In manufacturing, the efficiency of an assembly line can make or break a company's success. As production demands rise, so does the complexity of orchestrating a seamless flow from one station to the next. At the heart of this challenge lies the Assembly Line Balancing Problem (ALBP), a puzzle that manufacturers constantly strive to solve to optimise productivity, minimise costs, and maintain high-quality standards.
The ALBP entails meticulously distributing work tasks among different stations to ensure each station operates at its full potential, eliminating bottlenecks and preventing idle time. Unravelling this puzzle requires a nuanced understanding of production processes and a keen eye for optimising each step.
Amidst the complexities of the ALBP, a promising strategy has emerged as a beacon of efficiency Task Splitting. This innovative approach involves breaking down larger tasks into smaller, more manageable components, redistributing workloads, and strategically assigning them across the assembly line. In this blog post, we will embark on a journey through the world of assembly line balancing, shedding light on the intricacies of the ALBP and exploring how task splitting emerges as a powerful tool to overcome its challenges.
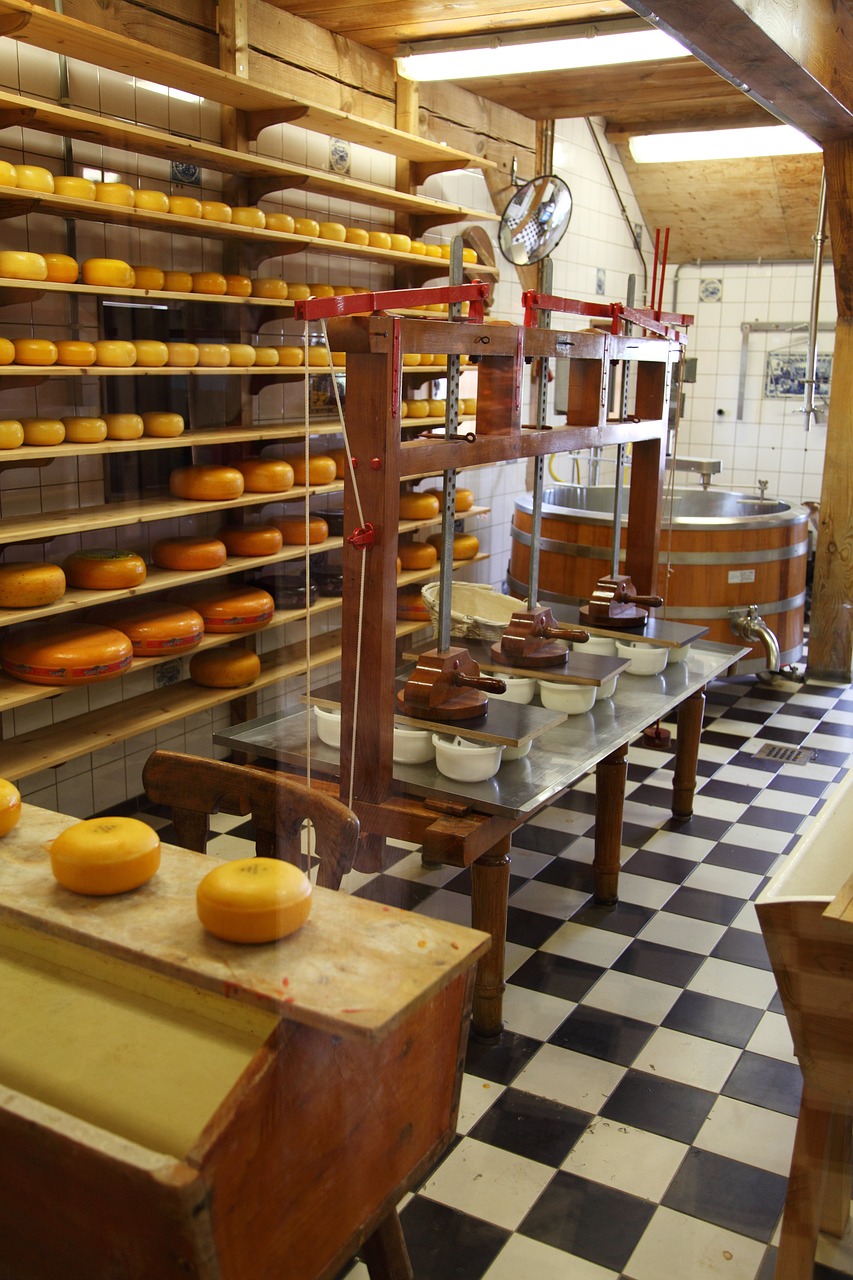
Understanding the Assembly Line Balancing Problem (ALBP)
In the labyrinth of modern manufacturing, the Assembly Line Balancing Problem (ALBP) stands as a formidable challenge that demands careful consideration. At its essence, ALBP involves the art of orchestrating a harmonious workflow across the assembly line, ensuring that each station operates at its peak efficiency. To comprehend the significance of this problem, let's delve into key aspects.
Significance of ALBP
The Assembly Line Balancing Problem refers to the task of optimising the allocation of tasks or work elements across different workstations along an assembly line. This optimisation seeks to achieve a balanced and efficient production process. A well-balanced assembly line directly impacts a company's bottom line. It reduces idle time, minimises bottlenecks, and enhances overall productivity. Moreover, it plays a pivotal role in maintaining product quality and meeting customer demands in a timely manner.
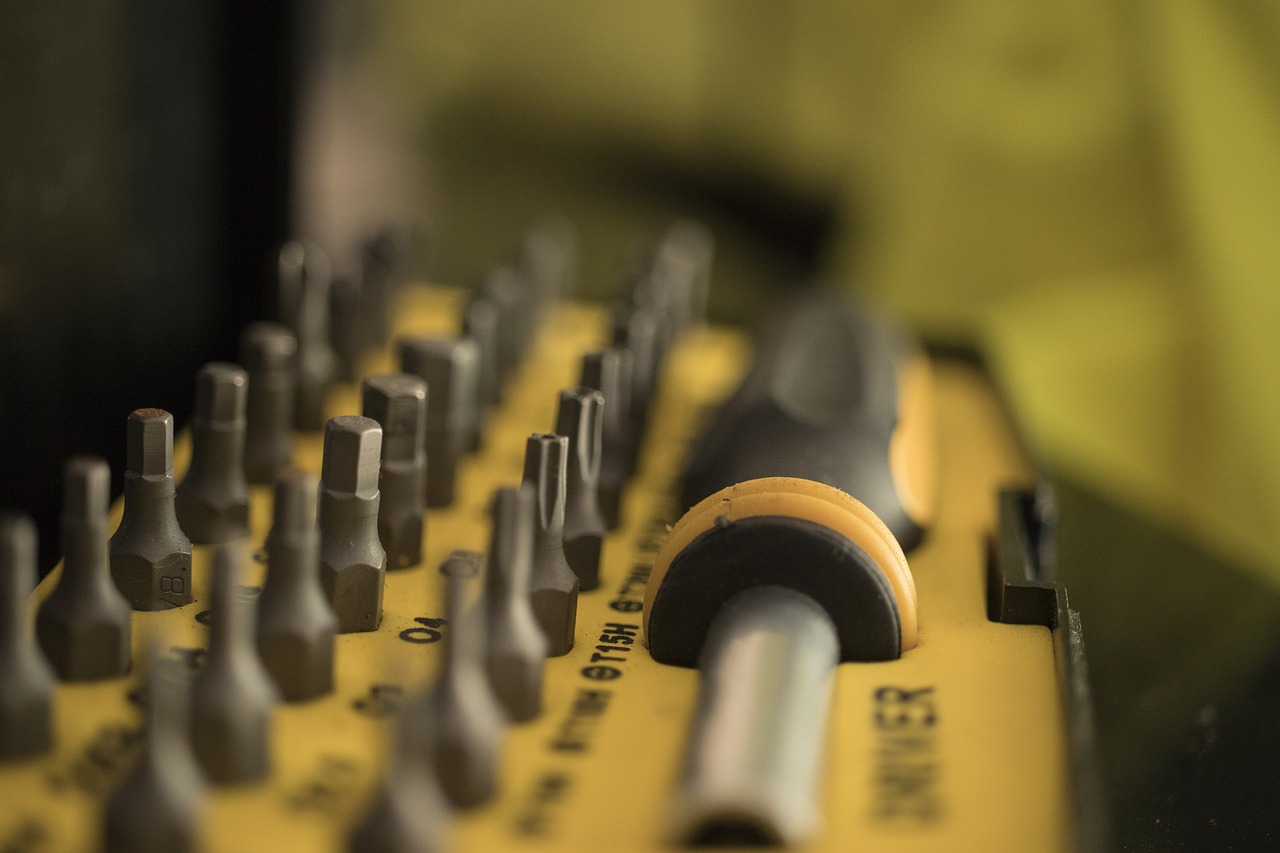
Impact of Unbalanced Assembly Lines
An unbalanced assembly line can lead to certain workstations being overburdened while others need to be more utilised. This imbalance can decrease overall productivity and increase production costs. Costs Inefficiencies in the assembly line can contribute to higher operational costs, affecting the competitiveness of a company in the market. An unbalanced assembly line may lead to variations in production speeds, potentially compromising the quality of the final product. Maintaining consistent quality standards becomes challenging in such scenarios.
Illustrating the Need for Efficient Assembly Line Balancing
Understanding the intricacies of the ALBP is the first step toward developing effective solutions. The automotive sector is a poignant example of the crucial role of the efficient assembly line. Balancing tasks across stations ensures that each vehicle undergoes the necessary assembly steps in a synchronised manner, optimising production time and quality. Also, in the production of electronic devices, the intricate nature of components and assembly steps demands a finely tuned assembly line. Any imbalance can result in delays, increased defect rates, and missed market opportunities.
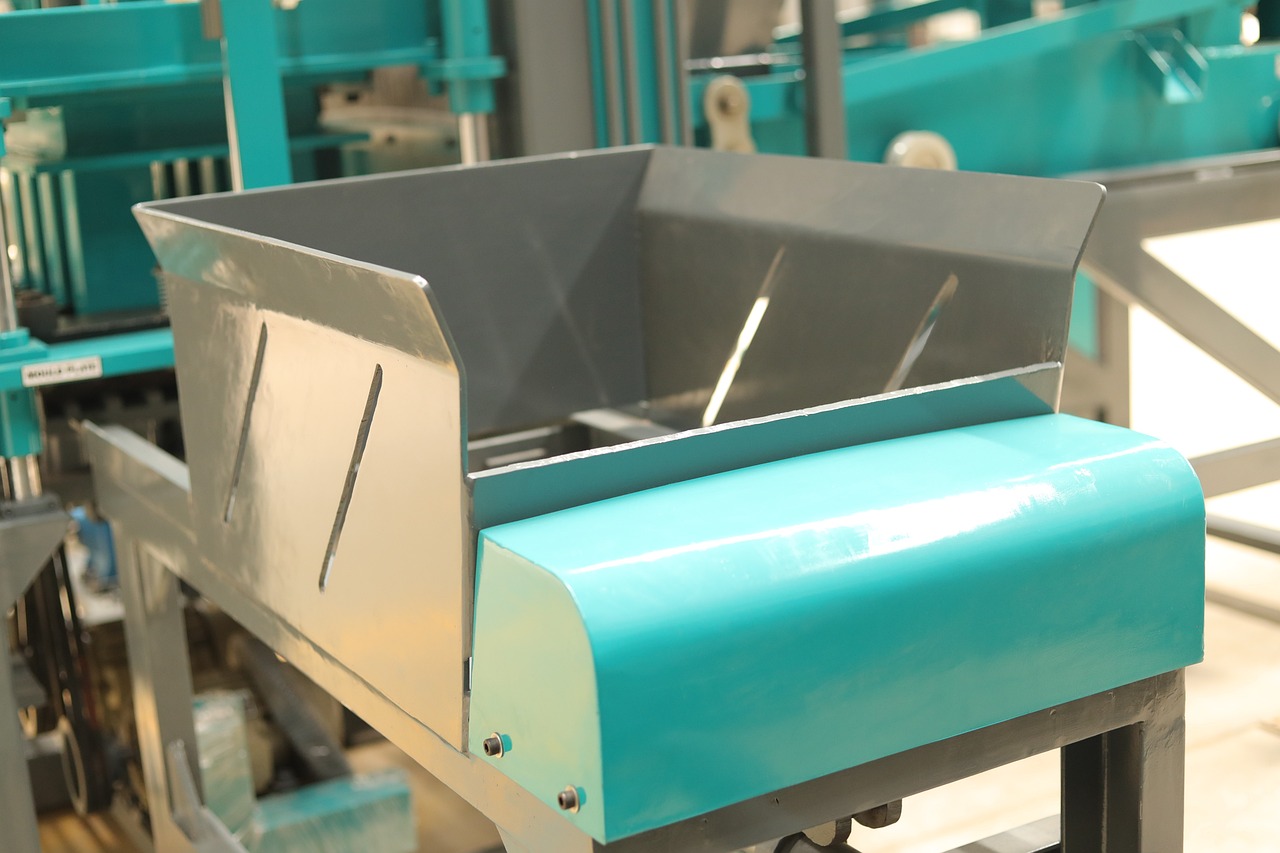
Unravelling the Task-Splitting Concept
As we navigate through the complexities of the Assembly Line Balancing Problem (ALBP), the spotlight turns to a dynamic strategy that has been gaining prominence in the realm of manufacturing optimisation Task Splitting. We aim to demystify the concept, providing a comprehensive understanding of what task splitting entails and why it is considered a valuable tool in the pursuit of efficient assembly line operations.
What is Task Splitting?
Task splitting involves breaking down larger tasks or work elements into smaller, more manageable components. These components are then strategically assigned across different workstations, contributing to a more balanced and efficient assembly line. In an assembly line tasked with building electronic devices, task splitting could involve breaking down the assembly process into sub-tasks such as component installation, quality checks, and final assembly. Each of these sub-tasks can then be assigned to specific workstations.
Benefits of Task Splitting in Optimizing Workflow
Enhanced Flexibility |
Task splitting provides some flexibility in adapting to varying production demands. It allows for the redistribution of workloads based on real-time needs and fluctuations in demand. |
Reduced Bottlenecks |
Task splitting helps alleviate bottlenecks by breaking down tasks into smaller components. This ensures that every workstation supports the overall production flow. |
Improved Resource |
Utilisation Workstations can be more efficiently utilised when tasks are split, preventing overburdening of specific stations and optimising the use of available resources. |
Task splitting is not a one-size-fits-all solution but rather a dynamic strategy that can be tailored to meet the specific needs of different manufacturing processes.
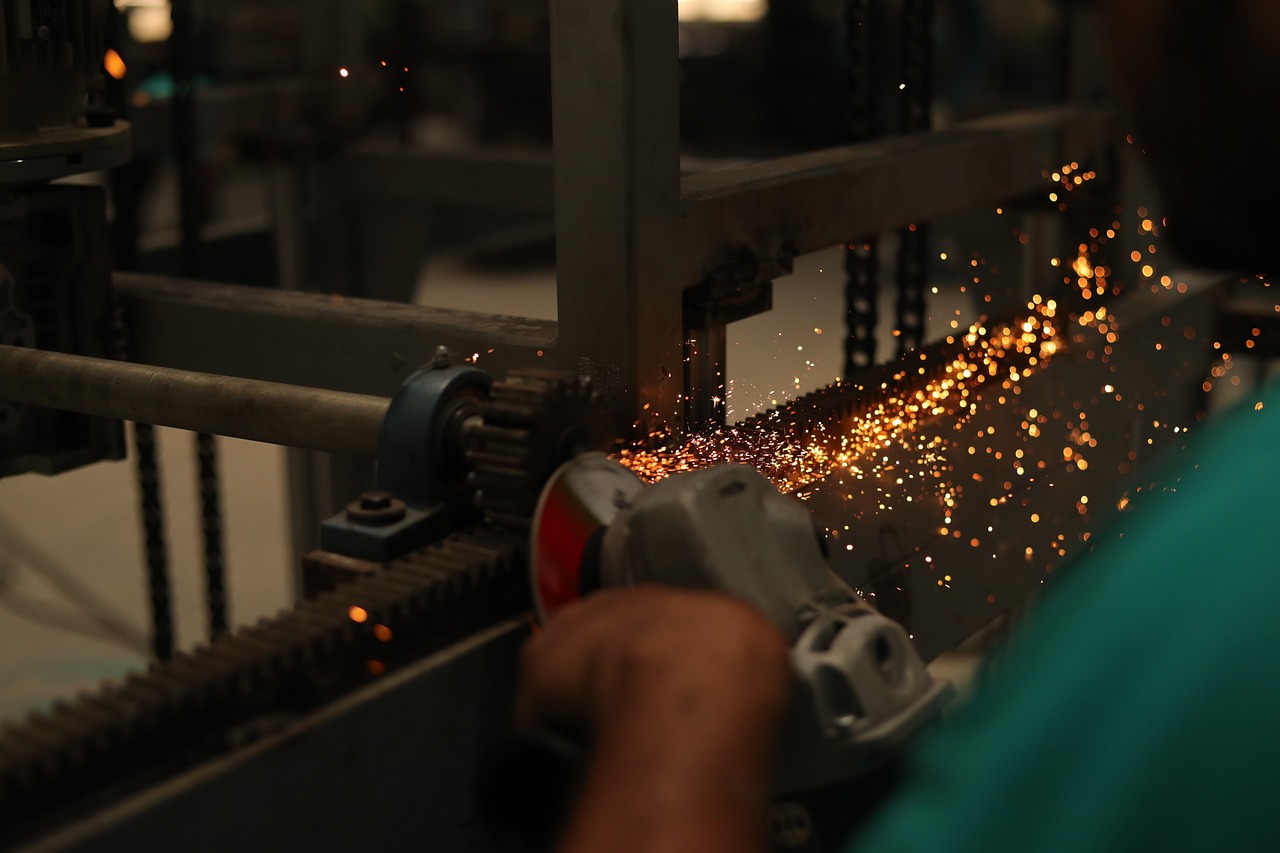
Challenges in Assembly Line Balancing and How Task Splitting Addresses Them
Assembly Line Balancing Problem (ALBP) requires an in-depth understanding of the challenges inherent in balancing complex production processes. In this section, we will dissect common challenges faced by manufacturers and elucidate how the strategic implementation of task splitting serves as a powerful tool in overcoming these hurdles.
Exploration of Common Challenges in Balancing Assembly Lines
Variability in Task Durations |
Unequal task durations can lead to uneven workloads across stations, creating bottlenecks and slowing down the entire assembly line. |
Dependency Relationships |
Some tasks may be dependent on the completion of others, leading to coordination challenges and potential delays. |
Changing Production Demands |
Fluctuations in production volumes or variations in product specifications can disrupt the balance of the assembly line. |
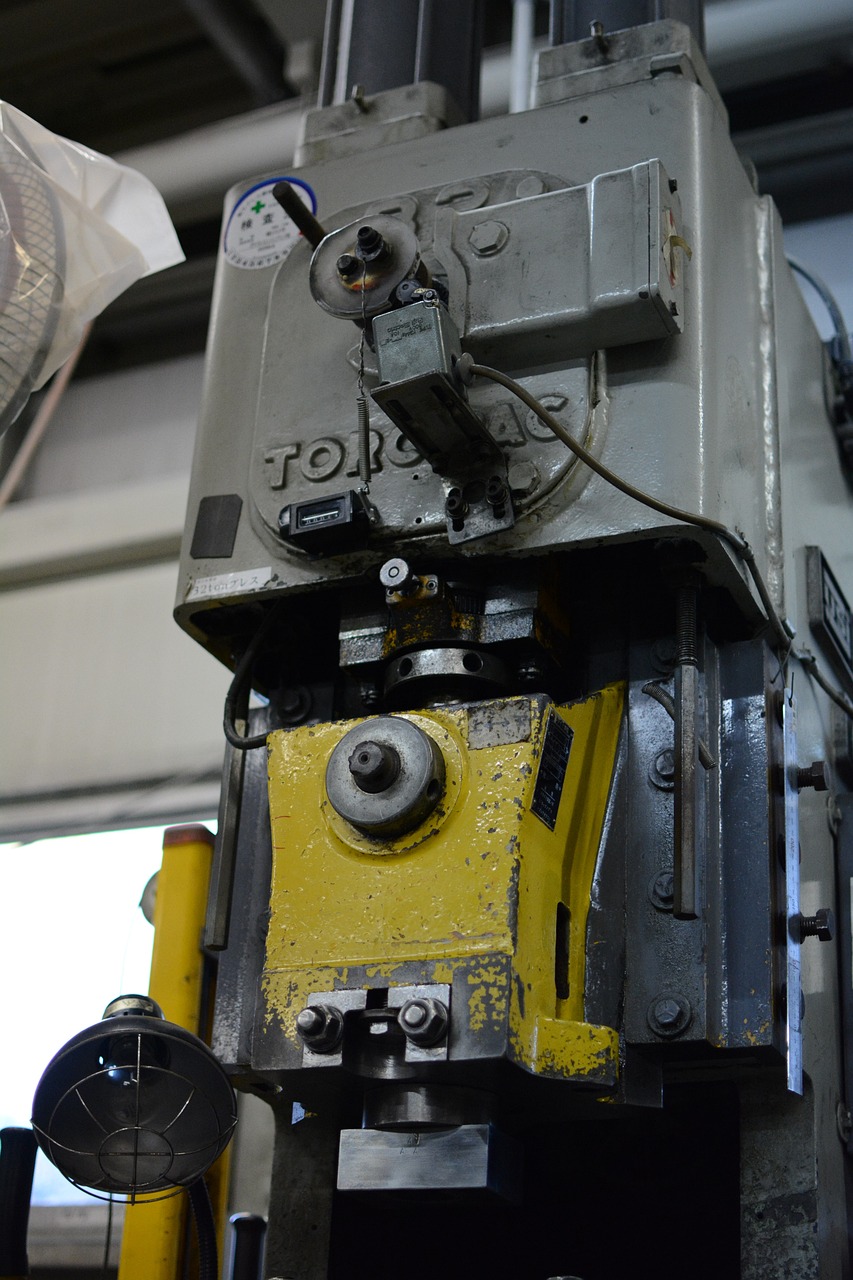
Detailed Explanation of How Task Splitting Tackles Challenges
Task Duration Variability |
Task splitting allows for breaking down tasks into smaller components, reducing the impact of variable task durations. Smaller, more manageable tasks facilitate a more even distribution of workloads. |
Dependency Relationships |
Task splitting enables parallelisation by breaking down dependencies. Sub-tasks with less interdependence can be assigned concurrently, preventing sequential bottlenecks. |
Changing Production |
Demands Task splitting offers flexibility by allowing the redistribution of work elements in response to changing demands. This adaptability helps maintain efficiency during periods of fluctuating production requirements. |
By strategically addressing these challenges through task splitting, manufacturers can navigate the intricacies of assembly line balancing with greater precision.
Strategies for Task Splitting in Assembly Line Balancing
As we explore the nuances of task splitting in the context of the Assembly Line Balancing Problem (ALBP), it becomes essential to delve into specific strategies that manufacturers can employ to implement this dynamic approach effectively. Here, we will outline various task-splitting methodologies and shed light on how these strategies can be harnessed to achieve optimal assembly line efficiency.
Task-Splitting Strategies and Methodologies
Sequential Task Splitting |
Breaking down tasks in a sequential manner, where one sub-task logically follows another, can help manage dependencies and ensure a smooth flow of work. |
Parallel Task Splitting |
Assigning multiple sub-tasks simultaneously to different workstations can expedite the assembly process by capitalising on parallelisation opportunities. |
Flexible Task Splitting |
Designing task-splitting strategies with adaptability in mind, allowing for the dynamic redistribution of work elements based on real-time production demands. |
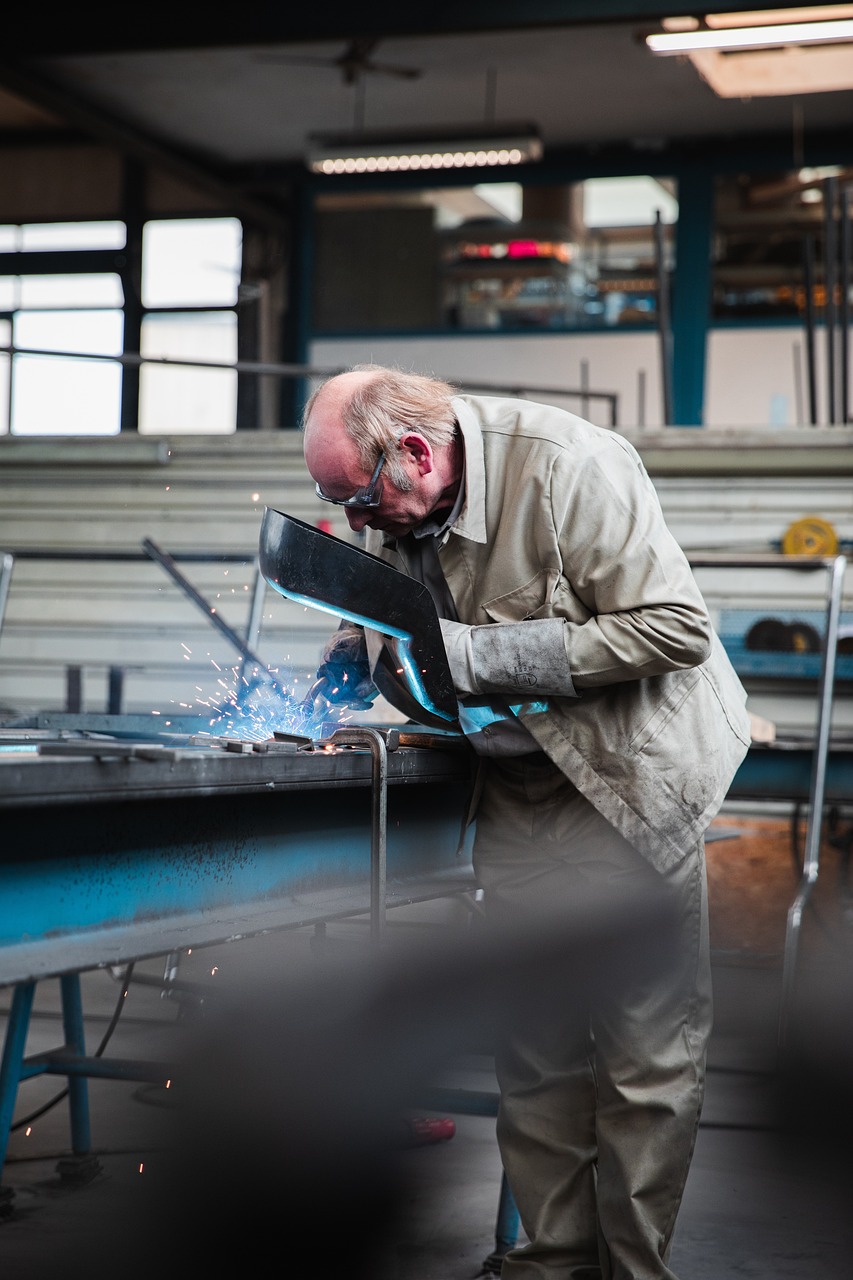
The Role of Technology in Aiding Task-Splitting Decisions
Simulation and Modeling |
Tools Advanced simulation tools enable manufacturers to model different task-splitting scenarios and predict their impact on assembly line efficiency before implementation. |
Data Analytics |
Harnessing data analytics to monitor and analyse real-time production data facilitates informed decision-making when redistributing workloads through task splitting. |
Machine Learning Algorithms |
Implementing machine learning algorithms can optimise task splitting by learning from historical data, adapting to changing production patterns, and suggesting optimal task distributions. |
Practical Tips for Implementing Task Splitting in Different Manufacturing Scenarios
Understand Workstation Capacities |
Prioritise task splitting based on the capacities and capabilities of each workstation, ensuring an even distribution of workloads. |
Regular Performance Monitoring |
Continuously monitor the assembly line's performance to identify bottlenecks or areas requiring adjustment in the task-splitting strategy. |
Employee Training and Collaboration |
Provide training to employees to adapt to the task-splitting approach and foster a collaborative environment that supports efficient workflow distribution. |
By tailoring task-splitting strategies to the specific needs of the assembly line, manufacturers can not only address the challenges of the ALBP but also enhance their overall production efficiency.
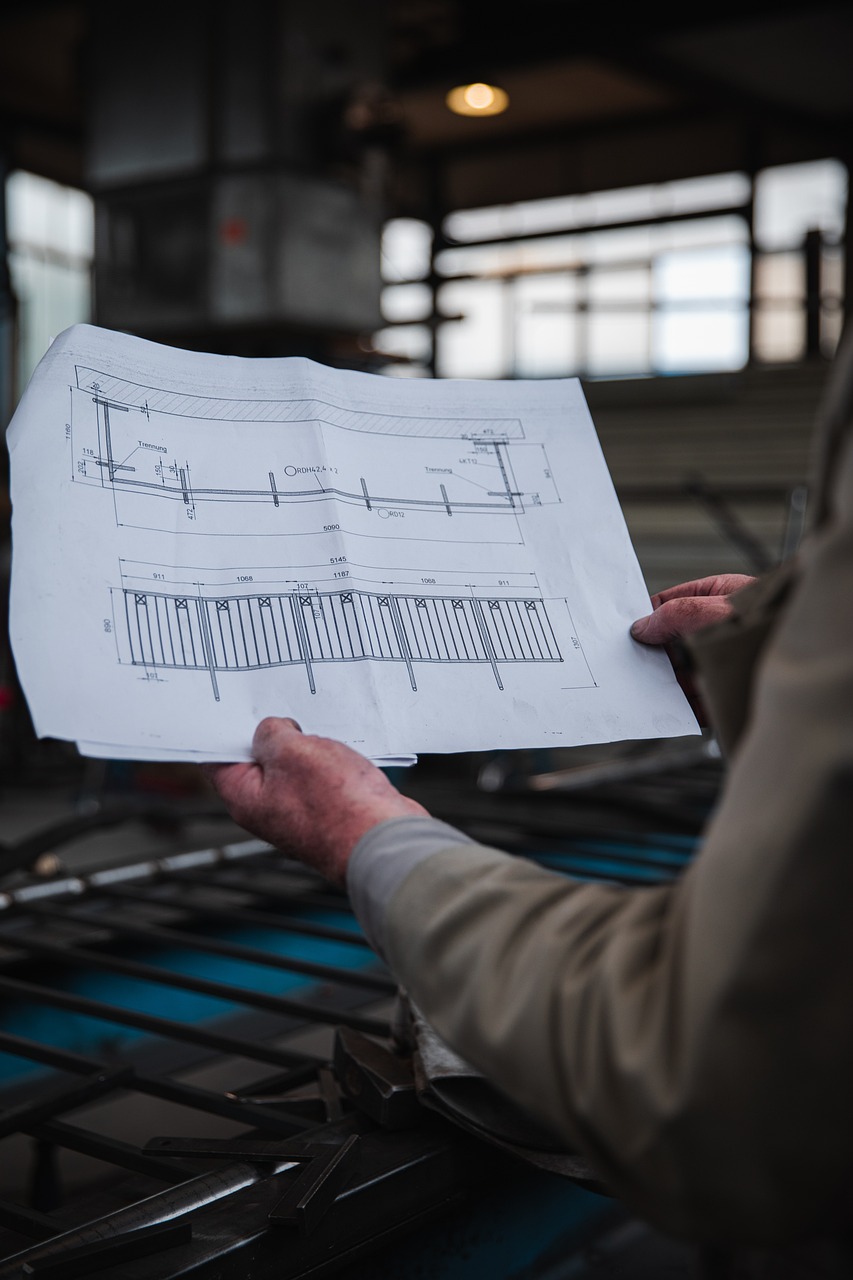
Features and Benefits of Task Splitting Tools in Streamlining the Process
Real-Time Monitoring and Analytics |
Tools equipped with real-time monitoring and analytics capabilities enable manufacturers to track the performance of each workstation. This facilitates data-driven decision-making when adjusting task-splitting strategies based on current production conditions. |
Collaborative Workforce Platforms |
Platforms that foster collaboration among workforce members enable seamless communication and coordination as task assignments change dynamically. |
Machine Learning |
Algorithms for Adaptive Optimization Delve into the potential of machine learning algorithms that continuously learn from historical data, adapting task splitting strategies to changing production patterns and optimising the overall assembly line balancing process. |
Selecting the Right Tools for Specific Manufacturing Needs
Scalability |
Assess the tools' scalability to ensure they can accommodate the manufacturing environment's evolving needs, especially those related to production expansions or changes in product lines. |
Integration with Existing Systems |
Evaluate the compatibility of task-splitting tools with existing manufacturing systems to ensure seamless integration without disrupting ongoing operations. |
User-Friendly |
Interfaces Consider tools with user-friendly interfaces to facilitate easy adoption by production managers and floor operators and promote efficient utilisation of task-splitting capabilities. |
By embracing these tools and technologies, manufacturers can empower themselves to navigate the complexities of assembly line balancing with precision.
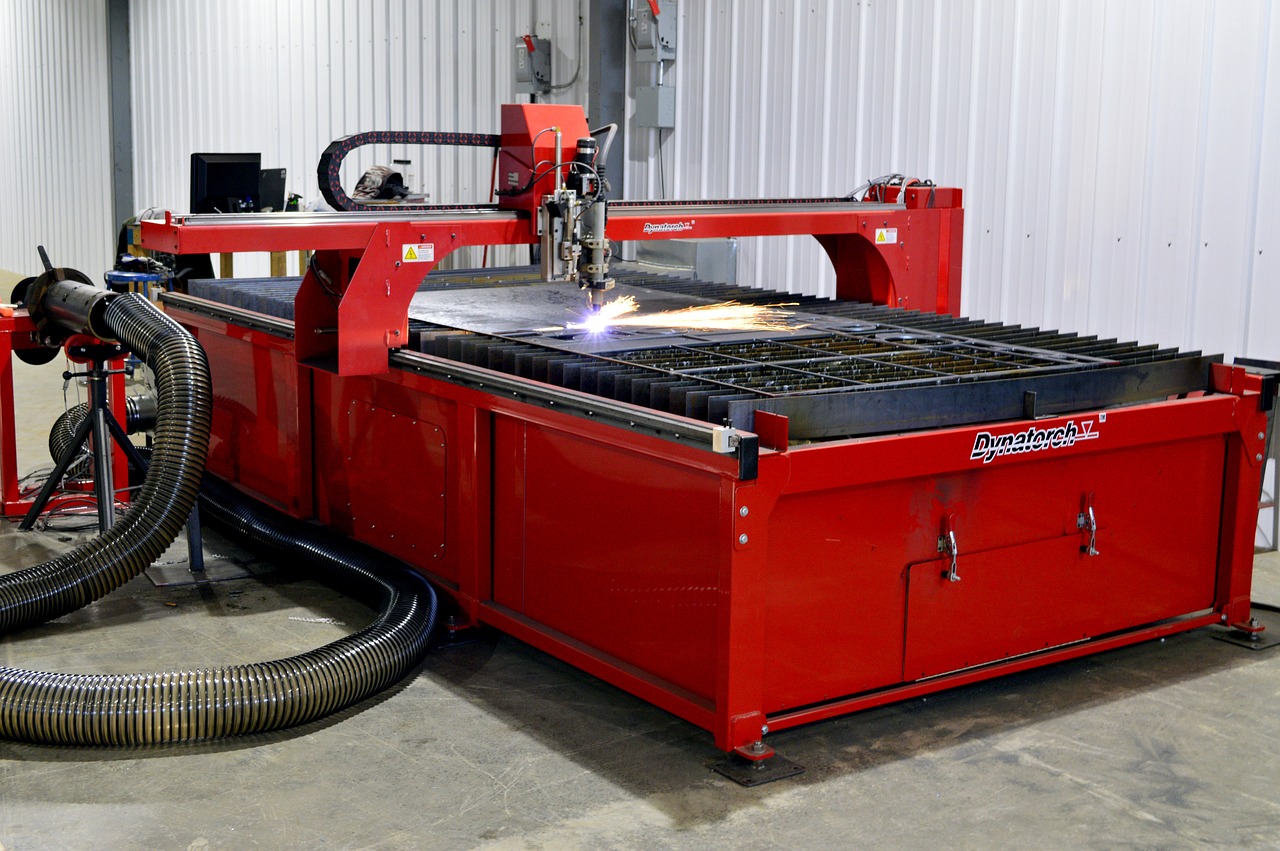
ALBP Emerges as a Critical Challenge that Demands Innovative Solutions
The Assembly Line Balancing Problem (ALBP) emerges as a critical challenge that demands innovative solutions. By exploring task splitting, we've unveiled a dynamic strategy that holds the potential to reshape the landscape of assembly line operations.
From understanding the foundational concepts of the ALBP to unravelling the intricacies of task splitting, our journey has taken us through the challenges faced by manufacturers and the strategic ways in which task splitting serves as a beacon of efficiency. Real-world case studies have illuminated the transformative impact of this approach across diverse industries, showcasing its adaptability and success.
The strategies outlined for task splitting, coupled with the insights into tools and technologies, provide manufacturers with a roadmap for optimising their assembly lines. From sequential and parallel task-splitting methodologies to the integration of simulation tools and machine learning algorithms, the possibilities for achieving a harmonious production flow are vast.
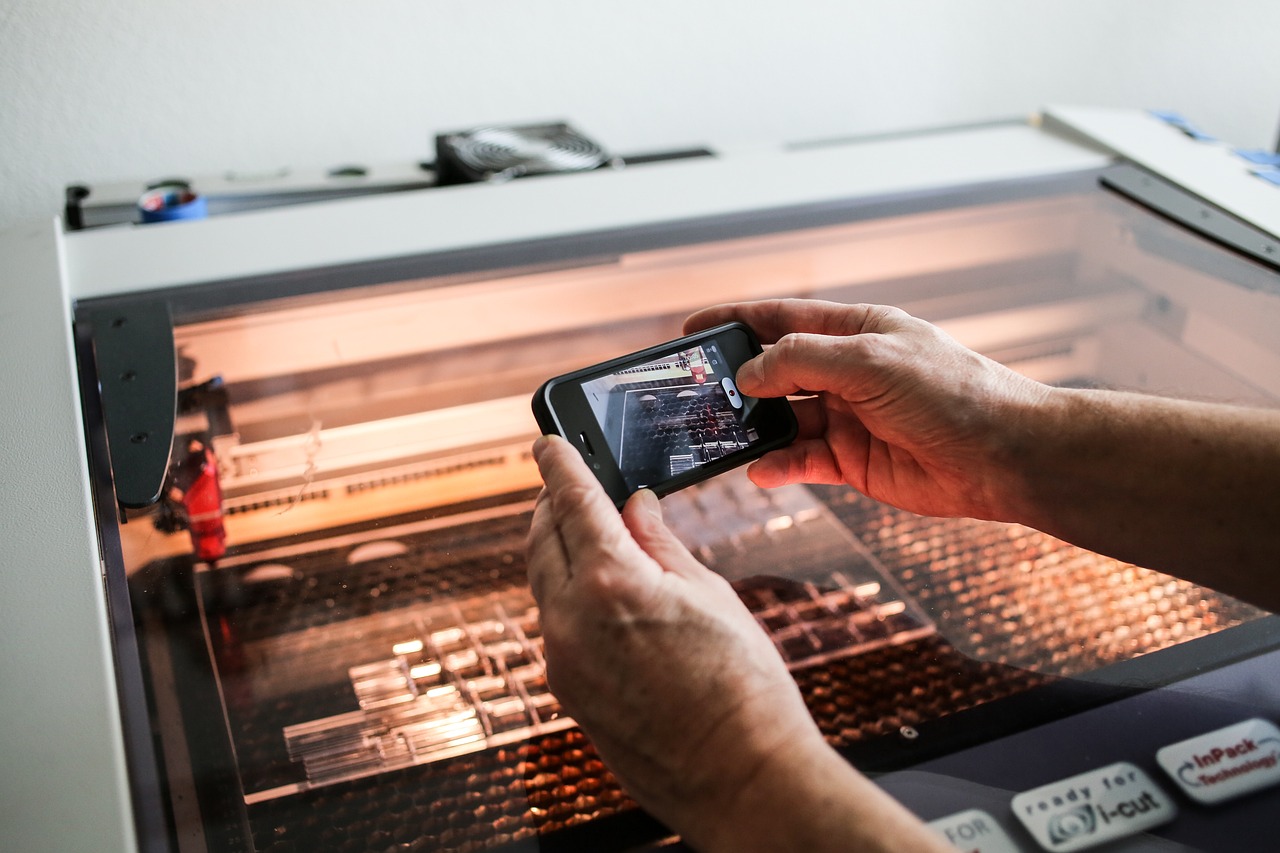
As manufacturers navigate an ever-evolving landscape, the adaptability and flexibility offered by task splitting become increasingly crucial. The ability to dynamically redistribute workloads in response to changing production demands positions task splitting as a cornerstone for agile and responsive manufacturing.
The Assembly Line Balancing Problem with Task Splitting is not just a theoretical puzzle but a practical challenge with tangible solutions. Manufacturers who embrace the power of task splitting can unlock new levels of efficiency, reduce idle time, and enhance overall productivity. As technology continues to advance and manufacturing processes evolve, task splitting stands as a beacon guiding the industry toward a future where assembly lines operate with unparalleled precision and adaptability.
IMAGE 10
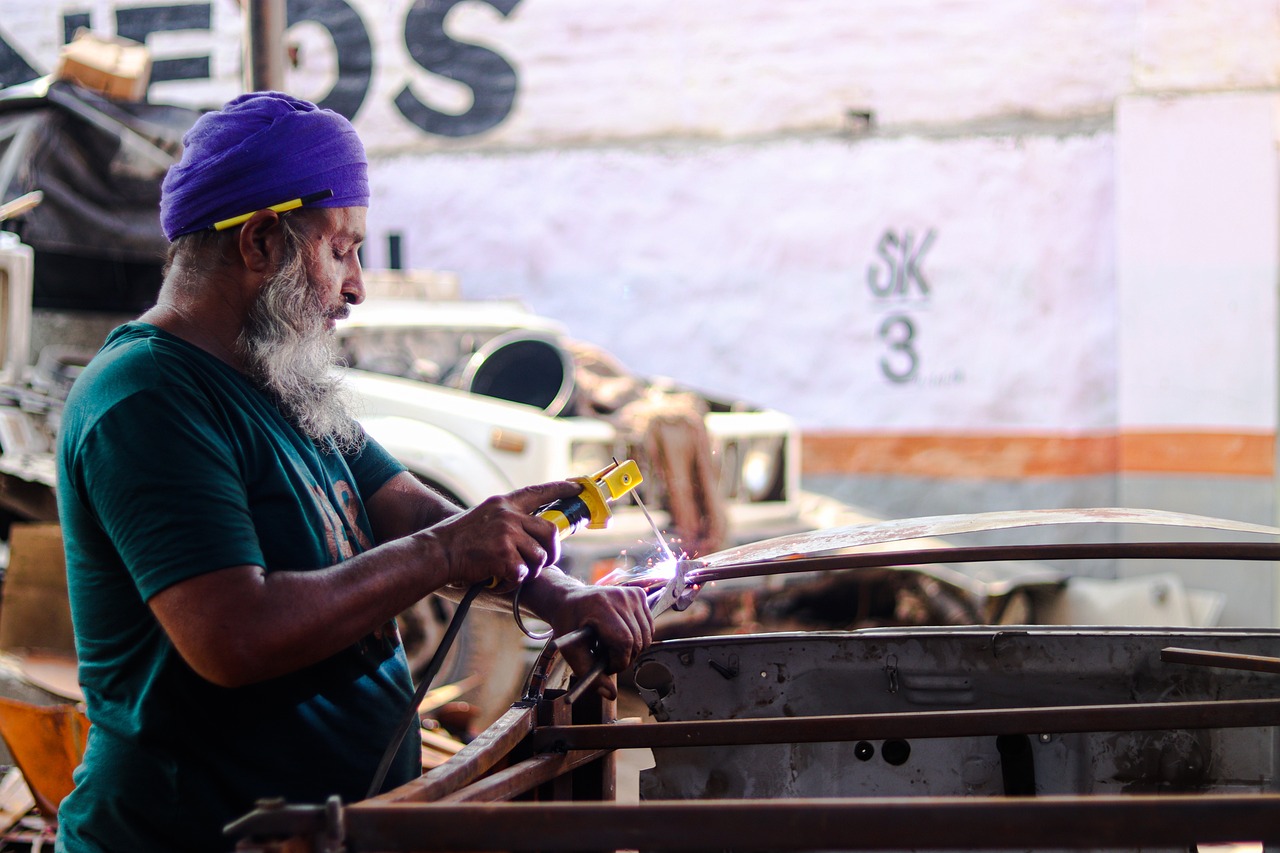
In the spirit of continuous improvement, the journey towards assembly line efficiency is ongoing. The fusion of strategic planning, real-world application, and cutting-edge technology represents a potent formula for success in tackling the complexities of assembly line balancing. As manufacturers embark on this journey, the transformative potential of task splitting beckons, promising a future where efficiency is not just a goal but a defining characteristic of modern manufacturing.
Comments
No comments yet!Add a Comment
You must be logged in to post a comment.