The quest for superior efficiency and unwavering quality is an enduring pursuit in the ever-evolving manufacturing landscape. Enter Performance Manufacturing, a dynamic approach that has redefined the manufacturing paradigm, steering it towards unprecedented operational excellence. This blog post embarks on a journey through the realms of Performance Manufacturing, unveiling its intricate tapestry of strategies, principles, and cutting-edge tools.
At its core, Performance Manufacturing is the relentless pursuit of perfection in every facet of the production process. It transcends traditional manufacturing methods and embraces a holistic philosophy where lean thinking, precision engineering, and statistical rigour converge. In today's hyper-competitive market, it's no longer enough to produce merely; one must make it with utmost efficiency and impeccable quality.
Consider this: A study by the National Institute of Standards and Technology (NIST) revealed that the cost of poor quality in manufacturing can account for as much as 20% of a company's revenue. Furthermore, an analysis by the Lean Enterprise Research Centre showed that nearly 60% of a typical manufacturing process is non-value-added activities, i.e., waste. These staggering statistics underscore the compelling imperative for manufacturers to embrace Performance Manufacturing as a means of survival and triumph.
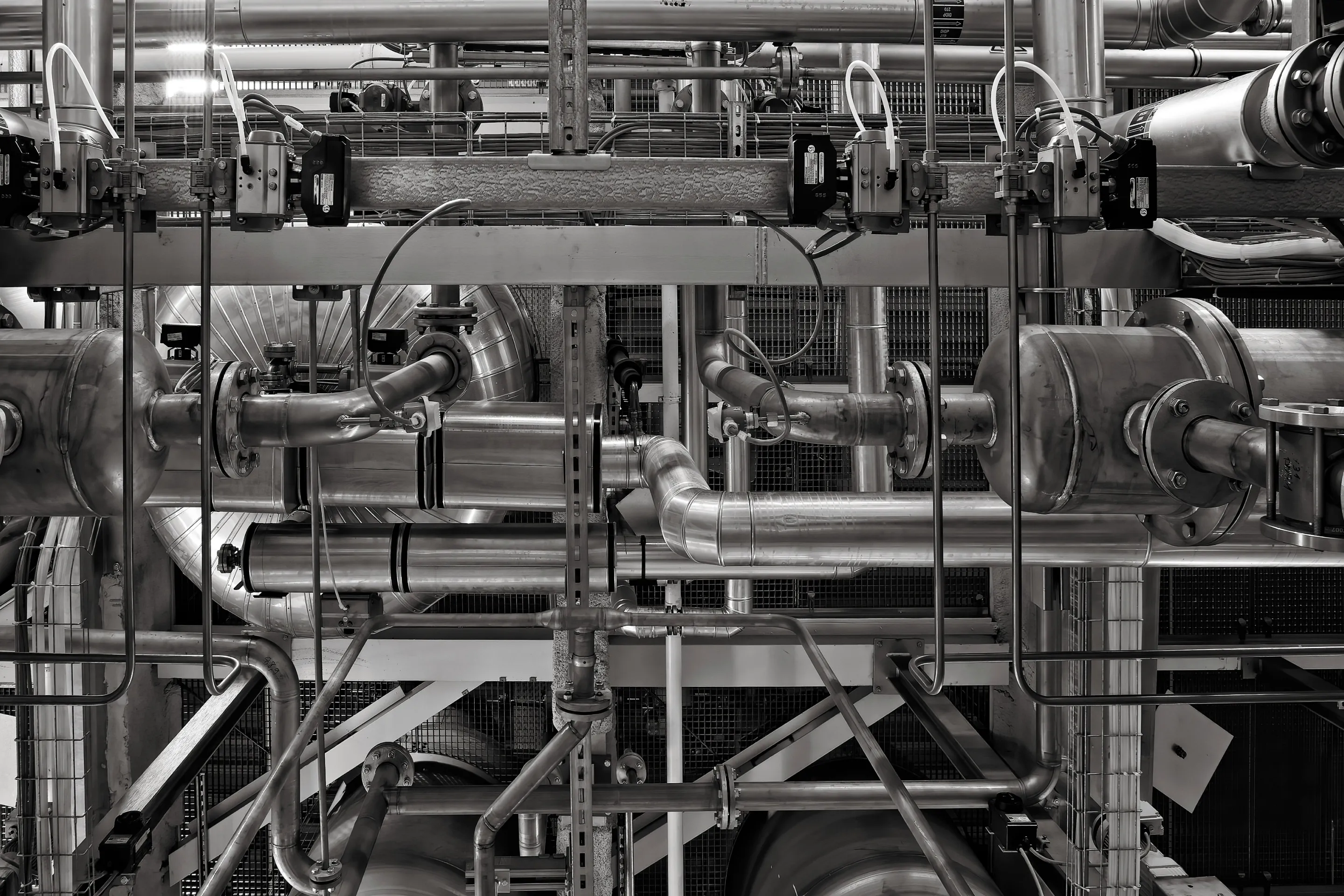
The evolution of manufacturing techniques has paved the way for Performance Manufacturing to take centre stage. Lean Manufacturing, with its relentless focus on waste elimination, has enabled companies to streamline their operations, reducing lead times and costs. On the other hand, Six Sigma is synonymous with quality control, and its DMAIC methodology has saved companies millions in defect-related expenses.
But Performance Manufacturing isn't just about principles; it's also about tools and techniques that empower manufacturers to optimise processes and realise their fullest potential. Value Stream Mapping, a visual representation of production processes, aids in identifying bottlenecks and inefficiencies. Total Quality Management (TQM) has been instrumental in shaping cultures of continuous improvement, fostering a relentless pursuit of quality excellence.
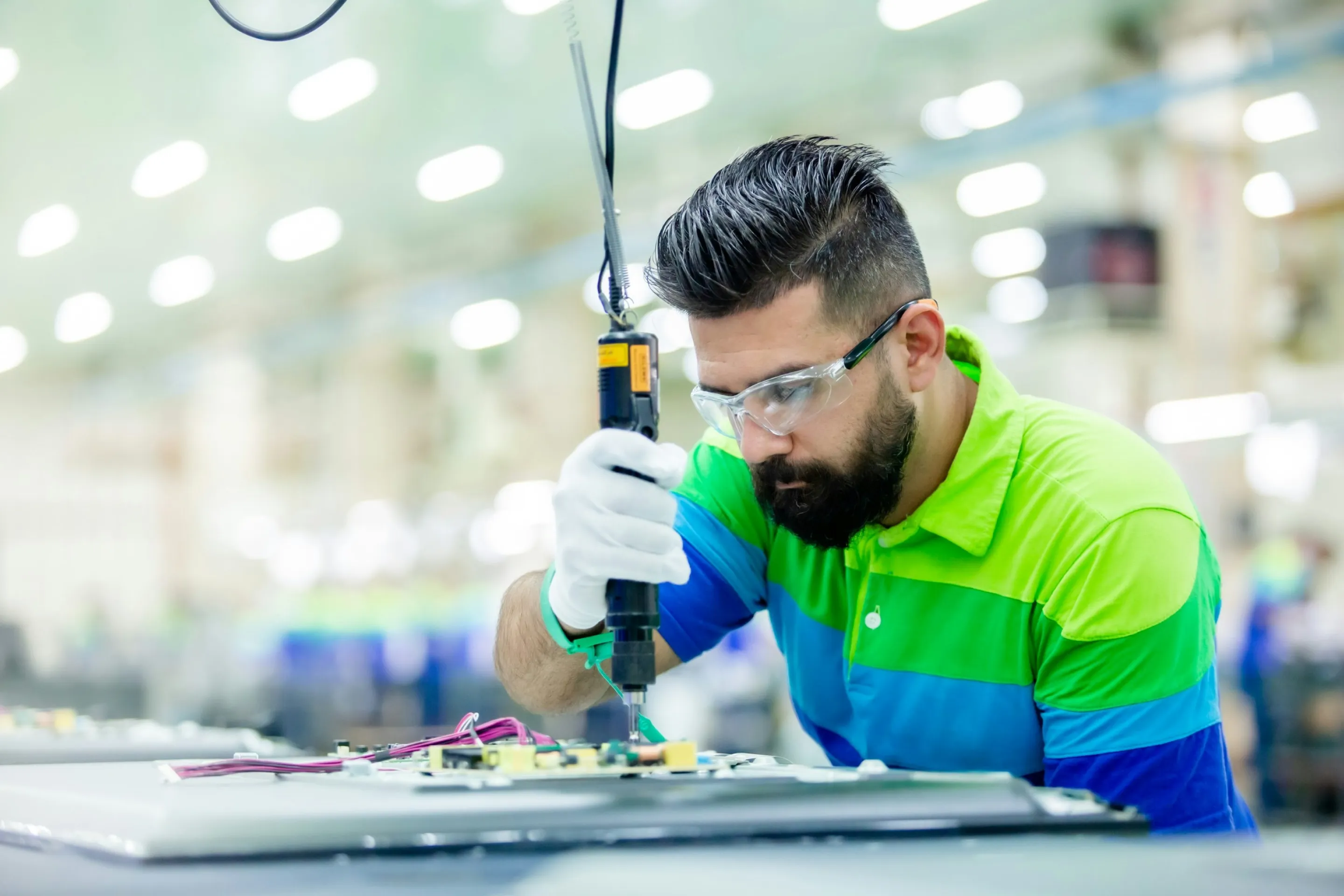
This blog post delves into the heart of Performance Manufacturing, dissecting its core principles, offering insights into the tools that drive transformation, and sharing real-world case studies of companies that have reaped the rewards of this approach. We'll also peer into the future, exploring the impact of Industry 4.0 and the sustainability agenda on Performance Manufacturing.
So, let us embark on this illuminating voyage, where data-driven precision and relentless improvement converge to unlock the true potential of manufacturing – where efficiency meets quality in perfect harmony. Welcome to the world of Performance Manufacturing.
Understanding Performance Manufacturing
Performance Manufacturing is more than just a buzzword; it's a transformative approach to production that places efficiency and quality at the forefront of operations. It's a paradigm shift from the traditional manufacturing methods that were once the norm. Instead of merely churning out products, Performance Manufacturing meticulously fine-tunes every aspect of the production process to maximise efficiency and ensure top-tier quality.
The figures speak volumes: A comprehensive survey conducted by McKinsey & Company found that companies that adopted Performance Manufacturing techniques achieved an average of 50% reduction in lead times and a 20% increase in productivity. These remarkable gains are not the result of chance but a deliberate shift towards more efficient and quality-driven manufacturing.
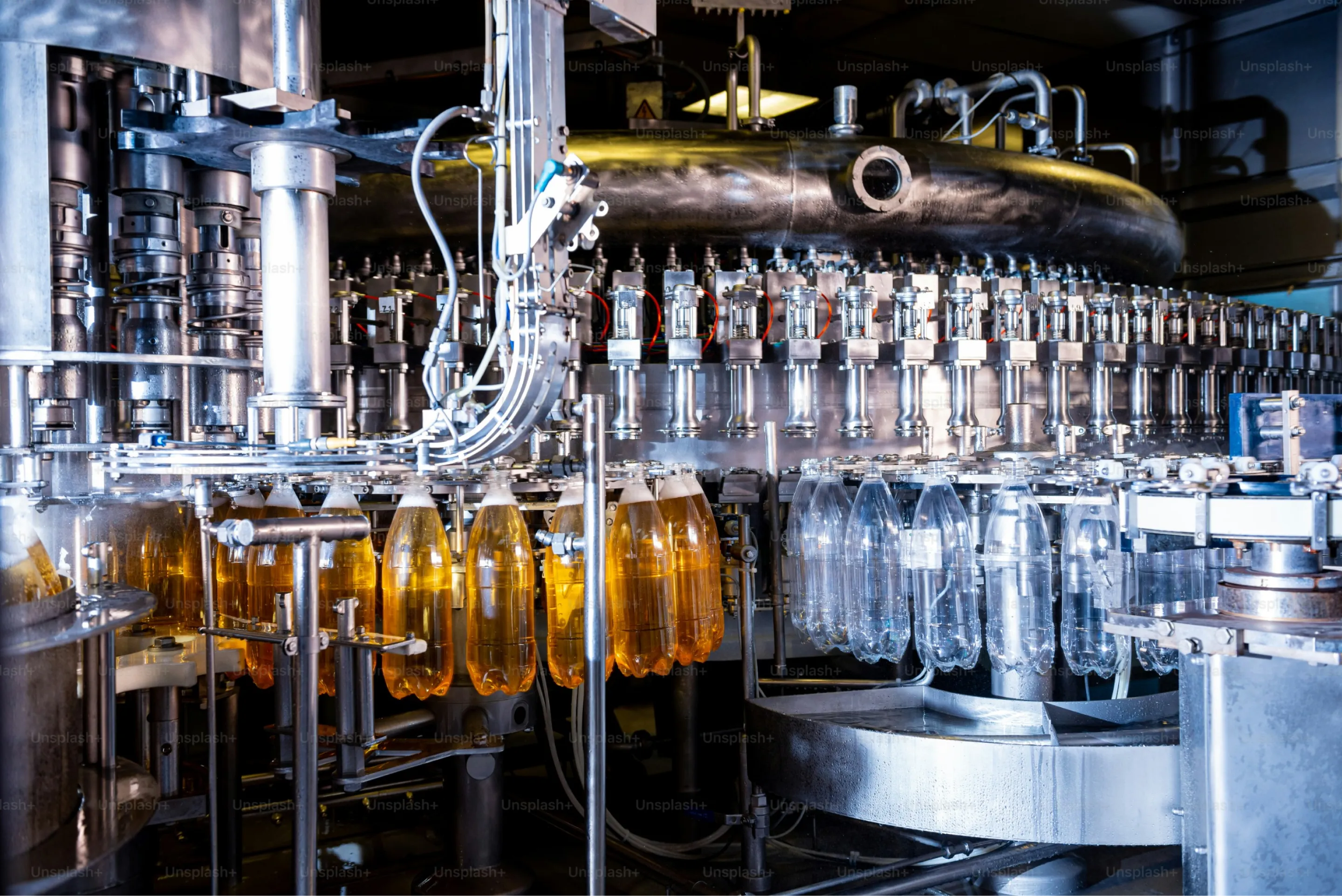
Lean Manufacturing, one of the pillars of Performance Manufacturing, exemplifies this shift. Born in the automotive industry but since embraced by sectors ranging from aerospace to healthcare, Lean Manufacturing focuses on the elimination of waste. In this context, waste encompasses anything that does not add value to the final product, be it overproduction, excess inventory, or unnecessary waiting times.
Toyota, a pioneer in Lean Manufacturing, provides a compelling case study. Through their relentless pursuit of waste reduction, Toyota reduced production lead times by a staggering 96% and achieved a 90% reduction in defects, saving billions in the process.
The Evolution of Manufacturing Techniques
To truly grasp the significance of Performance Manufacturing, we must examine the historical evolution of manufacturing techniques. Gone are the days of mass production, where economies of scale were the driving force. Today, the landscape is marked by customisation, rapid production, and demand-driven processes.
Several milestones have punctuated the journey towards Performance Manufacturing. The advent of Six Sigma, a methodology rooted in data-driven problem-solving, ushered in an era of precision and quality control. Companies like General Electric, which implemented Six Sigma across its operations, reported savings of $12 billion within five years.
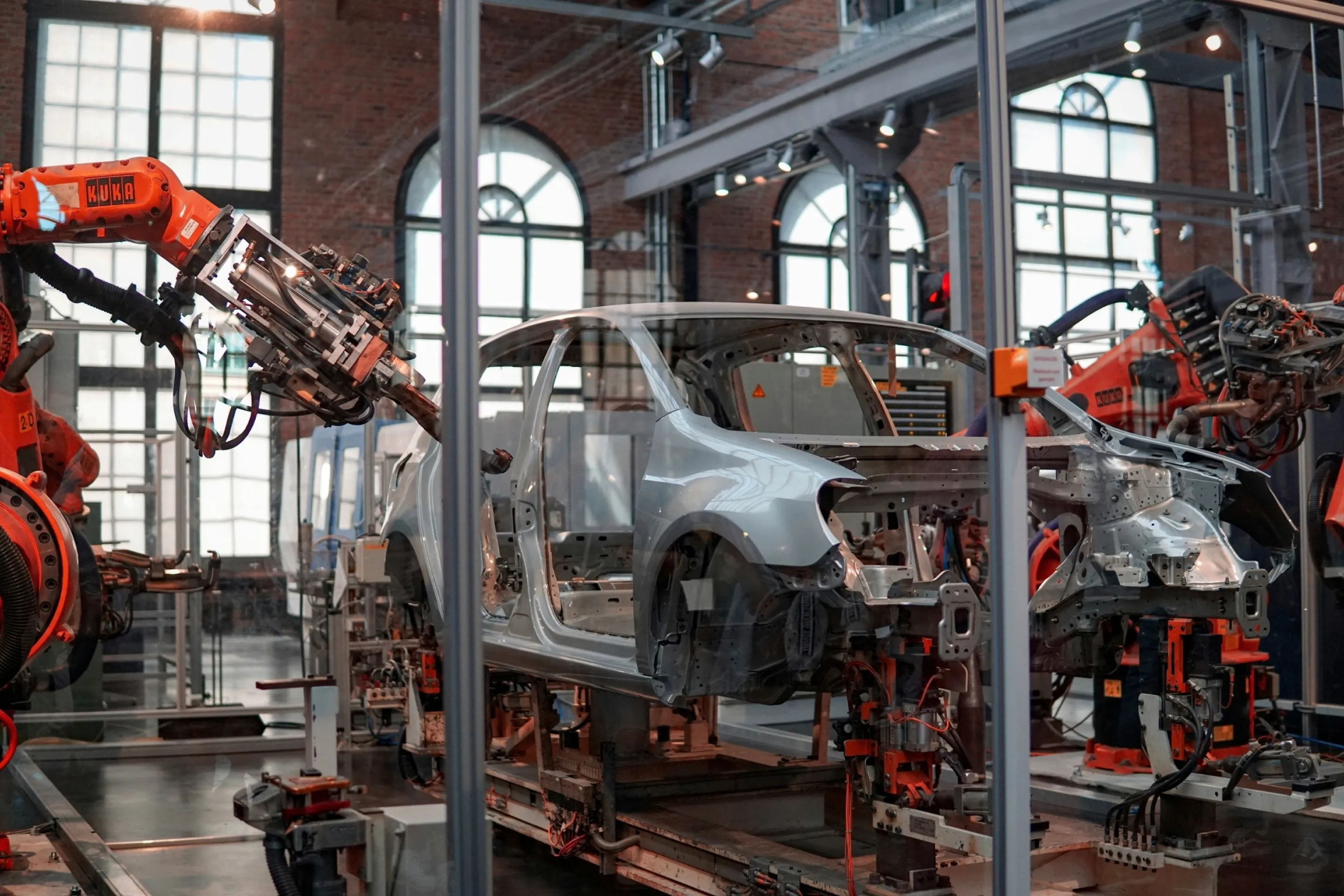
Just-in-Time (JIT) Manufacturing is yet another cornerstone of Performance Manufacturing. By synchronising production with customer demand, companies reduce excess inventory, freeing up capital and mitigating the risks associated with stockpiling goods. Dell's successful implementation of JIT is a testament to its transformative power, enabling the company to revolutionise the computer industry by offering custom-built computers with minimal lead times.
In essence, Performance Manufacturing responds to the demands of the modern market, where consumers expect customised, high-quality products to be delivered swiftly. It's a journey of efficiency, precision, and continuous improvement, and this blog post will guide you through its intricacies and potential.
The Core Principles of Performance Manufacturing
Lean Manufacturing, a pivotal component of Performance Manufacturing, revolves around eliminating waste and streamlining operations. Toyota birthed this methodology in the mid-20th century, and has since become a global standard, transcending industries.
Statistics offer a compelling argument for the adoption of Lean practices. Research conducted by the Lean Enterprise Research Centre reveals that the typical manufacturing process consists of a staggering 60% non-value-added activities, i.e., waste. These wasteful activities result in overproduction, excessive inventory, and unnecessary waiting times.
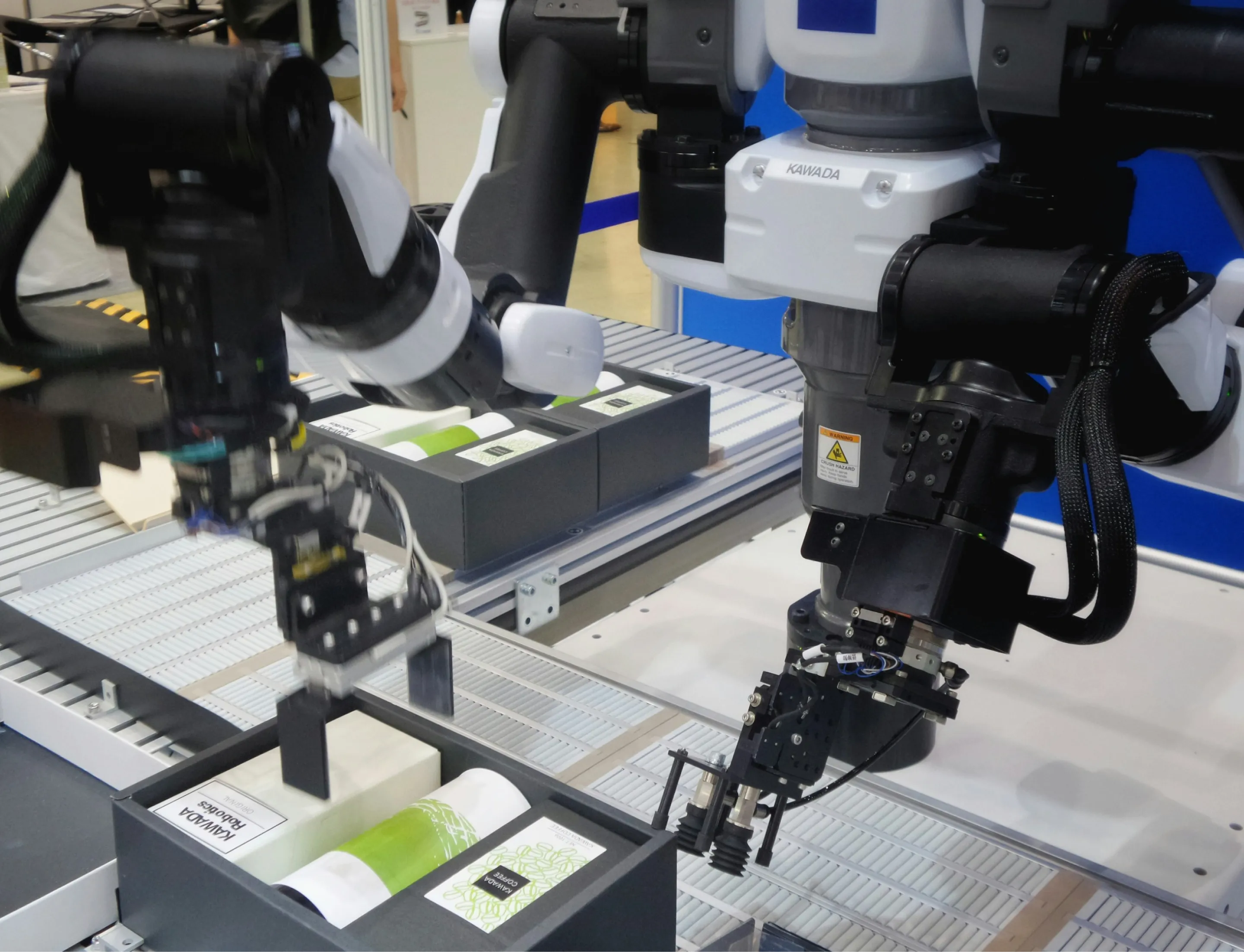
Consider the case of a leading car manufacturer. Implementing Lean principles and reducing the time it takes to produce a vehicle from 46 hours to 29 hours significantly reduced costs and improved product quality, leading to a 20% increase in customer satisfaction.
Six Sigma and Quality Control
In Performance Manufacturing, quality control is paramount. Six Sigma, a methodology rooted in data-driven problem-solving, acts as the vanguard of quality assurance. Its DMAIC (Define, Measure, Analyze, Improve, Control) process provides a structured approach to identifying and eliminating defects.
The financial implications of quality control are profound. According to the American Society for Quality (ASQ), the cost of poor quality in manufacturing can devour as much as 20% of a company's revenue. Through its meticulous attention to detail and statistical rigour, Six Sigma has enabled companies to curb this costly issue through careful attention to detail and statistical rigour.
General Electric's embrace of Six Sigma is a testament to its effectiveness. GE reported $12 billion in savings within five years of implementing the methodology. Their experience underscores the potential financial gains achievable through pursuing quality excellence.
Just-in-Time (JIT) Manufacturing
Just-in-Time (JIT) Manufacturing, another core principle of Performance Manufacturing, embodies producing goods exactly when needed and in the required quantities. By doing so, JIT eliminates excess inventory and associated carrying costs while enhancing production efficiency.
In practice, JIT has proven to be a game-changer. Dell, the renowned computer manufacturer, has harnessed JIT to significant effect. Dell revolutionised the industry by offering custom-built computers with minimal lead times, dramatically reducing its inventory carrying costs.
This section delves into the core principles underpinning Performance Manufacturing – Lean Manufacturing, Six Sigma, and JIT. These methodologies are not merely theoretical constructs but concrete pathways to achieving efficiency and quality that have yielded tangible results for businesses worldwide. The journey into Performance Manufacturing continues as we explore the tools and techniques that power this transformation in the subsequent section.
Tools and Techniques for Performance Manufacturing
Value Stream Mapping
Value Stream Mapping (VSM) is a critical tool in the Performance Manufacturing arsenal, offering manufacturers a visual representation of their production processes. By mapping the flow of materials and information, businesses can pinpoint bottlenecks, redundancies, and inefficiencies.
Statistics from the Lean Enterprise Research Centre corroborate VSM's impact, revealing that companies can reduce lead times by up to 90% through its practical use. A real-world illustration comes from the healthcare industry. A hospital applied VSM to its patient admission process, resulting in a staggering 90% reduction in the time required for admission, improving patient satisfaction and reducing costs.
Total Quality Management (TQM)
Total Quality Management (TQM) is a holistic approach to continuous improvement that fosters an organisation's culture of quality excellence. Its principles extend beyond the factory floor and encompass every facet of an enterprise, from product design to customer service.
Studies by the American Society for Quality (ASQ) highlight TQM's benefits. Firms that have successfully adopted TQM have reported significant improvements in customer satisfaction, with some recording a 50% reduction in customer complaints.
For instance, Tata Motors, an Indian automaker, embraced TQM and witnessed a remarkable reduction in vehicle defects by 60%, leading to higher customer trust and loyalty.
Process Optimization
Process Optimization is the art of fine-tuning manufacturing processes to achieve maximum efficiency and productivity. It encompasses a range of techniques, from reengineering workflows to embracing automation and data-driven decision-making.
One compelling example of process optimisation comes from the aerospace industry. Boeing, a global leader in aircraft manufacturing, employed process optimisation strategies to reduce the assembly time of its 777 model from 50 to 20 days, resulting in substantial cost savings and increased output.
The statistical gains achieved through these tools and techniques underscore the transformative potential of Performance Manufacturing. They empower manufacturers to not only identify inefficiencies but also to take concrete steps towards rectifying them. The journey towards operational excellence continues as we delve deeper into measuring and monitoring performance.
Measuring and Monitoring Performance
In Performance Manufacturing, the adage "You can't improve what you don't measure" couldn't be more relevant. Accurate measurement and monitoring are the cornerstones of achieving efficiency and quality targets.
Key Performance Indicators (KPIs)
Key Performance Indicators (KPIs) are the compass that guides organisations towards their desired objectives. These quantifiable metrics offer invaluable insights into the health of manufacturing processes. Research by the Aberdeen Group indicates that companies using KPIs effectively experience a 20% increase in operational efficiency and a 20% reduction in production costs.
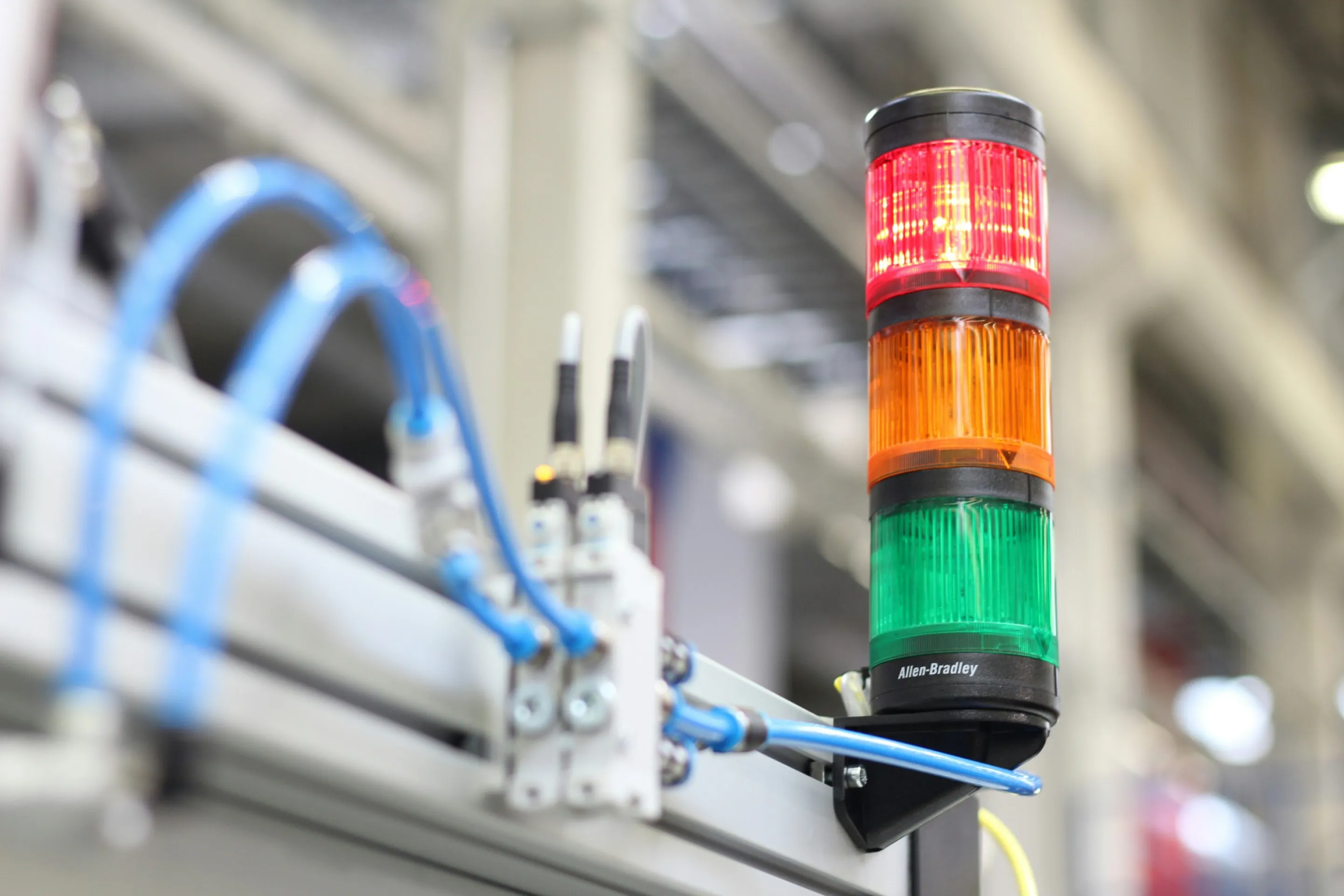
Consider the case of a pharmaceutical manufacturer. By monitoring KPIs such as on-time delivery and product defect rates, the company identified areas of improvement, leading to a 15% reduction in lead times and a 10% decrease in defects, ultimately enhancing customer satisfaction.
OEE (Overall Equipment Effectiveness)
OEE (Overall Equipment Effectiveness) is a vital metric for manufacturers, reflecting the efficiency of production equipment. It's calculated by multiplying availability, performance, and quality rates. A study by the National Institute of Standards and Technology (NIST) revealed that companies that optimised OEE experienced a 10% increase in production capacity and a 15% reduction in downtime.
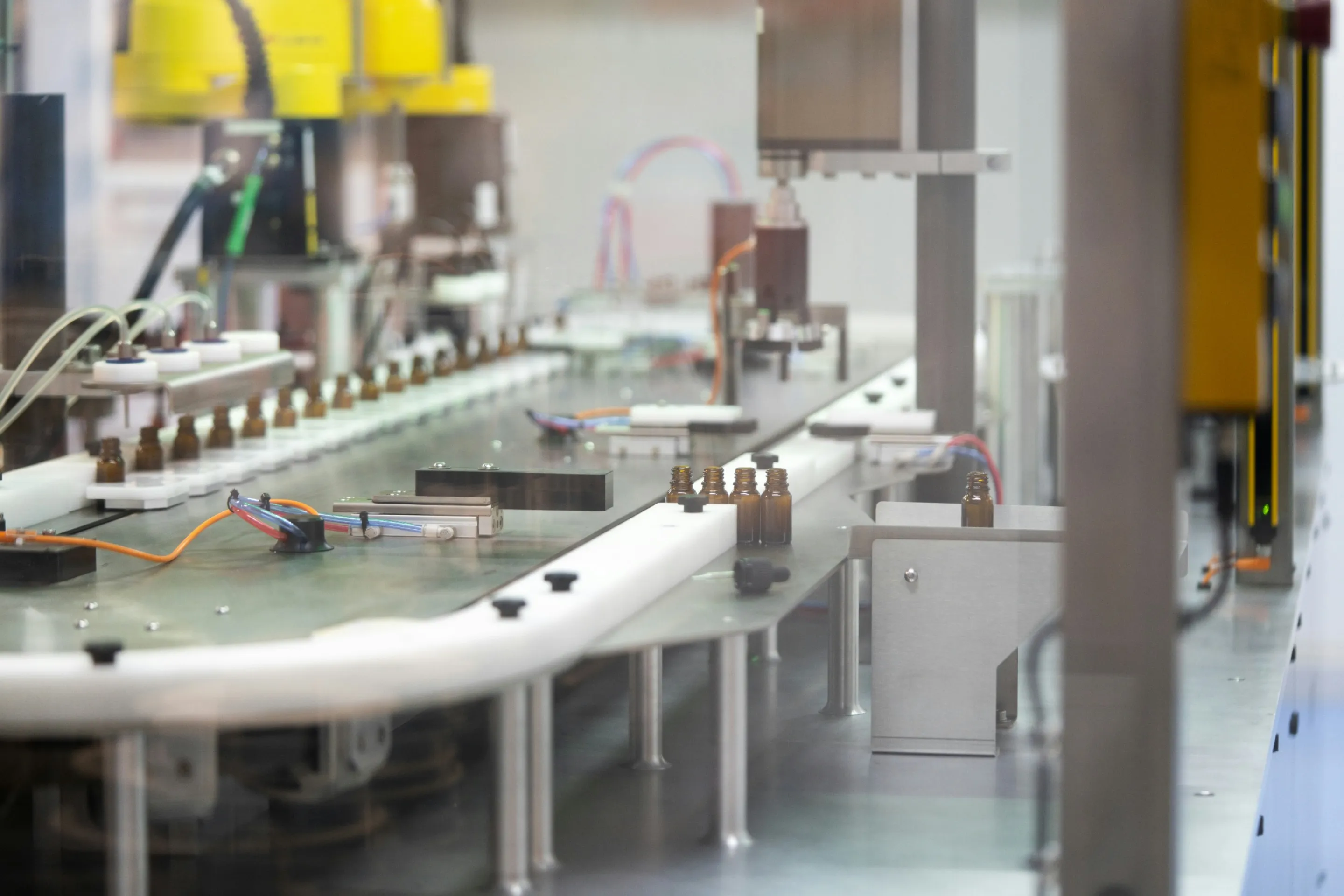
An aerospace manufacturer is a prime example. By measuring OEE and addressing underperforming machinery, they achieved a 12% boost in equipment efficiency and a 25% reduction in unplanned downtime, translating into substantial cost savings.
These metrics empower manufacturers to identify areas of improvement, allocate resources judiciously, and make data-driven decisions. They serve as the compass, guiding the ship of Performance Manufacturing towards the shores of efficiency and quality.
But measurement alone is not enough; it must be coupled with proactive actions, and this blog post will continue to explore strategies and best practices for implementing Performance Manufacturing.
Implementing Performance Manufacturing
Steps to Implement Performance Manufacturing
The journey to master Performance Manufacturing involves a series of deliberate steps akin to a well-choreographed dance. This section unveils a roadmap to implement Performance Manufacturing effectively.
Assessment and Benchmarking |
Begin by evaluating your current operations. Benchmark against industry leaders to identify gaps and set performance targets. Research by the Boston Consulting Group found that companies that benchmark their operations against industry leaders achieve a 9% reduction in operating costs within two years. |
Cultural Transformation |
Performance Manufacturing isn't just about processes; it's about people. Foster a culture of continuous improvement, where every employee plays a role in identifying and eliminating waste. Studies by Deloitte highlight that companies with a strong culture of constant improvement experience a 12% increase in productivity. |
Education and Training |
Equip your workforce with the necessary skills and knowledge to drive Performance Manufacturing. Training programs like Six Sigma and Lean can yield remarkable results. A case in point is General Electric, which attributes $10 billion in annual savings to its Six Sigma program. |
Process Optimization |
Implement Lean, Six Sigma, and other performance-driven methodologies to optimise processes systematically. This includes value stream mapping, waste reduction, and error-proofing techniques. A case study from Johnson & Johnson reported a 30% reduction in lead times and a 20% increase in productivity through process optimisation. |
Technology Integration |
Leverage technology and automation to enhance production efficiency. Research by the World Economic Forum reveals that Industry 4.0 technologies, such as IoT and AI, can lead to a 20% increase overall equipment effectiveness. |
Real-World Case Studies
Real-world success stories inspire and provide practical guidance for companies on the Performance Manufacturing journey.
Toyota |
They were often hailed as the poster child of Lean Manufacturing. Toyota's commitment to waste reduction and continuous improvement has led to remarkable gains. They achieved a 90% reduction in defects and a 50% reduction in lead times. |
Amazon |
The e-commerce giant is renowned for its efficient supply chain management, utilising JIT principles. Amazon's adoption of JIT has enabled it to reduce inventory carrying costs by billions while enhancing customer satisfaction through faster deliveries. |
Implementing Performance Manufacturing is not an option; it's imperative for companies aiming to remain competitive in today's global marketplace. By following the outlined steps and drawing inspiration from real-world successes, organisations can embark on a transformative journey towards manufacturing excellence.
Future Trends in Performance Manufacturing
The landscape of Performance Manufacturing is continually evolving, driven by technological advancements and changing market dynamics. To remain at the forefront of manufacturing excellence, businesses must anticipate and embrace these emerging trends.
Industry 4.0 and Smart Manufacturing
Industry 4.0, often dubbed the Fourth Industrial Revolution, represents the fusion of physical manufacturing with digital technology. This paradigm shift towards smart manufacturing has the potential to redefine how businesses operate.
Research by PwC suggests that companies adopting Industry 4.0 technologies can reduce operational costs by 3.6% annually and increase revenue by 2.9% annually. These technologies, including the Internet of Things (IoT), artificial intelligence (AI), and data analytics, enable real-time monitoring, predictive maintenance, and agile production.

Sustainable Manufacturing
Sustainability is no longer a choice but a necessity. Consumers and regulatory bodies are demanding eco-friendly products and environmentally responsible manufacturing processes.
A report by the World Economic Forum highlights that sustainable manufacturing practices can reduce energy costs by 10-30%, water consumption by 20-50%, and greenhouse gas emissions by 25-50%. Companies like Unilever have embraced sustainability, reducing waste across their supply chain and achieving a 53% reduction in environmental footprint.
Advanced Robotics and Automation
Integrating advanced robotics and automation reshape the factory floor. Robots increasingly work alongside humans, performing repetitive tasks with precision and speed.
A study by the International Federation of Robotics found that robot density in manufacturing industries is directly correlated with labour productivity. Countries with higher robot density, such as South Korea and Germany, boast significantly higher productivity levels.
In conclusion, the future of Performance Manufacturing is characterised by a fusion of technology, sustainability, and automation. Industry 4.0, sustainable practices and robotics represent the path forward. Embracing these trends will enhance efficiency and quality and ensure long-term competitiveness in the global manufacturing arena. As we conclude this exploration of Performance Manufacturing, we stand on the cusp of an exciting era of innovation and transformation.
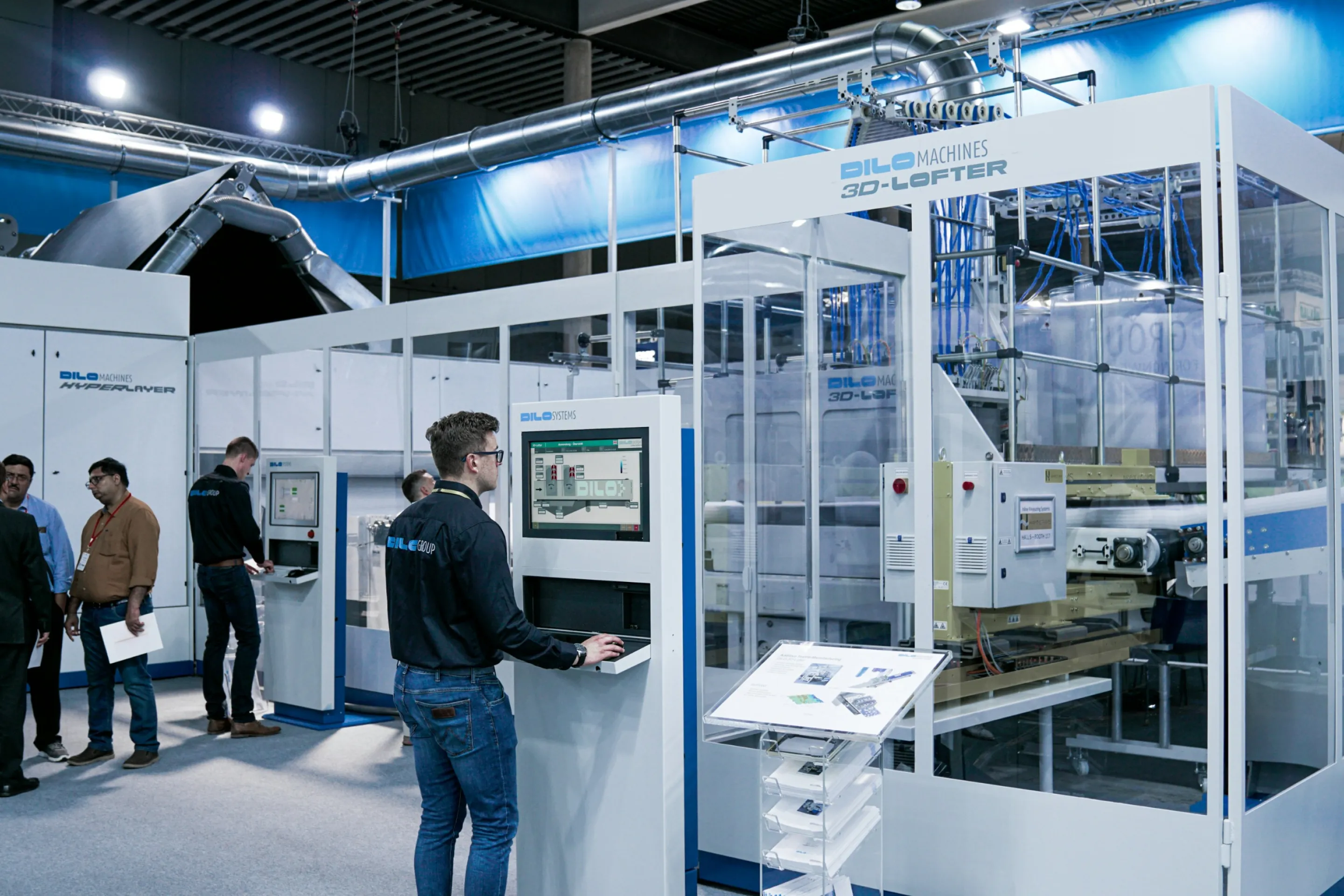
Revolutionizing Performance Manufacturing with Iwoscan
The right tools can make all the difference in the quest for Performance Manufacturing excellence. Enter Iwoscan, an innovative solution to redefine the manufacturing operations landscape. In this section, we'll explore the applicability of Iwoscan to Performance Manufacturing and delve into how it elevates manufacturing processes to unprecedented levels of efficiency and quality.
Iwoscan's Relevance to Performance Manufacturing
Iwoscan, short for Intelligent Workflow Optimization and Scheduling, is a cutting-edge technology that leverages the power of artificial intelligence and machine learning. Its primary goal? To optimise manufacturing workflows and schedules with unparalleled precision. How does this align with Performance Manufacturing? Let's delve into its applicability.
Iwoscan's Impact on Performance Manufacturing
Lean Manufacturing Augmented |
Iwoscan enhances Lean Manufacturing by providing real-time insights into production processes. By analysing data from machines and sensors, Iwoscan identifies potential bottlenecks and inefficiencies. This proactive approach allows manufacturers to address issues before they impact production, reducing waste significantly. |
Six Sigma Precision |
Iwoscan's data analytics capabilities resemble Six Sigma's data-driven methodology. It identifies the root causes of defects and deviations, enabling swift corrective actions. The result? Enhanced product quality and reduced defects, aligning with Six Sigma's core principles. |
JIT Efficiency |
Just-in-Time (JIT) manufacturing relies on precise scheduling. Iwoscan optimises production schedules, ensuring that materials and resources are delivered precisely when needed. This minimises inventory costs while maintaining operational efficiency, an essential aspect of JIT. |
Iwoscan stands out as the ultimate solution for Performance Manufacturing for several reasons.
Data-Driven Decision-Making |
Data is paramount in the era of Industry 4.0. Iwoscan's data analytics capabilities enable manufacturers to make informed decisions, improving processes and resource allocation. |
Real-Time Agility |
Iwoscan operates in real-time, allowing manufacturers to adapt swiftly to changing conditions. This agility ensures that production remains efficient, even in dynamic environments. |
Cost Savings |
The integration of Iwoscan typically results in substantial cost savings. For example, a study by McKinsey & Company found that AI-driven production optimisation can lead to a 15% reduction in production costs. |
In conclusion, Iwoscan is more than a tool; it's a game-changer in the realm of Performance Manufacturing. By enhancing Lean Manufacturing, embracing Six Sigma precision, and facilitating JIT efficiency, Iwoscan optimises manufacturing processes in a way that no other solution can. Its data-driven decision-making, real-time agility, and cost-saving potential position it as the ultimate solution for those who seek manufacturing excellence in the 21st century. As Performance Manufacturing continues to evolve, Iwoscan is the compass guiding manufacturers towards new heights of efficiency and quality.
Elevating Performance Manufacturing with Iwoscan
In the ever-evolving world of Performance Manufacturing, the pursuit of excellence never ceases. This journey has been marked by the relentless quest for efficiency and quality, guided by Lean Manufacturing, Six Sigma, and JIT methodologies. However, in this era of technological advancement and data-driven decision-making, a new champion has emerged - Iwoscan.
As we've explored in this blog post, Iwoscan, or Intelligent Workflow Optimization and Scheduling, is not just another tool in the manufacturing arsenal; it's a transformative force that optimises workflows and schedules with once unimaginable precision.
Statistics and real-world examples have showcased how Iwoscan aligns with the core principles of Performance Manufacturing. It enhances Lean Manufacturing by identifying inefficiencies in real-time, augments Six Sigma's data-driven precision, and ensures JIT efficiency by optimising production schedules.
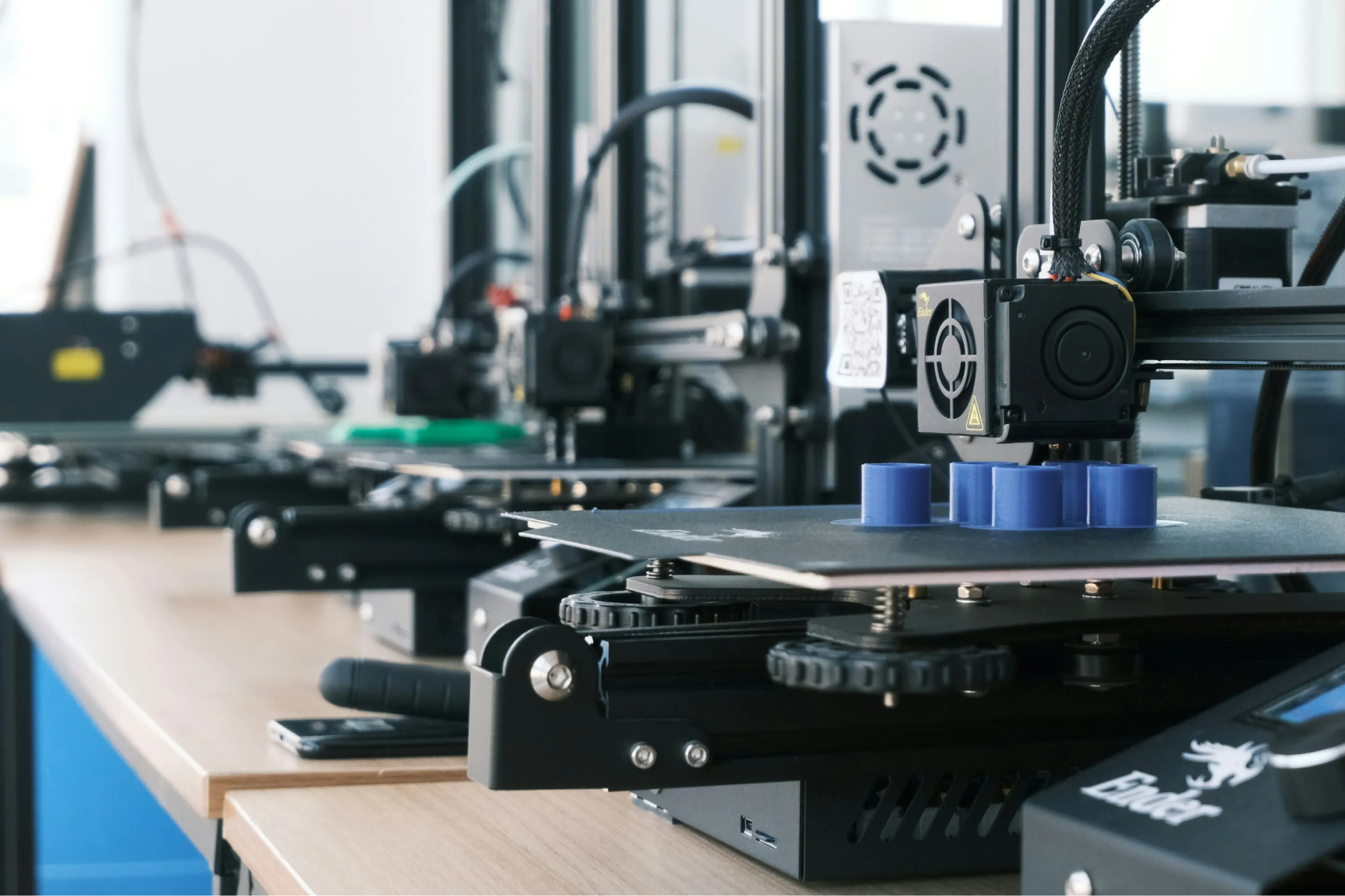
As we conclude this exploration of Performance Manufacturing, Iwoscan emerges as the compass guiding manufacturers towards new heights of efficiency and quality. It stands as a testament to the evolution of manufacturing in the 21st century, where technology, data, and intelligent decision-making converge to redefine what's possible. As the manufacturing landscape transforms, Iwoscan is the beacon lighting the path to operational excellence and enduring success.
Comments
No comments yet!Add a Comment
You must be logged in to post a comment.