In the ever-evolving manufacturing landscape, where precision, productivity, and profitability reign supreme, achieving peak operational efficiency has become a non-negotiable imperative. In this pursuit, a formidable adversary threatens to disrupt even the most well-oiled production machinery downtime. Whether planned or unplanned, the scourge of downtime can bring manufacturing processes to a grinding halt, resulting in substantial losses in revenue, productivity, and customer trust. The numbers tell a compelling story. A recent study conducted by the Manufacturing Enterprise Solutions Association International (MESA) revealed that unplanned downtime in manufacturing could cost companies up to €260,000 per hour, depending on the industry. Furthermore, the study found that, on average, manufacturing companies experience 800 hours of downtime annually, equating to a jaw-dropping potential loss of €208 million. These staggering figures underscore the urgency of tackling the downtime challenge head-on. In this blog post, we embark on a journey into the heart of manufacturing efficiency, focusing on the critical role of downtime control. The ability to minimise, manage, and mitigate downtime is not merely a goal; it's a lifeline for manufacturers seeking to optimise their operations. But we don't stop there. We introduce a game-changing ally in the battle against downtime - Iwoscan. Iwoscan is not just another technology solution; it's a revolutionary approach to downtime control that empowers manufacturers with real-time insights, predictive maintenance capabilities, and data-driven strategies.
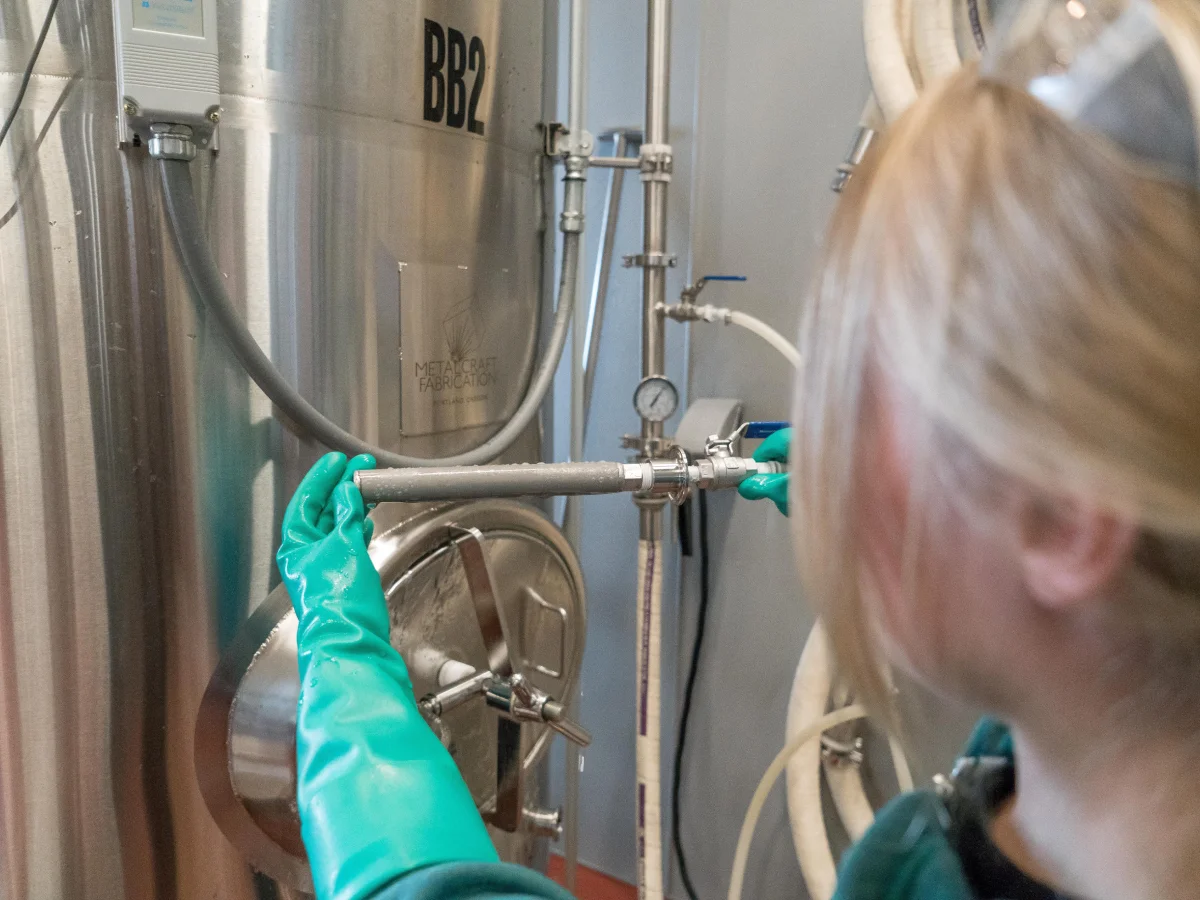
Understanding Downtime Control
To achieve manufacturing efficiency, it's paramount first to grasp the intricacies of downtime and its impact on operations. Downtime can be broadly categorised into two main types: planned and unplanned. While planned downtime is typically scheduled for maintenance, upgrades, or changeovers, unplanned downtime is the proverbial wrench in the gears, often caused by unexpected equipment failures, breakdowns, or other operational disruptions.
The statistics surrounding downtime are sobering. According to a survey by Vanson Bourne, 82% of companies experience at least one unplanned downtime incident annually. These incidents can last anywhere from a few hours to several days, resulting in significant financial losses and damage to a company's reputation and customer relationships.
To put the financial impact of downtime into perspective, the Aberdeen Group reported that, on average, unplanned downtime can cost an organisation €260,000 per hour. For manufacturers, this translates to colossal losses, which, as mentioned earlier, can reach up to €208 million annually.
Furthermore, planned downtime, although necessary for maintenance and updates, can also present challenges. Improving scheduling and execution can extend planned downtime, leading to production delays and increased costs. Hence, effective downtime control entails minimising unplanned downtime and optimising planned downtime for maximum efficiency.
At the core of downtime control lies the identification of root causes. Downtime events can result from equipment failures, lack of preventive maintenance, supply chain disruptions, and human error. Understanding these causes is essential for implementing effective strategies to mitigate downtime's impact.
In the following sections of this blog post, we will explore strategies, technologies, and real-world examples that shed light on how downtime control can be achieved and enhanced. The journey toward manufacturing efficiency begins with a comprehensive understanding of downtime's complexities and consequences.
Downtime Classification and Impact
In the intricate manufacturing realm, downtime is a formidable adversary, capable of disrupting operations and sapping resources. To combat this adversary effectively, it's crucial to understand downtime not as a monolithic force but as a multifaceted phenomenon with various classifications, each with its distinct impact on production.
Planned Downtime
Planned downtime, often referred to as scheduled maintenance, represents those carefully orchestrated pauses in production. While planned downtime is intentional, it's not immune to challenges. The key is to minimise the impact of planned downtime on productivity. Regular maintenance, equipment upgrades, and changeovers fall under this category. The effect of planned downtime is mitigated by efficient scheduling, quick execution, and meticulous planning. When managed effectively, planned downtime can optimise equipment performance and extend its lifespan, ultimately benefiting overall productivity.
Unplanned Downtime
Unplanned downtime, the more notorious sibling, strikes without warning. It encompasses a range of disruptive events, from equipment breakdowns to supply chain interruptions and human errors. The impact of unplanned downtime can be severe, resulting in production delays, increased costs, and even damage to a company's reputation. It's the relentless nemesis of efficiency, and minimising its occurrence and impact is paramount.
Minor Stops and Short Stops
Beyond the broad categories of planned and unplanned downtime, there are nuanced classifications worth exploring. Minor and short stops refer to brief interruptions in production, often lasting a few minutes or seconds. While inconsequential, these micro-downtimes can accumulate and collectively impact overall equipment efficiency (OEE). Identifying and addressing the root causes of minor stops can lead to significant productivity gains.
Setup and Changeover Time
Setup and changeover times are a unique form of planned downtime, where machinery is reconfigured to accommodate different products or processes. Efficient setup and changeover procedures can significantly reduce downtime's impact, enabling manufacturers to adapt swiftly to changing demands.
In the manufacturing landscape, downtime classification is essential because it informs strategies for mitigation and control. It empowers manufacturers to allocate resources effectively, prioritise maintenance efforts, and implement preventive measures. The ultimate goal is to minimise downtime's impact and unlock the full potential of manufacturing efficiency. This journey towards efficient downtime control is not merely a pursuit of operational excellence; it's a fundamental necessity in today's competitive manufacturing landscape.
Common Causes of Downtime
In pursuing manufacturing efficiency, it is imperative to delve into the multifaceted landscape of downtime's common causes. In all its disruptive glory, Downtime can be traced back to several key factors, each wielding the potential to halt production, strain resources, and impede progress. We must dissect these factors with a fine-toothed comb to optimise downtime control and appreciate their far-reaching consequences.
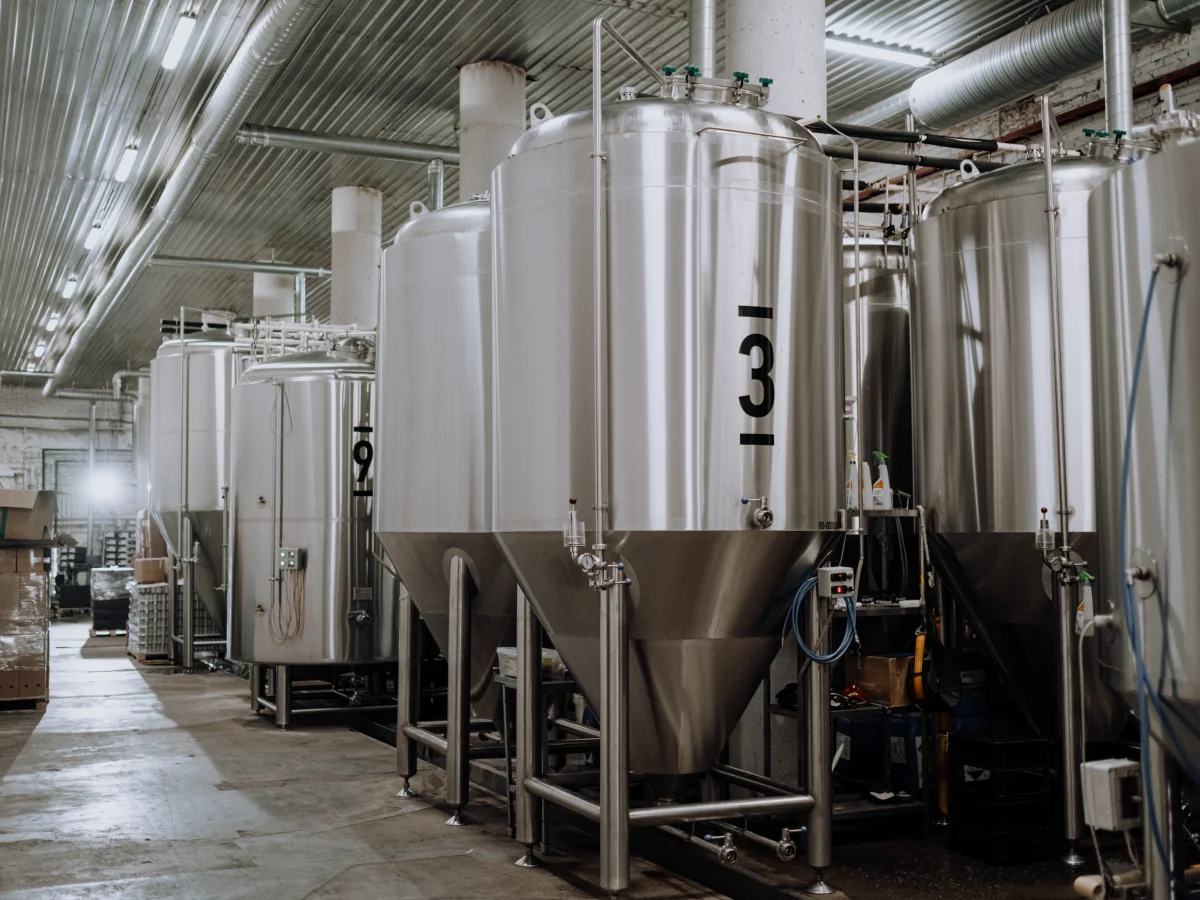
Equipment Failures: A Persistent Foe
At the heart of many downtime episodes lies the unforgiving spectre of equipment failures. Equipment failures can bring operations to an abrupt standstill, be it a crucial machine on the production line or a critical component. Bearings seize, motors burn out, and belts snap, sending ripples of disruption throughout the manufacturing process.
Preventive Maintenance Neglect
Equipment failures are a leading cause of unplanned downtime in manufacturing. These failures can range from minor glitches to catastrophic breakdowns, each impacting production. According to a study by Plant Engineering, equipment failure accounts for nearly 42% of all downtime incidents. The consequences can be costly, whether a malfunctioning motor, a faulty sensor, or worn-out components. Maintenance is an inconvenience, a temporary pause in the relentless march of production. However, neglecting preventive maintenance is akin to playing a high-stakes game of chance. Over time, wear and tear accumulate, and equipment becomes increasingly susceptible to breakdowns without regular check-ups and servicing.
Supply Chain Disruptions: The Domino Effect
Manufacturing relies on a delicate dance of supply and demand; any disruption in this intricate choreography can lead to downtime. Supply chain disruptions, such as delays in raw material deliveries, can send shockwaves through the production process, causing delays and idle machinery. The COVID-19 pandemic was a stark reminder of how vulnerable supply chains can be. An Institute for Supply Management survey found that nearly 75% of companies reported supply chain disruptions due to the pandemic.
Human Error: The Unpredictable Variable
No matter how advanced manufacturing technology becomes, the human element remains a potential source of downtime. Human mistakes can trigger downtime events, whether an operator is inputting incorrect settings, a technician overlooking maintenance procedures, or an assembly line worker making an error. Training, supervision, and error-reduction strategies are vital to mitigate this risk. Human error can lead to costly downtime incidents through operational mistakes, misconfigurations, or oversight.
Real-World Consequences: By the Numbers
To grasp the true gravity of these downtime causes, let's turn to statistics and real-world examples. According to industry reports, equipment failures account for approximately 42% of unplanned downtime incidents. Neglected preventive maintenance contributes to nearly 23% of such incidents. Supply chain disruptions, including raw material shortages, account for approximately 17% of unplanned downtime.
The financial repercussions of these downtime causes are nothing short of staggering. The manufacturing industry faces losses of billions of dollars annually due to unplanned downtime. For instance, a global food processing company reported losses exceeding €10 million annually due to equipment failures alone.
Understanding these common causes of downtime is the first step in developing effective downtime control strategies. It is essential to identify the root causes specific to your operations and implement measures to mitigate their impact. In the subsequent sections, we'll explore strategies, technologies, and real-world examples that show how downtime control can be achieved and enhanced. The journey toward manufacturing efficiency begins with a comprehensive understanding of downtime's complexities and consequences.
The Benefits of Effective Downtime Management
Now that we've uncovered the typical culprits behind downtime in manufacturing, it's time to explore why efficient downtime management is imperative. Downtime reduction isn't just a buzzword; it's a strategic move that can significantly impact a manufacturing operation's bottom line.
.png)
Cost Savings
Downtime comes at a steep cost. According to a report by the Aberdeen Group, unplanned downtime can cost an organisation up to €260,000 per hour on average. This staggering figure encompasses repairing equipment and the indirect costs of halted production, missed orders, and potential overtime payments to catch up. By implementing effective downtime management, manufacturers can harness substantial cost savings.
Increased Productivity
Reducing downtime translates directly into increased productivity. When machines and processes are running as intended, production throughput is maximised. Reducing unexpected stoppages allows operators to maintain a steady workflow, ultimately boosting overall output. An analysis by McKinsey & Company revealed that productivity improvements achieved through downtime reduction can increase manufacturing output by up to 20%.
Enhanced Equipment Lifespan
Regular preventive maintenance, a key component of downtime management, extends the lifespan of equipment. Manufacturers can avoid premature wear and tear by addressing issues proactively and keeping machinery in optimal condition. Prolonging the life of expensive industrial equipment reduces the need for costly replacements and capital expenditures.
Improved Quality and Customer Satisfaction
Downtime is more than lost production time; it can also impact product quality. Frequent stoppages and restarts can lead to defects and inconsistencies in the manufacturing process. These quality issues can result in product recalls, rework, and, more importantly, dissatisfied customers. Effective downtime management minimises disruptions, improving product quality and higher customer satisfaction rates.
Competitive Edge
In today's fast-paced manufacturing landscape, staying competitive is essential. Manufacturers who consistently meet delivery deadlines, maintain product quality, and optimise production processes gain a competitive edge. Reduced downtime allows for greater agility in responding to market demands, staying ahead of competitors, and pursuing growth opportunities.
Sustainability and Energy Efficiency
Reducing downtime aligns with sustainability goals. It not only conserves resources but also contributes to energy efficiency. When equipment operates efficiently and without unnecessary interruptions, energy consumption is optimised, reducing the environmental footprint of manufacturing operations.
Employee Morale and Safety
Frequent downtime events can demoralise employees who may become frustrated with stop-and-start work patterns. Effective downtime management fosters a more predictable and stable work environment, improving employee morale. Additionally, it can enhance safety by reducing the risks associated with unplanned shutdowns and maintenance activities.
In the following sections of this blog post, we'll delve into strategies, technologies, and real-world examples that showcase how manufacturers can harness these benefits by effectively managing downtime. The journey toward manufacturing efficiency involves recognising the advantages and implementing actionable measures to minimise downtime and maximise operational performance.
Strategies for Downtime Control
Understanding the significance of effective downtime control is just the beginning. Manufacturers must implement actionable strategies and best practices to harness the benefits and achieve manufacturing efficiency. Let's explore these strategies, including preventive maintenance, predictive maintenance, and other techniques, to pave the way for optimised operations.
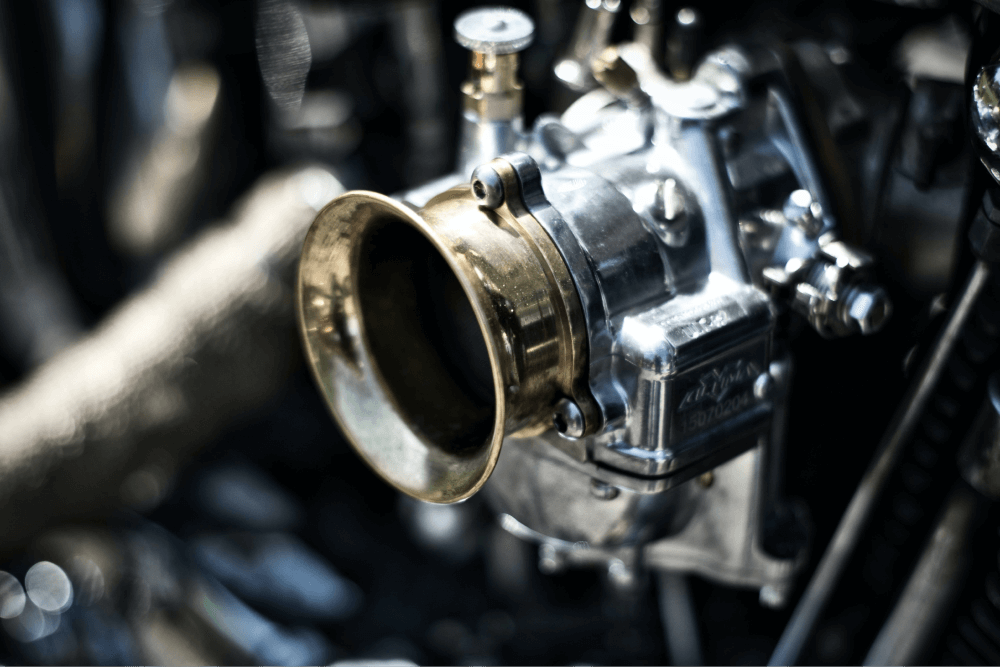
Preventive Maintenance
Preventive maintenance is a cornerstone of downtime control. It involves scheduled inspections, cleaning, and component replacement to prevent equipment failures before they occur. By adhering to a regular maintenance schedule based on equipment manufacturer guidelines, manufacturers can proactively identify and address potential issues. This approach minimises the risk of unplanned downtime caused by equipment breakdowns.
Iwoscan, a smart technology solution, is pivotal in preventive maintenance. It continuously monitors machine performance and provides real-time data insights. By detecting anomalies and deviations from normal operating conditions, Iwoscan can alert maintenance teams to take preventive actions before a breakdown occurs. This proactive approach not only reduces downtime but also extends equipment lifespan.
Predictive Maintenance
Predictive maintenance takes preventive maintenance further by using data and analytics to predict when equipment will fail. This data-driven approach leverages sensors and monitoring systems to gather real-time information about equipment performance. Machine learning algorithms analyse this data to identify patterns and anomalies that indicate potential issues.
Iwoscan, equipped with predictive maintenance capabilities, can accurately predict equipment failures. Continuously collecting and analysing data can provide early warnings of impending breakdowns. Maintenance teams can then schedule maintenance during planned downtimes, avoiding costly unplanned stoppages. This predictive approach optimises maintenance schedules and reduces downtime to a minimum.
Root Cause Analysis
Identifying and addressing the root causes of downtime events is crucial to control downtime effectively. Manufacturers can utilise techniques such as Failure Mode and Effects Analysis (FMEA) and Root Cause Analysis (RCA) to delve deep into the reasons behind equipment failures or process disruptions.
Iwoscan's data analytics capabilities aid in root cause analysis by providing a comprehensive view of equipment performance and process variables. It can pinpoint the exact factors contributing to downtime events, whether related to equipment malfunctions, maintenance issues, or operational inefficiencies. With this information, manufacturers can take targeted actions to eliminate root causes and prevent future downtime.
Condition Monitoring
Condition monitoring involves continuously tracking equipment performance parameters, such as temperature, pressure, vibration, and electrical currents. By monitoring these conditions in real time, manufacturers can detect early warning signs of impending failures or deviations from optimal performance.
Iwoscan excels in condition monitoring by offering real-time data visibility and alerts. It continuously collects data from sensors and equipment, allowing manufacturers to monitor the health of their assets. If conditions exceed predefined thresholds or exhibit unusual patterns, Iwoscan can trigger alerts, enabling immediate corrective actions.
Employee Training
Effective downtime control also involves educating and training employees. Operators and maintenance teams should be well-versed in equipment operation, troubleshooting, and preventive maintenance tasks. Proper training can lead to quicker issue identification and resolution, reducing downtime.
Incorporating Iwoscan into employee training programs can empower teams to utilise the technology effectively. Training on interpreting Iwoscan data and responding to alerts ensures that the workforce actively participates in downtime control efforts.
In the following sections, we will explore how technology, such as IoT and automation, can enhance downtime control, delve into the benefits of real-time monitoring, and discuss critical metrics and KPIs related to downtime control. These elements combine to form a comprehensive strategy for achieving manufacturing efficiency through effective downtime management.
Implementing Downtime Tracking and Analysis
Effective downtime control hinges on tracking and analysing downtime events systematically. In this section, we'll explore the critical role of data and analytics in downtime control and discuss the importance of implementing downtime tracking and analysis processes.
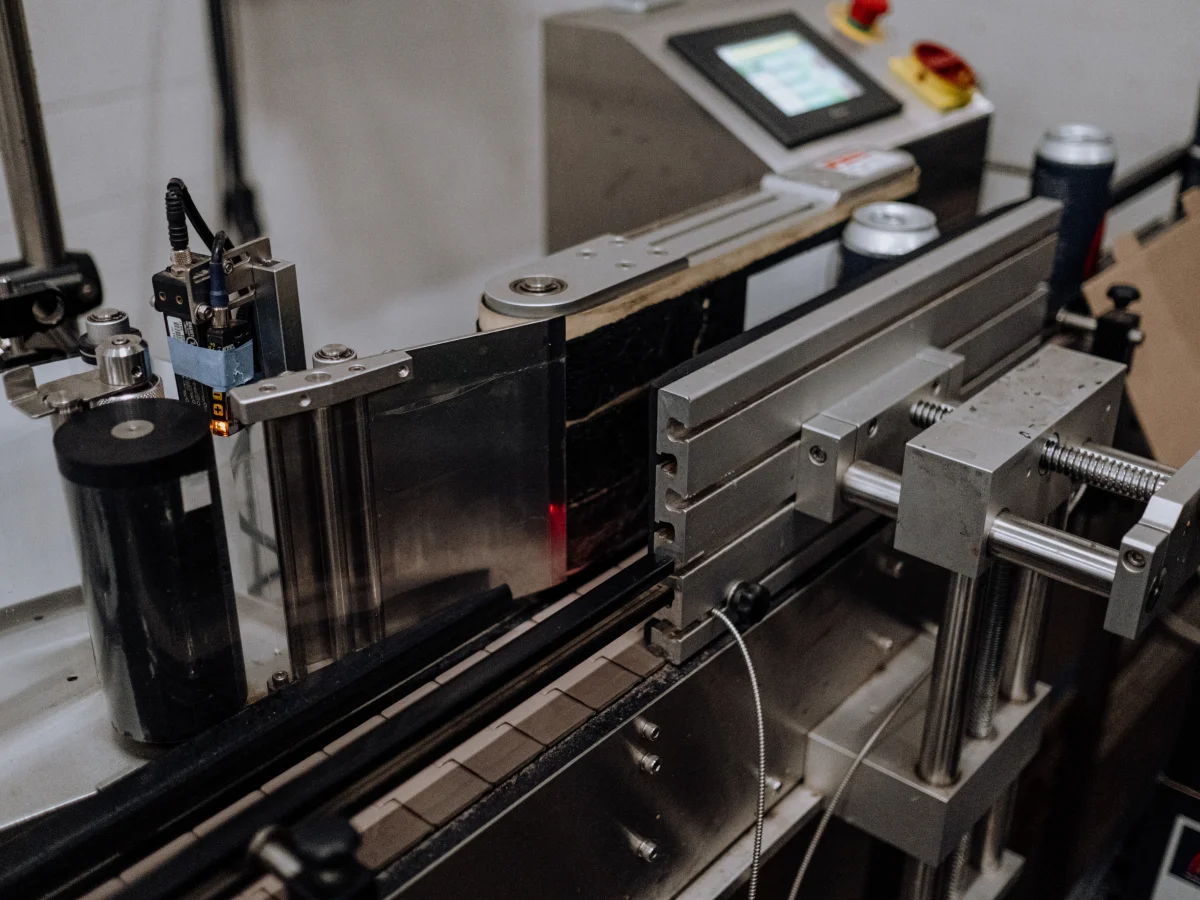
The Role of Data and Analytics
Data is the lifeblood of modern manufacturing and plays a pivotal role in downtime control. Manufacturers increasingly turn to data-driven decision-making to optimise operations, and downtime management is no exception. Real-time data and analytics enable manufacturers to gain valuable insights into equipment performance, identify patterns, and predict downtime events.
A Data-Driven Solution
One of the critical enablers of effective downtime tracking and analysis is Iwoscan. This smart technology solution continuously collects and analyses data from various sources, including sensors, machines, and production processes. Iwoscan provides real-time visibility into equipment performance, offering manufacturers actionable insights to mitigate downtime risks.
By integrating Iwoscan into their operations, manufacturers can:
.png)
Software and Tools for Downtime Tracking
In addition to Iwoscan, various software and tools are available for downtime tracking and analysis. These tools are designed to streamline the process of data collection, visualisation, and reporting. They provide manufacturers with user-friendly interfaces to monitor equipment status, view historical downtime data, and generate reports for analysis.
Implementing software solutions, in conjunction with Iwoscan, allows manufacturers to centralise downtime data, identify recurring issues, and make informed decisions to enhance efficiency and reduce unplanned stoppages.
Leveraging Technology for Downtime Control
Technology is pivotal in downtime control and efficiency improvement in today's fast-paced manufacturing landscape. Manufacturers increasingly turn to smart technologies, including IoT (Internet of Things), automation, and data analytics, to gain a competitive edge. Here, we explore how these technological advancements and solutions like Iwoscan revolutionise downtime control.
The Rise of Smart Manufacturing
Smart manufacturing represents a paradigm shift in the industry. It involves the integration of advanced technologies to create a highly interconnected and responsive manufacturing ecosystem. This shift is driven by the need for real-time visibility and data-driven decision-making, both instrumental in downtime control.
Smart manufacturing systems leverage IoT sensors and devices to collect vast data from equipment and processes. These data streams provide valuable insights into machine performance, product quality, and potential downtime triggers. For instance, sensors can monitor temperature, vibration, and energy consumption, allowing manufacturers to detect anomalies and address issues proactively.
An Enabler of Smart Downtime Control
One of the key enablers of smart downtime control is Iwoscan. Iwoscan's real-time monitoring capabilities empower manufacturers to capture a wealth of data from their production lines. By continuously monitoring machine performance, product quality, and other critical parameters, Iwoscan provides a comprehensive view of production processes.
Iwoscan excels in predictive maintenance, a vital component of downtime control. Analysing historical data and identifying patterns can predict equipment failures before they occur. This foresight enables manufacturers to schedule maintenance activities during planned downtimes, minimising disruptions and maximising productivity.
Additionally, Iwoscan's data analytics capabilities enable manufacturers to identify the root causes of downtime events. Whether it's equipment malfunctions, maintenance issues, or supply chain disruptions, Iwoscan's data-driven insights help manufacturers pinpoint the source of the problem and implement corrective actions swiftly.
Industry-Specific Solutions
Different industries have unique requirements when it comes to downtime control. For example, the pharmaceutical sector must adhere to strict regulatory standards, while the automotive industry focuses on precision and efficiency. Fortunately, technology providers, including Iwoscan, offer industry-specific solutions tailored to these needs.
Iwoscan's adaptability makes it a valuable asset in various manufacturing environments. Whether you're producing pharmaceuticals, automobiles, consumer electronics, or food and beverages, Iwoscan can be customised to suit your specific requirements.
Adopting smart technology and solutions like Iwoscan transforms downtime control from a reactive process to a proactive and data-driven strategy. In the following sections, we will delve deeper into the benefits of real-time monitoring of equipment and techniques, explore key metrics and KPIs for assessing downtime, and showcase additional case studies highlighting the success of smart downtime control implementations.
Monitoring Downtime in Real-Time
As manufacturing processes become increasingly complex and interconnected, the need for real-time monitoring of equipment and processes has never been more critical. In this section, we will delve into the benefits of real-time tracking and explore how it is transforming downtime control. We will also highlight the role of Iwoscan in enabling real-time monitoring and proactive downtime management.
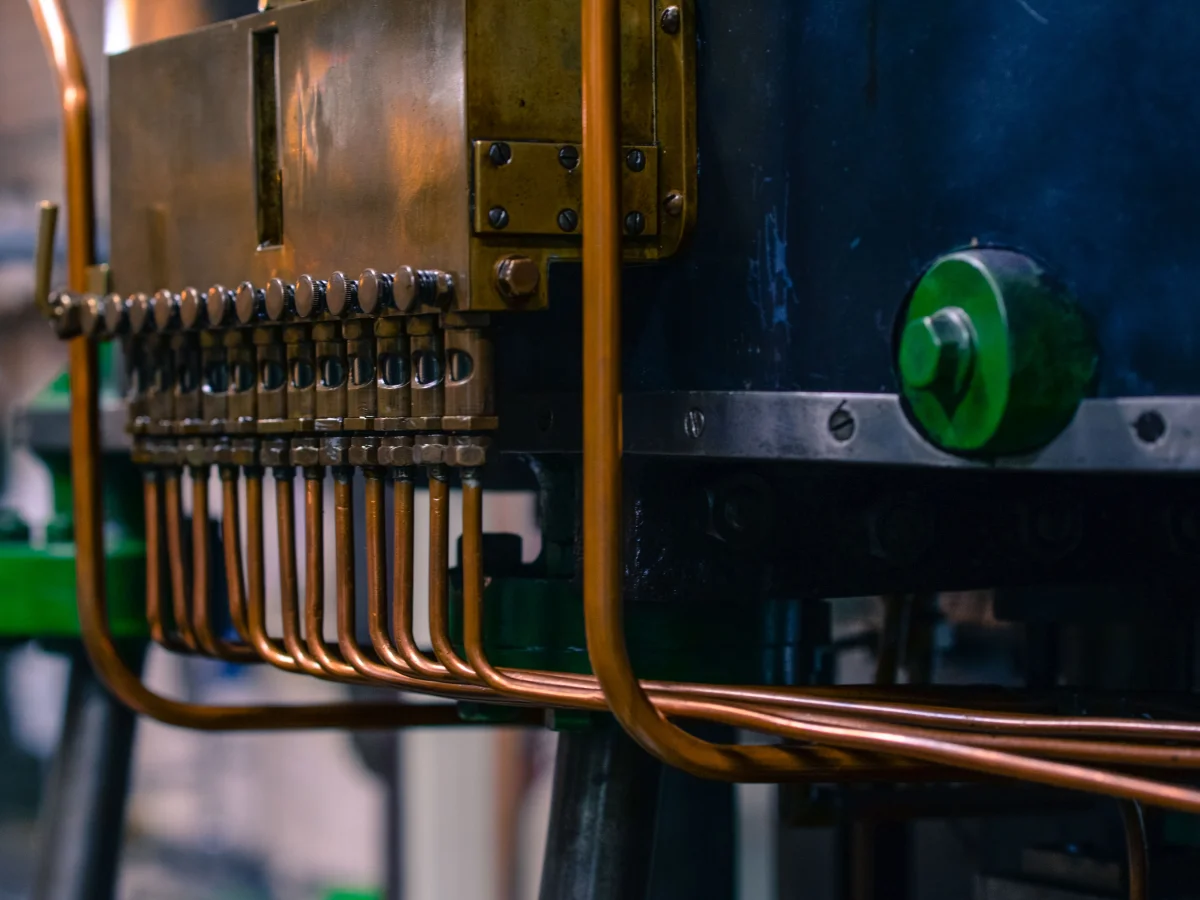
The Power of Real-Time Monitoring
Real-time monitoring involves continuously collecting and analysing data from various sources within a manufacturing facility. This data can encompass machine performance metrics, production line status, and product quality indicators. The key advantage of real-time monitoring is that it provides instantaneous insights into the health and performance of equipment and processes.
One of the significant benefits of real-time monitoring is the ability to detect anomalies and issues as they occur. For instance, real-time monitoring systems can flag these events immediately if a machine's temperature rises unexpectedly or a production line experiences a sudden slowdown. This rapid detection enables manufacturing teams to respond promptly, preventing minor issues from escalating into major downtime events.
Proactive Downtime Management with Iwoscan
Iwoscan, as a leading technology solution, excels in real-time monitoring capabilities. Its sensors and data collection devices are strategically placed throughout the manufacturing environment, capturing a continuous data stream. This data encompasses critical parameters such as machine performance, product quality, and process efficiency.
Iwoscan's real-time monitoring capabilities extend to predictive maintenance, a cornerstone of proactive downtime management. Iwoscan can identify patterns and anomalies indicative of potential equipment failures by analysing the data it collects. This foresight allows manufacturers to schedule maintenance activities during planned downtimes, minimising disruptions and costly unplanned downtime.
Moreover, Iwoscan's real-time data analysis enables manufacturers to make data-driven decisions on the fly. For example, if a specific machine operates outside its optimal parameters, Iwoscan can trigger alerts, prompting operators to adjust settings or take corrective actions immediately.
Overall Equipment Efficiency (OEE) and Real-Time Monitoring
Real-time monitoring also contributes to Overall Equipment Efficiency (OEE), a critical metric for assessing manufacturing efficiency. Overall Equipment Efficiency (OEE) considers equipment availability, performance, and quality factors to provide a holistic view of production efficiency. By leveraging real-time data from Iwoscan, manufacturers can calculate and optimise their OEE, leading to increased productivity and reduced downtime.
The next section will delve into key metrics and Key Performance Indicators (KPIs) related to downtime control. When monitored in real-time using solutions like Iwoscan, these metrics offer valuable insights into the health of manufacturing operations and enable proactive decision-making to minimise downtime.
Key Metrics and KPIs
In the realm of downtime control, measuring and assessing performance is essential for identifying areas of improvement. Key metrics and Key Performance Indicators (KPIs) are pivotal in this process, providing manufacturers with quantitative insights into their operations. This section will explore some crucial metrics and KPIs related to downtime control and efficiency enhancement, focusing on how Iwoscan can contribute to their measurement and improvement.
Overall Equipment Efficiency (OEE)
Overall Equipment Efficiency, or OEE, is a comprehensive metric that evaluates the overall performance of manufacturing equipment and processes. It combines three critical factors.
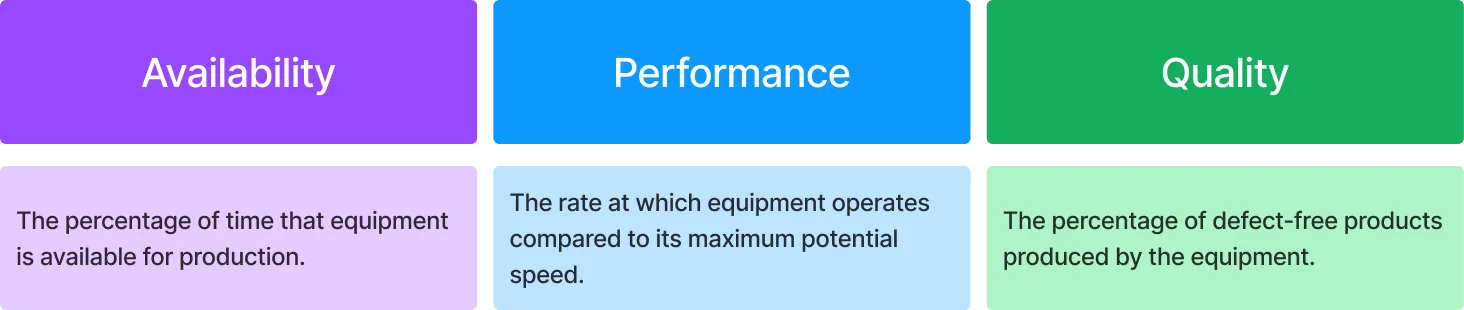
OEE offers a holistic view of manufacturing efficiency, highlighting areas where downtime and other losses occur. Iwoscan, with its real-time monitoring capabilities, provides the data necessary to calculate and optimise OEE. By continuously collecting and analysing performance data, Iwoscan enables manufacturers to identify and address inefficiencies promptly.
Mean Time Between Failures (MTBF)
MTBF is a reliability metric that calculates the average time between equipment failures. It provides insights into equipment reliability and can help predict when maintenance or repairs may be required. Iwoscan's predictive maintenance capabilities play a significant role in improving MTBF. By monitoring equipment health and performance, Iwoscan can detect early warning signs of potential failures, allowing for proactive maintenance and extending the time between failures.
Mean Time to Repair (MTTR)
MTTR measures the average time to repair and restore equipment to full operational status after a breakdown. Reducing MTTR is crucial for minimising downtime caused by unplanned maintenance. Iwoscan's real-time monitoring and predictive maintenance features aid in reducing MTTR by providing timely alerts and maintenance recommendations. This enables maintenance teams to address issues swiftly and efficiently, minimising production disruptions.
Downtime Tracking and Classification
Accurate tracking and classification of downtime events are fundamental for understanding their causes and patterns. Iwoscan's data collection capabilities facilitate precise tracking and categorisation of downtime events. Manufacturers can identify recurring issues by analysing the data collected and implementing targeted solutions to reduce downtime.
In the following section, we will delve into real-world case studies and success stories that showcase the practical implementation of downtime control strategies, including utilising Iwoscan as a valuable tool for improving efficiency and reducing downtime.
Enhance downtime control with Iwoscan.
In conclusion, achieving manufacturing efficiency through effective downtime control is not just a possibility but a necessity in today's competitive landscape. Downtime can significantly impact production costs, operational performance, and customer satisfaction. However, manufacturers can mitigate downtime and unlock substantial benefits with the right strategies, tools, and technologies.
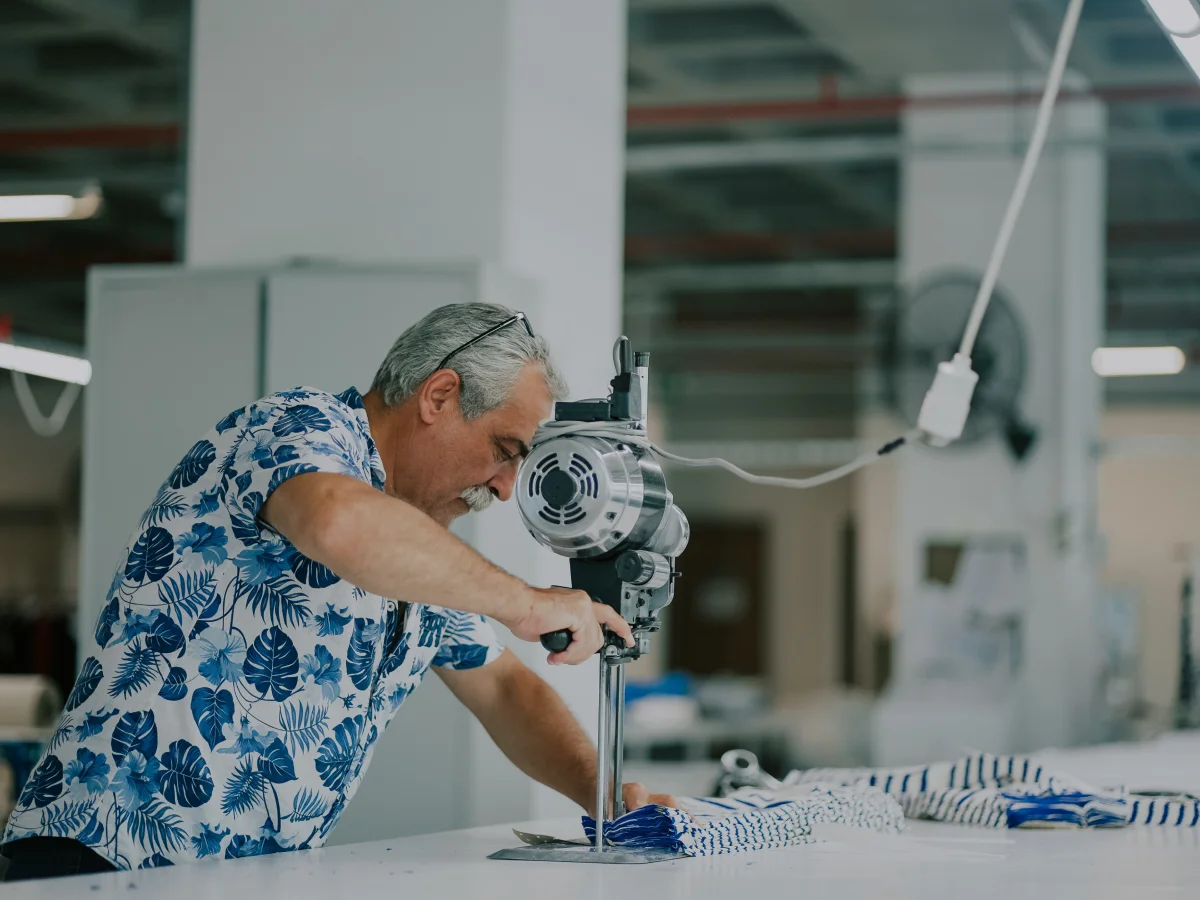
Throughout this blog post, we've explored the multifaceted aspects of downtime control, from understanding its significance to identifying common causes and implementing effective strategies. We've delved into the benefits of efficient downtime management, highlighting how it leads to cost savings, increased productivity, and enhanced overall performance.
Moreover, we've discussed the pivotal role of technology in modern manufacturing and how solutions like Iwoscan are transforming the downtime control landscape. Iwoscan's real-time monitoring capabilities, predictive maintenance features, and data-driven insights empower manufacturers to manage and reduce downtime proactively.
In pursuing manufacturing excellence, consider integrating Iwoscan into your operations to enhance downtime control, streamline processes, and maximise efficiency. By leveraging the insights and capabilities offered by Iwoscan, you can stay ahead of downtime-related challenges, optimise your production lines, and ensure your facility's smooth and efficient operation.
In a world where every minute of production matters, Iwoscan empowers you to master downtime control and achieve manufacturing efficiency that sets you apart in the competitive landscape. Embrace the future of manufacturing with Iwoscan and take control of your downtime.
Thank you for accompanying us through downtime control and manufacturing efficiency. We encourage you to explore more about Iwoscan to delve deeper into this critical solution of modern manufacturing. May your journey toward manufacturing efficiency be marked by reduced downtime, increased productivity, and continuous success.
Comments
test
Posted by User ID:Add a Comment
You must be logged in to post a comment.