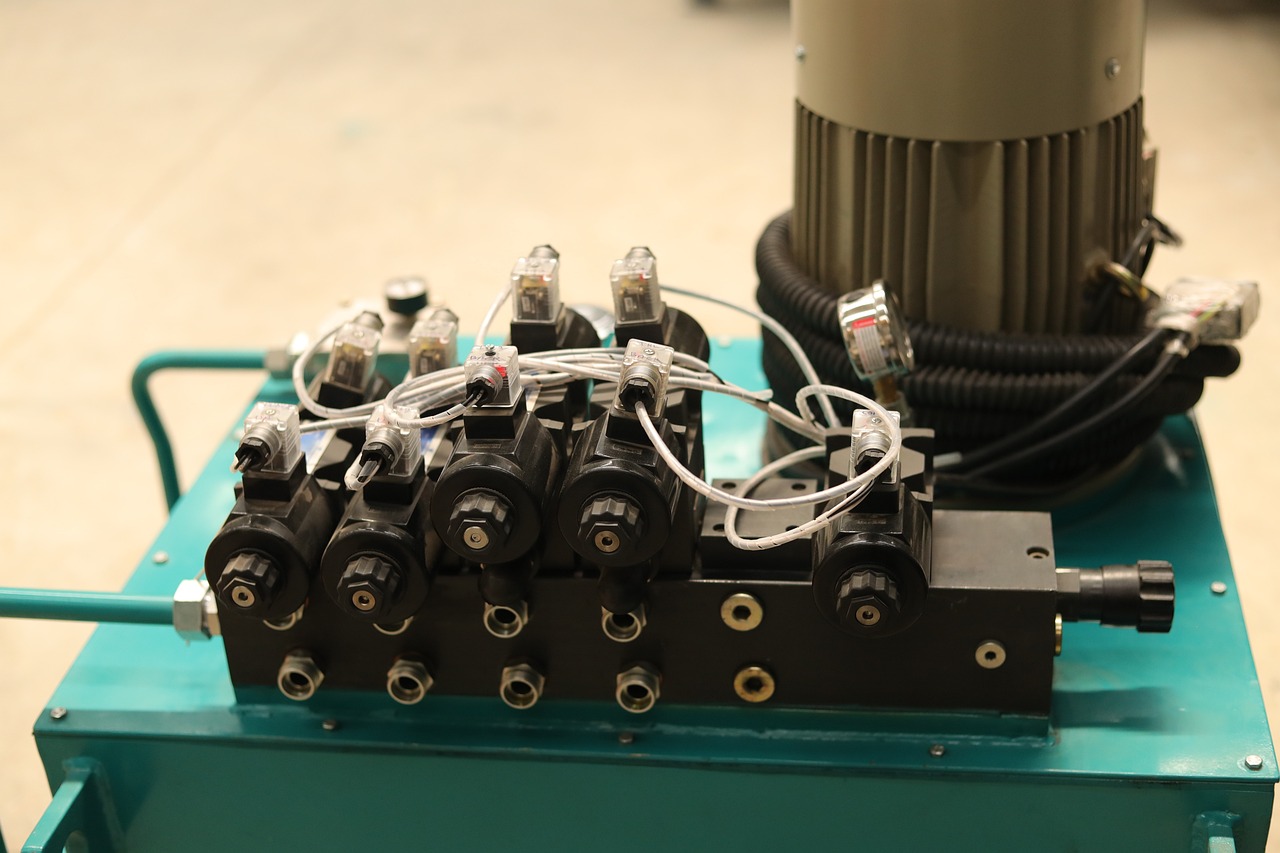
Recap of the Importance of Managing Downtime
Alright, we've taken a deep dive into the world of planned and unplanned downtime in manufacturing. It's a bit like exploring a big puzzle – we've looked at the pieces, seen how they fit together, and discovered why it matters. Now, let's wrap it up like a good book with a satisfying ending.
Planned Downtime vs. Unplanned Downtime |
We learned that planned downtime is like pressing pause on purpose, giving factories a chance to tune up their machines or make changes. On the flip side, unplanned downtime is like an unexpected intermission, causing interruptions that nobody likes. |
The Cost of Downtime |
We explored the wallet-wincing side of downtime, seeing how it can cost factories not just money but also their reputation and customer relationships. |
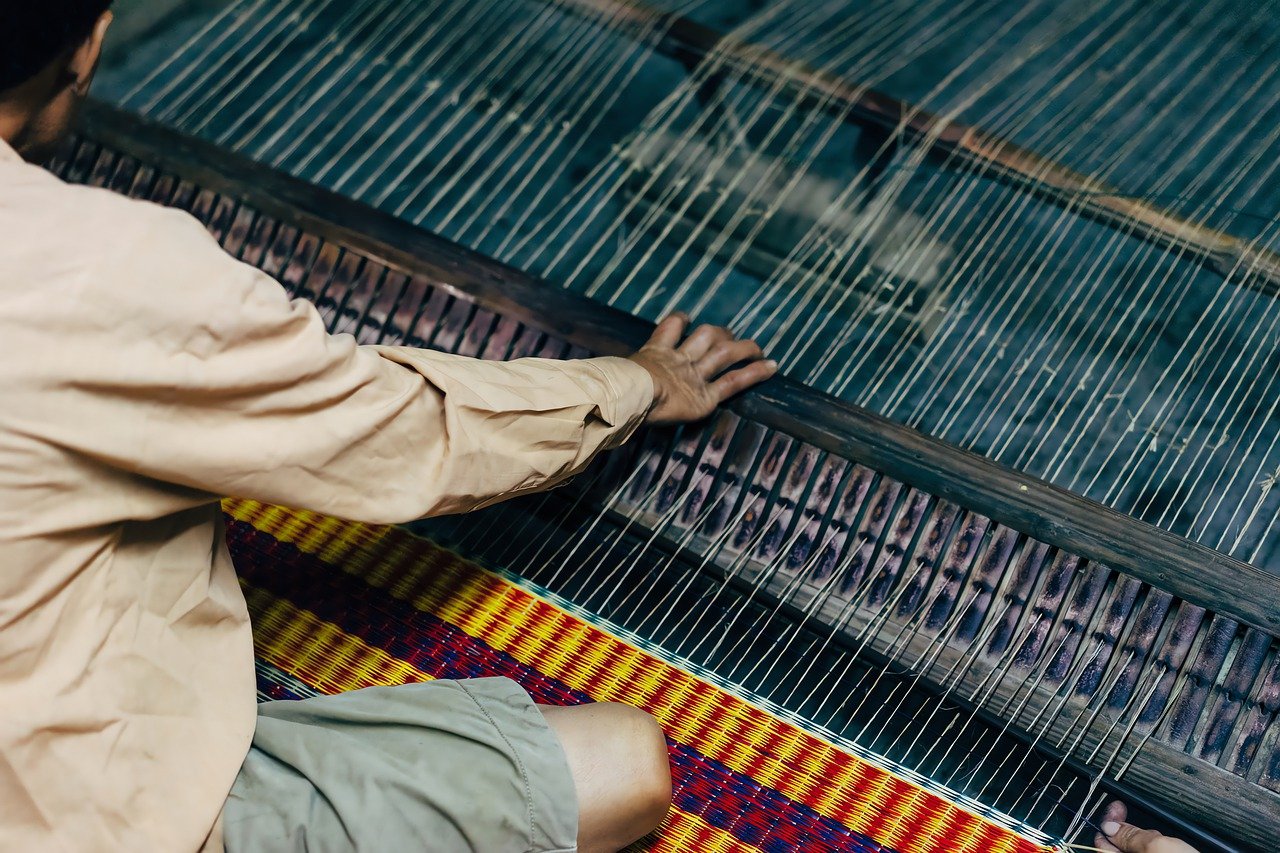
Call to Action for Manufacturers
Strategies for Minimizing Downtime |
We discussed strategies like proactive maintenance, efficient supply chain management, and employee empowerment—all geared towards keeping the production dance in full swing. |
Technology and Innovation |
We unveiled the superhero gadgets of Industry 4.0, from IoT sensors to predictive analytics and smart algorithms, showing how technology can be a mighty tool in the fight against downtime. |
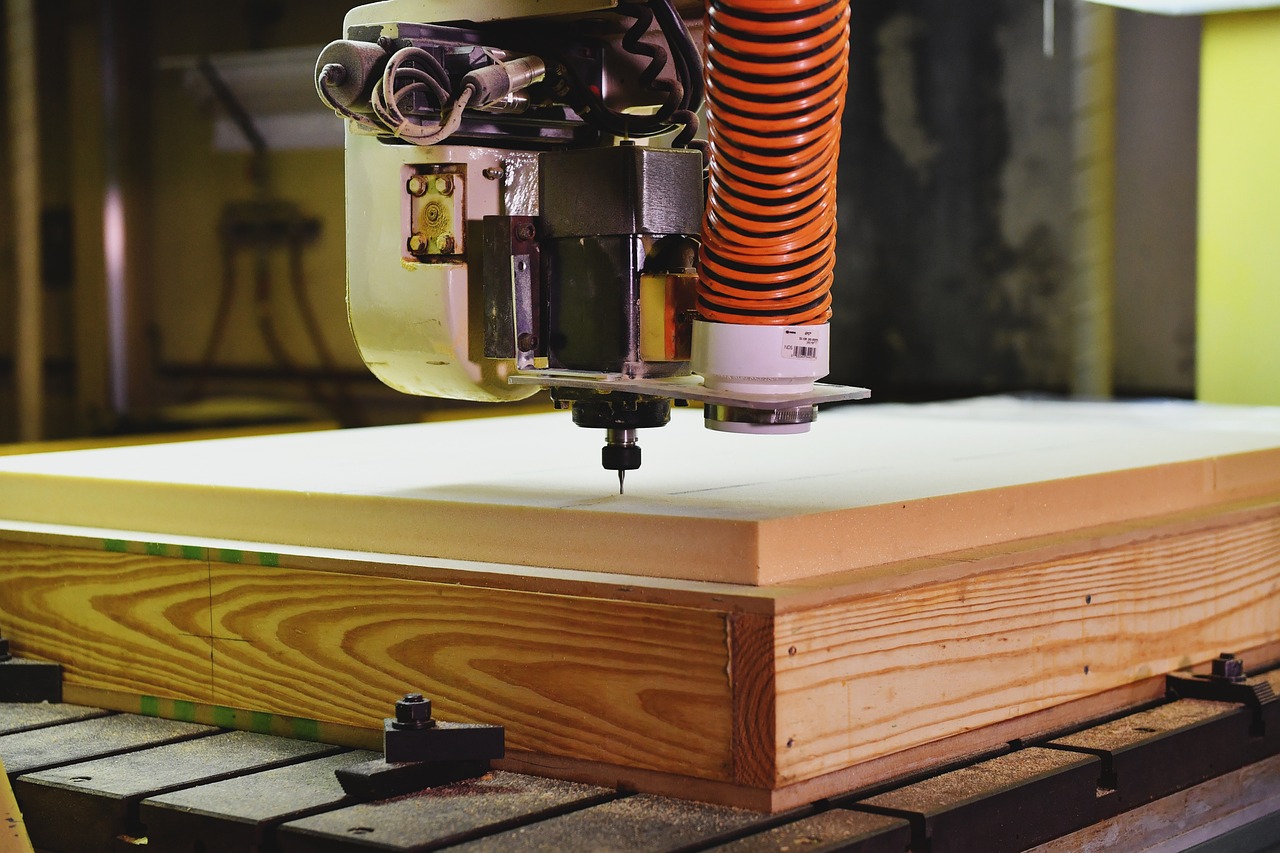
Future of Downtime Management
Continuous Improvement |
We wrapped up by emphasising the importance of a continuous improvement culture. With this mindset, factories are always looking for ways to make their production process smoother and more efficient. |
Looking to the Future |
The journey continues. As technology continues to advance and manufacturers embrace innovative strategies, the future holds exciting possibilities for even more streamlined and efficient production. |
In the grand finale, it's clear that managing downtime isn't just a task for factories – it's a strategic dance where every move counts. By implementing smart strategies, embracing technology, and fostering a culture of improvement, manufacturers can not only minimise downtime but also create a future where the production stage is a well-choreographed performance, dazzling audiences with its efficiency and success. So, let the manufacturing show go on!
Comments
No comments yet!Add a Comment
You must be logged in to post a comment.