In the intricate tapestry of manufacturing, where precision and consistency are paramount, the role of quality control stands as a beacon, ensuring that every product meets exacting standards. Effective quality control is not just a checkpoint in the production process; it's a comprehensive strategy that safeguards product integrity, customer satisfaction, and the reputation of manufacturing enterprises.
This blog post offers insights and tips to enhance its effectiveness. From fundamental principles to cutting-edge technologies, we will explore the diverse landscape of quality control methods and strategies that empower manufacturers to deliver excellence. Whether you're seeking to refine existing processes or navigating the challenges of implementation, this guide aims to be a valuable resource for elevating your quality control practices.
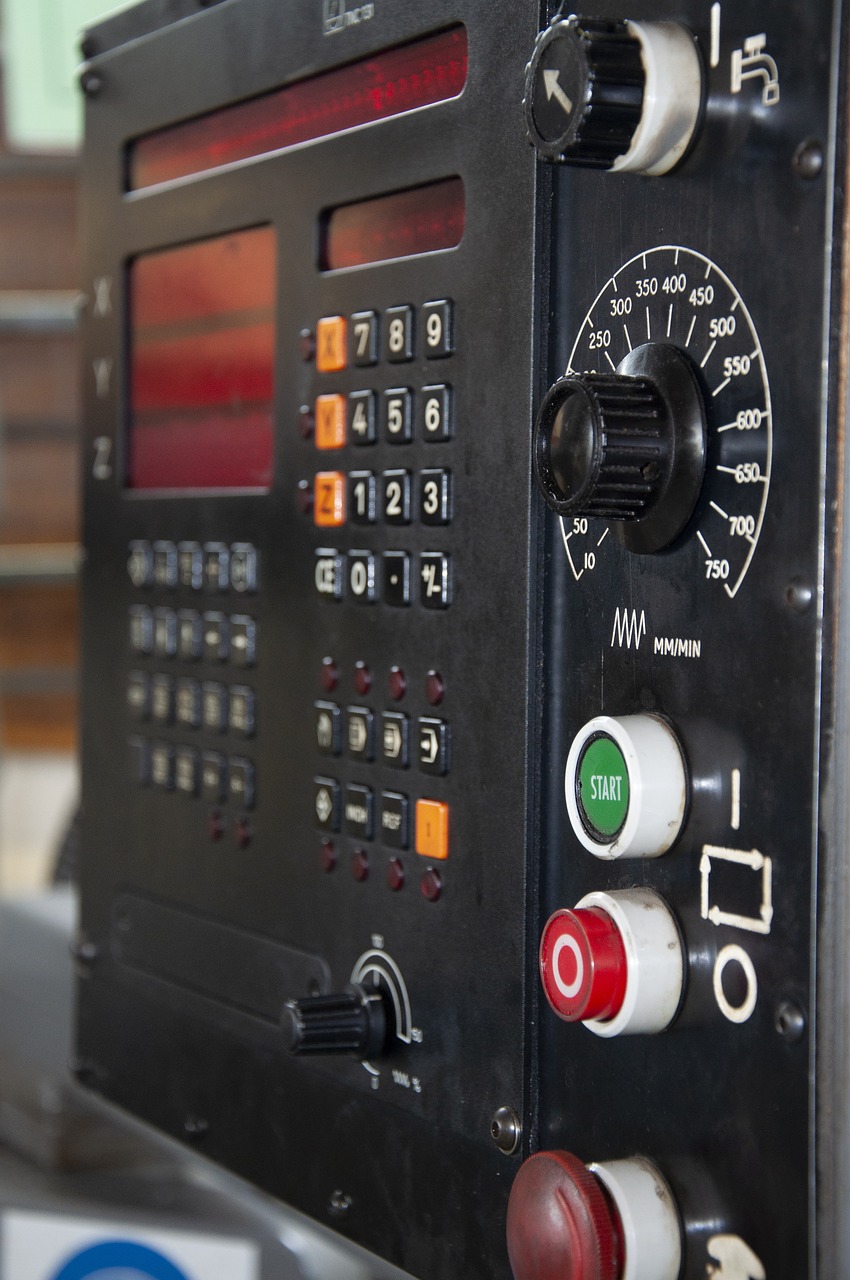
Fundamental Principles of Quality Control
Quality control serves as the vigilant guardian of manufacturing standards, ensuring that each product that leaves the production line meets exacting criteria.
Understanding the Distinction: Quality Control vs. Quality Assurance
The terms "quality control" and "quality assurance" often intertwine, but their roles are distinct, akin to different movements in the same performance.
Quality Control (QC)
QC is the vigilant sentinel stationed at the end of the production line. Its mission is to inspect, test, and scrutinise each product, identifying and rectifying any deviations from the predefined standards. QC is the reactive measure that ensures the end product is a flawless embodiment of quality.
Quality Assurance (QA)
QA, on the other hand, is the choreographer of the entire production ballet. It orchestrates a symphony of proactive measures, from establishing stringent standards and procedures to continuous monitoring and employee training. QA is the guiding force that seeks to prevent defects at every stage, fostering a culture where quality is not a checkpoint but an inherent characteristic of the entire process.
Key Elements of a Robust Quality Control Framework
Key Elements of a Robust Quality Control Framework |
|
Clear Quality Objectives |
Why it Matters: Quality objectives provide a roadmap, setting clear benchmarks for the manufacturing journey. They align the pursuit of quality with overarching business goals. |
Implementation Tip: Define specific, measurable, and achievable quality objectives that reflect the organisation's aspirations. |
|
Standard Operating Procedures (SOPs) |
Why it Matters: SOPs are the guiding scripts that ensure every actor in the production play follows the same cues. They reduce variability, enhance consistency, and provide a playbook for quality. |
Implementation Tip: Craft detailed SOPs for each production stage, leaving no room for ambiguity. SOPs should be living documents that evolve with insights from continuous improvement efforts. |
|
Training Programs |
Why it Matters: A skilled workforce is the backbone of effective quality control. Training programs empower employees to wield quality control tools with precision and confidence. |
Implementation Tip: Invest in regular training sessions, covering not only the technical aspects of quality control but also fostering a culture that values and prioritises quality. |
|
Data Collection and Analysis |
Why it Matters: In the age of Industry 4.0, data is the currency of insight. Real-time data collection and analysis empower manufacturers to make informed decisions and detect deviations early. |
Implementation Tip: Embrace digital tools and statistical methods to gather and analyse data. Transform data into actionable insights that drive continuous improvement. |
|
Continuous Monitoring |
Why it Matters: Continuous monitoring ensures that deviations are detected and rectified. It also allows for proactive interventions, preventing defects before they can tarnish the final product. |
Implementation Tip: Set up a system for continuous monitoring, employing key performance indicators (KPIs) as the compass. Regularly assess and recalibrate to keep processes within defined tolerances. |
|
Root Cause Analysis (RCA) |
Why it Matters: Addressing symptoms is a temporary fix; understanding and eliminating root causes is the path to lasting improvement. RCA digs deep to unearth the origins of defects. |
Implementation Tip: When defects occur, conduct a thorough root-cause analysis. Encourage a culture that views defects as opportunities to learn and refine processes. |
|
Feedback Loops |
Why it Matters: Communication between different stages of production is the lifeblood of quality control. Feedback loops facilitate real-time adjustments, ensuring a responsive and adaptive manufacturing ecosystem. |
Implementation Tip: Establish clear channels for feedback between production stages. Encourage open communication and consider technological solutions that streamline feedback processes. |
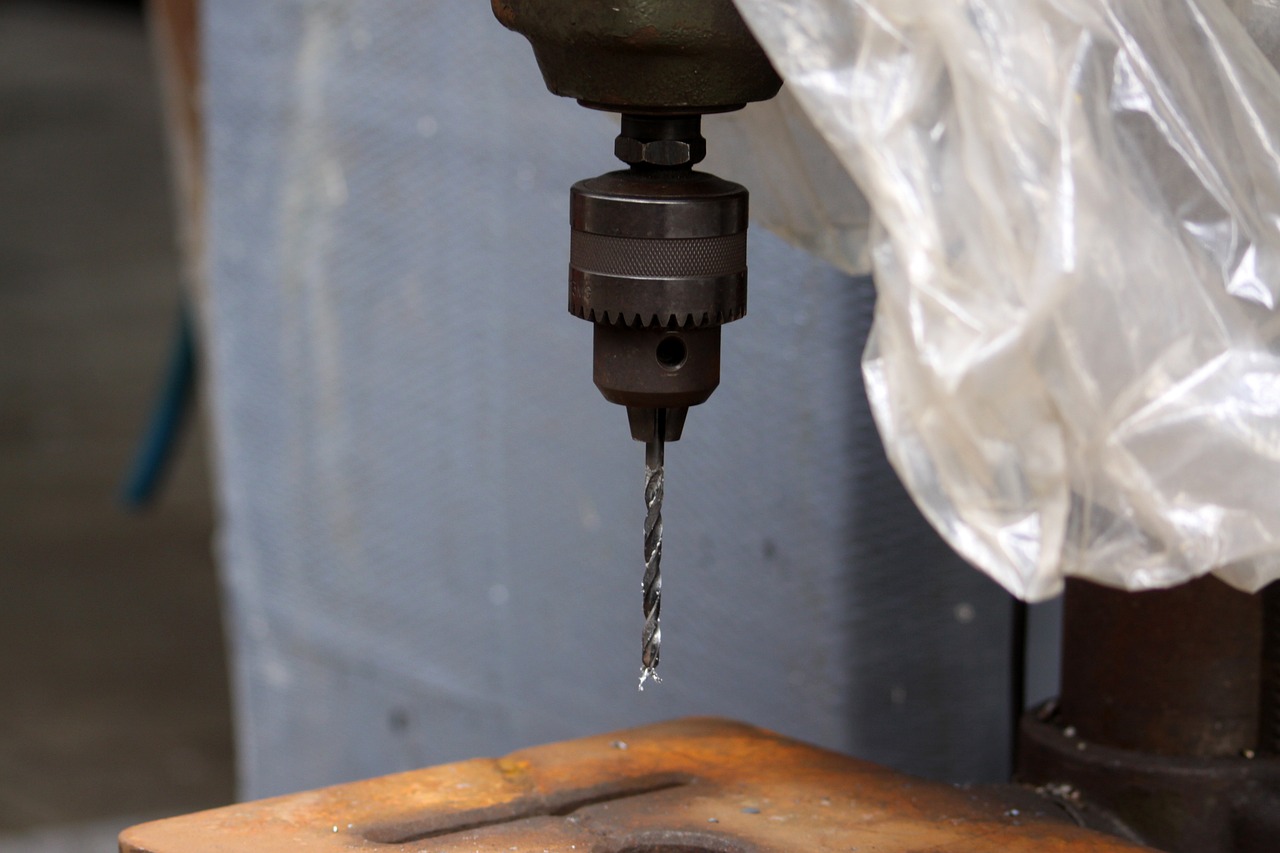
Common Quality Control Methods
Quality control methods serve as adaptable instruments in manufacturers' arsenals, allowing them to achieve precision and consistency across every aspect of production. From thorough inspections to statistical analyses, each method guarantees that the end product not only meets but often surpasses the predetermined standards. In this section, we embark on a comprehensive exploration of the common quality control methods that form the backbone of manufacturing excellence.
Inspection and Testing Techniques
Inspection and Testing Techniques represent the art and science of evaluating, measuring, and scrutinising products to guarantee their integrity, functionality, and compliance with established benchmarks. These techniques range from traditional methods rooted in craftsmanship to state-of-the-art technologies driven by innovation.
Inspection and Testing Techniques |
|
Visual Inspection |
The human eye is a potent instrument for identifying surface defects, irregularities, or deviations from visual standards. |
Application: Visual inspection is applied across various stages of the production process, ranging from evaluating raw materials to conducting the final inspection of finished products. This guarantees that the visual elements align with the predetermined quality standards. |
|
Enhancement: Integration of computer vision and image recognition technologies augments visual inspection, improving accuracy and efficiency. |
|
Dimensional Inspection |
Accurate measurements are critical in manufacturing. The dimensional inspection involves assessing the physical dimensions of components against specified tolerances. |
Application: Ensures that products meet size and shape requirements. Common techniques include callipers, gauges, and coordinate measuring machines (CMMs). |
|
Advancement: 3D scanning technologies enhance dimensional inspection, providing detailed, high-precision measurements for complex components. |
|
Non-Destructive Testing (NDT) |
NDT methods evaluate material properties without causing damage. They are vital for assessing the integrity of materials and components. |
Application: Techniques such as ultrasonic testing, radiography, and magnetic particle testing identify defects like cracks, voids, or inclusions. |
|
Innovation: Advancements in NDT include digital radiography and phased array ultrasonics, offering enhanced accuracy and quicker results. |
Statistical Process Control (SPC)
SPC employs statistical approaches to monitor and control production processes, ensuring consistency and preventing deviations.
Application |
Real-time monitoring of key variables to detect trends, patterns, or outliers. Maintains processes within specified control limits. |
Tools |
Control charts, histograms, and scatter diagrams provide visual representations for analysis and decision-making. |
Benefits |
SPC enables early identification of potential issues, reducing variability and enhancing overall process stability. |
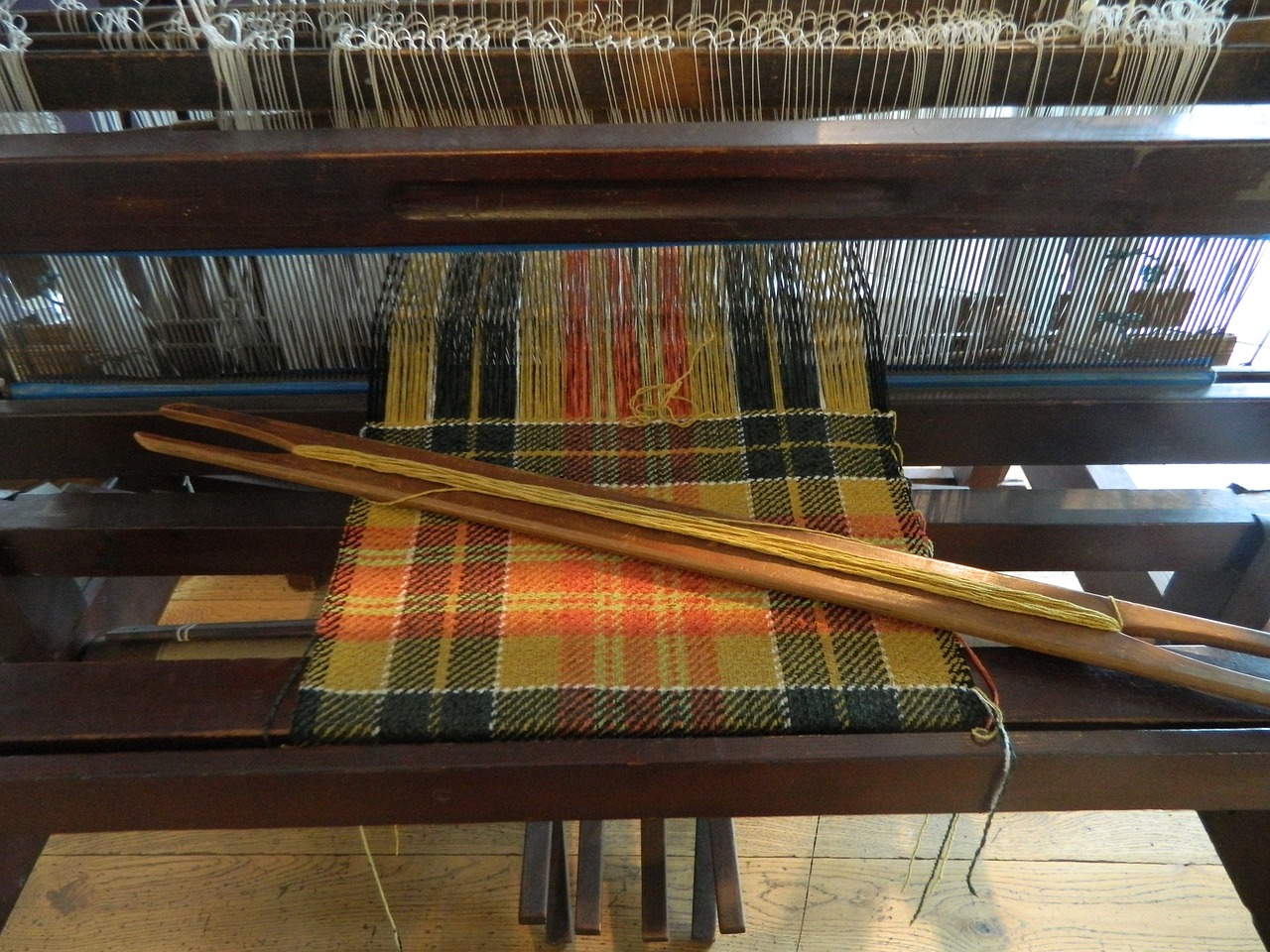
Six Sigma Methodology
Six Sigma is a data-driven methodology focused on minimising defects and improving process efficiency.
Application |
Define, measure, analyse, improve, and control (DMAIC) phases guide the systematic approach to problem-solving and process enhancement. |
Tools |
Six Sigma utilises statistical tools such as Pareto charts, cause-and-effect diagrams, and regression analysis. |
Results |
Six Sigma aims for near-perfect processes by striving for a Sigma level of six (3.4 defects per million chances). |
Failure Mode and Effects Analysis (FMEA)
FMEA is a proactive method for identifying potential failure modes in a process, evaluating their effects, and prioritising preventive actions.
Application |
applied during the design or planning phase to anticipate and mitigate potential risks. |
Steps |
Systematically assess failure modes, assign severity, occurrence, and detection ratings, and calculate risk priority numbers (RPNs). |
Benefits |
FMEA enhances risk management, guiding efforts to prevent defects and improve overall process reliability. |
Design of Experiments (DOE)
DOE is a method for systematically varying input factors to observe their impact on the output, helping optimise processes.
Application |
Used to identify critical process parameters, understand interactions, and optimise settings for desired outcomes. |
Tools |
Factorial designs, response surface methodologies, and analysis of variance (ANOVA) are common DOE tools. |
Advantage |
DOE provides insights into the relationship between variables, facilitating informed decision-making for process optimisation. |
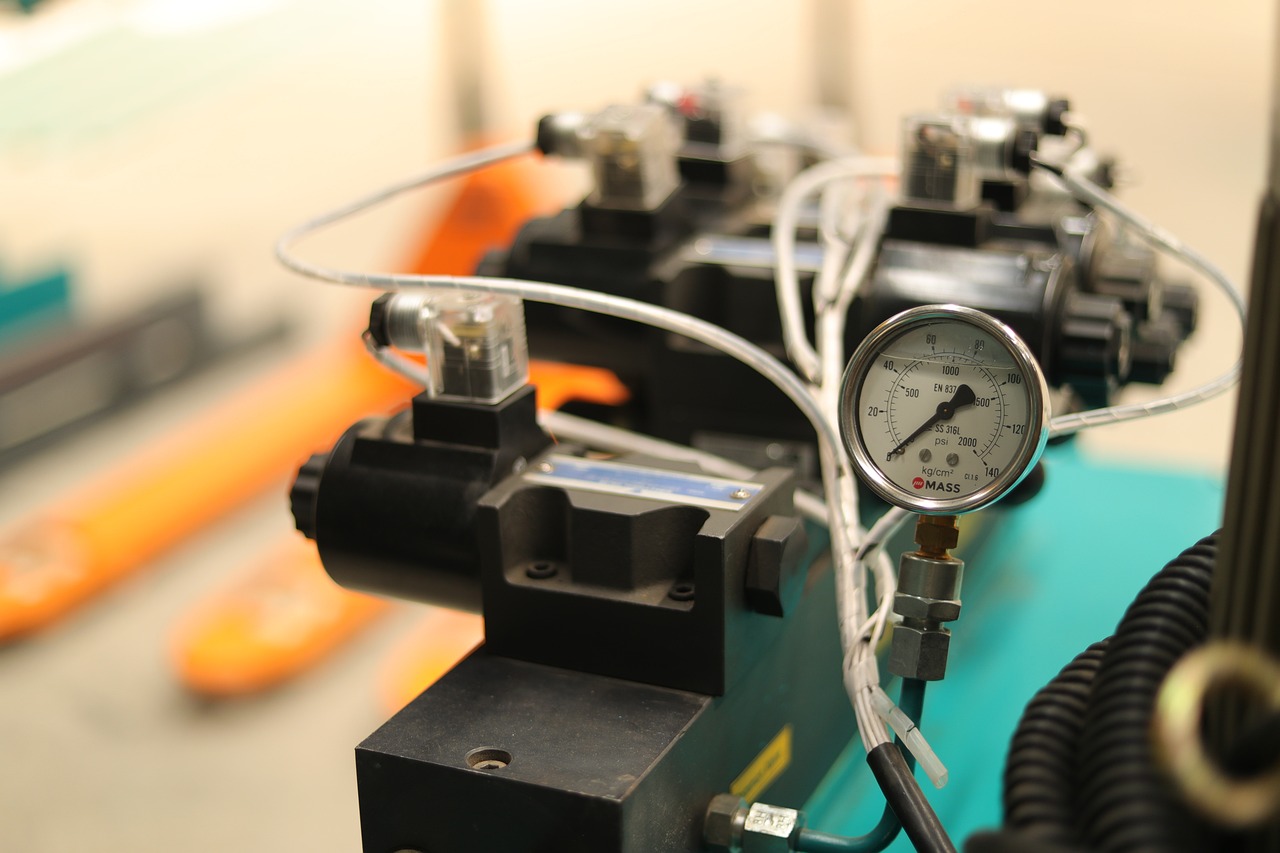
Implementing Technology in Quality Control
Technology helps as an assistant in the pursuit of precision and efficiency in quality control. From automating routine inspections to leveraging advanced data analytics, the integration of technology transforms traditional quality control methods, elevating them to new heights.
Role of Automation in Quality Control
Role of Automation in Quality Control |
|
Automated Inspection Systems |
Automation replaces manual inspection processes with systems that utilise sensors, cameras, and algorithms to assess product quality. |
Advantages: It speeds up inspection, reduces human error, and enables consistent evaluation. It is particularly effective for high-volume production environments. |
|
Applications: It is widely utilised in sectors such as automotive, electronics, and pharmaceuticals to perform tasks such as surface examination, defect identification, and verification of assembly processes. |
|
Automated Testing Solutions |
Automation extends to testing procedures, where machines conduct standardised tests rapidly and precisely. |
Advantages: It enhances testing accuracy, repeatability, and efficiency. It reduces reliance on manual testing, freeing human resources for more complex tasks. |
|
Applications: Widely used for functional testing, performance testing, and durability testing across various manufacturing sectors. |
|
Robotics in Quality Control |
Robots equipped with sensors and vision systems contribute to quality control by handling intricate tasks with speed and accuracy. |
Advancements: Collaborative robots (cobots) work alongside human operators, enhancing flexibility and adaptability in quality control processes. |
|
Applications: Robotics find applications in pick-and-place tasks, assembly verification, and complex inspections, ensuring precision in repetitive tasks. |
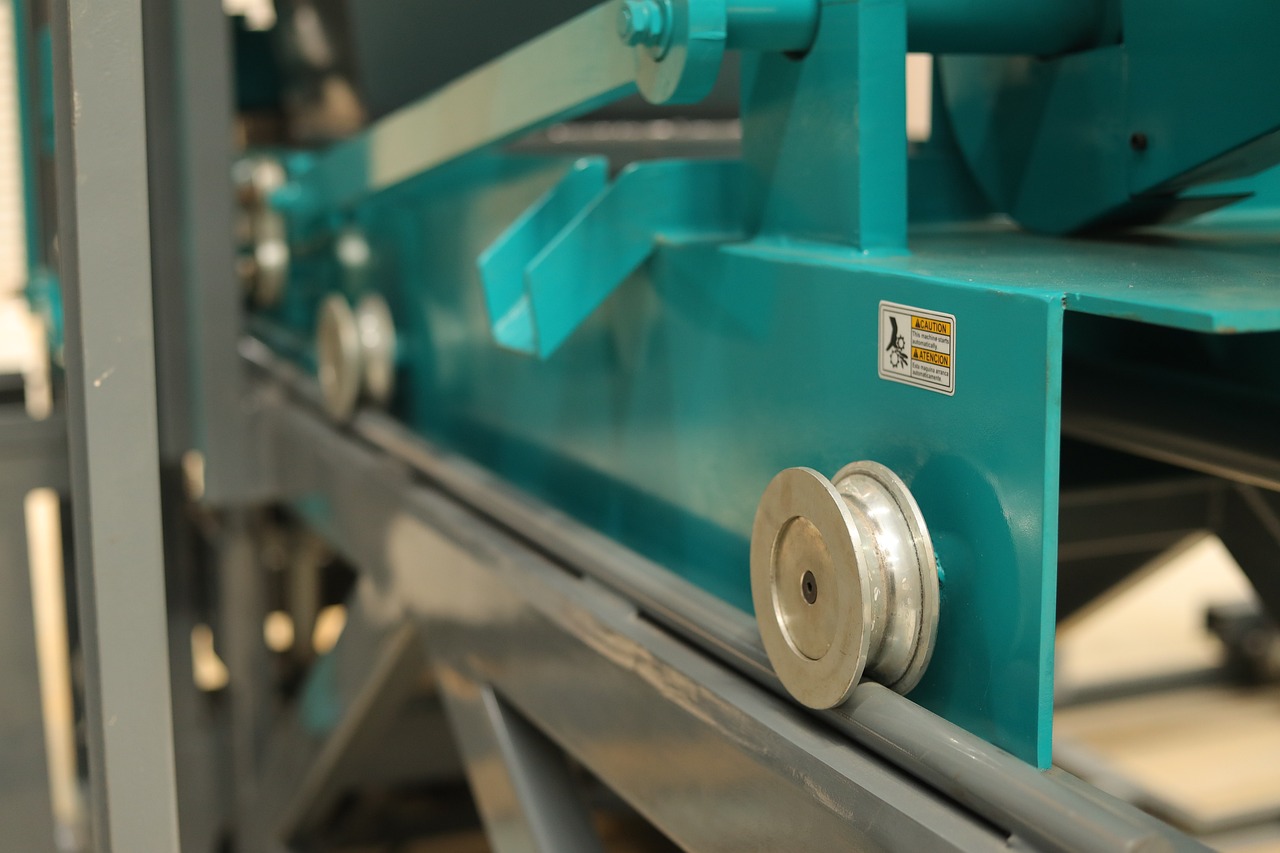
Advanced Inspection Technologies
Advanced Inspection Technologies |
|
Computer Vision and Image Recognition |
Computer vision algorithms analyse images and videos to identify patterns, defects, or anomalies in products. |
Applications: It is used for visual inspections, defect detection, and quality assessments in industries ranging from manufacturing to food processing. |
|
Enhancements: Machine learning algorithms enhance the capabilities of computer vision systems, enabling them to adapt and improve over time. |
|
3D Scanning and Metrology |
3D scanning technologies capture detailed geometric data, facilitating precise measurements and assessments. |
Advantages: Enables dimensional inspection of complex shapes, ensuring accurate analysis of intricate components. |
|
Applications: Commonly employed in aerospace, automotive, and medical industries for dimensional analysis, reverse engineering, and quality validation. |
|
Digital Radiography and NDT Innovations |
Digital radiography replaces traditional film-based methods, providing clearer and faster insights into material integrity. |
Advancements: Phased array ultrasonics offer advanced non-destructive testing capabilities, allowing for improved defect detection and characterisation. |
|
Applications: Critical for ensuring the structural integrity of materials in industries such as aviation, oil and gas, and infrastructure. |
Integration of the Internet of Things (IoT) for Real-Time Monitoring
Integration of the Internet of Things (IoT) for Real-Time Monitoring |
|
Sensor Networks |
IoT-enabled sensors collect real-time data from equipment and processes, providing continuous insights into production conditions. |
Benefits: Enables proactive monitoring, early defect detection, and preventive maintenance, reducing downtime and improving overall equipment effectiveness (OEE). |
|
Applications: Sensor networks find applications in monitoring temperature, humidity, vibration, and other variables critical to product quality. |
|
Data Analytics for Quality Insights |
Advanced data analytics tools process large datasets generated by IoT sensors to identify patterns, correlations, and potential quality issues. |
Advantages: Predictive analytics anticipate potential defects, enabling preemptive interventions. Data-driven decision-making enhances overall quality control strategies. |
|
Applications: Data analytics are applied in predictive maintenance, quality prediction, and process optimisation. |
Robotics and Automated Testing Solutions
Robotics and Automated Testing Solutions |
|
Overview of Robotics in Quality Control |
Integration: Robotics are increasingly becoming integral to quality control, handling tasks ranging from simple inspections to difficult assembly verifications. |
Advancements: Enhanced agility and the ability to work collaboratively with human operators make robotics versatile in quality control processes. |
|
Applications: Robotic arms, grippers, and vision systems are applied in tasks such as pick-and-place operations, packaging inspections, and intricate assembly verifications. |
|
Automated Testing Solutions |
Role: Automation extends to various testing processes, ensuring speed, accuracy, and repeatability in assessing product functionality and performance. |
Benefits: It accelerates testing timelines, reduces human error, and allows for testing at scale. This is critical for industries with stringent testing requirements. |
|
Applications: Functional testing, performance testing, and durability testing are efficiently conducted using automated testing solutions. |
Challenges and Considerations in Technology Integration
Challenges and Considerations in Technology Integration |
|
Data Security Concerns |
Challenge: The growing dependence on interconnected technologies gives rise to apprehensions regarding the security of data and the safeguarding of sensitive manufacturing information. |
Considerations: Implement robust cybersecurity measures, encryption protocols, and access controls to safeguard data. Regularly update security protocols to address emerging threats. |
|
Integration Complexity |
Challenge: Integrating diverse technologies and ensuring their seamless interaction can be complex, requiring careful planning and coordination. |
Considerations: Prioritize interoperability when selecting technologies. Conduct pilot projects to test integration feasibility before widespread implementation. |
|
Training and Skill Development |
Challenge: The introduction of advanced technologies may require additional skills and training for personnel involved in quality control. |
Considerations: Allocate resources to extensive training initiatives aimed at providing employees with the requisite skills for operating and maintaining emerging technologies. Cultivate a culture that values ongoing learning. |
|
Cost Considerations |
Challenge: The upfront costs associated with implementing advanced technologies can be significant. |
Considerations: Conduct a thorough cost-benefit analysis to assess the long-term advantages of technology integration. Explore financing options and prioritise technologies with a clear return on investment (ROI). |
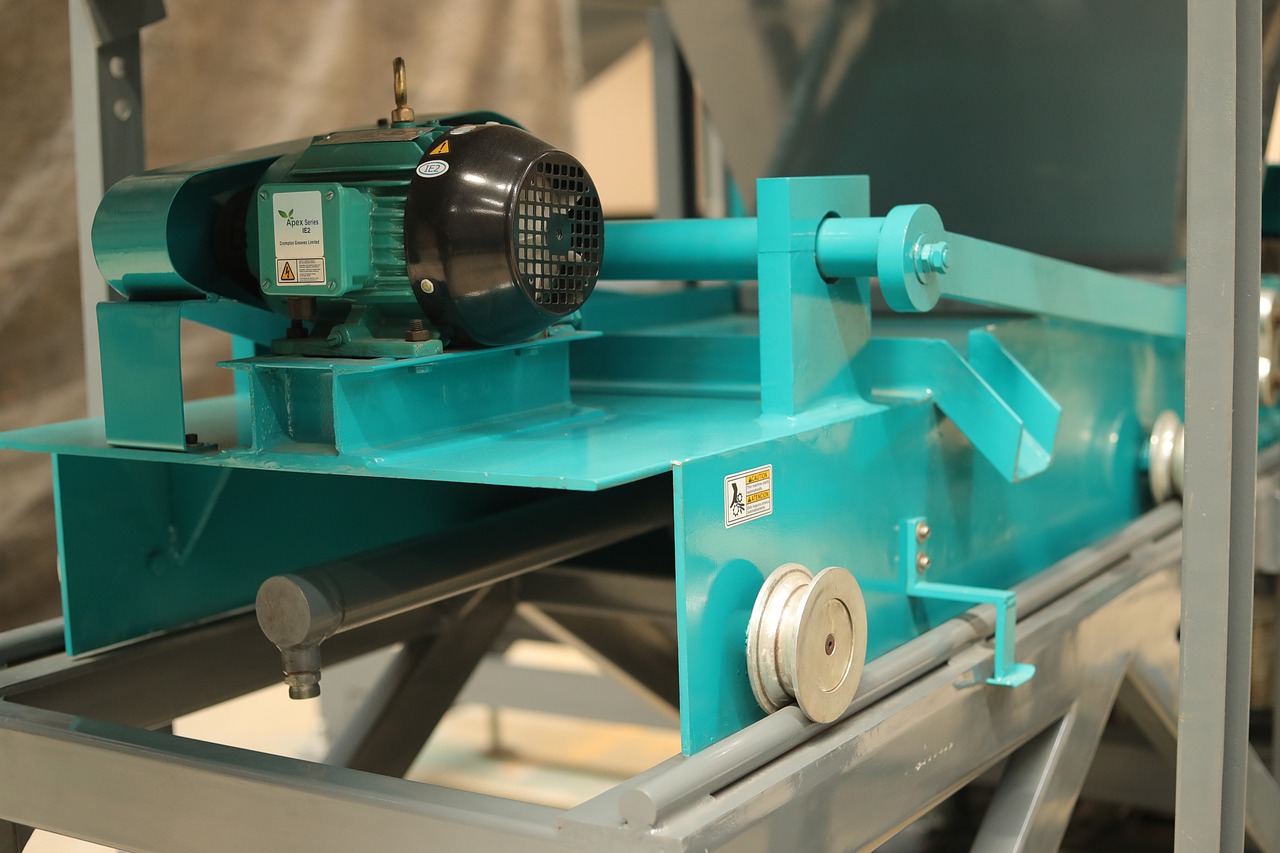
Strategies for Effective Quality Control
Effective quality control strategies emerge as the choreography that guides every movement in the manufacturing flow. Beyond the realm of technology and methodologies, these strategies encompass the human side of quality control—training, procedural clarity, and a relentless commitment to continuous improvement.
Training & Skill Development
Training & Skill Development |
|
Continuous Education on Quality Control Methods |
Rationale: As quality control methods evolve, providing ongoing education ensures that the workforce remains adept at utilising the latest tools and techniques. |
Implementation: Conduct regular training sessions covering advancements in quality control technologies, methodologies, and industry best practices. |
|
Cross-Functional Training |
Rationale: Fostering collaboration between different departments enhances a holistic understanding of the manufacturing process, contributing to more effective quality control. |
Implementation: Facilitate cross-functional training sessions where employees from various departments, including production, quality control, and research and development, share insights and knowledge. |
Establishing Clear Standard Operating Procedures (SOPs)
Establishing Clear Standard Operating Procedures (SOPs) |
|
Detailed SOPs for Each Production Stage |
Rationale: Standard operating procedures serve as the playbook for ensuring consistency, reducing variability, and providing a standardised approach to quality control. |
Implementation: Craft comprehensive SOPs for each production stage, outlining step-by-step instructions, criteria for acceptance, and procedures for handling deviations. |
|
Living Documents Evolving with Continuous Improvement |
Rationale: SOPs should not be static; they must evolve with insights from continuous improvement efforts to reflect the most effective and efficient practices. |
Implementation: Establish a system for regular review and update of SOPs based on feedback, lessons learned, and advancements in technology or methodologies. |
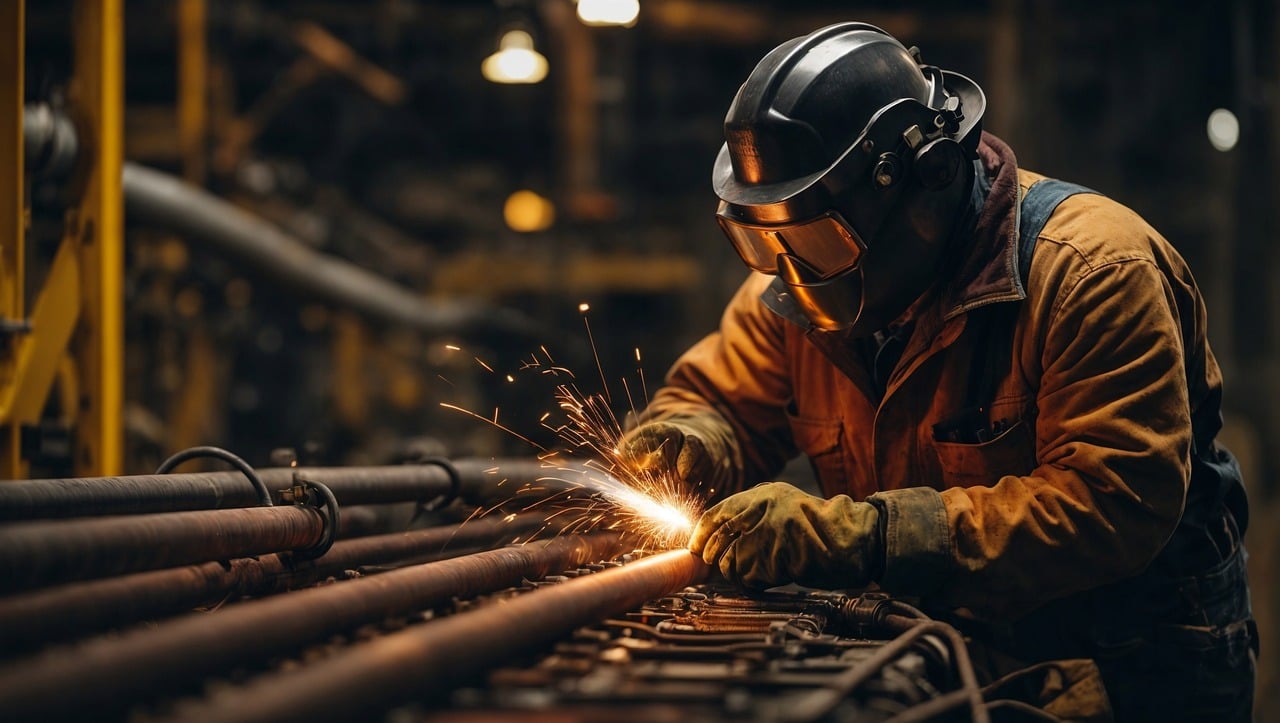
Emphasising a Culture of Continuous Improvement
Emphasising a Culture of Continuous Improvement |
|
Regular Audits and Assessments |
Rationale: Periodic audits ensure that quality control processes are aligned with standards and regulations, providing insights for improvement. |
Implementation: Conduct internal and external audits of quality control processes, analyse findings, and use them to refine and optimise practices. |
|
Kaizen Principles and Employee Involvement |
Rationale: Kaizen, the philosophy of perpetual improvement, motivates employees at every level to actively participate in continuous enhancements. |
Implementation: Instill a culture where employees feel empowered to identify and address inefficiencies, defects, and opportunities for improvement. Implement Kaizen principles through regular improvement initiatives. |
|
Innovation Hubs and Idea Generation Platforms |
Rationale: Creating spaces for idea generation and innovation encourages employees to propose novel solutions and improvements to existing processes. |
Implementation: Establish platforms, such as innovation hubs or suggestion boxes, where employees can contribute ideas. Recognise and reward innovative contributions. |
Regular Process Audits
Regular Process Audits |
|
Internal and External Audits |
Rationale: Routine audits offer an impartial assessment of quality control processes, guaranteeing adherence to industry standards and regulations. |
Implementation: Schedule internal audits conducted by in-house teams and external audits by third-party organisations to assess the effectiveness of quality control practices. |
|
Analysis of Audit Findings |
Rationale: Examining audit findings is a valuable tool for pinpointing areas for improvement and refining strategies within quality control. |
Implementation: Systematically analyse audit findings, categorise them based on severity and frequency, and use the insights to prioritise improvement efforts. |
Quality Control Certification and Industry Standards
Quality Control Certification and Industry Standards |
|
ISO Certification |
Rationale: Certifications from the International Organization for Standardization (ISO), like ISO 9001, offer a recognised framework for establishing and sustaining an efficient quality management system. |
Implementation: Pursue relevant ISO certifications to demonstrate commitment to quality and ensure continuous compliance with the standards outlined in the certification. |
|
Adherence to Industry-Specific Standards |
Rationale: Different industries may have specific quality control standards and regulations. Adherence to these standards is crucial for product quality and market acceptance. |
Implementation: Stay informed about industry-specific standards and ensure that quality control processes align with and exceed the requirements outlined by relevant regulatory bodies. |
Collaboration Between Quality Control and Other Departments
Collaboration Between Quality Control and Other Departments |
|
Integrated Quality Control Teams |
Rationale: Collaboration between quality control, production, and research and development teams fosters a holistic approach to quality and ensures that all aspects of the production process are considered. |
Establish cross-functional quality control teams that include members from different departments. Encourage open communication and knowledge sharing. |
|
Regular Cross-Functional Meetings |
Rationale: Regular meetings between representatives from various departments provide a platform for discussing challenges, sharing insights, and collectively addressing issues. |
Implementation: Facilitate regular cross-functional meetings where teams collaborate to solve problems, discuss improvements, and align on quality goals. |
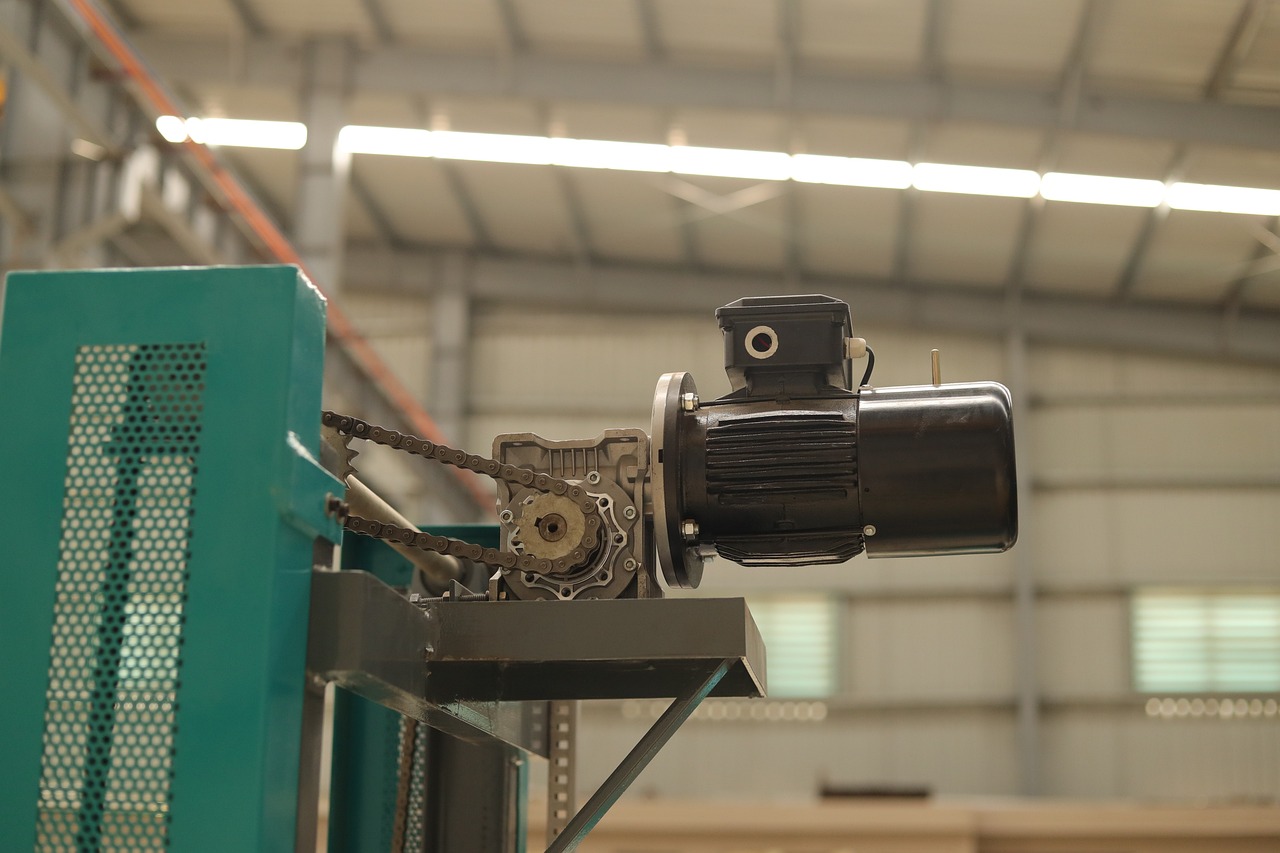
Investment in Cutting-Edge Technologies
Investment in Cutting-Edge Technologies |
|
Continuous Assessment of Emerging Technologies |
Rationale: The rapid evolution of technology necessitates continuous assessment of emerging tools and technologies relevant to quality control. |
Implementation: Establish a mechanism for regularly evaluating new technologies. Conduct pilot projects to assess feasibility and effectiveness before widespread implementation. |
|
Pilot Projects for Technology Integration |
Rationale: Implementing new technologies on a smaller scale through pilot projects allows for testing and fine-tuning before full-scale deployment. |
Implementation: Identify specific areas where technology integration can enhance quality control. Conduct pilot projects to assess the impact, identify challenges, and optimise the implementation process. |
Employee Recognition and Incentives
Employee Recognition and Incentives |
|
Recognition for Quality Achievements |
Rationale: Recognizing and rewarding employees for their contributions to quality control fosters a positive work environment and reinforces a culture of excellence. |
Implementation: Establish a recognition program that acknowledges individuals or teams for outstanding contributions to quality. Highlight success stories and share them across the organisation. |
|
Incentives for Continuous Improvement |
Rationale: Incentives for continuous improvement initiatives encourage employees to participate actively in improving quality control processes. |
Implementation: Introduce incentive programs that reward employees for suggesting and implementing improvements. Tie incentives to measurable outcomes, such as defect reduction or process optimisation. |
Supplier Collaboration and Quality Assurance
Supplier Collaboration and Quality Assurance |
|
Supplier Quality Collaboration |
Rationale: The quality of inputs significantly impacts the final product. Collaborating with suppliers ensures that raw materials meet specified standards. |
Implementation: Establish communication channels with suppliers to discuss quality requirements, conduct joint quality audits, and collaboratively address any issues. |
|
Supplier Quality Assurance Programs |
Rationale: Implementing supplier quality assurance programs establishes clear expectations and standards for suppliers, contributing to a more reliable supply chain. |
Implementation: Develop and communicate quality assurance criteria to suppliers. Regularly assess supplier performance and provide feedback to enhance collaboration and maintain quality standards. |
Data-Driven Decision-Making
Data-Driven Decision-Making |
|
Key Performance Indicators (KPIs) for Quality Control |
Rationale: The quality of inputs significantly impacts the final product. Collaborating with suppliers ensures that raw materials meet specified standards. |
Implementation: Identify relevant KPIs such as defect rates, inspection cycle times, and customer satisfaction scores. Regularly analyse and report on KPIs to inform decision-making. |
|
Predictive Analytics for Quality Prediction |
Rationale: Predictive analytics leverage historical data to forecast potential quality issues, enabling proactive interventions. |
Implementation: Implement predictive analytics models that analyse data from quality control processes. Use the insights to anticipate and address potential defects before they occur. |
Feedback Loops and Continuous Communication
Feedback Loops and Continuous Communication |
|
Establishing Clear Feedback Channels |
Rationale: Open and transparent communication channels for feedback ensure that information flows seamlessly between different stages of the production process. |
Implementation: Implement feedback loops that allow personnel from different departments to provide input on quality control processes. Encourage open communication and the sharing of insights. |
|
Real-Time Communication Platforms |
Rationale: Real-time communication platforms facilitate immediate response to quality issues, reducing the time between identification and resolution. |
Implementation: Utilize digital communication platforms to enable real-time communication between quality control teams, production teams, and relevant stakeholders. Ensure that critical quality information is communicated promptly. |
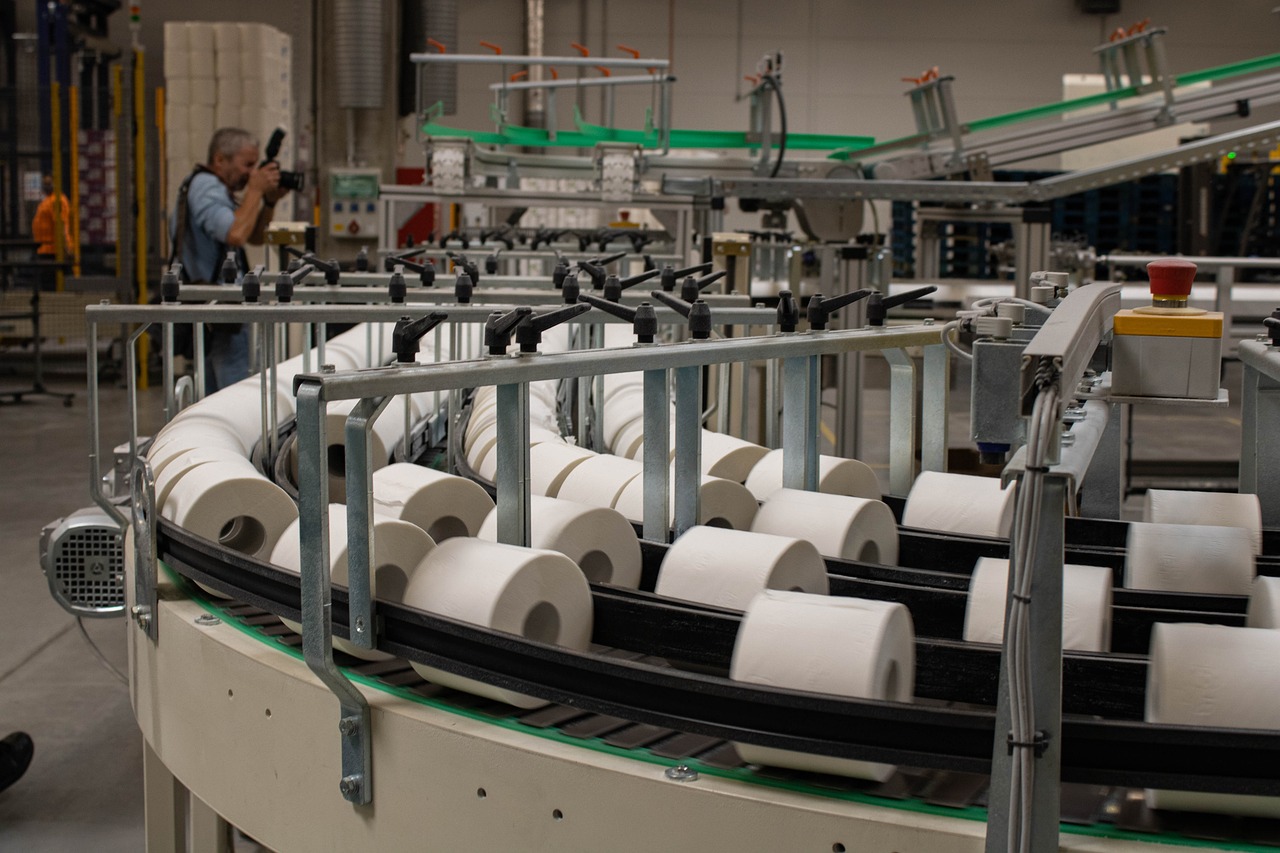
Regulatory Compliance and Documentation
Regulatory Compliance and Documentation |
|
Comprehensive Documentation Practices |
Rationale: Thorough documentation ensures traceability compliance with standards and provides a foundation for continuous improvement. |
Implementation: Implement robust documentation practices for quality control processes. Document inspection results, corrective actions, and changes to SOPs. Maintain documentation in compliance with relevant regulations. |
|
Regular Audits for Regulatory Compliance |
Rationale: Regular audits ensure that quality control processes adhere to regulatory requirements, reducing the risk of non-compliance. |
Implementation: Conduct internal and external audits specifically focused on regulatory compliance. Ensure that quality control practices align with industry-specific regulations and standards. |
Overcoming Challenges in Quality Control
The path to manufacturing excellence has its challenges, and a myriad of factors often challenge effective quality control. Identifying and overcoming these challenges is pivotal for ensuring that products meet stringent standards and customer expectations. In this section, we navigate through common challenges faced in quality control, offering insights and strategies to surmount these hurdles and fortify the foundation of manufacturing precision.
Variability in Production Processes
Variability in Production Processes |
|
Challenge |
Nature of Challenge: Production processes inherently possess variability due to factors like raw material variations, equipment performance fluctuations, and environmental conditions. |
Impact on Quality Control: Variability can lead to inconsistent product quality, making it challenging to maintain uniformity and meet defined standards. |
|
Strategies to Overcome |
Process Optimization: Regularly assess and optimise production processes to minimise variability. Implement advanced technologies, such as statistical process control (SPC) and design of experiments (DOE), to identify and address sources of variation. |
Real-Time Monitoring: Utilize real-time monitoring systems to detect deviations from set parameters promptly. Implement feedback loops to make instantaneous adjustments and maintain process stability. |
Ensuring Consistency Across Production Batches
Ensuring Consistency Across Production Batches |
|
Challenge |
Nature of Challenge: Achieving consistent quality across different production batches is a persistent challenge, especially in industries with high variability in raw materials. |
Impact on Quality Control: Inconsistencies across batches can lead to variations in product quality, affecting customer satisfaction and brand reputation. |
|
Strategies to Overcome |
Raw Material Standardization: Work closely with suppliers to standardise raw materials. Establish clear quality criteria and conduct regular assessments to ensure that incoming materials meet specifications. |
Advanced Testing Methods: Implement advanced testing methods, including non-destructive testing (NDT) and real-time monitoring, to assess product quality at various stages of production. Identify and address batch-specific issues promptly. |
Integration of New Technologies
Integration of New Technologies |
|
Challenge |
Nature of Challenge: The integration of new technologies, while beneficial in the long run, poses initial challenges in terms of implementation, employee training, and potential disruptions. |
Impact on Quality Control: Resistance to change and teething problems during integration can temporarily affect the efficiency of quality control processes. |
|
Strategies to Overcome |
Pilot Projects: Introduce new technologies through pilot projects to assess feasibility, identify challenges, and fine-tune the integration process before full-scale implementation. |
Comprehensive Training Programs: Invest in extensive training programs designed to equip employees with the essential skills required for operating and maintaining new technologies. Address any concerns and cultivate a positive attitude towards innovation. |
Managing Data Security and Privacy Concerns
Managing Data Security and Privacy Concerns |
|
Challenge |
Nature of Challenge: The increasing reliance on interconnected technologies raises concerns about data security, particularly sensitive manufacturing information. |
Impact on Quality Control: Inadequate data security measures can lead to data breaches, compromising the integrity of quality control processes and sensitive manufacturing data. |
|
Strategies to Overcome |
Robust Cybersecurity Measures: Implement strong cybersecurity measures, including encryption protocols, access controls, and regular security audits. Ensure that data storage and transmission adhere to industry standards. |
Employee Training on Data Security: Provide training to employees regarding the significance of data security and their responsibility in protecting sensitive information. Cultivate a culture of cybersecurity awareness across the organisation. |
Cost Considerations in Technology Integration
Cost Considerations in Technology Integration |
|
Challenge |
Nature of Challenge: The upfront costs associated with implementing advanced technologies for quality control can be significant, posing financial challenges for some organisations. |
Impact on Quality Control: Budget constraints may hinder the adoption of technologies that could otherwise enhance quality control processes. |
|
Strategies to Overcome |
Cost-Benefit Analysis: Perform an in-depth cost-benefit analysis to evaluate the enduring benefits of technology integration. Prioritise technologies that demonstrate a clear return on investment (ROI) and concentrate on areas with high impact. |
Exploration of Financing Options: Explore financing options, such as government grants, industry partnerships, or leasing arrangements, to alleviate the initial financial burden of technology adoption. |
Employee Resistance to Change
Employee Resistance to Change |
|
Challenge |
Nature of Challenge: Employees may resist changes in processes, especially when new technologies are introduced, leading to a reluctance to adopt innovative approaches. |
Impact on Quality Control: Resistance to change can hinder the successful integration of technologies and impede the optimisation of quality control processes. |
|
Strategies to Overcome |
Transparent Communication: Transparently communicate the advantages of changes, highlighting their contributions to overall efficiency, job satisfaction, and career development. Address any concerns and establish a platform for open dialogue. |
Inclusive Decision-Making: Involve employees in decision-making processes related to changes. Solicit feedback, encourage participation, and make them active stakeholders in the improvement journey. |
Ensuring Compliance with Evolving Regulations
Ensuring Compliance with Evolving Regulations |
|
Challenge |
Nature of Challenge: Evolving regulations and standards in the manufacturing industry require continuous monitoring and adaptation to remain compliant. |
Impact on Quality Control: Failure to stay updated on regulations may result in non-compliance, leading to legal consequences and reputational damage. |
|
Strategies to Overcome |
Regulatory Intelligence Programs: Establish regulatory intelligence programs to stay informed about changes in industry regulations. Regularly review and update quality control processes to ensure alignment with current standards. |
Engagement with Regulatory Bodies: Actively engage with regulatory bodies and industry associations to stay abreast of upcoming changes. Participate in discussions and seek clarification on ambiguous regulations. |
Balancing Automation and Human Oversight
Balancing Automation and Human Oversight |
|
Challenge |
Nature of Challenge: While automation enhances efficiency, there is a need for a balance with human oversight to address unforeseen circumstances and ensure adaptability. |
Impact on Quality Control: Overreliance on automation without human oversight may result in missed anomalies or the inability to adapt to unique situations. |
|
Strategies to Overcome |
Human-in-the-Loop Systems: Implement human-in-the-loop systems where automated processes are complemented by human oversight. Design workflows that allow humans to intervene when necessary. |
Continuous Training: Provide ongoing training to employees on the functioning of automated systems and emphasise the importance of their role in monitoring and decision-making. |
Global Supply Chain Challenges
Global Supply Chain Challenges |
|
Challenge |
Nature of Challenge: Global supply chain complexities, including geopolitical factors, transportation issues, and supplier disruptions, can impact the availability and quality of raw materials. |
Impact on Quality Control: Disruptions in the supply chain can lead to delays, shortages, or variations in raw materials, which can affect the quality of the final product. |
|
Strategies to Overcome |
Diversification of Suppliers: Diversify the supplier base to reduce dependency on a single source. Identify alternative suppliers and establish relationships to ensure a consistent and high-quality supply of raw materials. |
Real-Time Supply Chain Monitoring: Implement real-time monitoring of the supply chain to identify potential disruptions early. Collaborate with suppliers to address challenges promptly and maintain a resilient supply chain. |
Upholding Quality in High-Volume Production
Upholding Quality in High-Volume Production |
|
Challenge |
Nature of Challenge: Due to the speed and scale of operations, High-volume production environments often face challenges in maintaining consistent quality. |
Impact on Quality Control: Quality control processes may need help to keep pace with high-volume production, leading to potential oversights and defects. |
|
Strategies to Overcome |
Advanced Automation Solutions: Implement advanced automation solutions, such as robotic inspection systems and real-time monitoring, to enhance the speed and accuracy of quality control in high-volume environments. |
Parallel Quality Control Processes: Design parallel quality control processes that run concurrently with production to ensure continuous inspection without causing bottlenecks. |
Cultural Shift Towards Quality Excellence
Cultural Shift Towards Quality Excellence |
|
Challenge |
Nature of Challenge: Shifting the organisational culture towards a relentless pursuit of quality excellence requires time, commitment, and alignment at all levels. |
Impact on Quality Control: A culture that does not prioritise quality may result in a lack of motivation, accountability, and adherence to quality control processes. |
|
Strategies to Overcome |
Employee Empowerment: Empower employees to take ownership of quality by providing them with the tools, knowledge, and authority to contribute to continuous improvement efforts. |
Employee Empowerment: Empower employees to take ownership of quality by providing them with the tools, knowledge, and authority to contribute to continuous improvement efforts. |
Adapting to Technological Advancements
Adapting to Technological Advancements |
|
Challenge |
Nature of Challenge: The rapid pace of technological advancements requires organisations to adapt quickly to remain competitive. |
Impact on Quality Control: Lagging in adopting new technologies may result in outdated quality control practices, hindering competitiveness. |
|
Strategies to Overcome |
Agile Adoption Frameworks: Implement agile frameworks for technology adoption, allowing for rapid testing and integration of new technologies. Foster a culture that embraces experimentation and learning. |
Collaboration with Technology Partners: Collaborate with technology partners and stay connected with industry trends. Leverage partnerships to access cutting-edge technologies and remain at the forefront of innovation. |
Future Trends in Quality Control
The landscape of quality control is undergoing a profound transformation driven by technological advancements, evolving consumer expectations, and a heightened focus on sustainability. As industries embrace the era of Industry 4.0, the future of quality control is shaped by innovative trends that promise to redefine the way products are manufactured, inspected, and ensured for compliance. In this section, we explore the cutting-edge trends poised to shape the future of quality control.
Integration of Artificial Intelligence (AI) and Machine Learning (ML)
Integration of Artificial Intelligence (AI) and Machine Learning (ML) |
|
AI-Powered Predictive Quality Analytics |
AI algorithms analyse vast datasets from production processes, identifying patterns and predicting potential quality issues before they occur. |
Impact: Proactive identification of defects allows for preventive measures, reducing rework costs and enhancing overall product quality. |
|
Machine Learning for Anomaly Detection |
ML models continuously learn from normal production data, enabling them to detect anomalies and deviations that may indicate potential defects. |
Impact: Real-time anomaly detection enhances the speed and accuracy of identifying irregularities, minimising the risk of defective products reaching the market. |
Digital Twins for Virtual Quality Control
Digital Twins for Virtual Quality Control |
|
Digital Twin Technology |
Digital twins create virtual replicas of physical products or processes, allowing for in-depth analysis and simulation. |
Impact: In quality control, digital twins enable the virtual inspection of products, predicting potential defects and validating quality without physical prototypes. |
|
Virtual Reality (VR) and Augmented Reality (AR) for Inspection |
VR and AR technologies provide immersive experiences for inspectors, allowing them to visualise and assess products in a virtual environment. |
Impact: Inspectors can identify defects, assess product features, and collaborate remotely, streamlining inspection processes and reducing the need for physical presence. |
Blockchain for Transparent and Traceable Quality Assurance
Blockchain for Transparent and Traceable Quality Assurance |
|
Blockchain in Supply Chain Quality Assurance |
Blockchain technology creates a decentralised and transparent ledger for recording and verifying transactions across the supply chain. |
Impact: Enhanced traceability ensures the authenticity of products, reduces the risk of counterfeiting, and provides consumers with verifiable information about the origin and quality of goods. |
|
Smart Contracts for Automated Compliance |
Smart contracts are self-executing contracts with the terms directly written into code, automating compliance checks throughout the supply chain. |
Impact: Automated compliance ensures that quality standards are consistently met, minimising the likelihood of deviations and improving overall supply chain efficiency. |
IoT-Enabled Smart Sensors and Real-Time Monitoring
IoT-Enabled Smart Sensors and Real-Time Monitoring |
|
Proliferation of IoT-Enabled Sensors |
IoT sensors embedded in equipment and products collect real-time data on various parameters such as temperature, humidity, and performance. |
Impact: Continuous monitoring allows for early detection of deviations, facilitates preventive actions, and ensures that products meet quality standards. |
|
Edge Computing for Real-Time Data Processing |
Edge computing processes data locally on IoT devices, reducing latency and enabling real-time analysis of quality-related data. |
Impact: Faster decision-making based on real-time insights enhances the agility of quality control processes, particularly in high-speed production environments. |
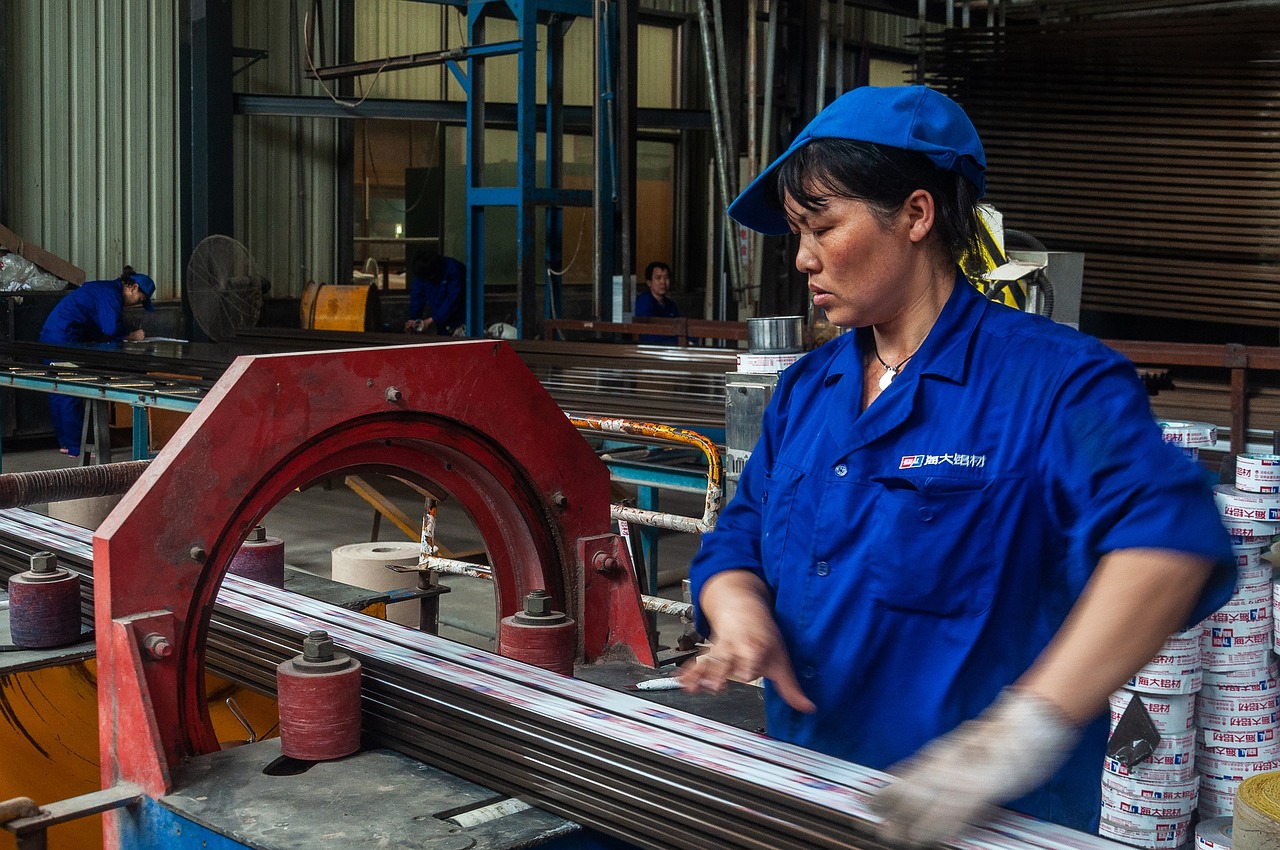
Advanced Robotics and Collaborative Automation
Advanced Robotics and Collaborative Automation |
|
Evolution of Collaborative Robotics (Cobots) |
Cobots, designed to work alongside humans, are becoming more sophisticated and adaptable, enhancing collaboration in quality control processes. |
Impact: Collaborative automation increases flexibility, efficiency, and precision in tasks such as assembly verification, inspection, and handling delicate components. |
|
Robotics with AI Vision Systems |
Robotics equipped with AI-powered vision systems can visually assess and identify defects, enhancing the accuracy of inspection processes. |
Impact: AI-driven robotics offer a level of sophistication in defect detection, ensuring high precision and reducing false positives. |
Advanced Non-Destructive Testing (NDT) Techniques
Advanced Non-Destructive Testing (NDT) Techniques |
|
Advancements in NDT Technologies |
NDT methods, such as ultrasonic testing, radiography, and magnetic particle testing, are evolving with digitalisation and automation. |
Impact: Digital radiography, phased array ultrasonics, and other advancements provide more detailed and efficient defect detection, particularly in complex structures. |
|
Incorporation of AI in NDT |
AI is being integrated into NDT processes to analyse complex data sets, improving the accuracy and speed of defect identification. |
Impact: AI enhances the capabilities of NDT techniques, enabling more nuanced analysis and reducing the reliance on human interpretation. |
Quality Control in Additive Manufacturing (3D Printing)
Quality Control in Additive Manufacturing (3D Printing) |
|
In-Process Monitoring in 3D Printing |
Real-time monitoring and feedback systems are being integrated into 3D printing processes to ensure the quality of printed components during production. |
Impact: Continuous monitoring prevents defects and deviations in real time, optimising the additive manufacturing process. |
|
Machine Learning for Material Quality Prediction |
ML algorithms are employed to predict material properties and quality in 3D printing, aiding in material selection and process optimisation. |
Impact: Predictive models enhance the understanding of how different materials behave during printing, contributing to the production of high-quality and reliable 3D-printed components. |
Focus on Sustainable and Green Manufacturing Practices
Focus on Sustainable and Green Manufacturing Practices |
|
Circular Economy Principles in Quality Control |
Embracing circular economy principles involves designing products for longevity, reusability, and recyclability, reducing waste and environmental impact. |
Impact: Quality control plays a crucial role in ensuring products are manufactured with sustainability in mind, aligning with growing consumer demands for eco-friendly practices. |
|
Environmental Impact Assessment in Quality Metrics |
Quality control metrics are expanding to include assessments of a product's environmental impact, considering factors such as energy efficiency and materials used. |
Impact: Manufacturers can make informed decisions to reduce their carbon footprint, aligning with global efforts towards sustainable and responsible production. |
Collaborative Quality Assurance Platforms
Collaborative Quality Assurance Platforms |
|
Cloud-Based Collaborative Platforms |
Cloud-based platforms enable real-time collaboration among stakeholders, including manufacturers, suppliers, and quality control teams. |
Impact: The seamless collaboration fosters a conducive environment for enhanced communication, expedites decision-making processes, and guarantees that all stakeholders engaged in the supply chain are in harmonious alignment regarding quality standards. This collaborative synergy not only promotes efficient information exchange but also contributes to a unified understanding of and commitment to maintaining stringent quality benchmarks. |
|
Integration of Quality Assurance with Enterprise Systems |
Quality assurance systems are progressively becoming more intertwined with enterprise resource planning (ERP) and manufacturing execution systems (MES), fostering a comprehensive and streamlined approach to operations. This strategic integration not only ensures the seamless alignment of quality control processes with broader organisational systems but also contributes to the synergy of data and processes. This holistic integration aims to enhance operational efficiency, data visibility, and overall effectiveness, thereby reinforcing the commitment to achieving operational excellence in the manufacturing landscape. |
Impact: Integration reduces silos, enhances data visibility, and enables more efficient quality control processes, contributing to overall operational excellence. |
Regulatory Embrace of Advanced Technologies
Regulatory Embrace of Advanced Technologies |
|
Regulatory Recognition of Innovative Quality Control Technologies |
Regulatory bodies are acknowledging and adapting to the integration of advanced technologies in quality control processes. |
Impact: Regulatory acceptance facilitates the widespread adoption of innovative technologies, promoting a harmonised approach to quality standards. |
|
Collaboration Between Regulators and Industry Innovators |
Regulatory agencies are increasingly collaborating with industry innovators to understand and adapt regulations to emerging technologies. |
Impact: This collaboration fosters an environment where regulations remain relevant, ensuring that they support rather than impede the adoption of cutting-edge quality control practices. |
Navigating the Horizon of Quality Control Excellence
As we conclude this exploration of quality control excellence, it is evident that the journey is far from over. The horizon of possibilities stretches endlessly, inviting organisations to embark on a voyage marked by innovation, resilience, and a commitment to surpassing existing standards. One more time, let's reflect on the key takeaways and the enduring principles that underpin a culture of continuous improvement.
The Power of Continuous Improvement |
Adaptability as a Cornerstone. Continuous improvement is not a destination but a mindset—an ongoing commitment to adapt, evolve, and enhance. Organisations that embrace change with resilience are better positioned to navigate the uncertainties of the manufacturing landscape. |
Human-Centric Approach. Empowering employees through training, recognition, and a collaborative culture fuels the engine of continuous improvement. |
|
The Interplay of Technology and Tradition |
Harmony Between Automation and Human Oversight. The rise of advanced technologies like AI, IoT, and robotics does not diminish the importance of human judgment. Striking a balance between automation and human oversight is key to a harmonious and effective quality control ecosystem. |
Preservation of Core Principles. Amidst technological advancements, the core principles of quality control—consistency, precision, and adherence to standards—must remain unwavering. Technology should amplify these principles rather than compromise them. |
|
The Interplay of Technology and Tradition |
Harmony Between Automation and Human Oversight. The rise of advanced technologies like AI, IoT, and robotics does not diminish the importance of human judgment. Striking a balance between automation and human oversight is key to a harmonious and effective quality control ecosystem. |
Preservation of Core Principles. Amidst technological advancements, the core principles of quality control—consistency, precision, and adherence to standards—must remain unwavering. Technology should amplify these principles rather than compromise them. |
|
Strategies to Navigate Challenges |
Proactive Problem Solving. Challenges in quality control are not roadblocks but opportunities for innovation. Proactive problem-solving, whether in the face of variability, resistance to change, or global supply chain complexities, is the catalyst for growth. |
Cultural Transformation. Shifting an organisational culture towards quality excellence requires persistent effort and leadership commitment. A culture that values quality at its core inspires employees, fosters collaboration, and propels the organisation towards continuous improvement. |
|
Eyes on the Future: Anticipating Trends |
Innovation as a Guiding Light. Future trends in quality control, from AI-driven analytics to sustainable manufacturing practices, are beacons guiding organisations towards innovation. Understanding these trends is key to staying ahead in an ever-evolving landscape. |
Regulatory Alignment and Collaboration. Regulatory bodies are evolving to embrace technological advancements, reflecting a synergy between industry innovation and regulatory compliance. Organisations that actively collaborate with regulators can navigate the regulatory landscape more seamlessly. |
|
The Tapestry of Quality Control Excellence |
Holistic Integration. Quality control is not a siloed function but an integrated tapestry woven into the fabric of manufacturing. Cloud-based platforms, digital twins, and collaborative approaches are threads that bind various elements into a seamless whole. |
Sustainability as a Guiding Principle. In the pursuit of quality, the integration of sustainability is not just a trend; it's a priority. Circular economy principles, environmental impact assessments, and green manufacturing are integral components of a responsible and forward-thinking approach. |
In the ever-shifting landscape of manufacturing, those who dare navigate the seas of continuous improvement and embrace emerging technologies will not merely survive—they will thrive. The future belongs to the pioneers, innovators, and champions of quality control excellence.
So, as you stand on the precipice of the future, equipped with insights, strategies, and a mindset of perpetual improvement, the question is not just "What challenges lie ahead?" but rather "What extraordinary heights can we reach?"
May your journey be filled with discovery, innovation, and a relentless pursuit of quality that propels you to new summits of manufacturing excellence. Safe travels, and may the winds of continuous improvement carry you ever forward.
Comments
No comments yet!Add a Comment
You must be logged in to post a comment.