Discover the success story of Iwoscan, where the focus is on enhancing production lines and mitigating defects in manufacturing processes. This use case highlights how Iwoscan brings about a remarkable 90% reduction in unfinished orders, seamless optimisation throughout the manufacturing journey—particularly in final stages like assembly and packaging—a substantial decrease in downtime, and a heightened 50-80% clarity regarding order progress and estimated completion times.
Addressing Manufacturing Challenges with Iwoscan
When faced with the challenging scenario of a disorganised production pipeline and a workforce navigating a complex workflow, the leading manufacturer in Lithuania sought the expertise of Iwoscan. Recognising that Iwoscan held the key to the solution, the focus shifted to understanding the specific challenges within the manufacturing line.
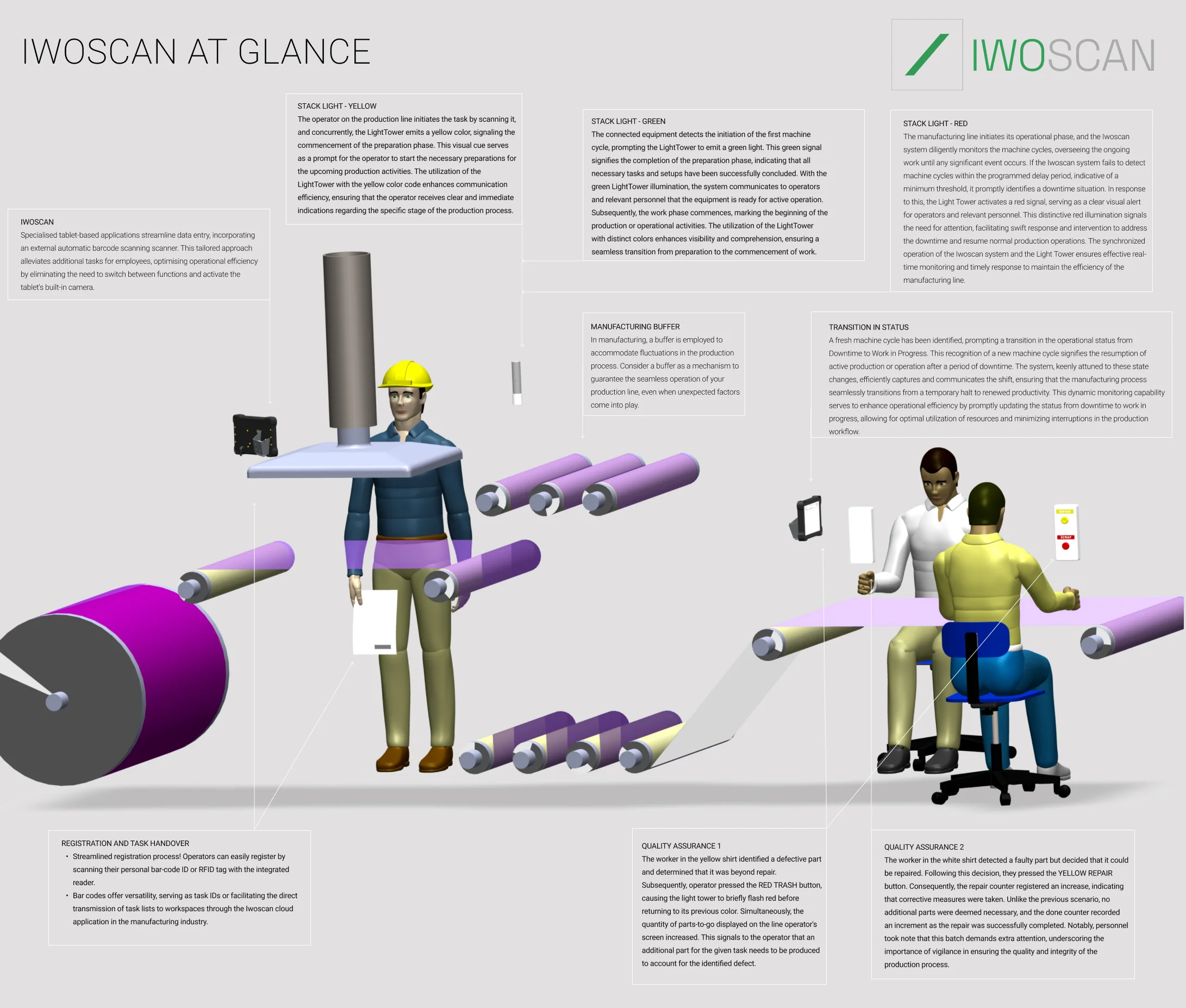
These challenges could be categorised into three interrelated issues. The client encountered a significant problem in the manufacturing process, characterised by unplanned machine restarts on the production lines.
I problem
Unintended restarts resulted in numerous inefficiencies, production defects, waste, and financial losses. This translated to heightened manufacturing costs, disengaged teams, and a negative return on investment (ROI).
II problem
Additionally, every rearrangement of the manufacturing line had a cascading effect on other processes. Operators from different production lines had to intervene when a line stopped, disrupting not just one but multiple manufacturing lines. This approach contradicted the principles of lean manufacturing.
III problem
The third challenge was related to defect identification. In continuous manufacturing processes, defects occurring midway through the process often go unnoticed by operators at the beginning of the manufacturing line. This lack of awareness, whether determined or undetermined, could result in unfinished orders due to the absence of data on process flaws.
The manufacturing lines faced complications due to numerous distinct stages, leading to inaccuracies and an increased risk of defects. While buffering areas were traditionally employed to mitigate these risks, their effectiveness could have been improved due to the complexity and elongated nature of the production process. Consequently, implementing a solution like Iwoscan became imperative for identifying defects mid-process and promptly disseminating this knowledge across the manufacturing line to empower operators in adjusting their inputs for optimal efficiency.
Iwoscan's Manufacturing Solution in Action
Efficiently addressing the manufacturing challenges, our team seamlessly integrated Iwoscan devices with every machinery piece in the factory, swiftly transforming operational chaos into a well-coordinated efficiency. The integration process, typically completed within a week (though varying based on case complexity), represented the culmination of our on-site intervention. Iwoscan's robust durability emerged as the linchpin, ensuring a failure-free implementation.
In practical terms, Iwoscan played a pivotal role in identifying defects mid-process. This timely identification empowered the gatekeeper or Quality Assurance (QA) operator to communicate promptly with their colleague at the beginning of the manufacturing line. Adjustments to instructions or quantities of materials could then be made proactively. Simultaneously, the QA operator could make informed decisions regarding the defective product's fate, considering options such as reusing it in other production lines for sustainability or incorporating it into different production stages.
Facilitating the circulation of critical knowledge stands as a cornerstone in achieving performance excellence in manufacturing and bolstering return on investment (ROI). It's important to note that the capabilities of Iwoscan extend far beyond this scenario, offering a comprehensive toolkit for enhancing overall manufacturing performance.
Iwoscan's Impact on Manufacturing Operations
Witness the transformative effects as Iwoscan integrates with machinery and tablets, facilitating the smooth flow of raw data to the factory's core—the accounting system. The benefits are far-reaching, offering a comprehensive overview of the manufacturing pipeline, the ability to pinpoint bottlenecks, and real-time tracking of orders. Iwoscan's integration also streamlines onboarding processes, eliminates human errors, and unveils cost savings, empowering workers who hold the universe in their palms through tablets connected to Iwoscan.
Our commitment goes beyond mere words; we substantiate it with quantifiable results. Specifically, we assure a substantial 90% reduction in unfinished or orders requiring additional corrections. Our guarantee extends to flawless optimisation of the entire manufacturing process, particularly in critical stages like assembly and packaging. Experience a significant decrease in downtime, resulting in the shortened duration from product pureeing to its handover to the customer. Furthermore, it benefits from a heightened 50-80% clarity regarding an order's position in the production process and a reasonably accurate prediction of its completion timeline. Iwoscan delivers tangible improvements backed by concrete metrics, ensuring a robust enhancement in manufacturing efficiency.
Iwoscan Operational Workflow in Manufacturing
Discover the intricacies of the Iwoscan solution tailored for continuous production in the manufacturing industry. Specialised tablet-based applications streamline data entry, incorporating an external automatic barcode scanning scanner. This tailored approach alleviates additional tasks for employees, optimising operational efficiency by eliminating the need to switch between functions and activate the tablet's built-in camera. Now, let's delve into the precise workings of Iwoscan in manufacturing processes.
Connection to the Manufacturing Line. Iwoscan is seamlessly integrated into the manufacturing line.
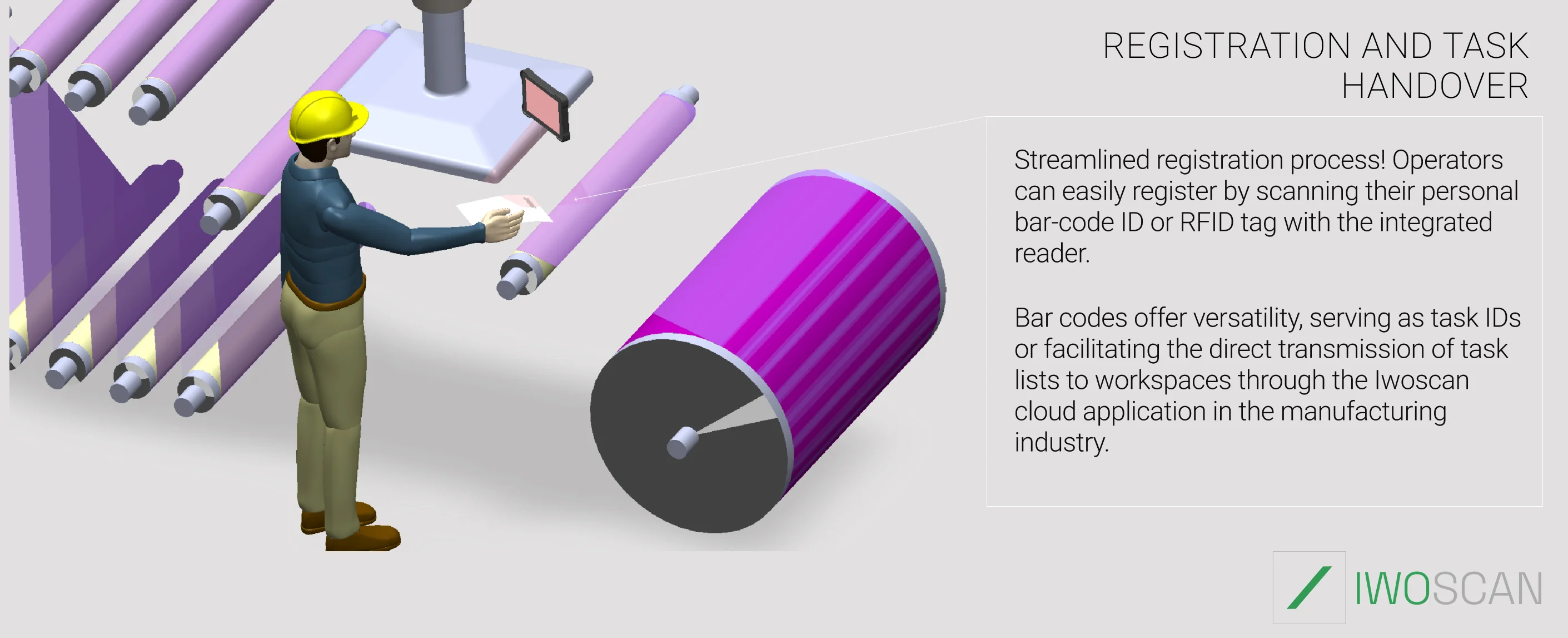
Primary Product/Raw Material Integration. It starts with entering the primary product or raw material into the production flow.
Error Detection in Sequential Phases. Throughout the sequential phases, any potential errors are noticed or discovered.
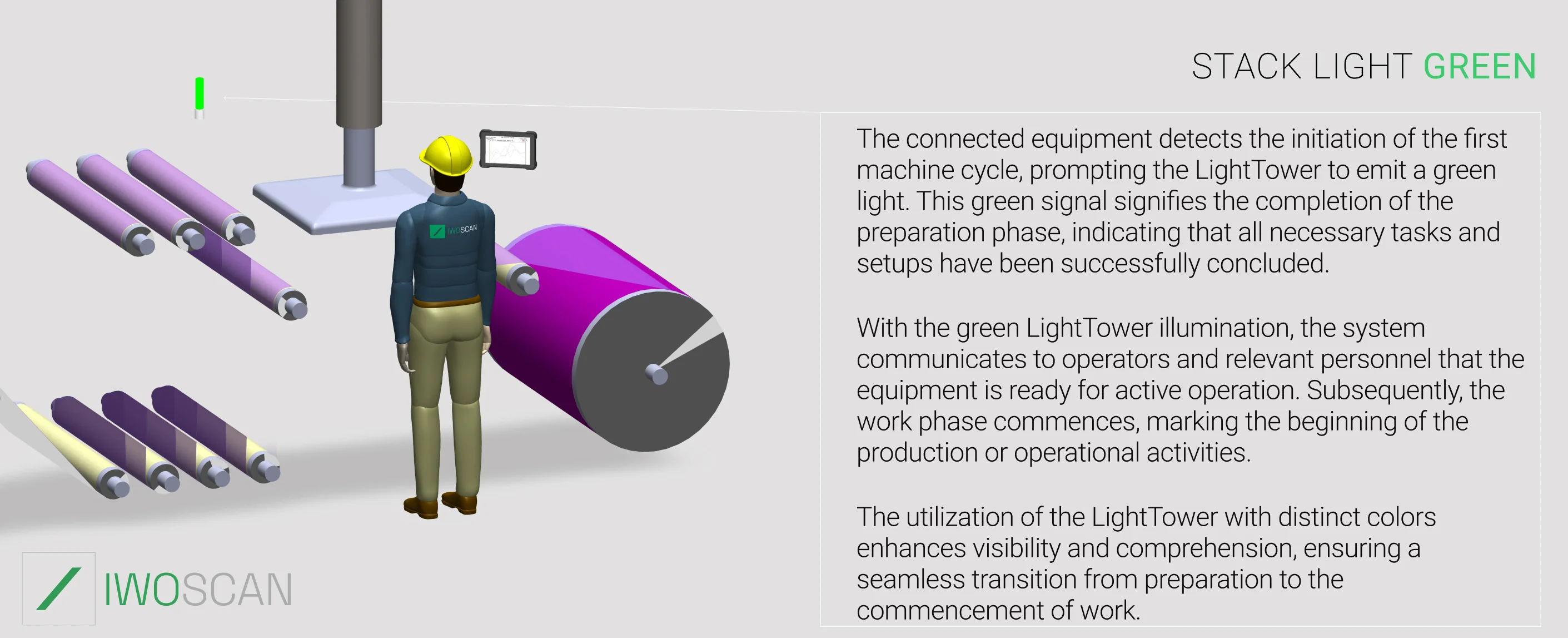
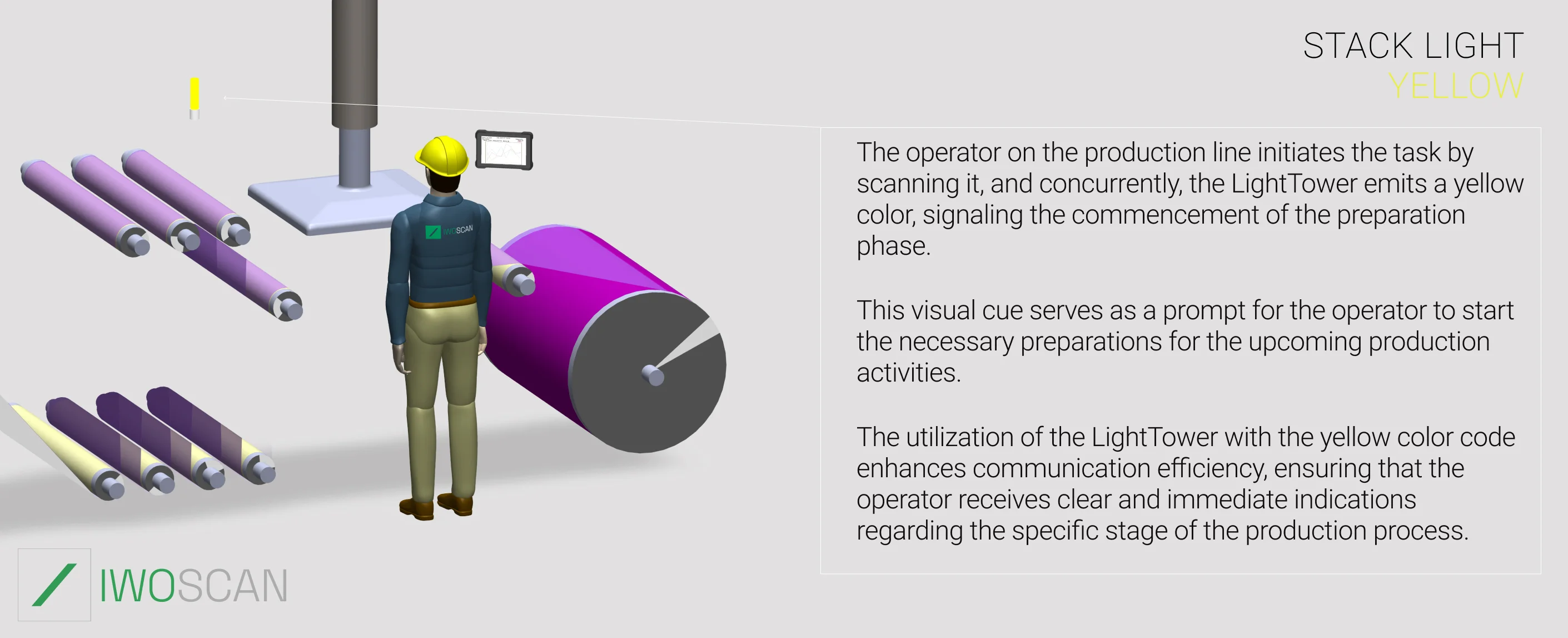
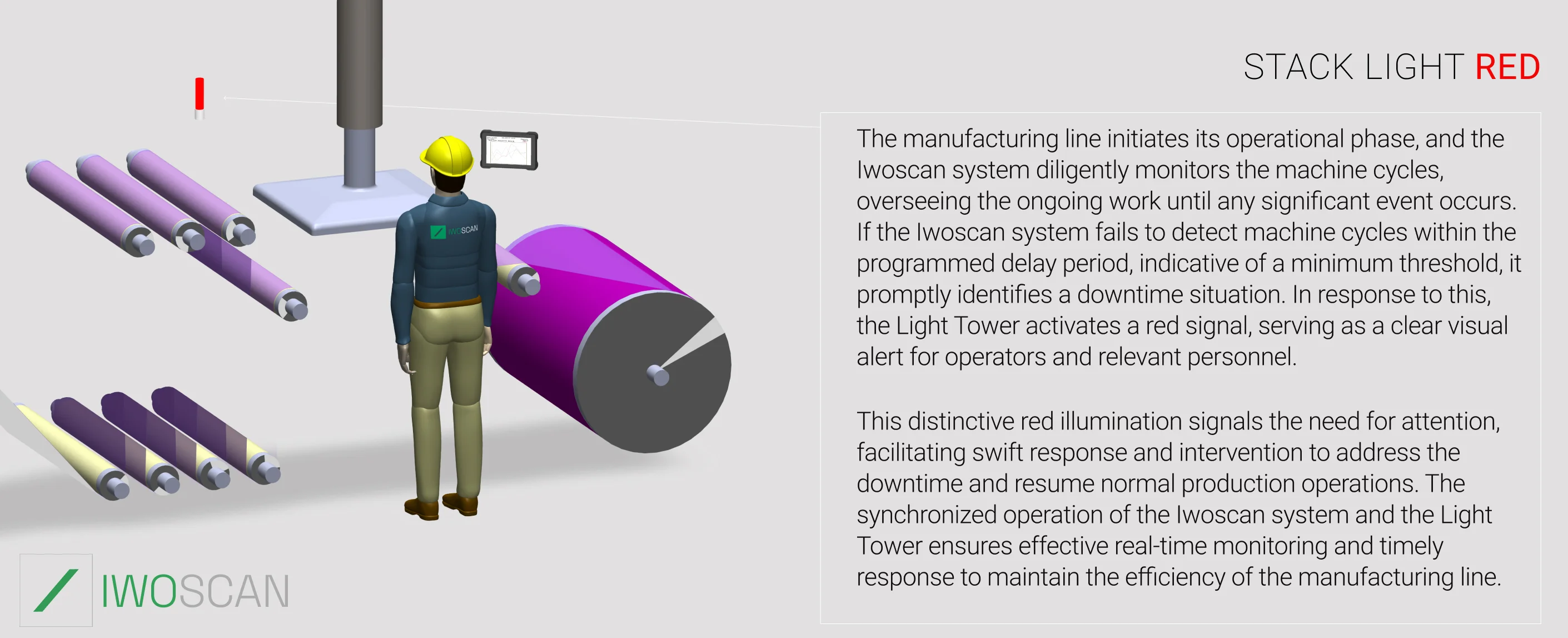
Operator Decision-Making. The operator plays a crucial role in deciding the nature of the defect. Whether it is irreparably damaged, can be remanufactured by restarting the process, or can be repurposed for another order. Once the decision is made, the operator communicates this information to the start of the production line, indicating the need for additional products to complete the order.
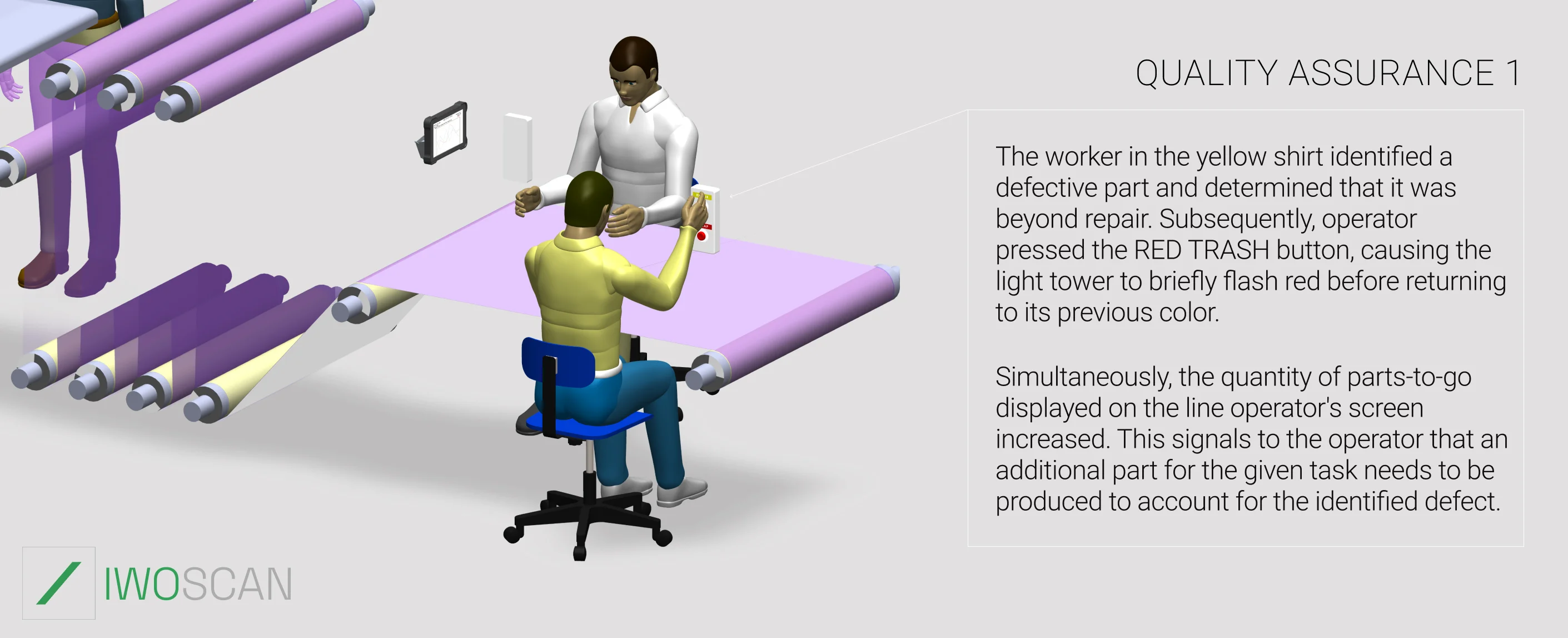
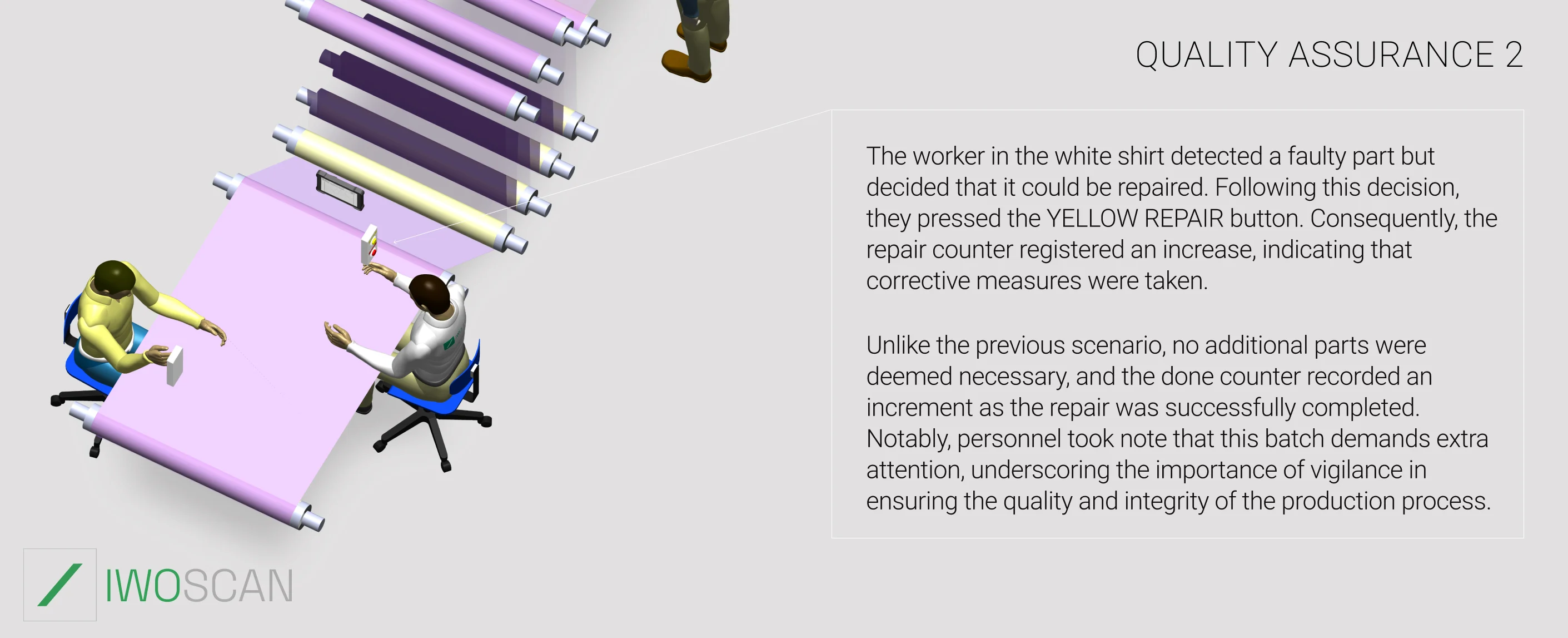
The climax of this process is the barcode scanning, unleashing a cascade of insights onto the tablet. Customised data seamlessly flows into the factory's accounting system, showcasing Iwoscan's adaptability even with manual machinery, enriching the management database. The result is breathtaking—streamlined part ordering, optimised purchases, and a comprehensive view of the factory's operational heartbeat. Iwoscan's connectivity to CNC centres also unveils Overall Equipment Effectiveness (OEE), culminating in a symphony of success where the initial chaos is transformed into a masterpiece of craftsmanship.
Critical Insights from Collaborative Endeavors in Manufacturing
Throughout our collaborative journey, we've uncovered pivotal revelations that have reshaped our approach. Firstly, Iwoscan played a pivotal role in enhancing the efficiency of the manufacturing line, refining task flows, optimising purchase processes, and providing a comprehensive overview of the factory's operational pulse. This collaboration also revealed the newfound capabilities of connected CNC centres, leading to substantial improvements in Overall Equipment Effectiveness (OEE).
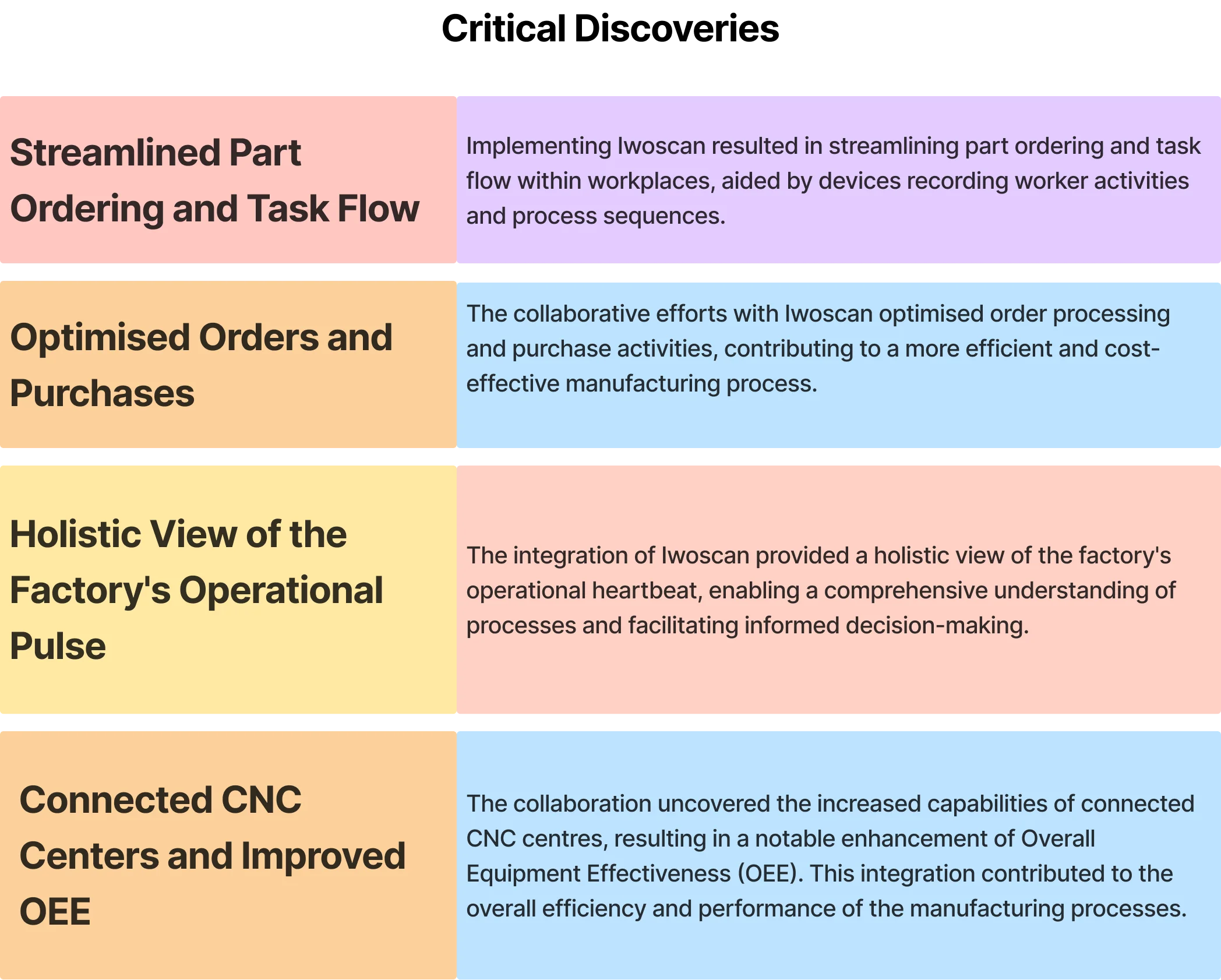
These critical insights underscore the transformative impact of our collaborative efforts, emphasising the multifaceted benefits that Iwoscan brings to the manufacturing industry.
Comments
No comments yet!Add a Comment
You must be logged in to post a comment.