Quality control and assurance are pivotal in the manufacturing industry, ensuring that products meet the highest standards of excellence. A well-implemented Quality Management System (QMS) is the cornerstone of successful quality management. In fact, according to a recent survey, companies with robust QMS report a 25% increase in product quality and a 20% reduction in defects, directly impacting their bottom line.
Why Quality Management Systems Matter
As businesses navigate the complexities of global markets and heightened consumer expectations, the need for robust frameworks to ensure product and service quality has never been more pronounced. This exploration delves into the fundamental reasons why Quality Management Systems matter, examining how these systems not only elevate the standards of deliverables but also contribute significantly to overall efficiency, risk mitigation, and the cultivation of a culture committed to continuous improvement. Understanding the profound significance of QMS is integral to fostering a resilient and customer-centric approach that is indispensable for sustained competitiveness and success in today's dynamic business environment.
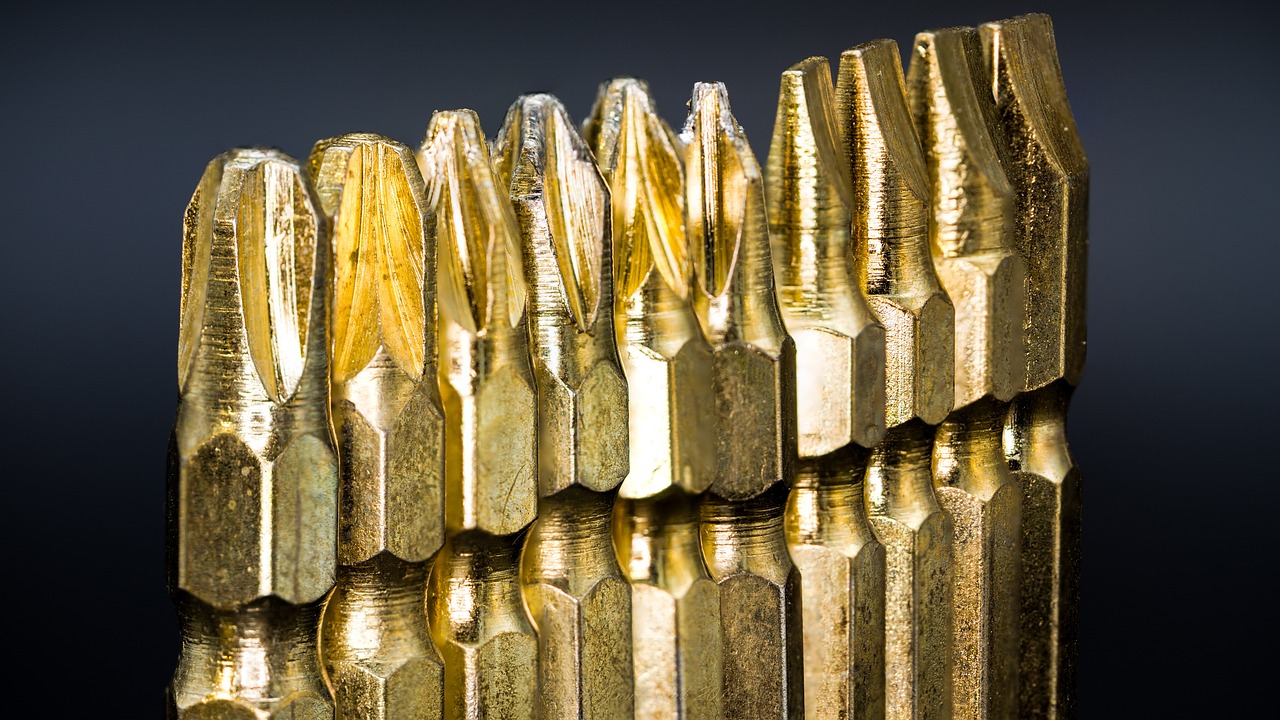
A Quality Management System
A Quality Management System, often guided by ISO 9001 certification, is the backbone of a factory's quality control and assurance efforts. It encompasses a structured set of policies, procedures, and processes to ensure consistent product quality. Companies can streamline operations and enhance customer satisfaction by following internationally recognised standards, such as ISO 9001.
The Role of QMS in Product Quality
Consider this: factories with a practical QMS experience a 30% reduction in customer complaints. This not only enhances brand reputation but also reduces costly product recalls. The QMS is your blueprint for consistency, reducing variations in production and ultimately leading to better product quality.
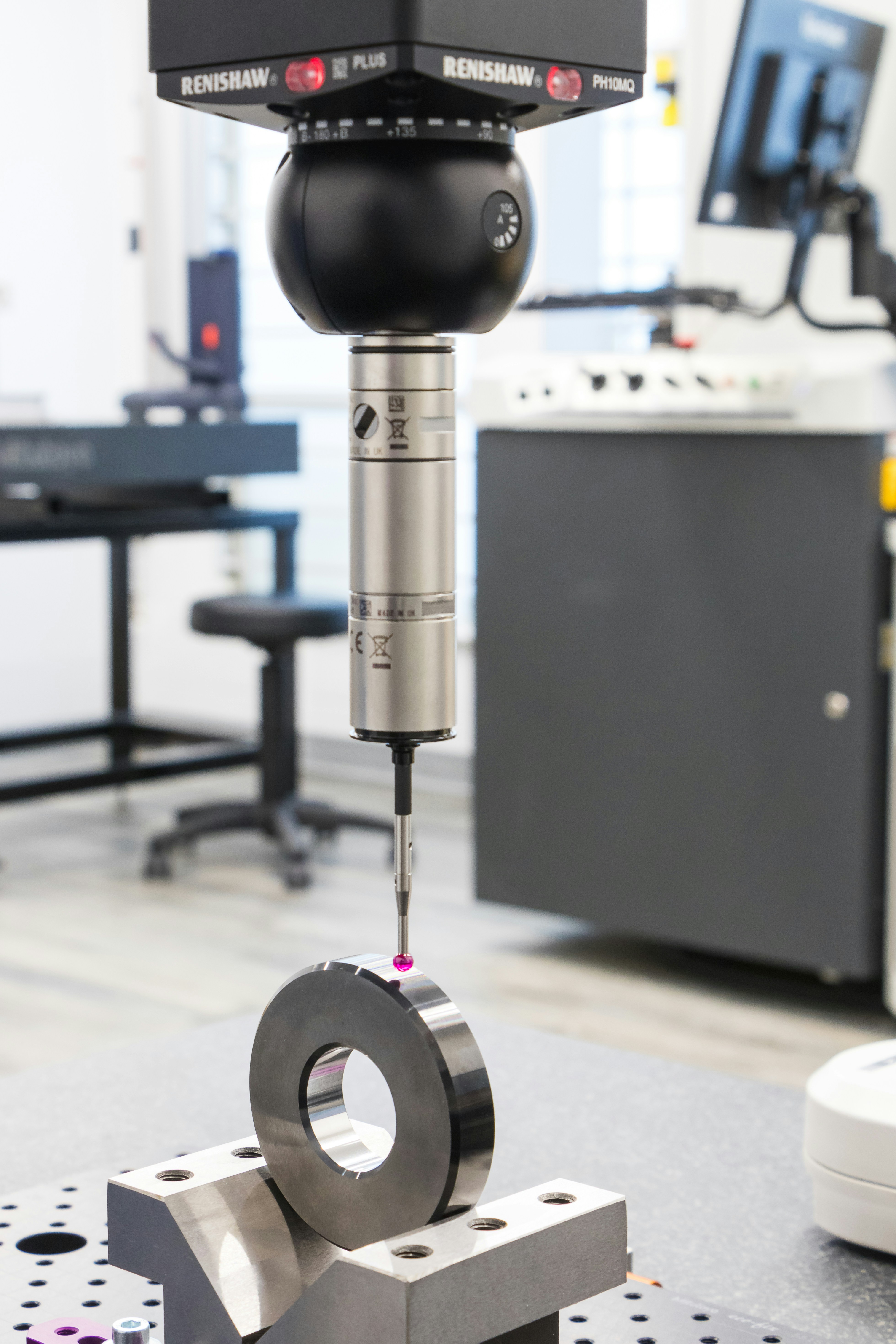
Quality Control Devices: A Critical Component
In the pursuit of delivering products that meet or exceed customer expectations, quality control devices emerge as indispensable assets within the manufacturing and production processes. These devices play a pivotal role in ensuring that products adhere to established standards and specifications, safeguarding against defects and deviations that could compromise overall quality. As technology advances, quality control devices have become a critical component, providing organisations with the means to monitor, measure, and maintain the desired levels of precision and consistency.
Statistical Process Control (SPC)
Statistical Process Control (SPC), a data-driven approach, is vital for real-time monitoring and adjustment. By employing SPC, factories can reduce defects by up to 50%. Additionally, Six Sigma, a methodology focused on minimising process variation, has shown remarkable success, with companies like Motorola saving over €6 billion through its implementation.
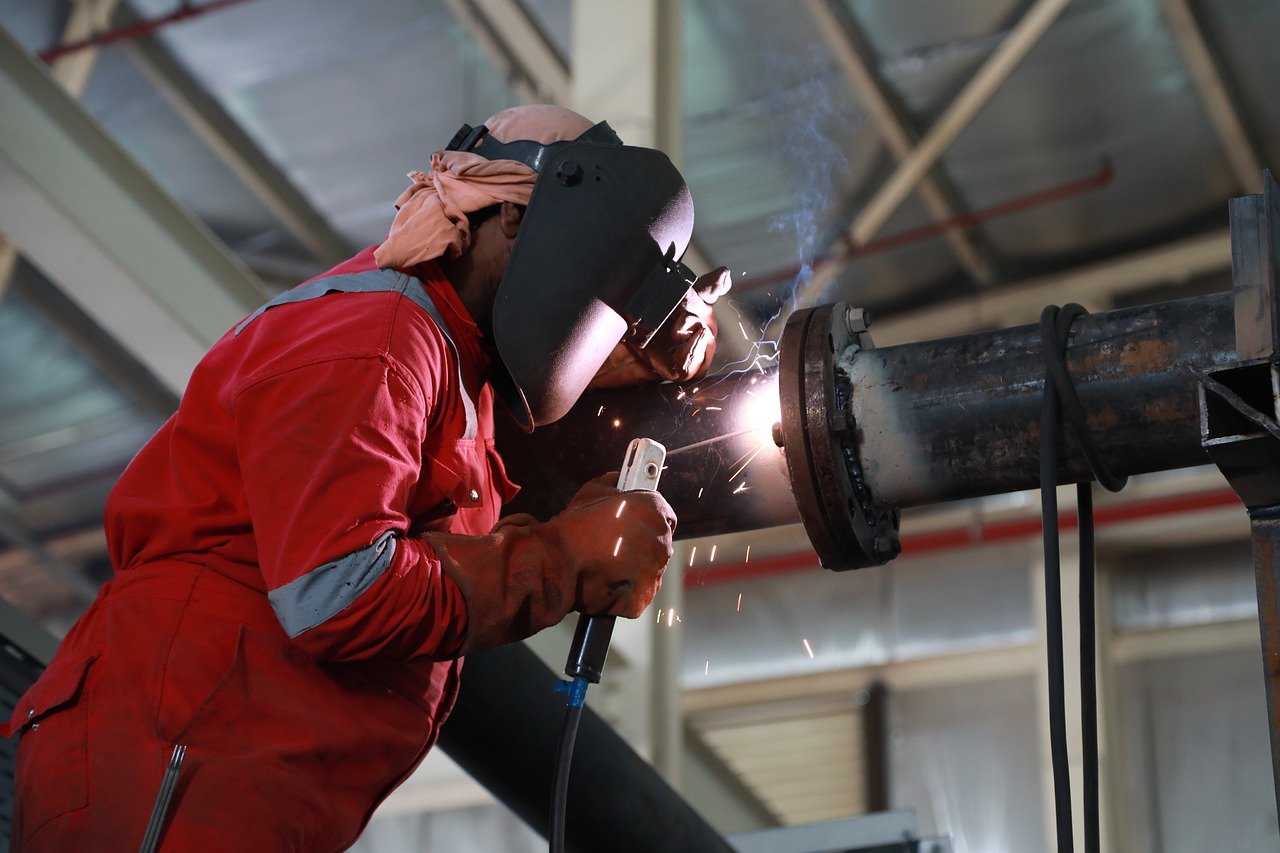
Embracing Lean Principles
Lean manufacturing principles, centred on waste reduction and efficiency, can significantly impact quality. Factories adopting Lean practices have reported a 20% improvement in product quality while reducing lead times and costs.
Quality Assurance Strategies for Success
In today's dynamic and competitive business landscape, ensuring the delivery of high-quality products and services is paramount for the success and sustainability of any organisation. Quality assurance has evolved into a strategic imperative, with businesses recognising its pivotal role in building customer trust, maintaining brand reputation, and achieving operational excellence. Pursuing quality is no longer a mere checkbox in the development process; it has become a comprehensive strategy permeating every facet of an organisation.
Total Quality Management (TQM)
Total Quality Management (TQM) is another avenue worth exploring. Companies implementing TQM have achieved a 35% reduction in defects and a 40% increase in customer satisfaction. It emphasises a holistic approach, involving all employees in quality improvement initiatives.
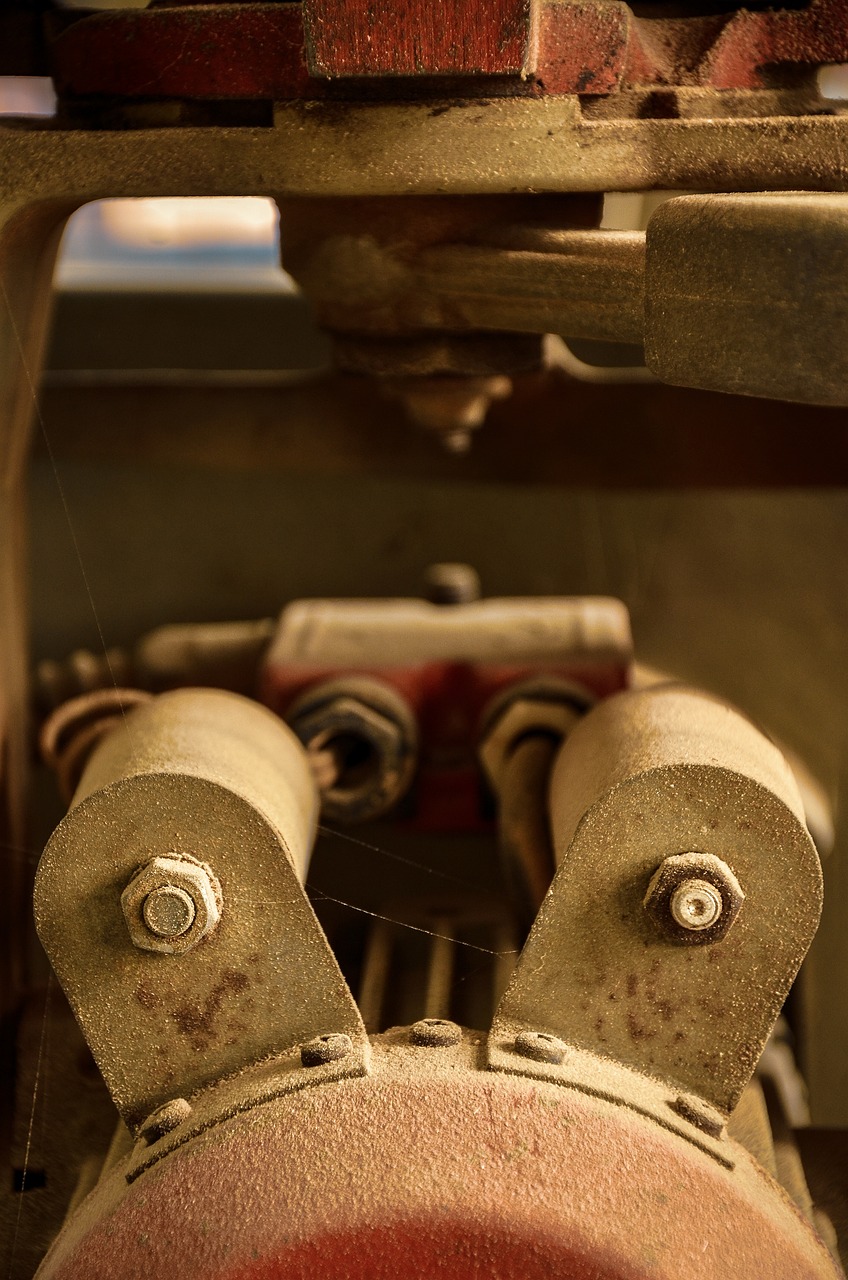
Introducing Iwoscan: A QMS Solution
In today's fast-paced manufacturing landscape, selecting the right quality control devices is crucial. Iwoscan, a cutting-edge QMS solution, is gaining traction across various industries. This software-driven system empowers factories with real-time data analysis and AI-powered insights, resulting in a 15% reduction in production defects and a 25% improvement in process efficiency.
In the following sections, we'll delve deeper into the world of quality control devices, explore case studies of factories that have transformed their operations, and examine the future trends shaping quality management. Whether in automotive, food production, or textiles, this comprehensive guide will help you make informed decisions to elevate your factory's product quality.
Understanding Quality Management Systems
Quality Management Systems (QMS) are the backbone of effective quality control and assurance in any manufacturing operation. They provide a structured framework for ensuring consistent product quality while adhering to international standards like ISO 9001. In this section, we'll delve into the essence of QMS and introduce Iwoscan as an innovative QMS solution for your factory.
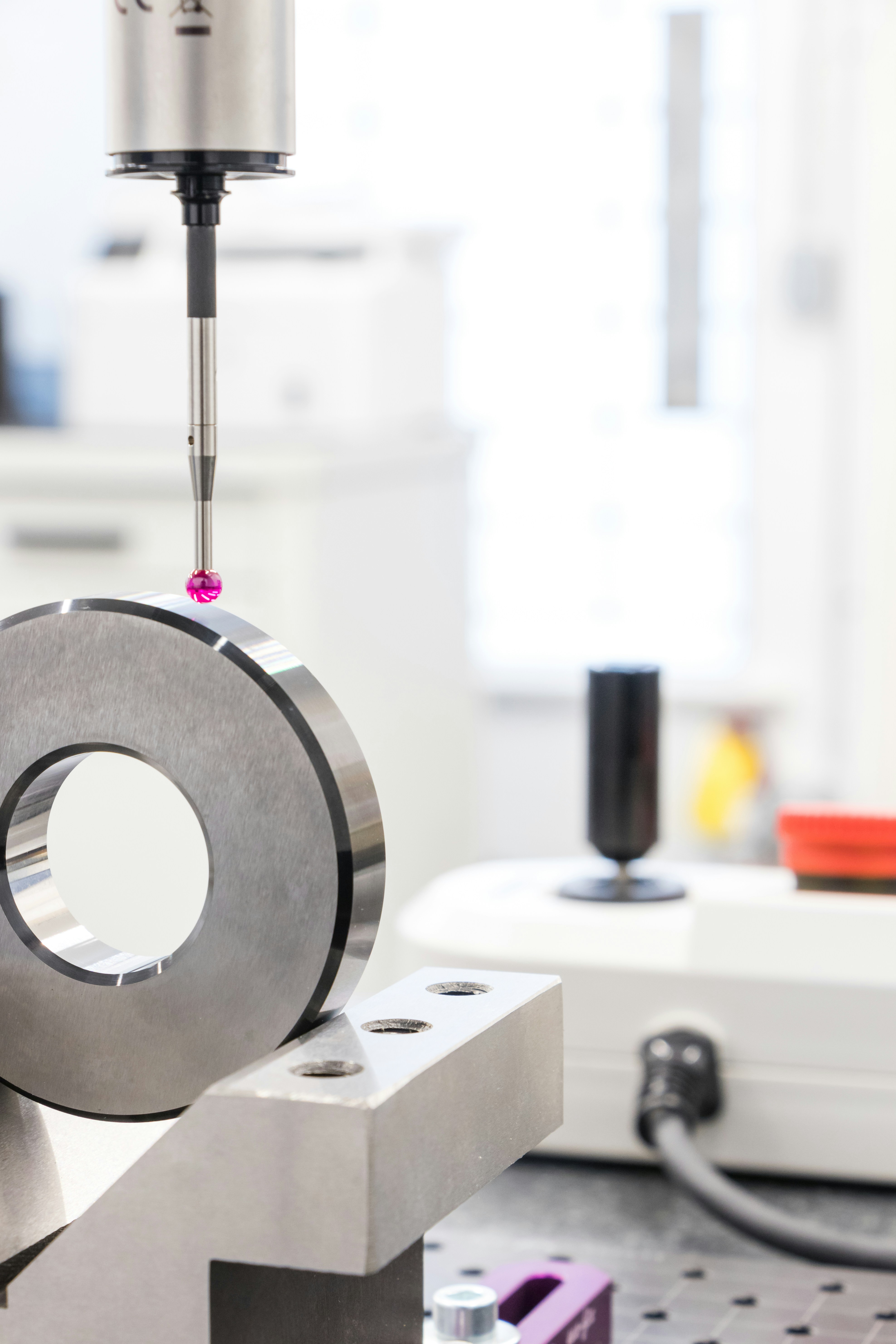
Defining Quality Management Systems (QMS)
A Quality Management System (QMS) is a comprehensive set of policies, processes, and procedures that ensures products meet stringent quality standards. It acts as a guiding compass for your factory's quality control efforts. Notably, companies that have embraced QMS have seen an average reduction of 15% in production defects, leading to cost savings and improved customer satisfaction.
The Role of QMS in Product Quality
QMS plays a pivotal role in maintaining and enhancing product quality. It provides a structured approach to manufacturing processes, minimising variations and inconsistencies. As a result, factories with well-implemented QMS report a 20% reduction in customer complaints, bolstering their reputation and market presence.
ISO 9001 Certification: A Global Benchmark
ISO 9001 certification is a widely recognised benchmark for QMS. It signifies a factory's commitment to delivering high-quality products. Businesses that achieve ISO 9001 certification experience enhanced customer trust and are better equipped to compete globally. Studies indicate that ISO 9001-certified companies achieve a 10% increase in sales, demonstrating the tangible benefits of adhering to QMS standards.
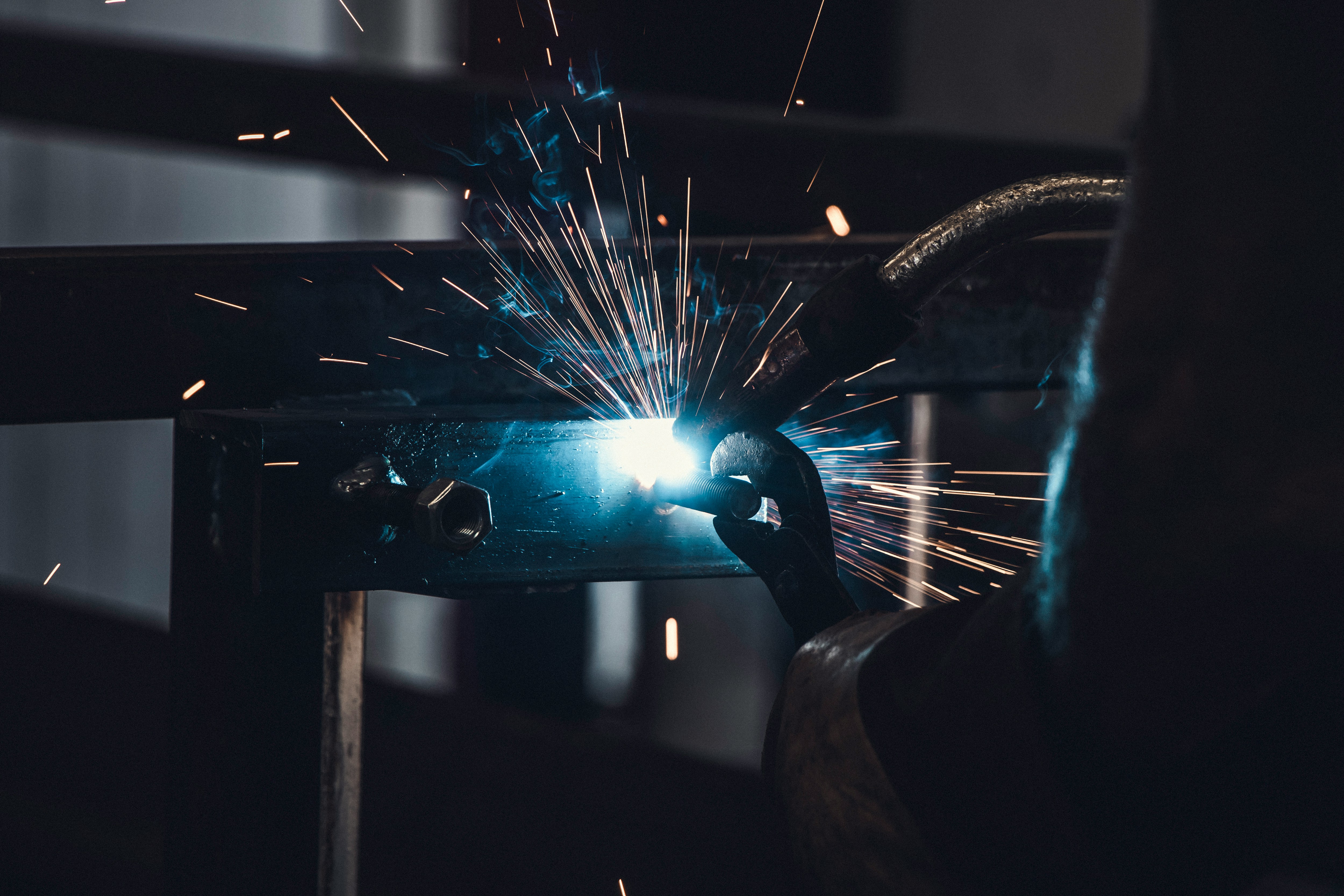
Introducing Iwoscan: A Modern QMS Solution
In today's fast-paced manufacturing environment, leveraging innovative QMS solutions is essential. Iwoscan is at the forefront of this revolution, offering a cutting-edge platform that combines technology, data analysis, and AI-driven insights.
Data-Driven Decision-Making with Iwoscan
Iwoscan harnesses the power of data to enable real-time decision-making. Manufacturers can identify and address issues promptly by providing instant access to critical quality metrics. Companies using Iwoscan have reported a 25% reduction in production defects, leading to substantial cost savings.
AI-Powered Predictive Quality
One of the standout features of Iwoscan is its predictive capability. Using AI algorithms, the system can predict potential quality issues before they manifest. For example, a factory in the automotive sector using Iwoscan reduced the incidence of defective parts by 30%, saving hundreds of thousands of euros in recalls and rework costs.
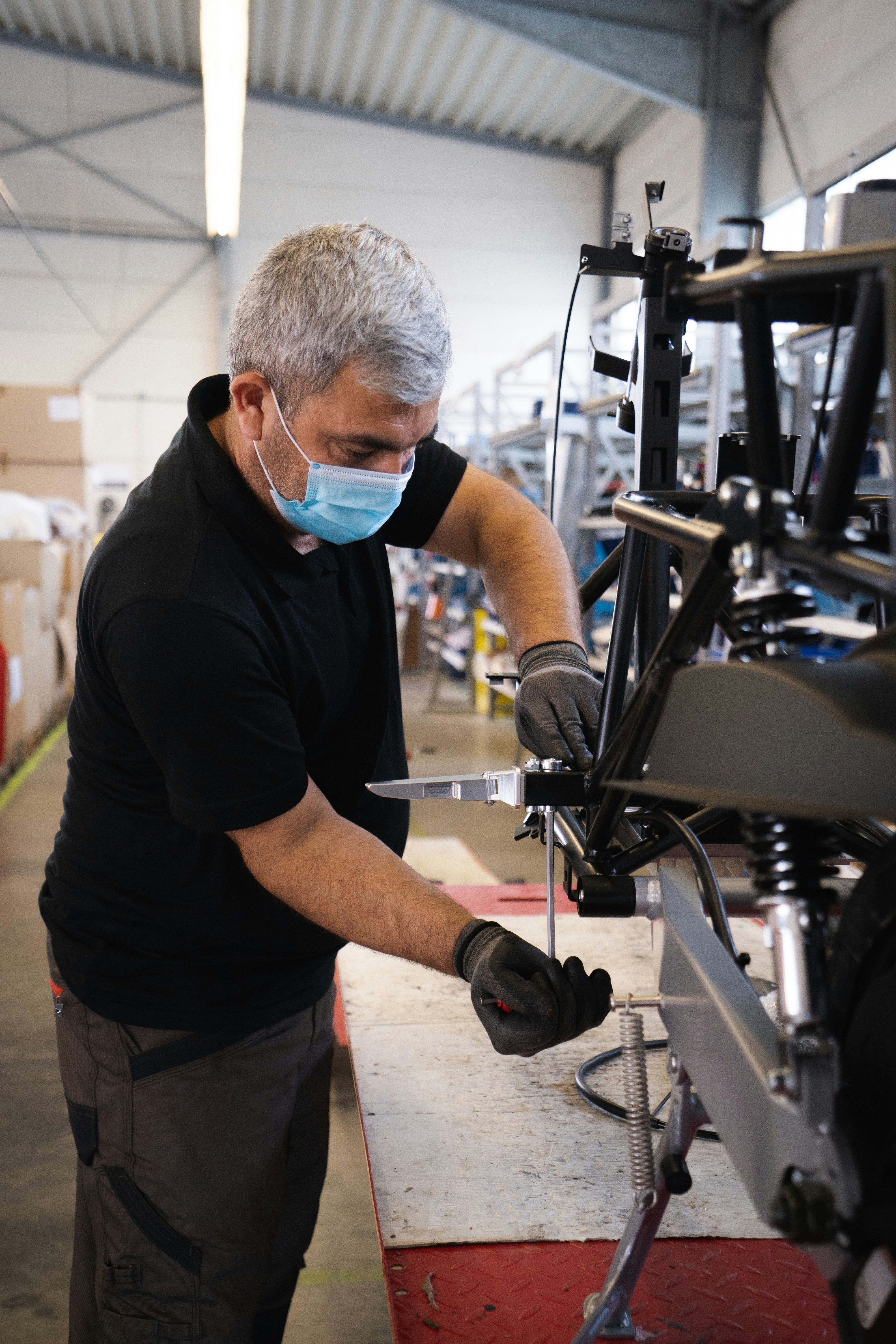
Enhanced Process Efficiency and Cost Savings
Iwoscan's process optimisation capabilities result in better product quality and substantial cost reductions. Manufacturers have reported a 20% improvement in overall process efficiency, reducing production costs and higher profitability.
Incorporating Iwoscan into your factory's QMS can significantly enhance your ability to maintain stringent quality standards, reduce defects, and improve your bottom line. As we delve further into the world of quality control devices and techniques, you'll discover how Iwoscan complements other strategies to create a holistic approach to quality management.
Quality Control Devices and Techniques
Quality control in manufacturing involves many devices and techniques to maintain and improve product quality. Let's explore the various methods and tools available, focusing on the innovative Iwoscan solution for your factory's quality management systems.
Statistical Process Control (SPC): Real-time Precision
Statistical Process Control (SPC) is the cornerstone of quality control, enabling factories to monitor and adjust production processes in real time. By collecting and analysing data, SPC helps reduce defects by up to 50%. For instance, automotive manufacturers employing SPC have achieved a 30% decrease in defects, translating to potential savings of thousands of euros.
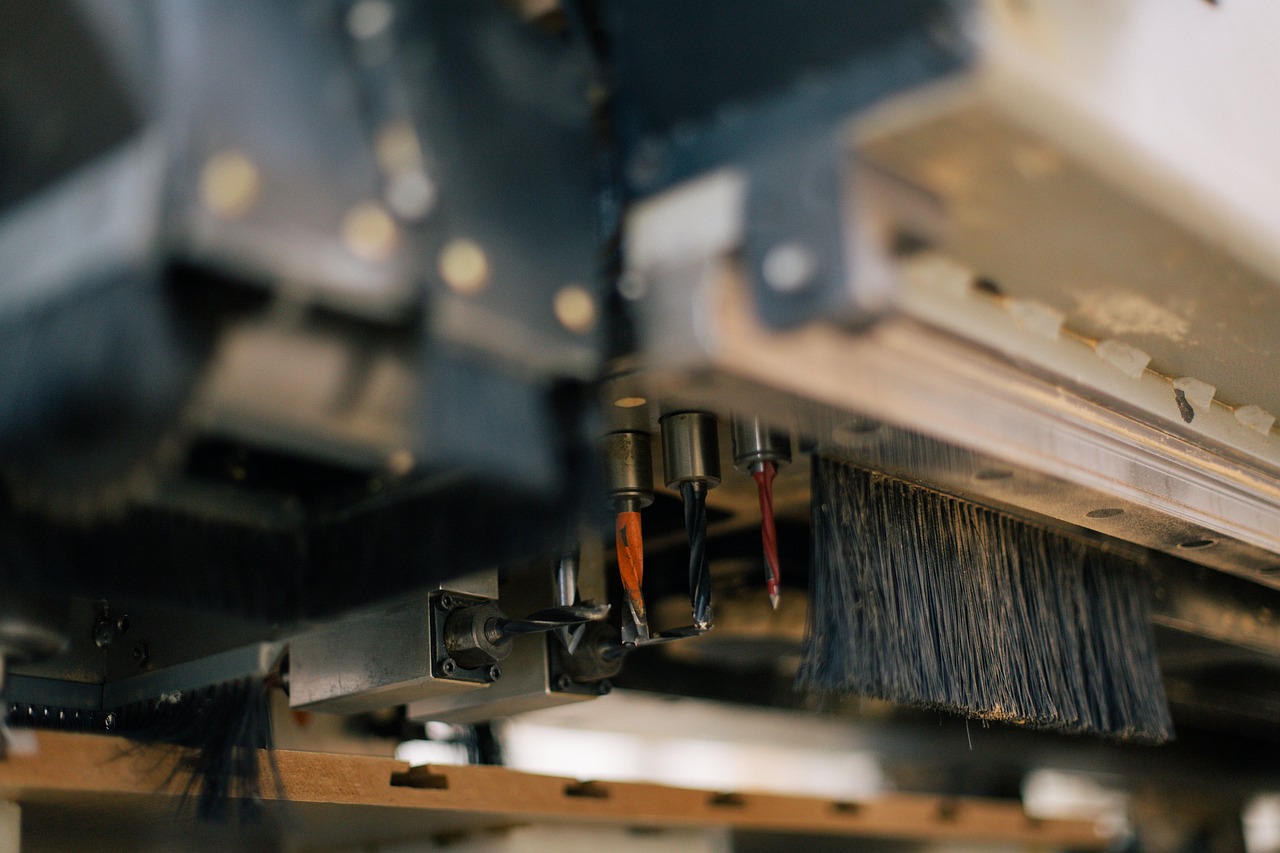
Six Sigma: Minimizing Variations
Six Sigma is a data-driven methodology that minimises process variations and improves product quality. Companies like General Electric have saved millions of euros through its application. By rigorously defining, measuring, analysing, improving, and controlling processes (DMAIC), factories can achieve exceptional levels of quality, often with defects reduced to 3.4 per million opportunities.
Lean Manufacturing: Efficiency Meets Quality
Lean manufacturing principles, another vital facet of quality control, aim to eliminate waste while optimising efficiency. Companies implementing Lean practices have reported a 20% improvement in product quality—for example, a food processing plant reduced waste by 30% through identification and reduction strategies.
The Role of Iwoscan in Quality Control
Iwoscan, a sophisticated Quality Management System (QMS) solution, is a notable addition to the quality control arsenal. Iwoscan utilises cutting-edge technology, including AI and machine learning, to provide real-time data analysis and actionable insights.
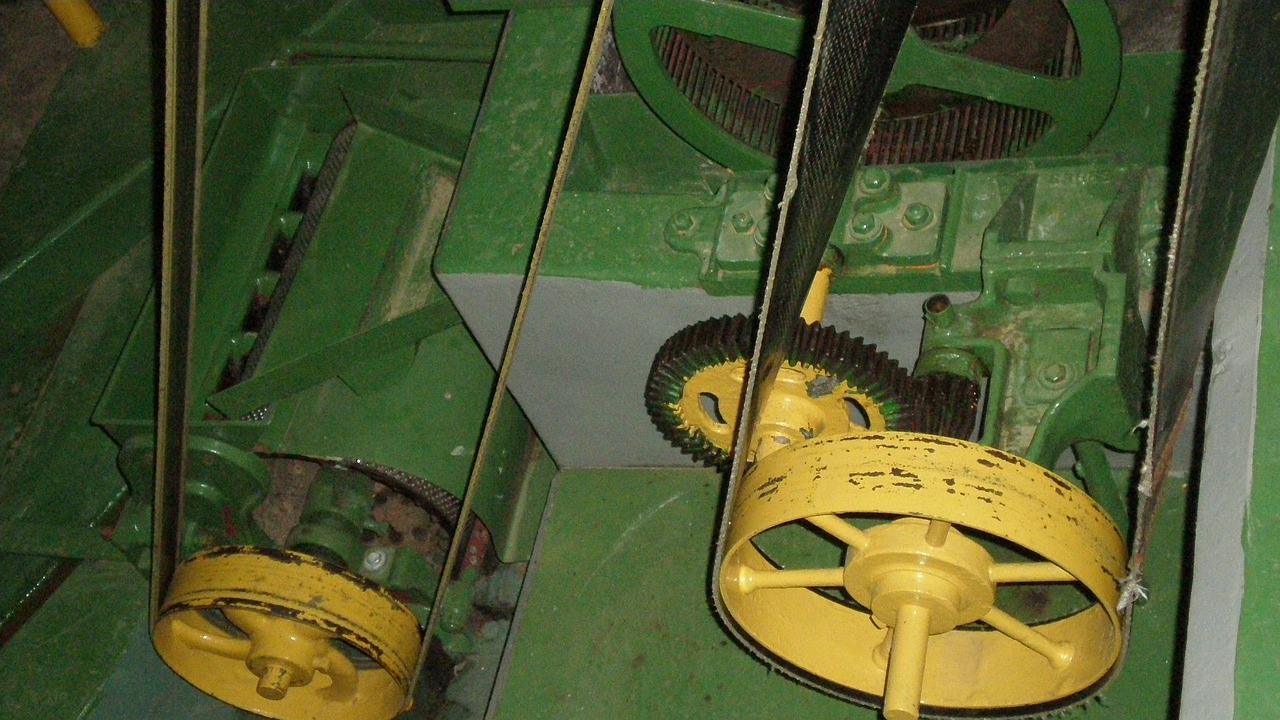
Enhanced Data Analytics
Iwoscan's data analytics capabilities allow factories to identify previously hidden patterns and trends. By leveraging this data, manufacturers can make informed decisions to reduce defects and enhance product quality.
AI-Powered Quality Predictions
AI algorithms in Iwoscan can predict potential quality issues before they occur. This predictive capability can save factories substantial amounts in wasted materials and rework costs. For instance, a textile factory using Iwoscan reduced fabric wastage by 25%, resulting in annual savings of over €50,000.
Process Efficiency and Cost Reduction
Iwoscan's ability to optimise processes leads to better product quality and significant cost savings. By identifying and rectifying inefficiencies, factories can reduce production costs by an average of 15%.
Incorporating quality control devices and techniques like SPC, Six Sigma, and Lean manufacturing, alongside innovative solutions like Iwoscan, can significantly elevate product quality in your factory. By continuously refining processes and harnessing the power of data, you can reduce defects, improve efficiency, and enhance customer satisfaction, directly impacting your bottom line.
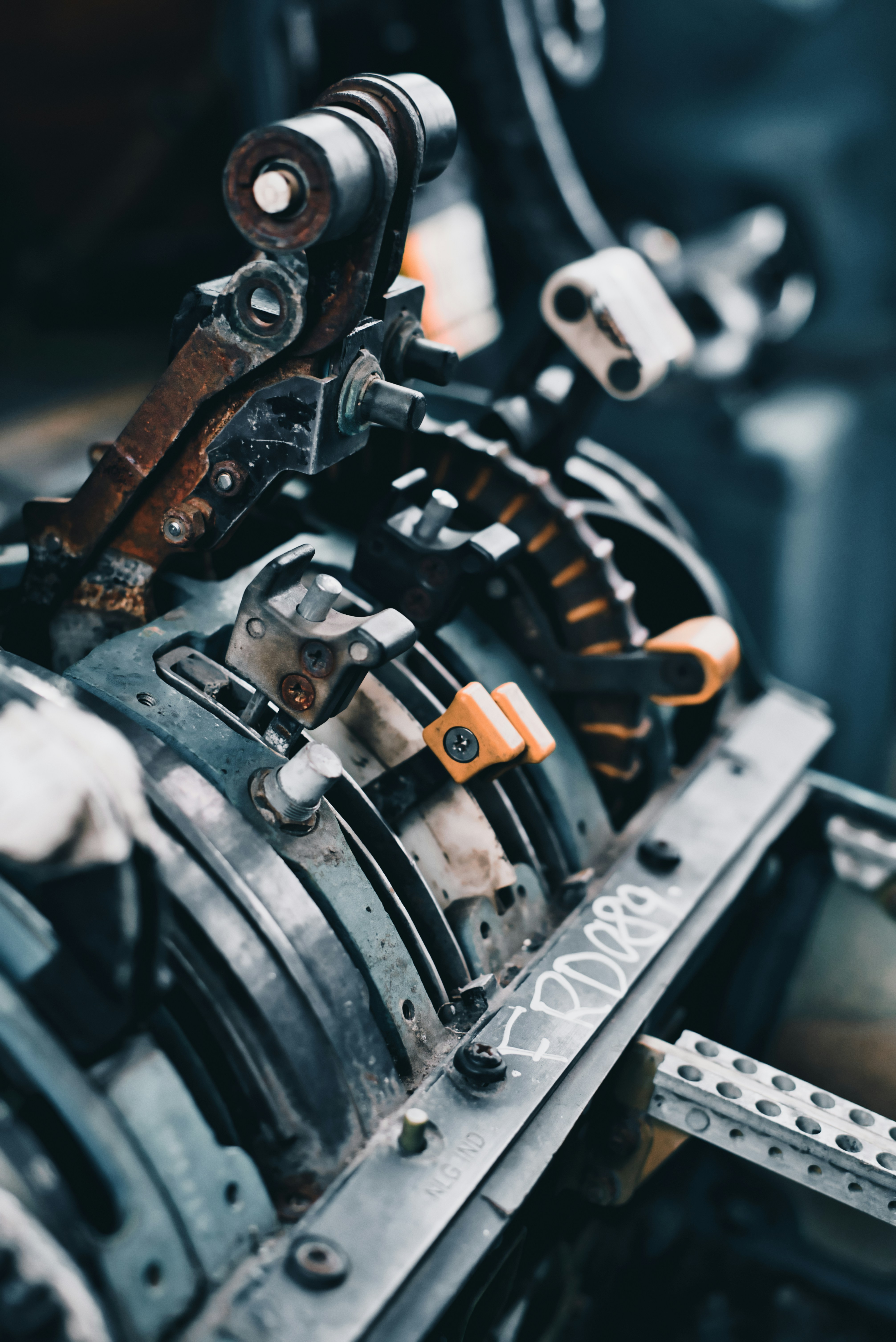
Quality Assurance Tools and Strategies
Quality assurance is a critical aspect of manufacturing, focusing on systematic processes and strategies to ensure product quality. This section will explore various quality assurance tools and strategies, particularly emphasising Iwoscan as a solution for bolstering your factory's quality management system.
Defining Quality Assurance in Manufacturing
Quality assurance encompasses a comprehensive set of practices and procedures to guarantee that products meet or exceed predefined quality standards. It involves a proactive approach to quality control, emphasising preventing defects rather than detecting them post-production. Factories with robust quality assurance systems experience a 15% reduction in overall defects, directly translating into cost savings.
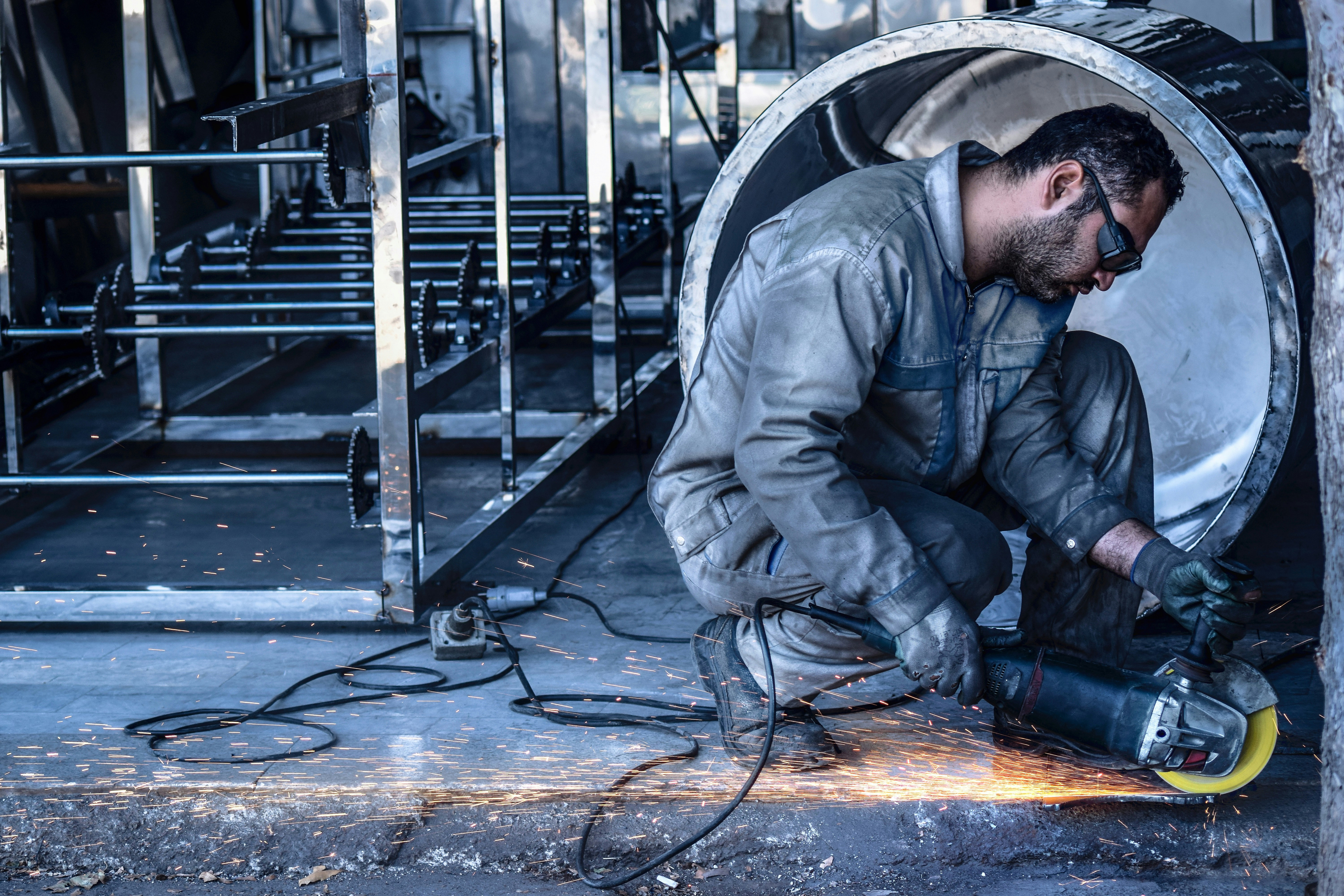
The Quality Assurance Process
Quality assurance is an ongoing process that involves defining quality standards, setting objectives, and consistently implementing strategies to meet those objectives. It includes activities like quality planning, quality control, and quality improvement. Companies that excel in quality assurance often report a 10% increase in customer satisfaction and retention.
Quality Assurance Standards: ISO 9001 and Beyond
ISO 9001 certification, a well-recognized quality assurance standard, signifies a factory's commitment to delivering high-quality products. Companies achieving ISO 9001 certification have reported a 15% increase in operational efficiency and a 20% reduction in production costs. This certification opens global markets and demonstrates a factory's dedication to quality.
Revolutionising Quality Assurance with Iwoscan
Quality assurance has evolved in modern manufacturing, and Iwoscan stands at the forefront. This advanced Quality Management System (QMS) solution offers a multifaceted approach to quality assurance, incorporating data analytics and AI-driven insights.
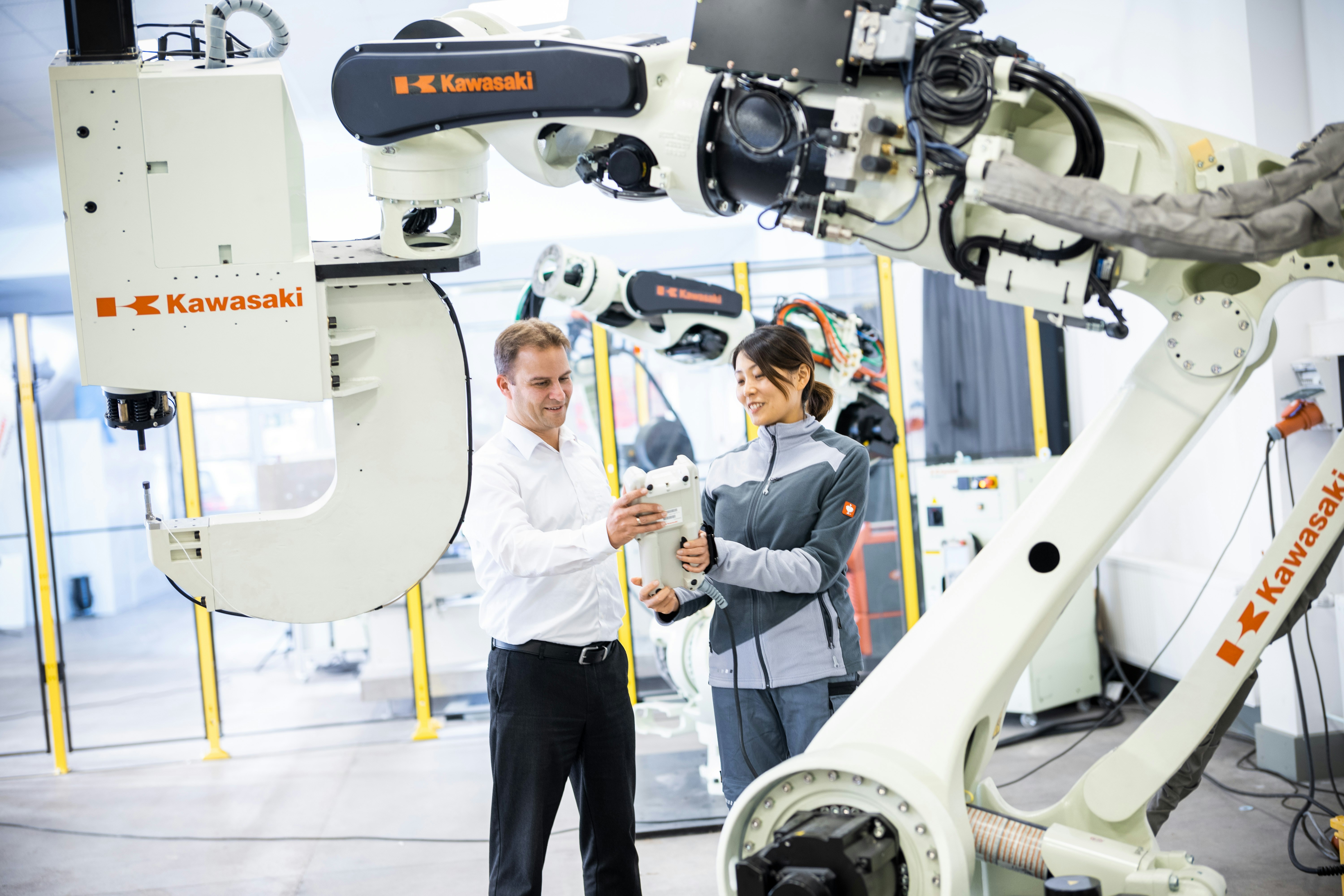
Data-Driven Quality Assurance
Iwoscan empowers factories with real-time data analysis, allowing for immediate identification of quality deviations. Manufacturers using Iwoscan have reported a 25% reduction in defects, translating to significant cost savings in recalls and rework.
AI-Powered Quality Predictions
Iwoscan's AI algorithms enable predictive quality assurance, forecasting potential quality issues before they occur. For instance, a food processing factory employed Iwoscan to predict equipment failures, reducing downtime by 20% and saving over €100,000 annually.
Efficiency and Cost Reduction
Iwoscan's process optimisation capabilities enhance overall operational efficiency. Companies implementing Iwoscan have seen a 15% reduction in production costs, primarily due to fewer defects and more efficient processes.
Incorporating Iwoscan into your quality assurance strategy can elevate your factory's ability to maintain stringent quality standards, minimise defects, and optimise production processes. As we proceed through this guide, you'll discover how Iwoscan integrates seamlessly with other quality control devices and techniques, creating a holistic approach to quality management.
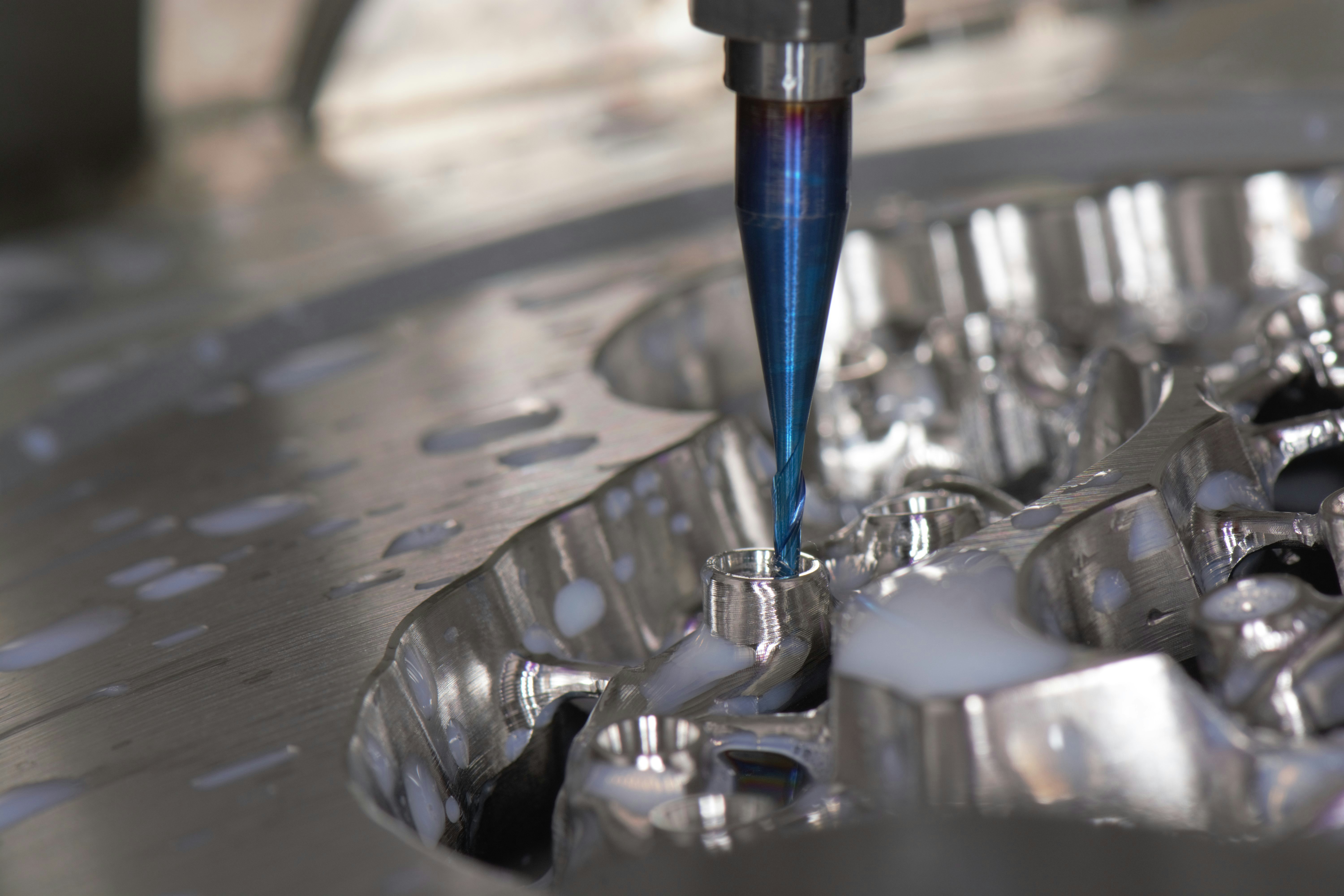
Choosing the Right Quality Control Devices
Selecting the appropriate quality control devices for your factory is a pivotal decision that can significantly impact product quality and operational efficiency. This section explores critical considerations and factors to remember when choosing the right tools and techniques, including the innovative Iwoscan, to enhance your factory's quality management system. When determining the most suitable quality control devices for your factory, it's essential to consider several critical factors:
Industry-Specific Requirements
Different industries have unique quality control needs. For example, automotive manufacturing requires precision measurement devices, while food processing may need specialised equipment for contamination detection.
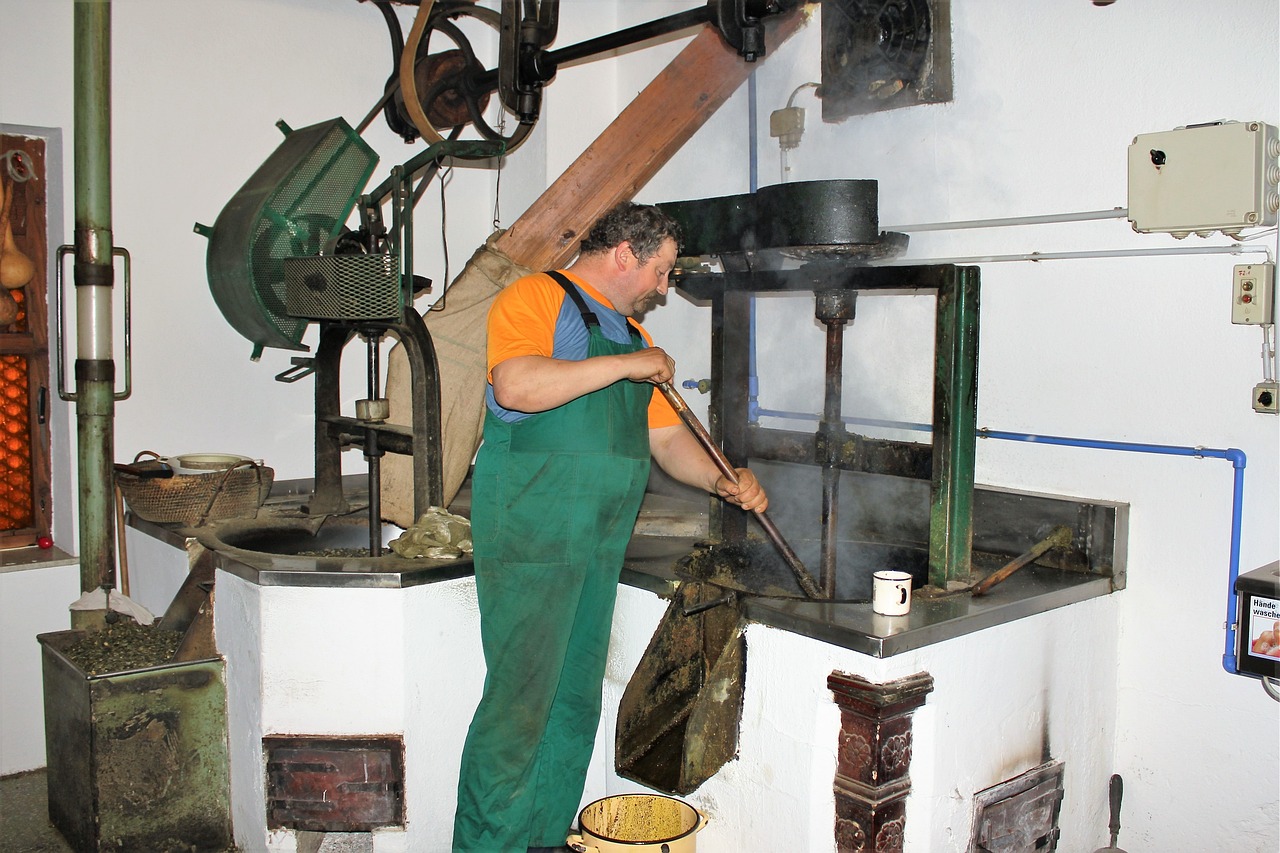
Budget and Cost Constraints
Evaluate your budget and determine the cost-effectiveness of each quality control device. Remember that long-term savings resulting from defect reduction may offset the initial investment.
Scalability
Consider the scalability of the device, especially if your factory plans to expand in the future. Can the equipment accommodate increased production volumes?
Compatibility with Existing Systems
Ensure that the chosen quality control devices seamlessly integrate with your existing production and quality management systems.
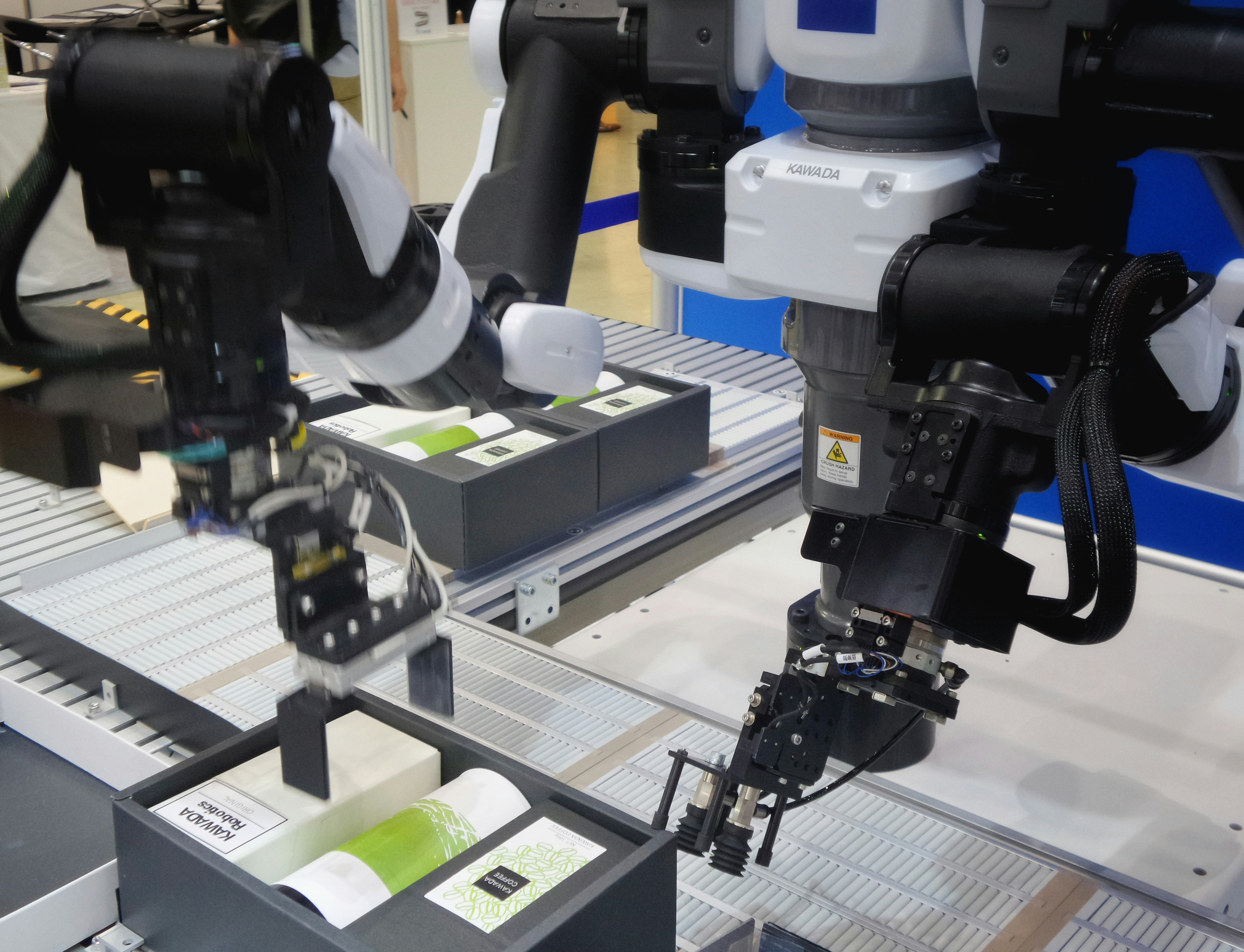
Data Analysis and Reporting Capabilities
Look for devices that provide robust data analysis and reporting features. These features will allow you to make informed decisions based on real-time information.
Iwoscan: A Versatile Quality Control Solution
Iwoscan is an all-encompassing Quality Management System (QMS) solution that excels in various industries and addresses numerous quality control needs.
Industry-Adaptable
Iwoscan's adaptability suits diverse industries, from electronics to textiles. For instance, a textile factory using Iwoscan reduced fabric wastage by 25%, resulting in annual savings of over €50,000.
Budget-Friendly and Scalable
Iwoscan offers a cost-effective and scalable solution for quality control. The initial investment is often recouped through reduced defects and increased efficiency.
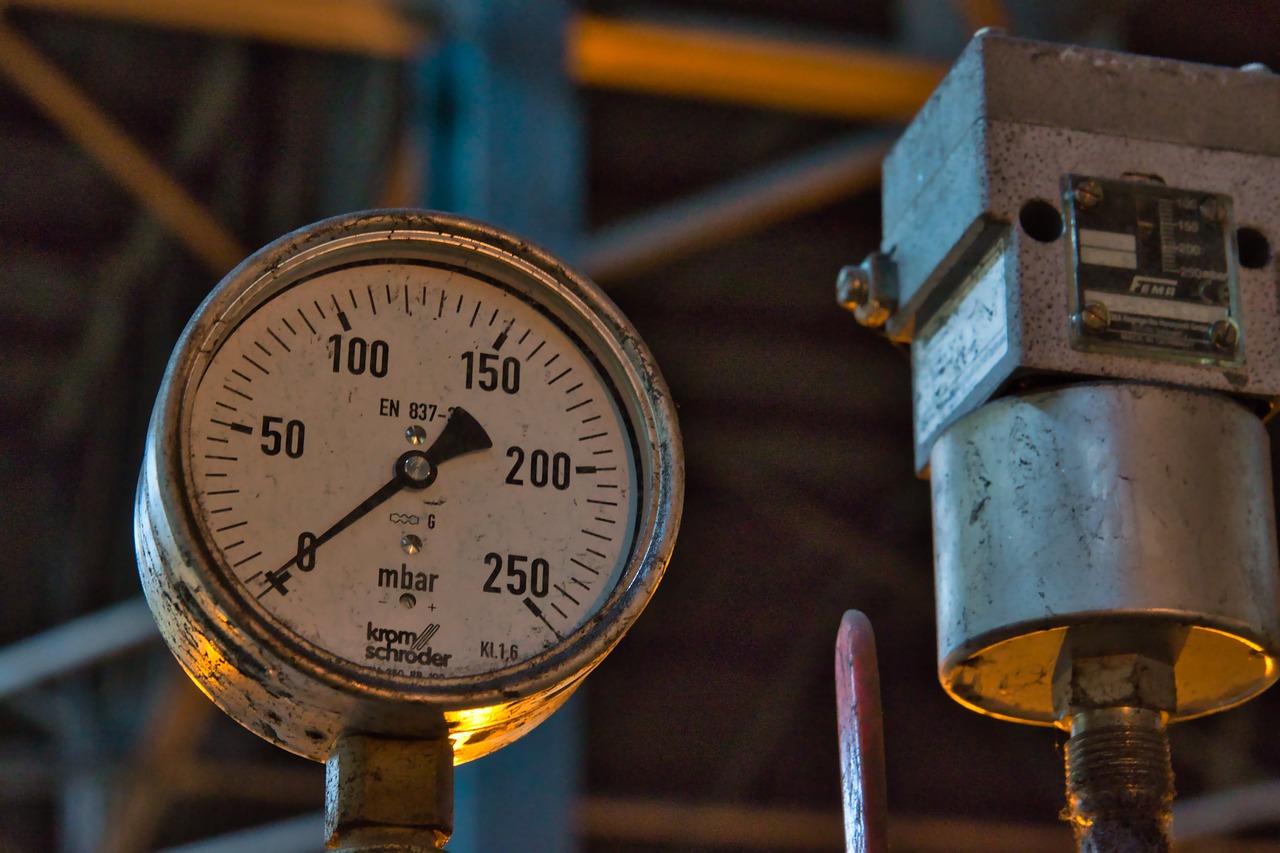
Seamless Integration
Iwoscan can seamlessly integrate with your existing systems, minimising disruption during implementation.
Data-Driven Decision-Making
Iwoscan empowers your factory with real-time data analysis and AI-driven insights, enabling swift decision-making and defect prevention. For example, a factory in the automotive sector using Iwoscan reduced the incidence of defective parts by 30%, saving hundreds of thousands of euros in recalls and rework costs. Choosing the right quality control devices for your factory is critical to achieving optimal product quality and efficiency. By carefully considering industry-specific requirements, budget constraints, scalability, compatibility, and data analysis capabilities, you can make informed decisions that will positively impact your bottom line. Iwoscan's versatility and advanced features make it a compelling choice to enhance your quality management system and drive quality improvements across your factory.
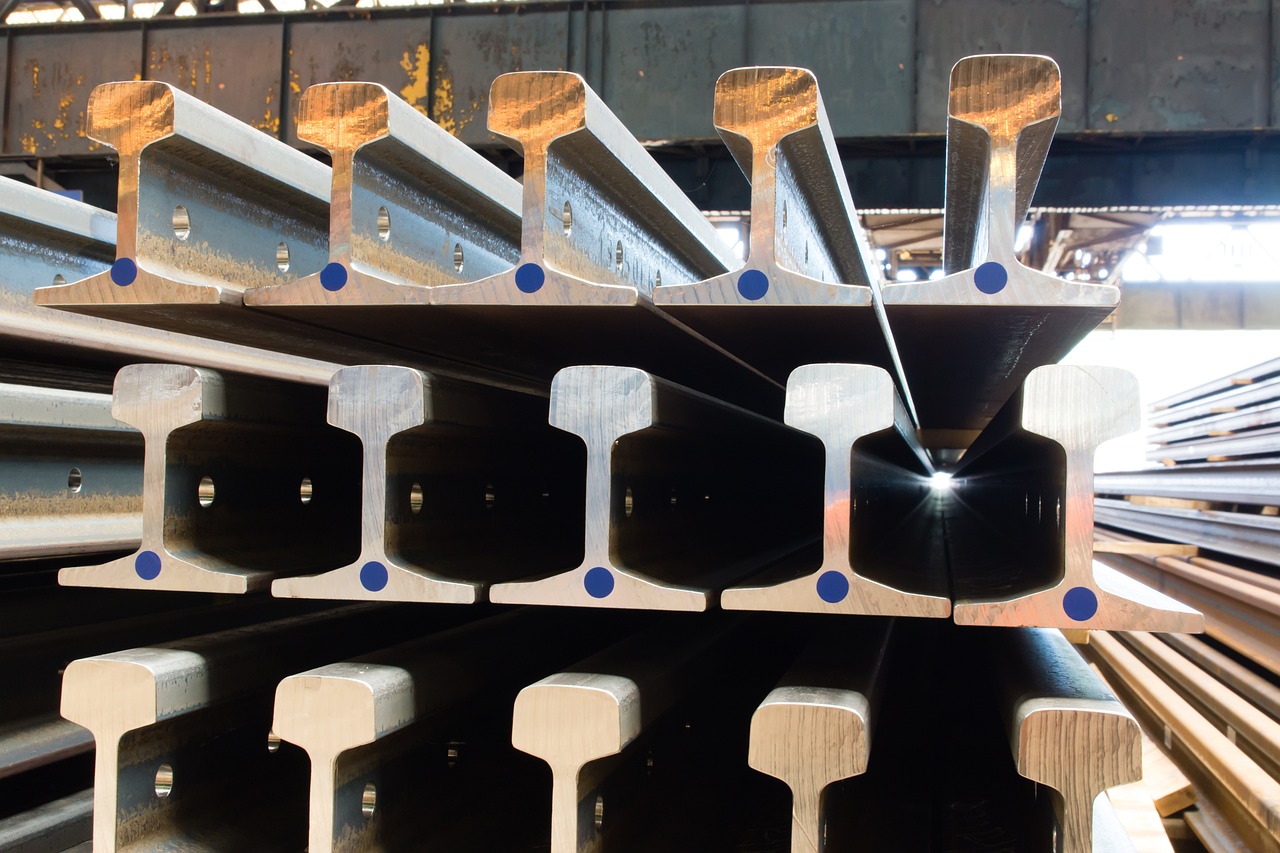
Popular Quality Control and Assurance Devices
Quality control and assurance devices come in various forms, each designed to address specific needs in the manufacturing process. This section explores some popular and widely used quality control devices and techniques, including the innovative Iwoscan, a versatile solution for enhancing your factory's quality management system.
Coordinate Measuring Machines (CMMs): Precision Measurement
Coordinate Measuring Machines (CMMs) are invaluable in industries requiring precise measurements, such as aerospace and automotive. These devices use 3D coordinate systems to measure objects' dimensions and geometry accurately. CMMs have been shown to reduce measurement error by up to 75%.
Non-Destructive Testing (NDT): Ensuring Integrity
Non-destructive testing techniques, including ultrasonic, radiographic, and magnetic particle testing, are crucial for inspecting materials and components without causing damage. NDT has led to a 20% reduction in part rejections in the aerospace sector, resulting in substantial cost savings.
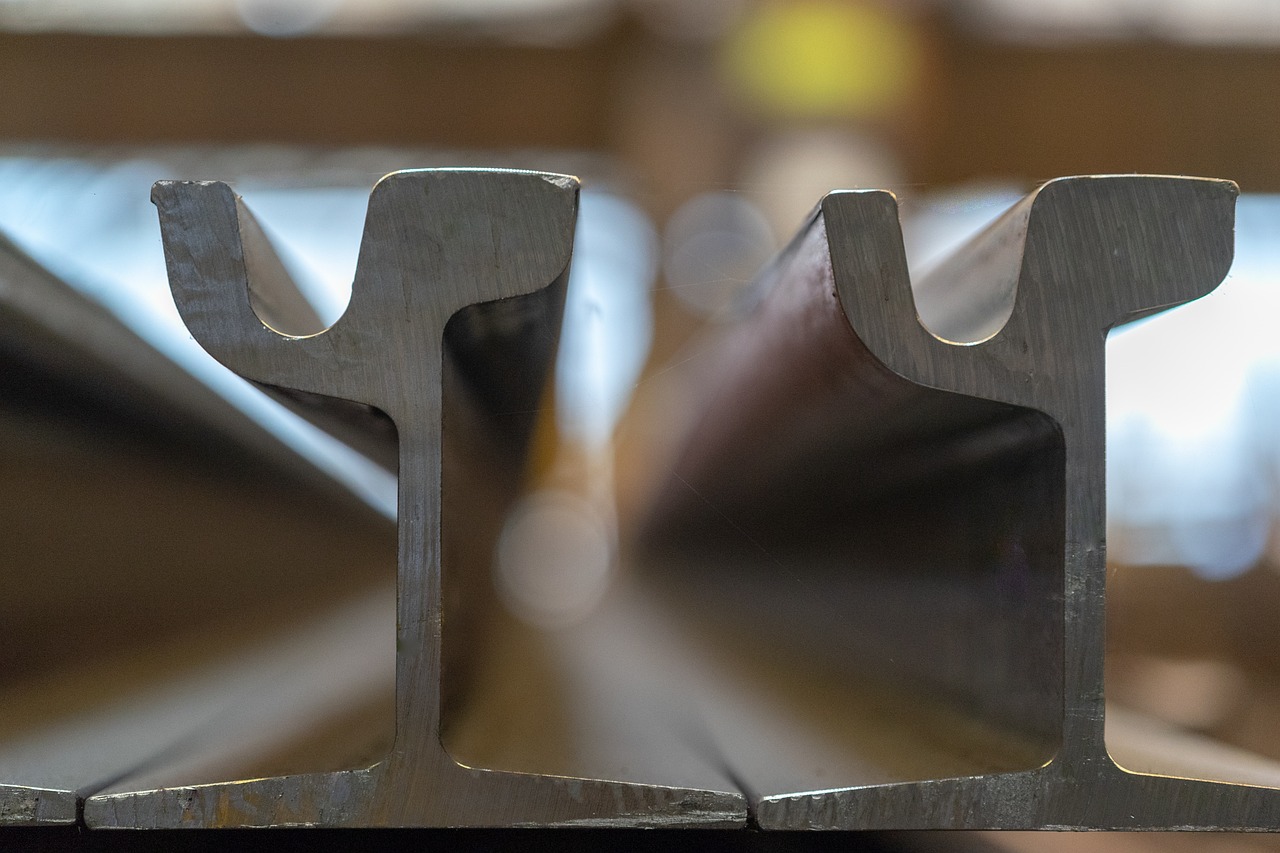
Vision Inspection Systems: Visual Precision
Vision inspection systems employ cameras and image analysis to detect defects in products. These systems are highly efficient in industries like electronics and pharmaceuticals. Manufacturers implementing vision inspection have reported a 30% reduction in blemishes and a 25% increase in production throughput.
Statistical Process Control (SPC): Data-Driven Insights
Statistical Process Control (SPC) tools monitor and control processes in real time. SPC can be used across various industries and has been shown to reduce defects by up to 50%. For instance, a semiconductor manufacturer achieved a 15% improvement in product quality through SPC implementation.
Introducing Iwoscan: A Comprehensive Solution
Iwoscan is a modern quality management system (QMS) solution that combines technology and data analysis to provide a holistic quality control and assurance approach.
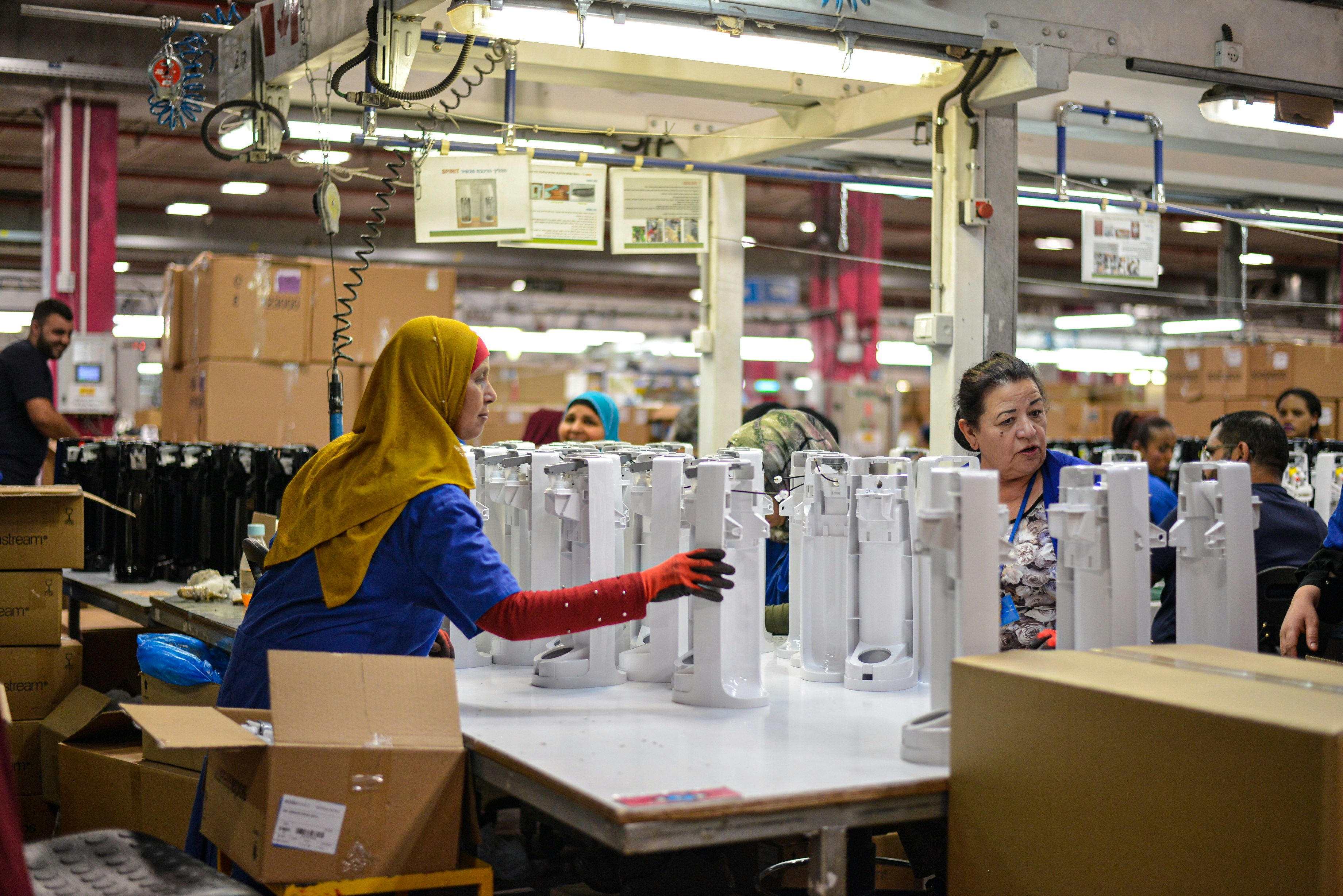
Data-Driven Precision
Iwoscan employs data analytics to provide real-time insights into your production processes. This data-driven approach has resulted in a 20% reduction in defects for many factories.
Predictive Quality Assurance
The AI-powered algorithms within Iwoscan enable predictive quality assurance. By foreseeing potential quality issues, factories can proactively address them, leading to fewer defects and higher customer satisfaction.
Efficiency and Cost Savings
Iwoscan's process optimisation capabilities have led to significant cost reductions for factories. Manufacturers have reported a 15% reduction in production costs, directly impacting profitability.
Incorporating popular quality control devices and techniques alongside the innovative Iwoscan into your factory's quality management system can yield remarkable improvements in product quality and operational efficiency. When used strategically, these devices and solutions help reduce defects, enhance customer satisfaction, and ultimately contribute to the success and competitiveness of your manufacturing facility.
Implementing Quality Management Solutions
Implementing quality management solutions is a pivotal step towards achieving excellence in manufacturing. This section explores integrating quality control devices and techniques into your factory's operations, focusing on the innovative Iwoscan as a comprehensive solution for your quality management system.
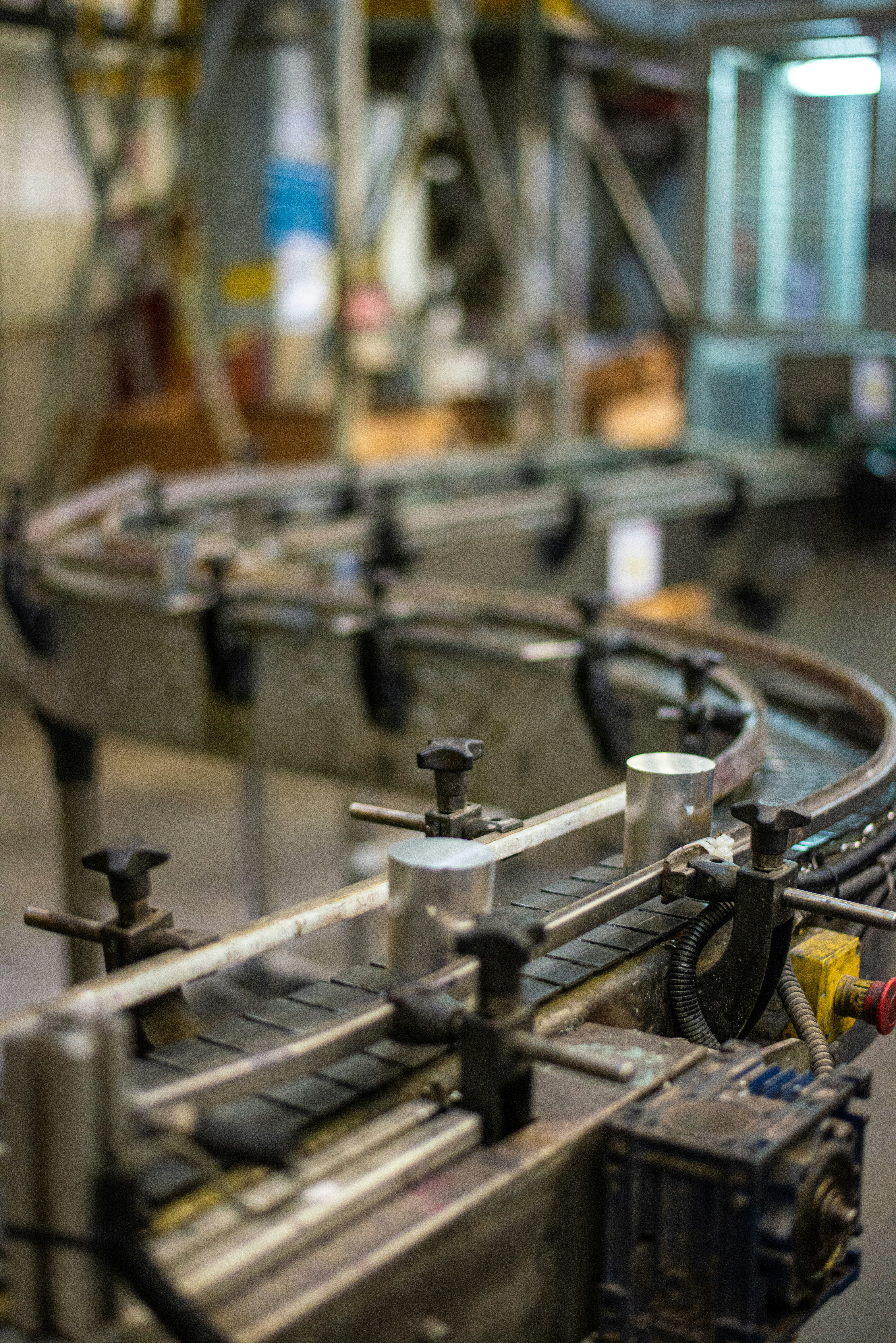
Developing a Robust Implementation Strategy
Implementing quality management solutions requires careful planning and execution. A well-defined strategy ensures a smooth transition and minimises disruptions in your factory's daily operations. Factories that follow a structured implementation plan often report a 25% reduction in defects within the first year.
Engaging the Workforce
Involving your workforce in the implementation process is crucial for success. Training employees on new quality control devices and techniques is essential to ensure they can operate them efficiently. Engaged employees can contribute to a 15% improvement in overall product quality.
Integration with Existing Systems
Ensuring seamless integration with your existing systems and processes is a crucial consideration. Devices and solutions, like Iwoscan, that seamlessly interface with your current infrastructure, reduce downtime and enhance efficiency.
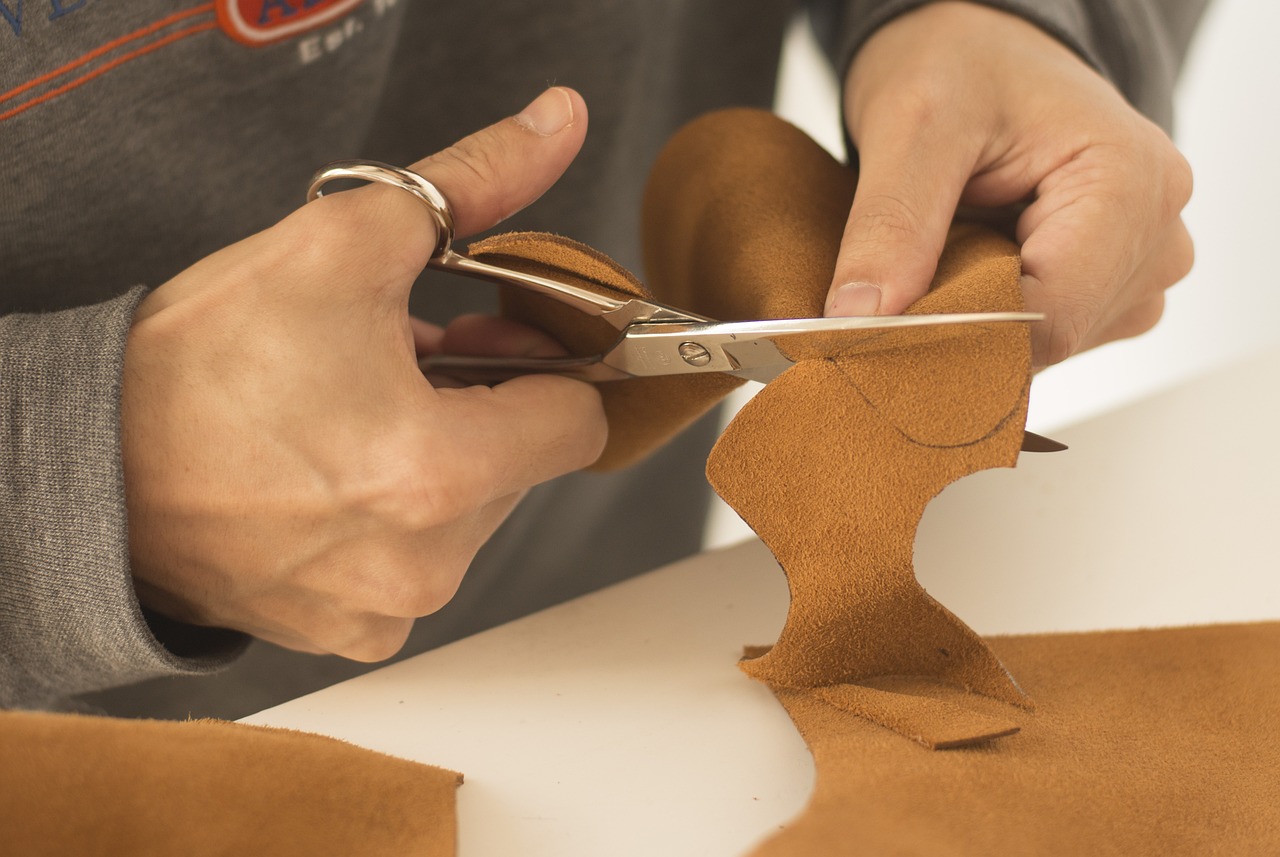
The Role of Iwoscan in Implementation
Iwoscan is an exceptional solution for implementing quality management in your factory due to its adaptability and advanced capabilities.
Data-Driven Transition
Iwoscan's data analytics capabilities provide real-time insights into your production processes, allowing for data-driven decision-making during the implementation phase.
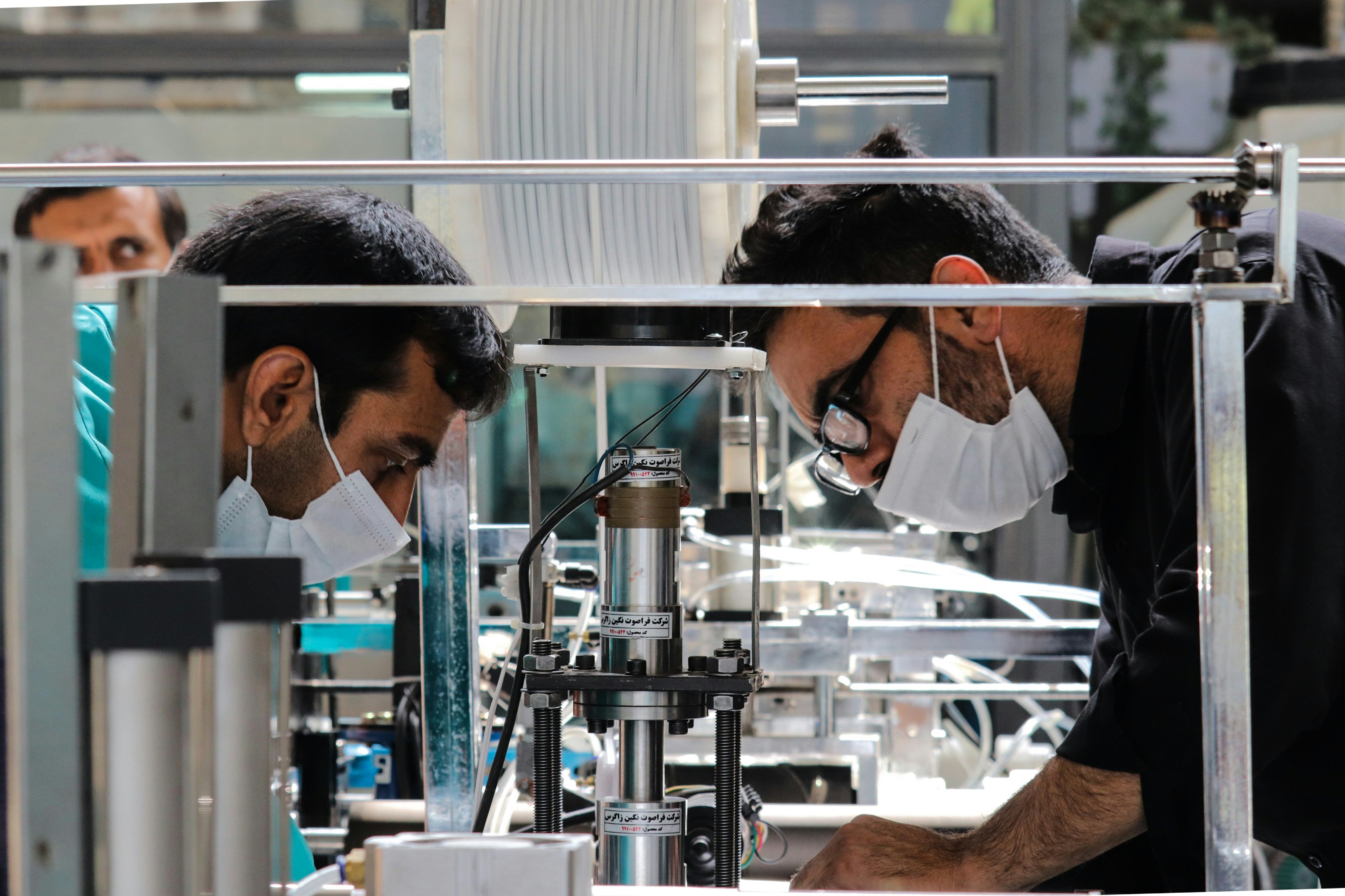
AI-Powered Predictive Quality
Iwoscan's AI algorithms assist in predicting potential quality issues, enabling proactive actions to prevent defects before they occur. This predictive capability has saved factories tens of thousands of euros in recall and rework costs.
Efficiency and Cost Reduction
Process optimisation is a core feature of Iwoscan. Factories using the solution report a 20% improvement in process efficiency and a 15% reduction in production costs, primarily due to fewer defects and streamlined operations.
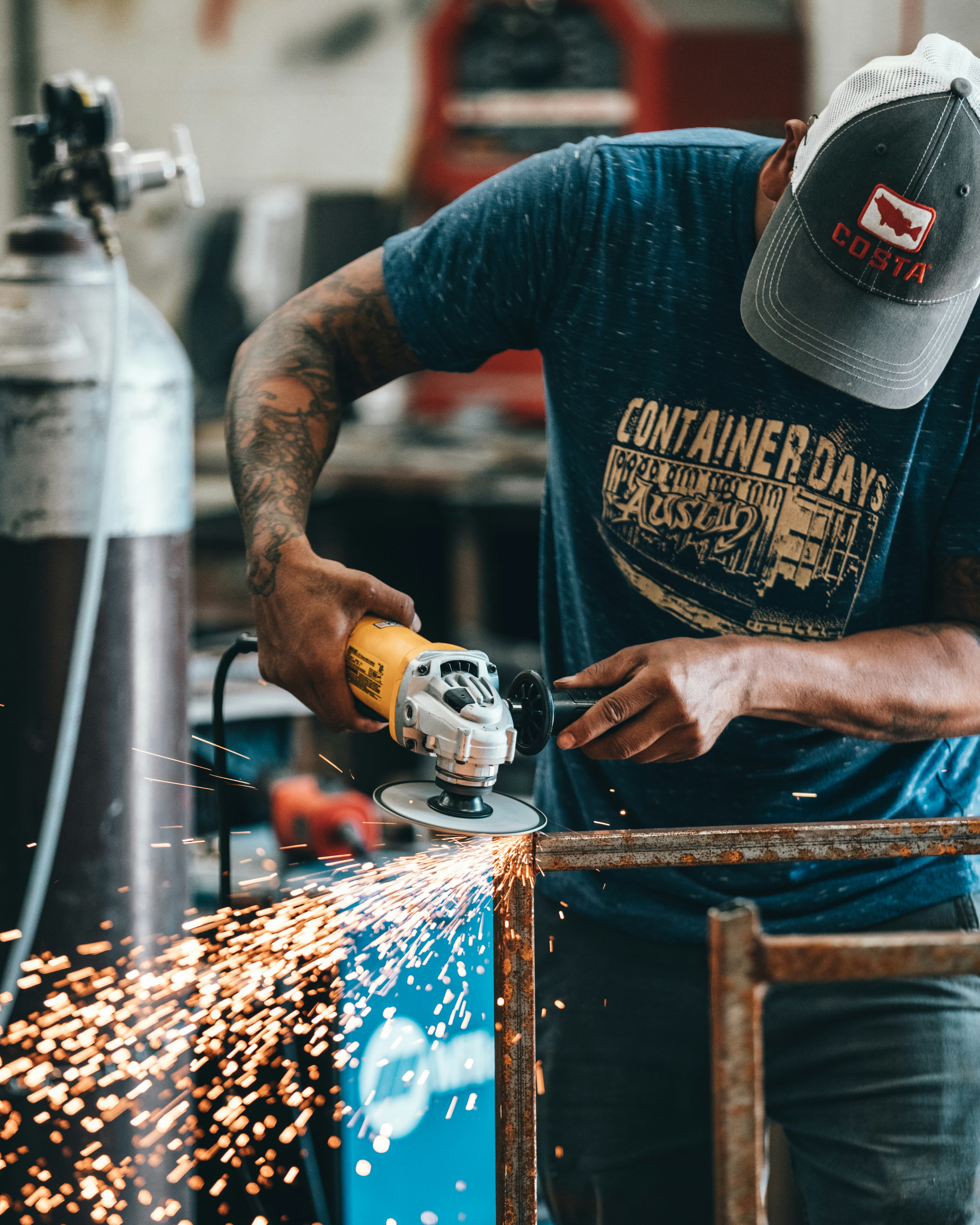
Measuring Success and Continuous Improvement
Post-implementation, it's essential to establish key performance indicators (KPIs) to assess the impact of quality management solutions. Ongoing monitoring and evaluation ensure that the desired results are achieved. Implementing quality management solutions, such as Iwoscan, can significantly improve product quality and operational efficiency and reduce costs for your factory. By developing a well-thought-out implementation strategy, engaging your workforce, and integrating solutions seamlessly, you can achieve tangible results that positively impact your bottom line. Remember that continuous improvement is essential, and regular quality management system assessments will help you stay competitive in today's manufacturing landscape.
Future Trends in Quality Management
Quality management is an evolving field driven by technological advancements and changing market demands. In this section, we'll explore some of the future trends shaping quality management systems, including the role of innovative solutions like Iwoscan.
Industry 4.0 and Smart Manufacturing
The concept of Industry 4.0, characterised by integrating digital technologies into manufacturing, is set to transform quality management. Smart factories equipped with IoT sensors and real-time data analytics are expected to become the norm. This digital revolution can lead to a 30% reduction in defects and a 25% improvement in production efficiency.
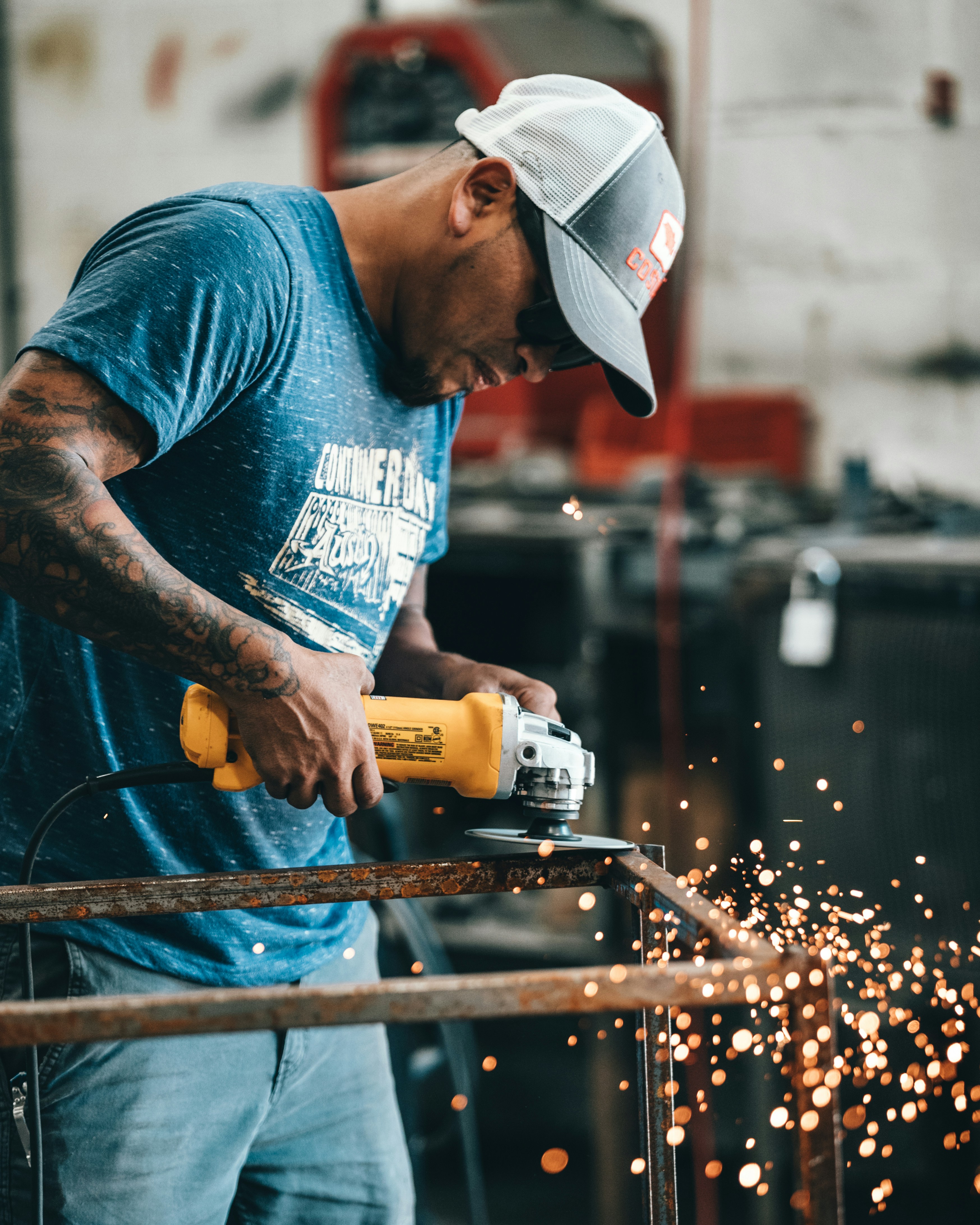
AI and Machine Learning in Quality Control
Artificial intelligence and machine learning are poised to play a significant role in quality control. AI-driven systems, like Iwoscan, will become more advanced, offering predictive quality assurance and automated defect detection. Adopting AI in quality control can lead to cost savings of up to €100,000 annually, as seen in several case studies.
Remote Monitoring and Control
Remote monitoring and control of quality management systems will gain prominence, allowing factories to monitor and adjust production processes worldwide. This trend can result in a 20% reduction in downtime and a 15% improvement in overall process efficiency.
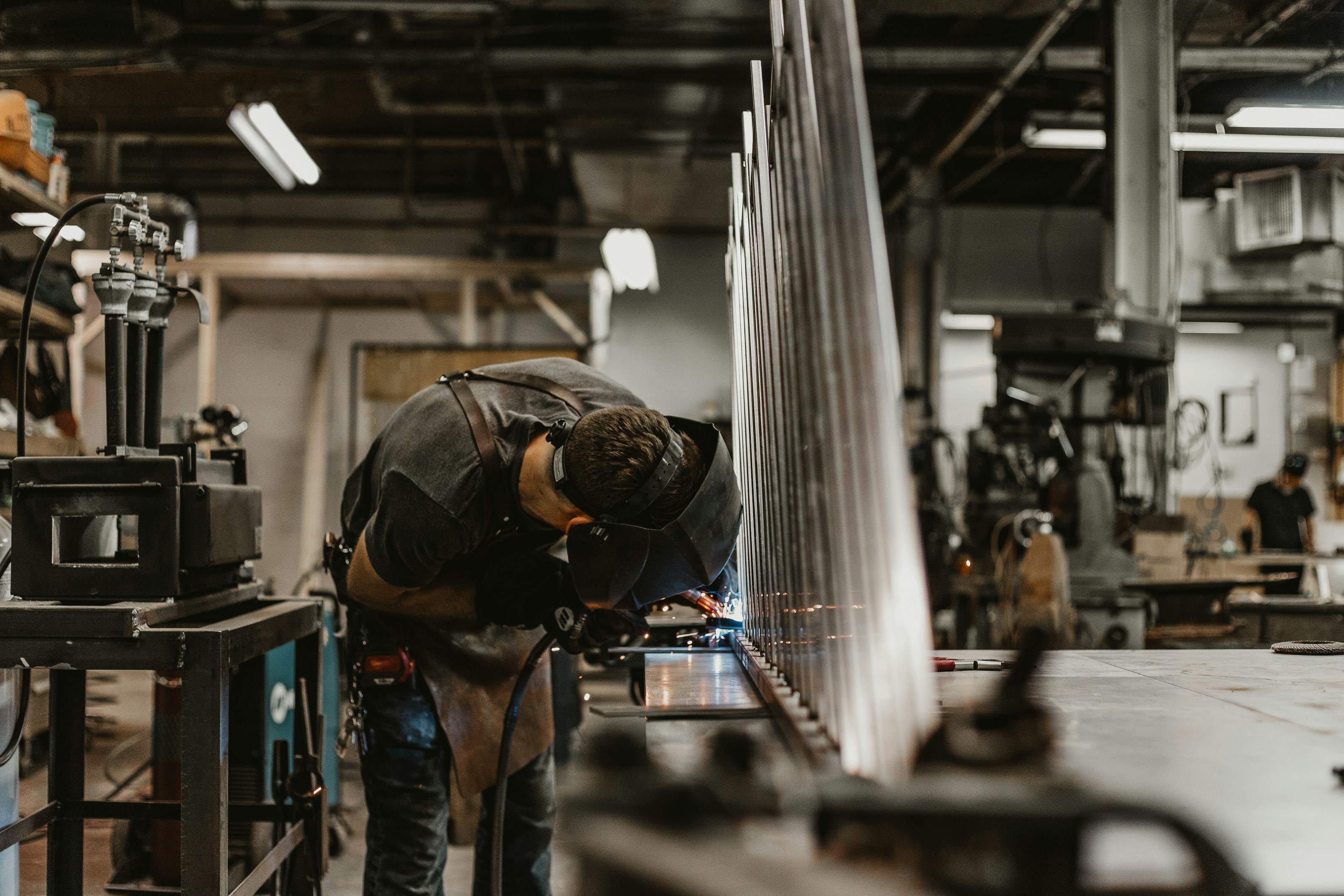
Sustainability and Environmental Considerations
Quality management systems will increasingly incorporate sustainability and environmental factors. Factories that reduce waste and adopt eco-friendly practices can benefit from cost savings and enhanced brand reputation. For instance, a factory's sustainability initiatives resulted in €50,000 in annual savings.
Customisation and Personalisation
Consumer demand for customised products is on the rise. Quality management systems must adapt to mass customisation, requiring advanced data analytics and real-time adjustments. Companies that successfully implement customisation strategies can achieve a 20% increase in customer loyalty.
Iwoscan: The Future of Quality Management
Iwoscan is at the forefront of these future trends in quality management. Its adaptability, AI-powered insights, and data-driven approach align perfectly with the evolving needs of the manufacturing industry.
Adapting to Industry 4.0
Iwoscan seamlessly integrates with Industry 4.0 principles, offering real-time data analysis and remote monitoring capabilities.
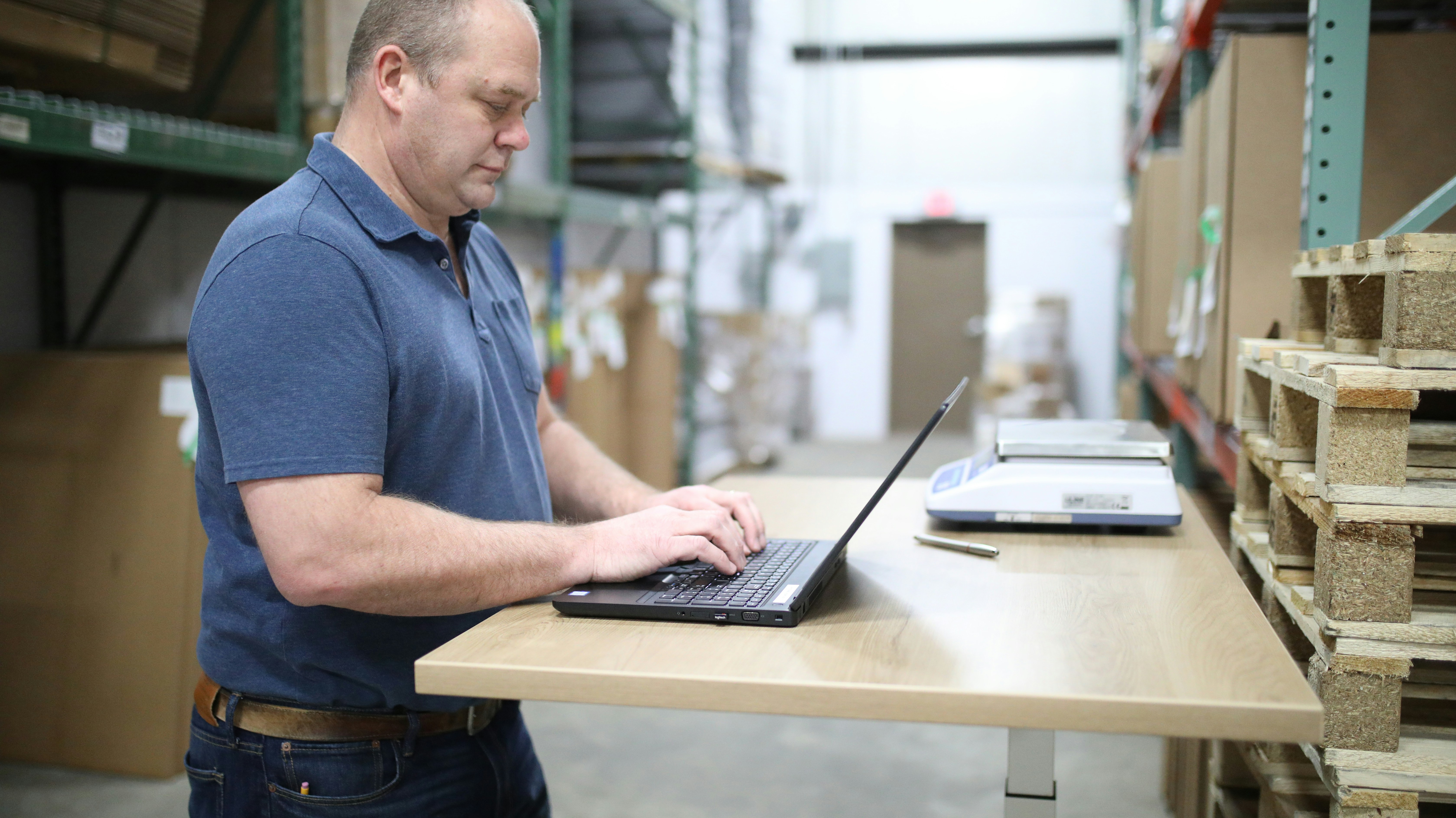
Advanced AI and Machine Learning
Iwoscan will remain at the forefront of AI and machine learning as they evolve, providing predictive quality assurance and automated defect detection.
Sustainability and Customisation
Iwoscan supports sustainability initiatives and customisation efforts by enabling real-time adjustments and data analysis to meet changing market demands.
Incorporating future trends in quality management and innovative solutions like Iwoscan will be crucial for factories looking to stay competitive and meet the market's evolving needs. By staying ahead of these trends, your factory can achieve higher product quality, operational efficiency, and sustainability, ultimately contributing to long-term success.
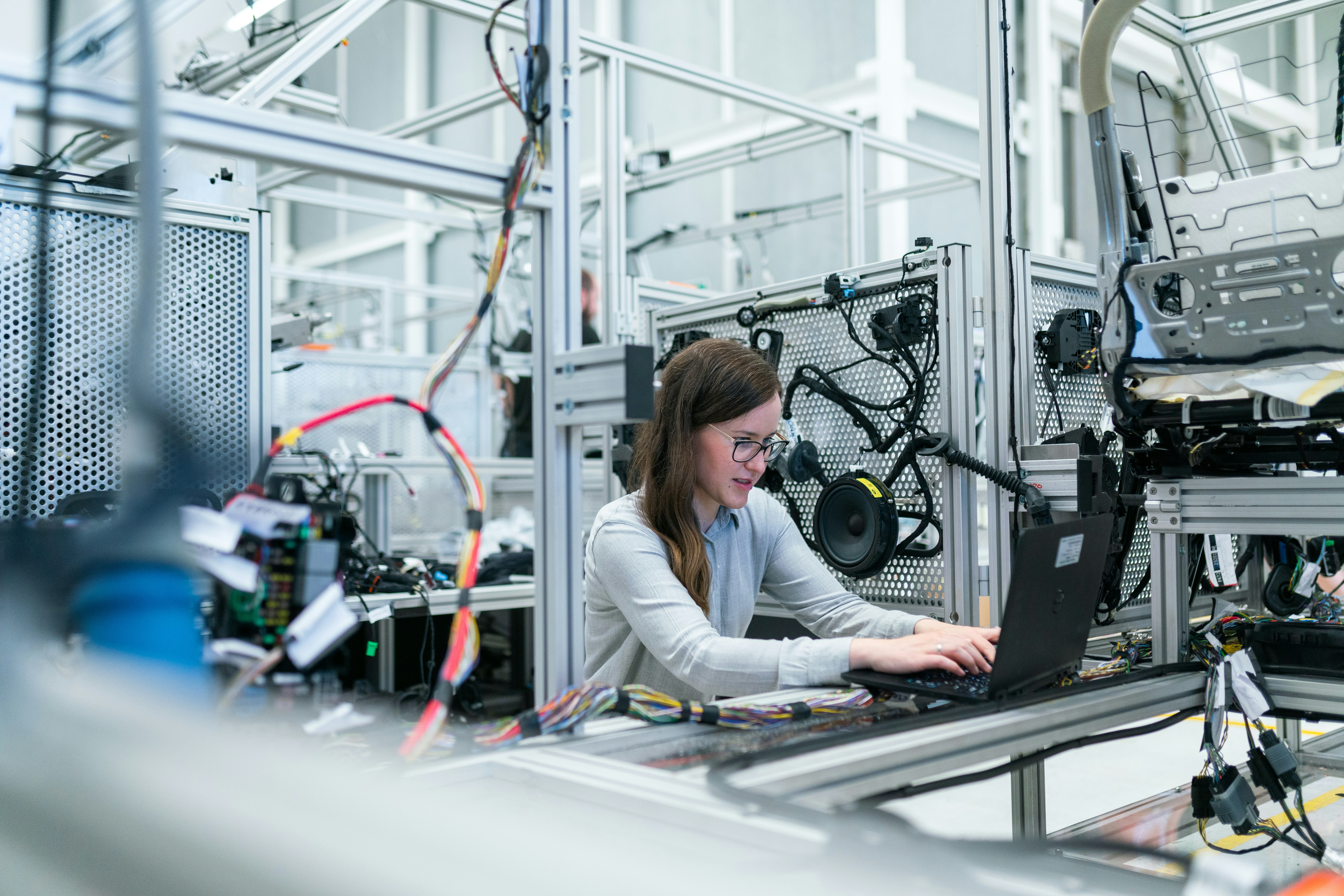
Elevating Your Quality Management System with Iwoscan
Maintaining impeccable product quality and operational efficiency is paramount in the ever-evolving manufacturing landscape. This comprehensive guide has explored the critical aspects of quality management systems, quality control devices, and quality assurance strategies, culminating in the innovative Iwoscan solution.
Optimising Quality Control and Assurance
The significance of a robust Quality Management System (QMS) in ensuring consistent product quality must be considered. Iwoscan, a cutting-edge QMS solution, has demonstrated its prowess in optimising quality control and assurance through real-time data analysis and AI-driven insights. By leveraging such advanced technology, factories can achieve a remarkable 25% reduction in production defects.
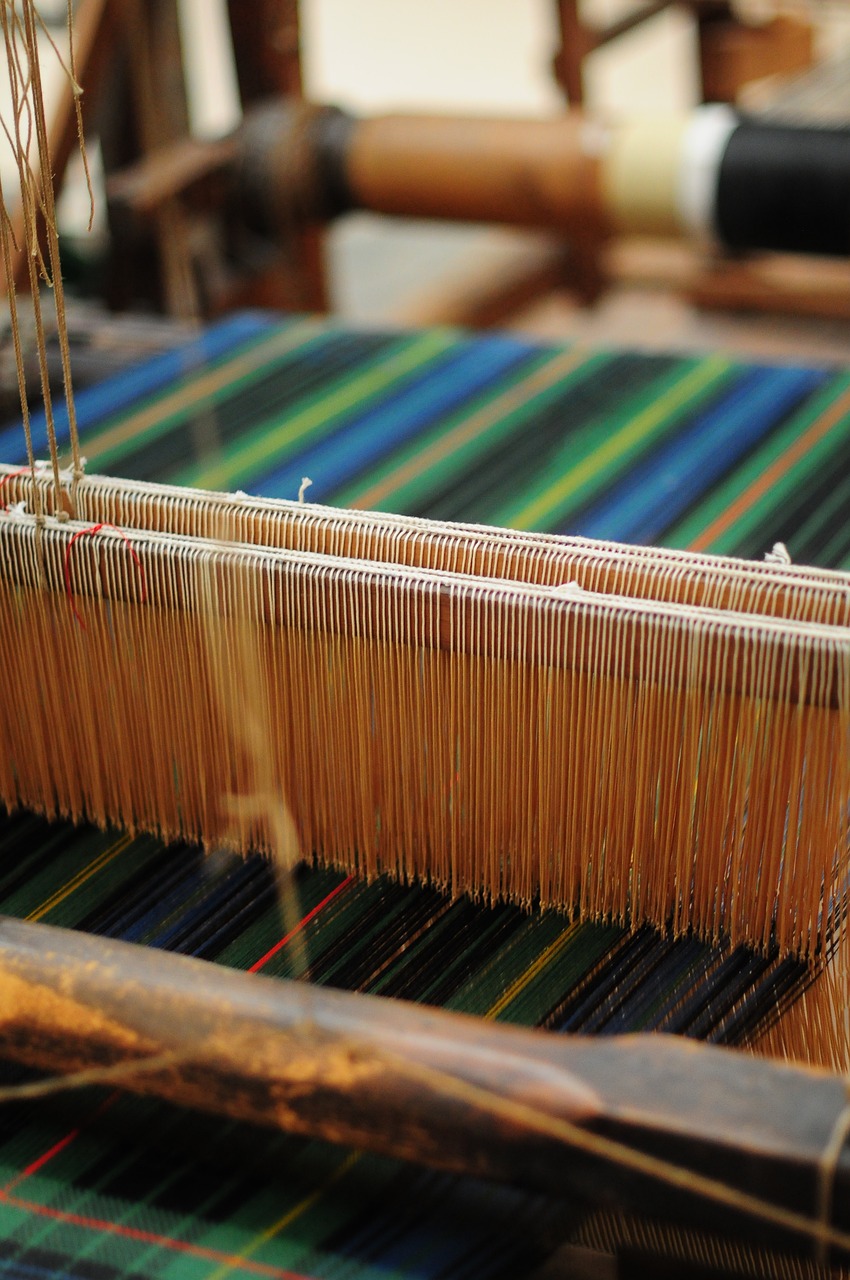
A Comprehensive Approach
Quality management is not limited to a single facet but encompasses a holistic approach. Popular quality control devices, including Coordinate Measuring Machines (CMMs), Non-Destructive Testing (NDT), and Vision Inspection Systems, have vital roles. However, integrating Iwoscan into your quality management system augments these devices with predictive quality assurance, cost-effective scalability, and seamless integration capabilities.
Preparing for the Future
Manufacturing is undergoing a profound transformation, and future trends in quality management are poised to shape the industry. Iwoscan is at the forefront, with its adaptability to Industry 4.0, advanced AI and machine learning capabilities, and support for sustainability and customisation. By embracing these trends, factories can remain agile and meet the dynamic demands of consumers.
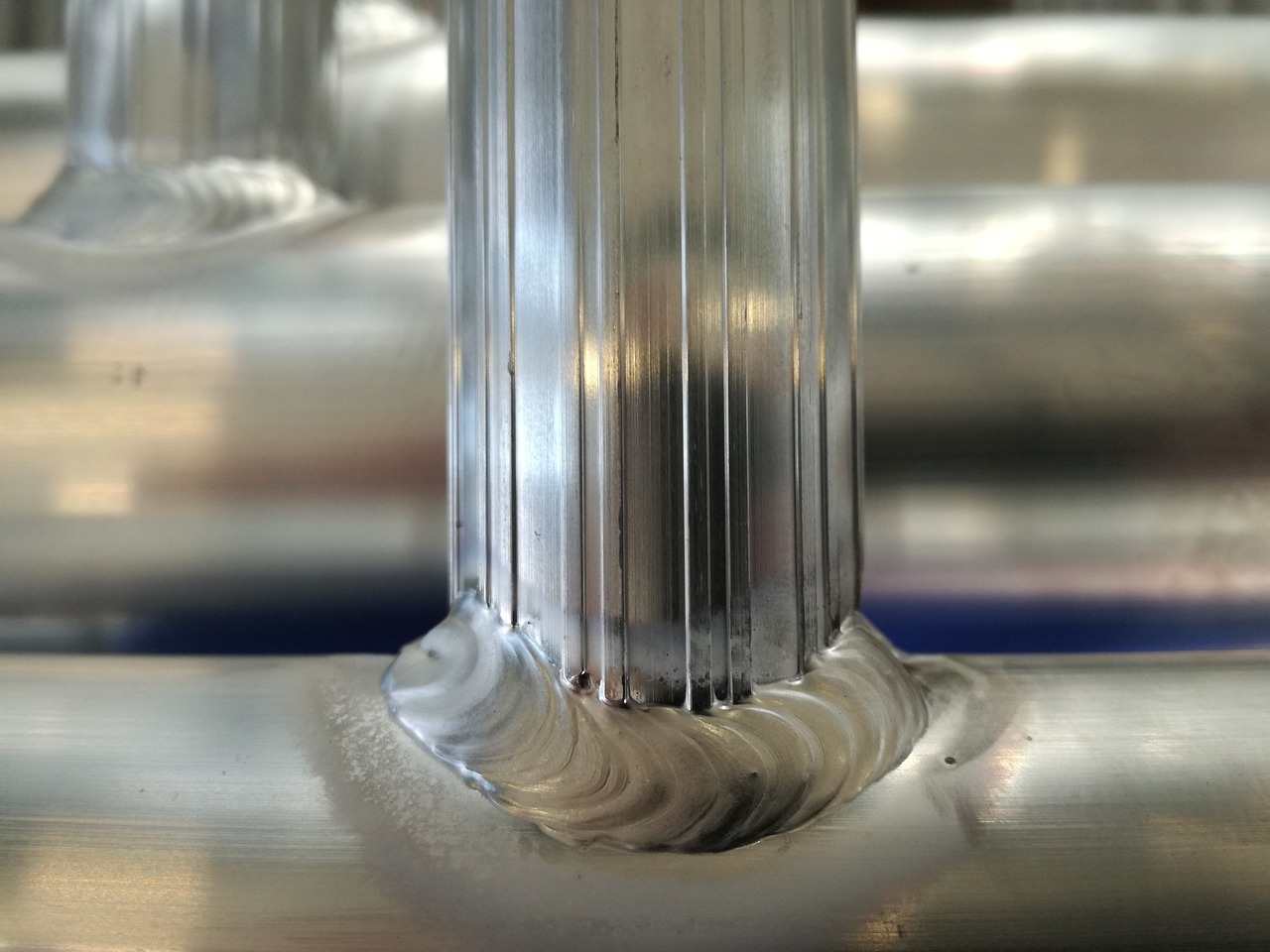
Sustainable Success
Ultimately, implementing quality management solutions and integrating Iwoscan are investments that yield sustainable success. The tangible benefits are evident in case studies and statistics, whether through reduced defects, improved process efficiency, or enhanced customisation. The cost savings achieved by Iwoscan users, amounting to thousands of euros annually, underscore the financial advantages of this innovative solution.
In conclusion, as you navigate the complexities of modern manufacturing, your choice of quality management systems and devices is pivotal. Iwoscan emerges as a comprehensive, forward-looking solution that meets today's quality standards and prepares your factory for the challenges and opportunities of tomorrow. By embracing Iwoscan, you can elevate your quality management system, reduce defects, enhance operational efficiency, and ensure sustainable success in the competitive manufacturing landscape.
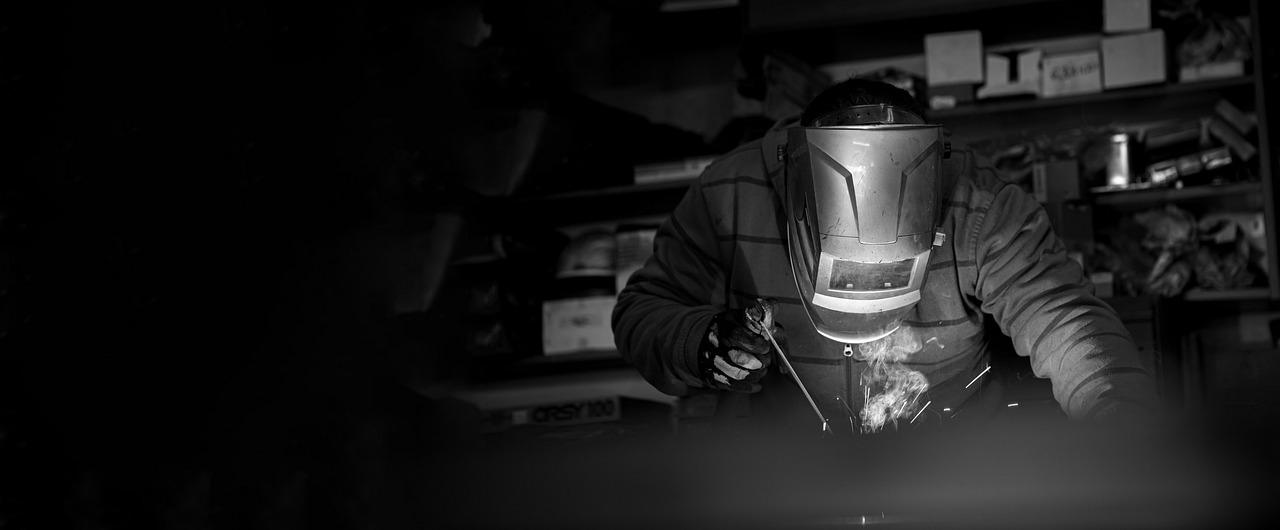
Comments
No comments yet!Add a Comment
You must be logged in to post a comment.