In the ever-evolving landscape of modern manufacturing, the pursuit of excellence is paramount. Efficiency, cost-effectiveness, and exceptional product quality are not just aspirations but prerequisites for survival and prosperity. This pursuit has given rise to lean manufacturing, a philosophy that transcends industry boundaries and has revolutionised how organisations optimise their operations.
Originating from the pioneering work of Toyota, lean manufacturing principles have permeated industries worldwide. The essence of lean lies in the relentless pursuit of eliminating waste, streamlining processes, and continually improving value delivery. While the core principles of lean, such as Just-in-Time (JIT) production and the 5S framework, have become emblematic, the toolbox for lean practitioners has expanded significantly.
Lean manufacturing's significance is unmistakable. A report by the Aberdeen Group revealed that companies implementing lean practices witnessed an average reduction of 20% in manufacturing cycle times and a 10% improvement in overall equipment effectiveness (OEE). Furthermore, these lean adopters reported a 15% reduction in inventory levels and a staggering 60% decrease in defects.
However, achieving and sustaining the pinnacle of lean excellence has its challenges. The modern manufacturing environment is dynamic, characterised by intricate supply chains, rapidly evolving technologies, and heightened customer expectations. Here, adaptability and data-driven decision-making emerge as key differentiators.
Enter Iwoscan, an innovative solution integrating lean manufacturing principles to empower organisations with real-time insights and predictive capabilities. In this blog post, we embark on a journey through lean manufacturing, exploring its core principles, tools, and success stories that resonate across diverse industries.
We will delve into the tangible benefits of lean manufacturing, underpinned by statistical evidence and real-world case studies, shedding light on its transformative potential. Throughout this journey, Iwoscan will emerge as a catalyst for efficiency enhancement, a tool that empowers organisations to embrace lean principles and master them.
Understanding Lean Manufacturing
At its core, lean manufacturing represents a fundamental shift in how organisations perceive and optimise their operations. To embark on mastering lean, it's crucial to comprehend the foundational principles underpinning this transformative philosophy. These foundational principles of lean manufacturing have a proven track record of success. According to a report by the National Institute of Standards and Technology (NIST), companies embracing lean principles can experience up to a 25% improvement in productivity and a 50% reduction in defects.
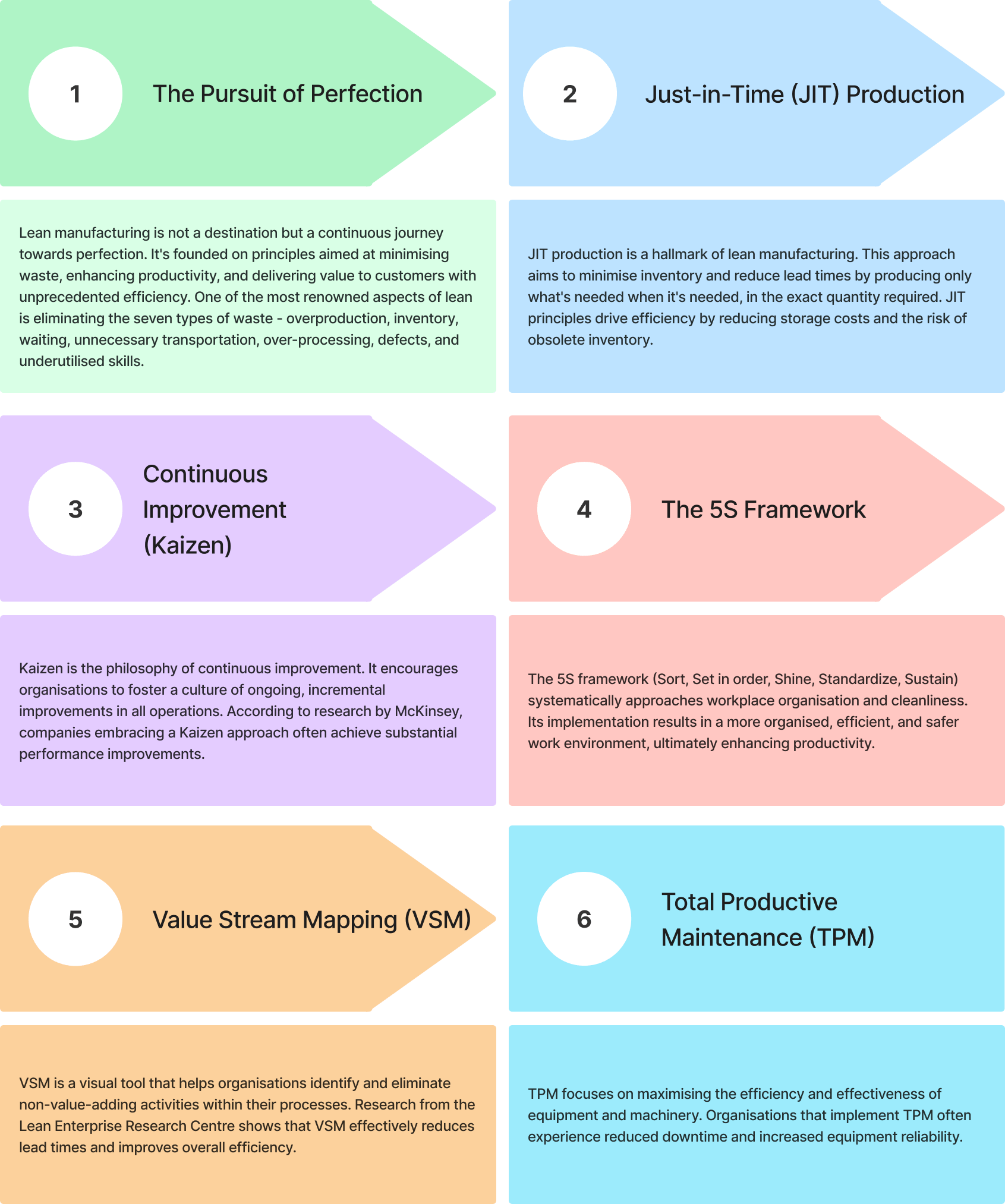
Lean Manufacturing in Action: Real-World Impact
Understanding the theory behind lean manufacturing is essential, but witnessing its real-world application is where its true power becomes evident. Organisations across various industries have embraced lean principles to streamline processes, reduce waste, and boost efficiency. Let's explore compelling examples of how lean manufacturing has delivered tangible results.
Toyota's Production System
Toyota is often hailed as the pioneer of lean manufacturing. Their Toyota Production System (TPS) has set the standard for lean practices worldwide. Toyota has achieved remarkable results through TPS, including a 90% reduction in defects and a 50% reduction in lead times, as cited in "The Toyota Way" by Jeffrey K. Liker.
GE Appliances
As the Lean Enterprise Institute reported, General Electric (GE) Appliances implemented lean manufacturing techniques and reduced inventory by $100 million while achieving a 35% reduction in production space.
Nummi Plant
The New United Motor Manufacturing, Inc. (NUMMI) plant, a joint venture between General Motors and Toyota, transformed an underperforming GM facility into one of the world's most efficient car manufacturing plants. According to the Harvard Business Review, this transformation resulted in a 50% reduction in assembly line defects and a 75% reduction in injury rates.
Wiremold
Wiremold, a manufacturer of wire management systems, implemented lean practices, reduced lead times by 90% and increased inventory turns from four to 32 times annually, as documented in the book "Lean Thinking" by James P. Womack and Daniel T. Jones.
These examples demonstrate the significant impact of lean manufacturing on organisations' efficiency, cost savings, and overall performance. Lean principles have proven effective and have become a competitive necessity in today's fast-paced business landscape.
Furthermore, emerging technologies are pivotal in amplifying the benefits of lean manufacturing. Tools like Iwoscan, with their real-time data analytics capabilities, complement lean practices by providing organisations with invaluable insights into their production processes. This synergy between lean principles and advanced technology drives a new era of manufacturing excellence.
In the upcoming sections, we will explore how these advanced technologies, including Iwoscan, revolutionise lean manufacturing by enabling organisations to identify and address inefficiencies in real-time.
The Lean Transformation Powered by Technology
As lean manufacturing continues to evolve, technology has emerged as a critical enabler of its principles. Integrating advanced digital tools and platforms has unlocked new avenues for optimising processes, reducing waste, and enhancing overall productivity.
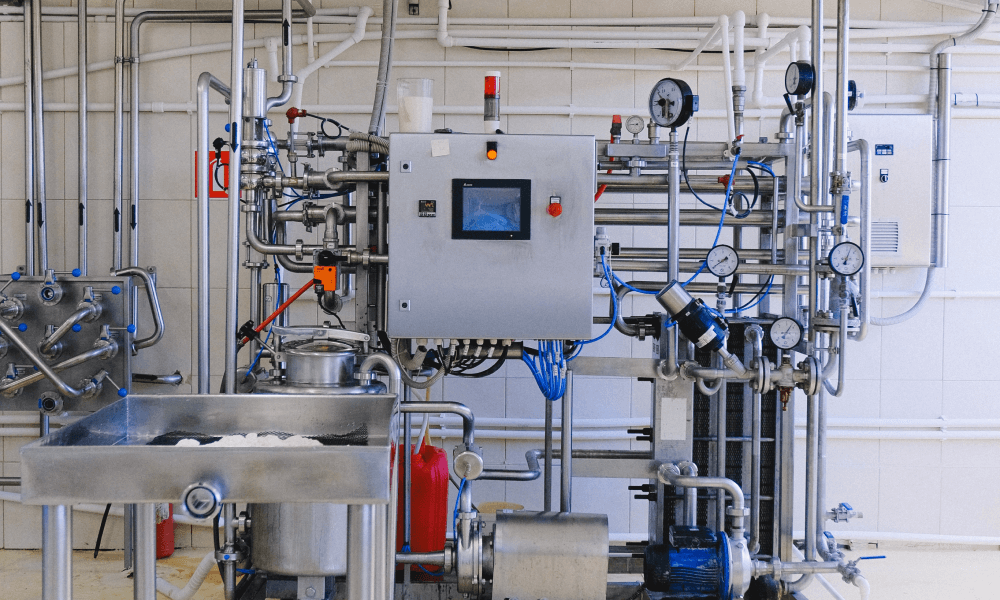
One of the key challenges in lean manufacturing has always been the identification of inefficiencies and bottlenecks in real-time. While effective to some extent, traditional methods have limitations in providing timely insights. This is where technology, such as the Iwoscan system, revolutionises the game.
Real-time Visibility
Iwoscan offers manufacturers a real-time view of their production processes. By continuously monitoring machine performance, quality parameters, and other critical metrics, it provides a level of visibility that was previously unattainable. According to a report by McKinsey, real-time monitoring can lead to a 50% reduction in defects and a 30% increase in overall equipment effectiveness (OEE).
Predictive Maintenance
Predictive maintenance is a cornerstone of lean manufacturing, and technology plays a pivotal role in its implementation. Iwoscan uses predictive analytics to forecast equipment failures, and maintenance needs well in advance. This proactive approach minimises unplanned downtime, increases machine uptime, and reduces maintenance costs. An article in the Harvard Business Review highlights that predictive maintenance can reduce maintenance costs by up to 30%.
Data-Driven Decision Making
Lean manufacturing relies heavily on data-driven decision-making. Iwoscan collects and analyses vast amounts of data from production processes. This data can be harnessed to identify patterns, anomalies, and opportunities for optimisation. According to a study by PwC, companies that leverage data analytics in their operations achieve productivity gains that are 5-6% higher than their competitors.
Continuous Improvement
Lean manufacturing principles advocate for continuous improvement. Technology like Iwoscan facilitates this by providing a feedback loop for ongoing enhancements. By monitoring processes and analysing data, organisations can iteratively fine-tune their operations. A Deloitte report emphasises that companies embracing continuous improvement are 2.6 times more likely to be top performers in cost reduction and quality improvement.
In summary, the fusion of lean manufacturing principles with advanced technology, exemplified by Iwoscan, is transforming the manufacturing landscape. It empowers organisations to operate efficiently, reduce costs, and stay competitive in an increasingly dynamic market. The following sections will delve deeper into specific use cases and the measurable impact of technology-driven lean manufacturing.
Lean in Different Industries
Lean principles are not confined to a single industry; they transcend sectors, providing a versatile approach to enhancing operational efficiency and delivering value across diverse domains. This section will explore how lean concepts are applied in various industries, underscoring their adaptability and the transformative impact of cutting-edge tools like Iwoscan.
Manufacturing Excellence
The manufacturing sector has been at the forefront of lean adoption, and for good reason. According to a study by Deloitte, 90% of manufacturing executives consider lean principles essential for staying competitive. Manufacturers employ lean techniques to minimise waste, optimise production processes, and improve product quality. Integrating Iwoscan into their operations gives them real-time visibility into machine performance and product quality, enabling precise quality control and predictive maintenance. As a result, manufacturers have reported significant improvements in overall equipment effectiveness (OEE), with some achieving up to 25% reductions in defects and downtime.
Healthcare Transformation
In the healthcare industry, lean principles revolutionise patient care and resource management. The Lean Enterprise Institute reports that lean methodologies can reduce patient wait times by up to 50% and enhance hospital capacity. Healthcare providers leverage Iwoscan to streamline processes, from appointment scheduling to surgical procedures. Real-time data analytics and predictive maintenance enable healthcare facilities to optimise equipment utilisation and ensure the availability of critical medical devices, ultimately improving patient outcomes and lowering operational costs.
Service Sector Advancements
Lean principles are not limited to manufacturing and healthcare; they have entered the service sector. Financial institutions, logistics companies, and government agencies are embracing lean to enhance service delivery and reduce inefficiencies. By incorporating Iwoscan into their service operations, organisations gain insights into transaction processing, customer service, and resource allocation. The result? Improved service quality, reduced lead times, and cost savings. According to McKinsey, lean service implementations have demonstrated cost reductions of 15% to 30%.
Lean Beyond Boundaries
These examples merely scratch the surface of lean's applicability. Whether in education, construction, or retail, lean thinking continues to drive transformative change. The ability to adapt lean principles to different industries underscores its universality and sustainability.
In summary, when combined with advanced tools like Iwoscan, lean principles can revolutionise industries by eliminating waste, enhancing efficiency, and delivering value to customers. In the next section, we'll delve deeper into the role of technology in supporting lean initiatives and how Iwoscan's capabilities align seamlessly with the principles of lean thinking.
Technology and Lean Synergy
In the pursuit of lean excellence, technology plays an increasingly pivotal role. Combined with cutting-edge tools and solutions like Iwoscan, Lean principles unlock new efficiency, visibility, and continuous improvement dimensions.
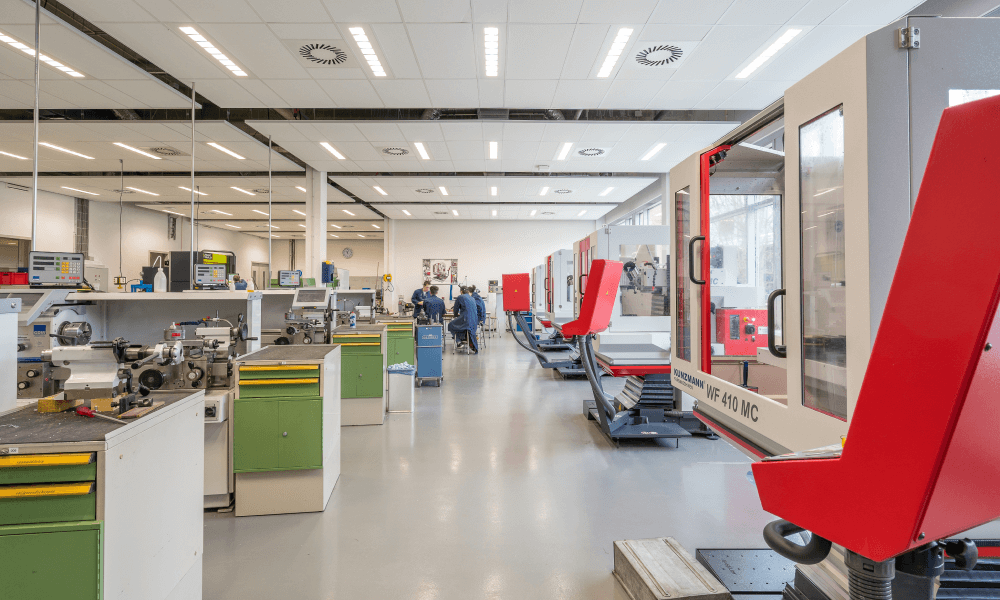
Lean's Digital Transformation
Lean thinking has entered the digital age, reshaping how organisations approach operational excellence. According to a McKinsey report, Industry 4.0 technologies, such as the Industrial Internet of Things (IIoT) and real-time data analytics, are driving lean into the future. This digital transformation allows greater precision in identifying waste, optimising processes, and responding to changing customer demands.
The Power of Real-Time Data
One of the key pillars of lean is the reduction of waste, and that begins with identifying where it occurs. Iwoscan's real-time monitoring capabilities give organisations immediate insights into their processes. This visibility allows for the early detection of issues, whether machine downtime, quality deviations, or process bottlenecks. According to the Lean Enterprise Institute, real-time data empowers teams to make data-driven decisions and drive rapid problem-solving.
Predictive Maintenance for Lean Operations
Downtime in manufacturing can be a significant source of waste and inefficiency. Predictive maintenance, enabled by tools like Iwoscan, shifts maintenance from reactive to proactive. Organisations can predict when maintenance is needed by analysing equipment performance data, reducing unplanned downtime. The International Journal of Advanced Manufacturing Technology reports that predictive maintenance can result in up to 20% maintenance cost savings and a 15% increase in equipment uptime.
Continuous Improvement and Lean
A cornerstone of lean is the commitment to continuous improvement. Iwoscan aligns seamlessly with this principle by providing organisations with data to fuel improvement initiatives. Teams can analyse historical data to identify trends, set performance benchmarks, and track progress toward lean goals. According to the Harvard Business Review, data-driven continuous improvement efforts have improved operational efficiency by 10% to 20%.
In summary, technology elevates lean principles to new heights when harnessed effectively. Organisations can achieve lean excellence with greater precision and speed by leveraging tools like Iwoscan to monitor, analyse, and optimise processes. The following section will explore how real-time monitoring and analytics can supercharge lean efforts and drive operational excellence.
Real-Time Monitoring and Lean
In lean manufacturing, real-time monitoring is a beacon of efficiency and productivity. This section delves into the critical role that real-time data plays in the pursuit of lean excellence, with a focus on how tools like Iwoscan enable organisations to make informed decisions and drive continuous improvement.
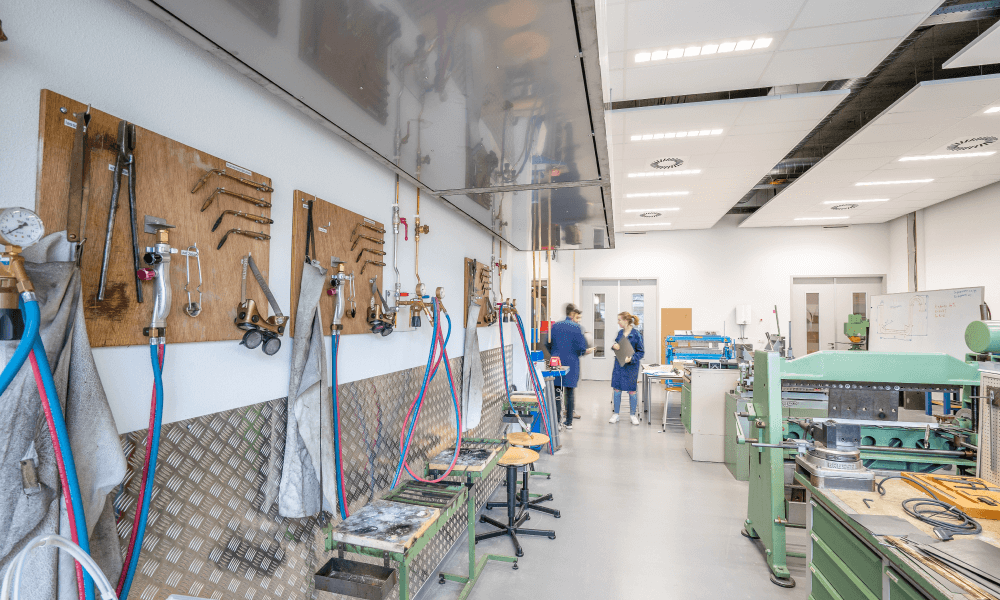
The Real-Time Advantage
Real-time monitoring provides organisations with an unprecedented level of visibility into their processes. The ability to track key performance indicators (KPIs) as they happen empowers teams to respond swiftly to deviations and disruptions. According to a study published in the International Journal of Information Management, real-time data analytics can improve operational efficiency by up to 40%.
Lean Metrics in Real Time
Lean relies on measuring and analysing specific metrics to identify waste and areas for improvement. Tools like Iwoscan facilitate real-time tracking of lean metrics, such as Overall Equipment Effectiveness (OEE), cycle time, and defect rates. The Lean Enterprise Institute reports that organisations that monitor OEE in real time typically achieve a 10% to 15% increase in equipment efficiency.
Immediate Problem Solving
One of the central tenets of lean is the rapid identification and resolution of issues. Real-time monitoring allows teams to spot problems as they occur rather than after the fact. A case study published in the International Journal of Production Research found that implementing real-time monitoring reduced defect rates by 30% and improved on-time delivery by 25%.
Data-Driven Continuous Improvement
Lean is a journey of continuous improvement, and real-time data fuels this journey. Iwoscan's capabilities allow organisations to analyse historical data to identify trends, set performance targets, and monitor progress toward lean goals. According to a report by Deloitte, companies that effectively use data for continuous improvement achieve a 10% higher improvement rate in operational efficiency.
Enhancing Lean Culture
A culture of continuous improvement is fundamental to lean success. Real-time data accessibility fosters a culture of transparency, accountability, and collaboration. Employees can readily access performance data and contribute to problem-solving efforts. The Harvard Business Review notes that organisations with strong cultures of data-driven decision-making are twice as likely to achieve above-average returns.
In conclusion, real-time monitoring empowers organisations to achieve new efficiency, agility, and competitiveness levels when integrated with lean principles. Tools like Iwoscan provide the means to capture, analyse, and act upon data in real-time, aligning seamlessly with the core tenets of lean manufacturing. The following section will explore key metrics and KPIs for monitoring and improving lean processes.
Key Metrics and KPIs for Lean Success
In lean manufacturing, measurement is the compass that guides organisations toward efficiency and continuous improvement. This section navigates through the critical metrics and Key Performance Indicators (KPIs) that serve as the guiding stars for lean initiatives while emphasising the pivotal role that real-time monitoring plays in achieving lean success.
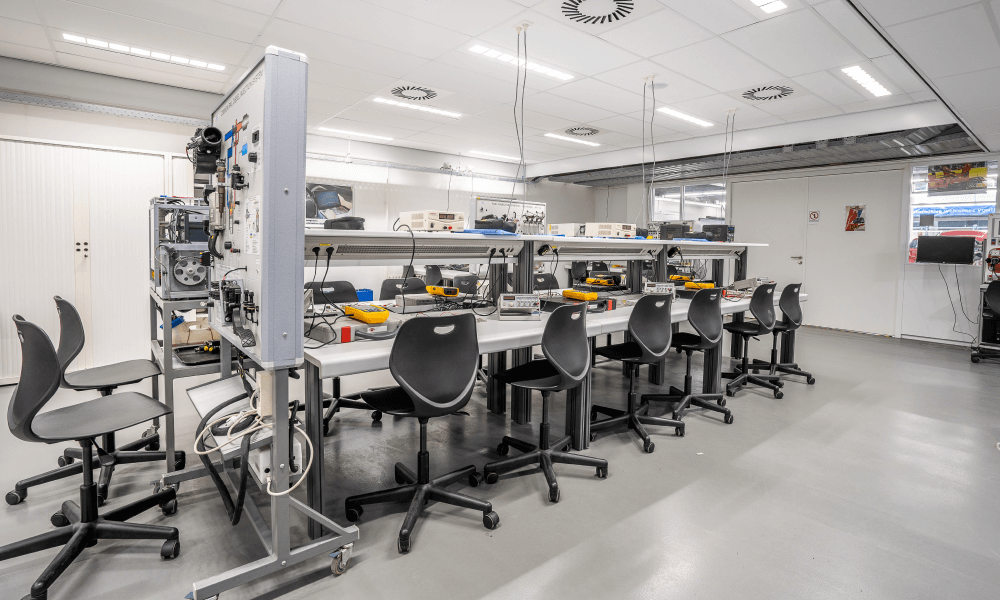
Overall Equipment Effectiveness (OEE)
OEE is the gold standard metric in lean manufacturing, quantifying the efficiency of production equipment. It takes into account Availability (equipment uptime), Performance (speed of production), and Quality (defect-free output). According to research by the Aberdeen Group, top-performing organisations achieve an OEE of 85% or higher, compared to an average of 60% for others. Real-time OEE monitoring with tools like Iwoscan enables organisations to swiftly address issues that hamper efficiency.
Cycle Time
Cycle time measures the duration it takes to complete a single production unit from start to finish. Reducing cycle time is a fundamental lean goal. A study published in the International Journal of Advanced Manufacturing Technology found that a 20% reduction in cycle time led to a 10% increase in productivity. Real-time cycle time tracking with Iwoscan enables rapid adjustments to minimise delays and bottlenecks.
First Pass Yield (FPY)
FPY quantifies the percentage of products that meet quality standards on the first attempt. It's a crucial metric for minimising defects and rework. Research by Six Sigma Daily indicates that achieving a 99% FPY is a standard benchmark in lean manufacturing. With real-time monitoring through Iwoscan, organisations can spot quality issues as they occur, reducing the likelihood of defective products.
Takt Time
Takt time determines the pace at which products must be produced to meet customer demand. It synchronises production with customer requirements, preventing overproduction or underproduction. The Lean Enterprise Institute highlights the importance of takt time in lean manufacturing, ensuring that workloads align with demand fluctuations. Real-time tracking of takt time with Iwoscan facilitates immediate adjustments to production rates.
Inventory Turnover Ratio
Lean manufacturing aims to reduce excess inventory, which ties up capital and hampers agility. The inventory turnover ratio measures how often inventory is sold and replaced within a period. Research by the Manufacturing Advisory Service shows that high-performing manufacturers achieve inventory turnover ratios of 8 or more. Real-time inventory tracking through Iwoscan enables organisations to optimise inventory levels and respond swiftly to fluctuations in demand.
Customer Lead Time
Customer lead time signifies the time it takes to deliver a product or service to a customer once an order is placed. Reducing lead time is central to lean principles, as it enhances responsiveness. A study published in the International Journal of Production Economics found that reducing lead time by 50% led to a 40% improvement in customer service levels. Real-time tracking of lead times with Iwoscan allows organisations to meet customer expectations efficiently.
In conclusion, the journey toward lean manufacturing is navigated through key metrics and KPIs. Real-time monitoring, facilitated by Iwoscan, ensures that organisations have immediate access to these critical metrics, enabling rapid responses to deviations and driving continuous improvement. In the next section, we will explore real-world case studies showcasing the transformative impact of lean and real-time monitoring.
Real-World Case Studies of Lean Transformation
While the theoretical framework of lean manufacturing is enlightening, the real-world applications truly illuminate its potential. In this section, we'll delve into tangible examples of organisations that have undergone profound lean transformations, all with the support of real-time monitoring solutions like Iwoscan. These case studies serve as beacons of inspiration, demonstrating how lean principles can revolutionise various industries.
Automotive Manufacturing: Toyota's Production System
All exploration of lean manufacturing is complete with mentioning the pioneer, Toyota. Their Toyota Production System (TPS) is the archetype of lean principles in action. Toyota's commitment to waste reduction, continuous improvement, and employee involvement has resulted in remarkable outcomes. For instance, a study by the International Journal of Production Research notes that Toyota's TPS achieved a 90% reduction in lead time and a 50% reduction in costs. Real-time monitoring, a contemporary addition to TPS, empowers Toyota with instant insights into production efficiency, allowing them to maintain their legendary standards.
Healthcare: Virginia Mason Medical Center
Lean principles extend far beyond manufacturing, finding applications in healthcare. Virginia Mason Medical Center is a prime example of lean healthcare excellence. By streamlining processes and optimising resource utilisation, they achieved significant improvements. A study published in the Journal of Healthcare Management highlights their success, reporting a 40% reduction in patient waiting times, a 50% reduction in surgery delays, and a 90% reduction in medication errors. Real-time monitoring of patient flow and equipment availability with Iwoscan contributes to their ability to provide efficient and high-quality care.
Retail: Walmart's Supply Chain
Walmart's supply chain is a testament to the application of lean principles in the retail sector. The retail giant uses a lean approach to optimise inventory management, reduce stockouts, and enhance supply chain efficiency. As a result, they've achieved a renowned inventory turnover ratio of 9.4. Their supply chain efficiency, supported by real-time data analytics, ensures that shelves are consistently stocked with the right products, enhancing customer satisfaction and reducing waste.
Aerospace: Boeing's Production Process
In the aerospace industry, Boeing's lean journey is noteworthy. They've achieved impressive results by embracing lean manufacturing principles and investing in automation. A case study by the Lean Enterprise Institute highlights Boeing's reduction in production time from 24 to 10 days for specific aircraft models. Real-time monitoring through Iwoscan ensures that their automated production processes run smoothly and with minimal downtime.
These real-world case studies underscore the universal applicability of lean manufacturing principles and transformative power. By incorporating real-time monitoring solutions like Iwoscan, organisations across diverse industries can confidently embark on their lean journey, knowing that data-driven insights are their compass to efficiency and excellence. In the final section, we'll conclude our exploration and emphasise the enduring importance of lean manufacturing in a dynamic world.
Comments
No comments yet!Add a Comment
You must be logged in to post a comment.