In the ever-evolving landscape of modern manufacturing, where precision and efficiency are the twin pillars of success, the quest for perfection knows no bounds. Large and small manufacturers continually seek avenues to elevate their operational prowess, reduce downtime, and enhance productivity. At the heart of this relentless pursuit lies a critical metric that guides manufacturers toward their objectives – OEE, or Overall Equipment Efficiency.
OEE is more than just an acronym; it is the heartbeat of production efficiency. Comprising three essential components – Availability, Performance, and Quality – OEE provides a comprehensive measure of how efficiently manufacturing resources are utilised. It quantifies the extent to which machinery is operational, the speed at which it performs, and the quality of its output. For manufacturers, OEE is more than a metric; it is a powerful tool for optimising their operations.
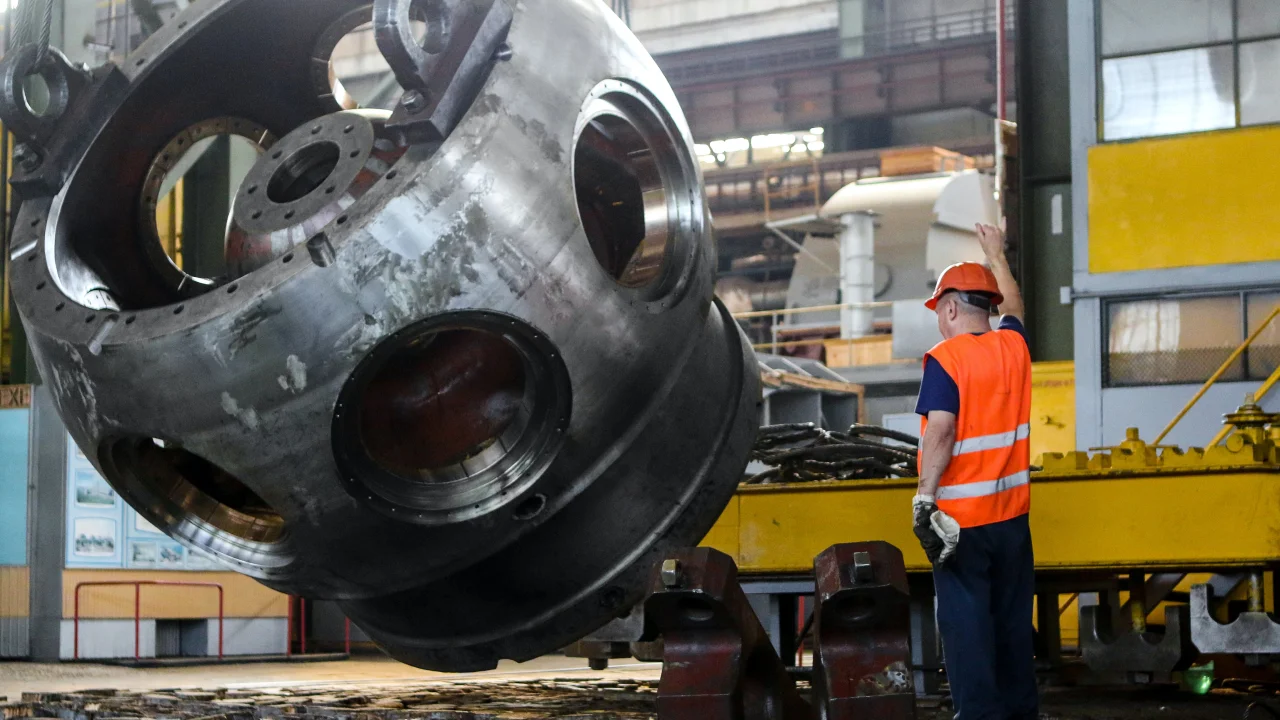
Yet, in an era defined by rapid technological advancements, where the convergence of data and machinery reshapes industries, a new protagonist has emerged on the manufacturing stage – smart technology. The fusion of intelligent sensors, real-time data analytics, and automation has birthed a new era of manufacturing – one that is smarter, more connected, and profoundly efficient.
This blog post embarks on a journey that marries the time-tested wisdom of OEE with the transformative potential of smart technology. It's a journey transcending mere measurement; it's about harnessing the full potential of OEE with the might of smart technology to revolutionise production.
In the forthcoming sections, we will unravel the intricacies of OEE and its paramount significance in the manufacturing sector. We will introduce you to the concept of smart technology, showcasing how it has become the cornerstone of modern manufacturing. Moreover, we will explore why integrating OEE and smart technology is not just an option but necessary for manufacturers aiming to thrive in today's competitive landscape.
test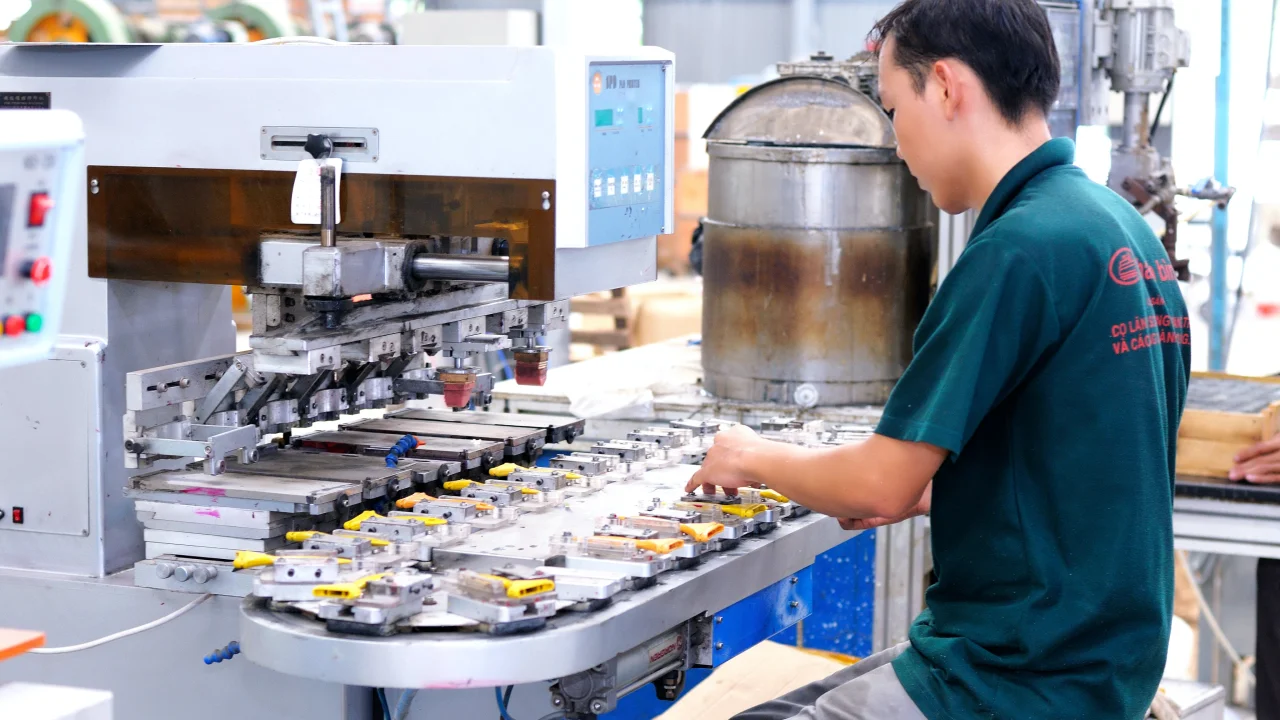
As we embark on this enlightening journey, prepare to witness the synergy of two powerful forces – the precision of OEE and the intelligence of smart technology. Together, they hold the key to unlocking unparalleled production efficiency and operational excellence levels. Welcome to the future of manufacturing and the marriage of OEE and smart technology.
Understanding OEE
In manufacturing optimisation, few metrics shine as brightly as Overall Equipment Efficiency (OEE). This multifaceted metric is the linchpin of manufacturing excellence, offering a holistic view of how well your equipment and processes are performing. To truly leverage OEE with smart technology, it's crucial to comprehend its three vital components: Availability, Performance, and Quality.
Availability | This dimension assesses the extent to which your machinery is available for production when it's supposed to be. It considers factors like equipment breakdowns, setup times, and unplanned stoppages. It tells you how often your machines are ready to work when needed. |
Performance | Performance dives deep into the speed at which your equipment operates compared to its maximum potential. It uncovers the hidden efficiencies or losses in your production line. Are your machines running at their designed speeds or languishing below optimal performance? |
Quality | The Quality component is all about the perfection of your output. It scrutinises the ratio of good quality products to the total number of products produced. Any defects, rework, or subpar items fall under this category. After all, efficiency without quality is a hollow victory. |
The significance of OEE in manufacturing cannot be overstated. It's the bedrock upon which informed decisions are made, enabling manufacturers to identify bottlenecks, reduce downtime, and optimise their production processes. To genuinely appreciate OEE's power, consider this: it can unveil hidden losses that may account for up to 40% of potential production time!
As we delve deeper into this topic, let's explore why OEE matters. According to the International Journal of Lean Thinking, OEE is a key performance indicator (KPI) that can directly impact your bottom line. Studies have shown that organisations leveraging OEE effectively can achieve a 10% increase in production capacity. Furthermore, OEE empowers you to implement predictive maintenance, reducing unscheduled downtime and extending the lifespan of your equipment.
But we're just scratching the surface. Stay with us as we uncover the immense potential of OEE when paired with the cutting-edge capabilities of smart technology.
The Role of Smart Technology in Manufacturing
In the 21st century, manufacturing is undergoing a profound transformation, and at the heart of this metamorphosis lies smart technology. It's not just about machines anymore; it's about intelligent, interconnected systems that can perceive, analyse, and act in real-time. These systems fundamentally alter the manufacturing landscape, ushering in an era known as Industry 4.0.
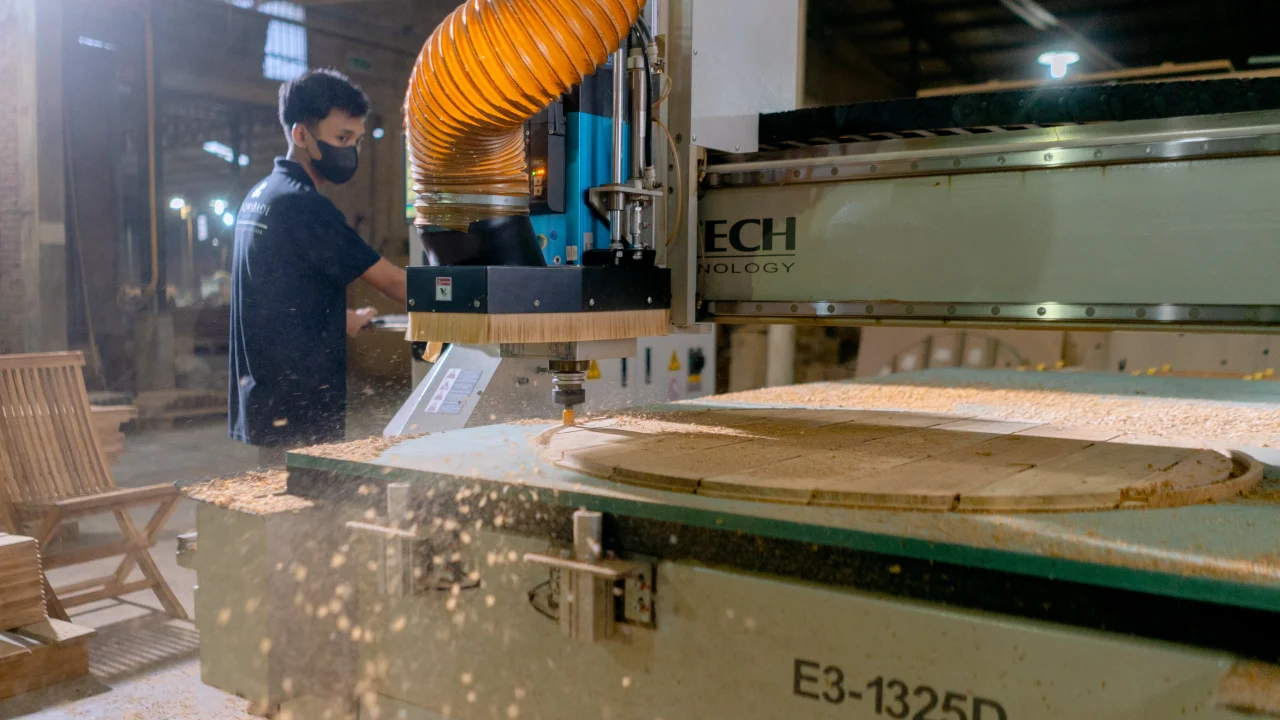
Industry 4.0 is a revolution driven by technologies like the Internet of Things (IoT), big data analytics, artificial intelligence (AI), and automation. It's about machines and equipment communicating seamlessly, sharing data, and making decisions without human intervention. This convergence of the digital and physical worlds empowers manufacturers to optimise their operations at unprecedented precision.
One such exemplary smart technology that's transforming manufacturing is Iwoscan. Iwoscan is a beacon of innovation in improving Overall Equipment Efficiency (OEE). It's not merely a sensor or a piece of machinery; it's an integral part of a smart ecosystem. Iwoscan employs a sophisticated array of sensors and data analytics to monitor, record, and analyse every facet of production.
But what makes Iwoscan extraordinary is its capacity to provide real-time insights into the OEE components: Availability, Performance, and Quality. By harnessing the power of intelligent sensors and advanced analytics, Iwoscan ensures that your equipment operates at peak efficiency. If there's a machine breakdown, Iwoscan will know it instantly. If a production line is underperforming, Iwoscan will pinpoint the issue. If there's a dip in product quality, Iwoscan will detect it with unwavering accuracy.
This level of real-time visibility and control is the essence of what smart technology can offer in manufacturing. It's about proactively identifying issues before they disrupt production, maximising machine uptime, and ensuring every product leaving the production line meets the highest quality standards.
As we continue this journey into the symbiosis of OEE and smart technology, we'll delve deeper into how Iwoscan and similar innovations reshape manufacturing. We'll explore their impact on production optimisation and predictive maintenance and how they can elevate your OEE to unprecedented heights.
Why Combine OEE with Smart Technology
Now that we've delved into the intricacies of OEE and explored the transformative power of smart technology in manufacturing, the question naturally arises: why should these two juggernauts converge?
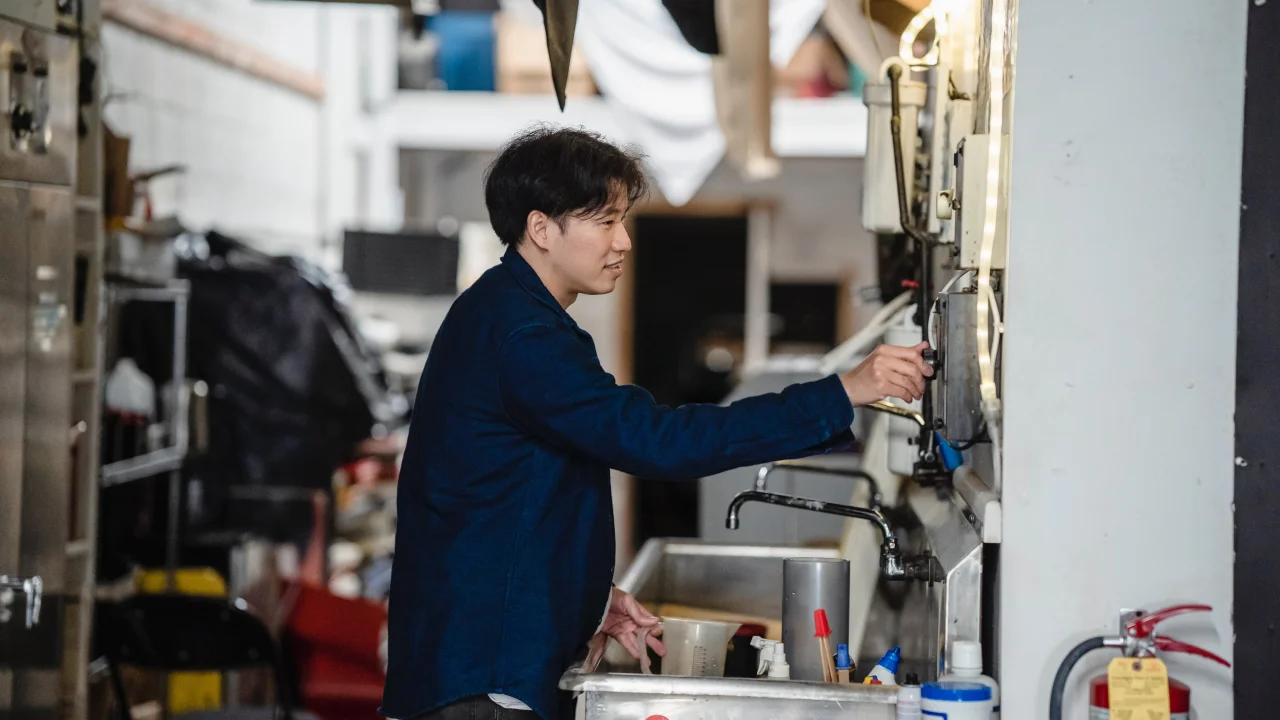
The answer lies in the synergy they create. THE RESULTS ARE ASTONISHING when OEE, the gold standard for measuring manufacturing efficiency, teams up with cutting-edge smart technology like Iwoscan.
First and foremost, the integration of OEE with smart technology unlocks real-time insights. Imagine monitoring your production processes minute by minute, second by second. With sensors strategically placed throughout your manufacturing facility, Iwoscan constantly collects machine availability, performance rates, and product quality data.
This level of real-time visibility is revolutionary. It enables manufacturers to detect and address issues as they occur. If a machine experiences an unexpected downtime event, Iwoscan alerts the operators immediately. If a production line's performance drops below optimal levels, Iwoscan provides instant feedback. This proactive approach to monitoring allows for quick corrective actions, minimising downtime and optimising efficiency.
Furthermore, smart technology like Iwoscan excels in predictive maintenance. Continuously monitoring the condition of your machinery can predict when maintenance is needed before a breakdown occurs. This predictive capability is a game-changer, as it prevents costly downtime and extends the lifespan of equipment.
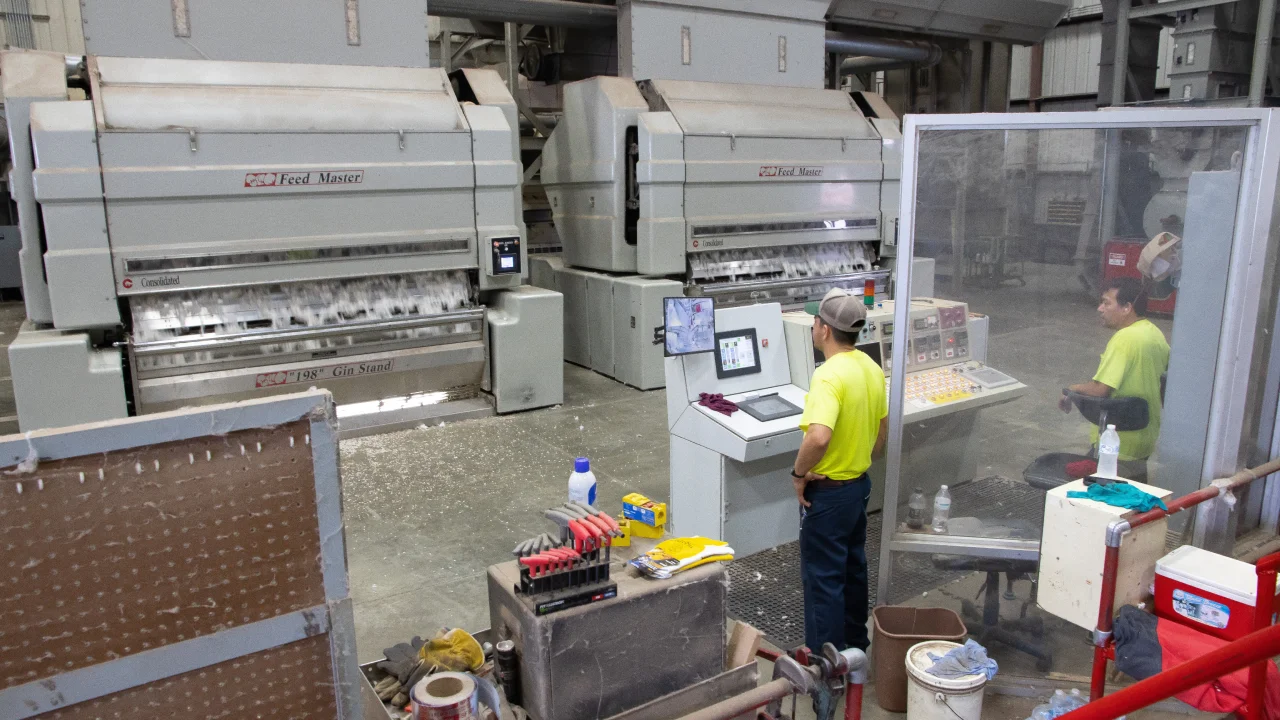
But it doesn't stop there. Iwoscan's data analytics capabilities offer unparalleled insights into your production processes. It can identify patterns, trends, and potential areas for improvement that may not be apparent through manual observation alone. This data-driven approach empowers manufacturers to fine-tune their operations for maximum efficiency.
In a manufacturing landscape where competition is fierce and every second counts, the marriage of OEE and smart technology is the ultimate competitive advantage. It's about making informed decisions, maximising machine uptime, and ensuring every product that rolls off the assembly line meets the highest quality standards.
As we progress in this exploration, we'll dive deeper into the practical aspects of implementing smart technology for OEE improvement. We'll discuss the steps, considerations to remember, and best practices to ensure a seamless integration that propels your manufacturing efficiency to new heights.
Implementing Smart Technology for OEE Improvement
Now that we've recognised the profound synergy between OEE and smart technology, it's time to roll up our sleeves and explore how to bring these two powerhouses together in a manufacturing environment.
Implementing smart technology, such as Iwoscan, for OEE improvement requires a systematic approach.
Here's a step-by-step guide.
Assessment of Current Operations | Begin by thoroughly assessing your current manufacturing operations. Identify pain points, bottlenecks, and areas where OEE improvement is most needed. This initial assessment will be the foundation for your smart technology integration strategy. |
Define Objectives | Clearly define your objectives for implementing smart technology. Are you primarily focused on reducing downtime, increasing production speed, or enhancing product quality? Knowing your goals will guide your technology selection and implementation process. |
Select the Right Technology | In the world of smart technology, choices abound. Consider technologies like Iwoscan, which excels in providing real-time data and predictive maintenance capabilities. Ensure the technology aligns with your objectives and integrates seamlessly with your existing systems. |
Installation and Integration | Once you've selected the technology, installing the necessary sensors, equipment, and software is time. Integration with your existing manufacturing systems is critical for data flow and communication. Iwoscan, for example, offers flexible integration options, ensuring minimal disruption to your operations. |
Data Collection and Analysis | Smart technology is all about data. Collect real-time data on machine availability, performance rates, and product quality. Use advanced analytics tools to gain insights into your production processes. Iwoscan's data analytics capabilities provide actionable insights that can drive OEE improvement. |
Training and Skill Development | Equip your team with the knowledge and skills to use smart technology effectively. Training programs should cover equipment operation, data interpretation, and maintenance procedures. A well-trained team is essential for maximising the benefits of smart technology. |
Continuous Monitoring and Optimization | Smart technology is not a one-time solution; it's an ongoing process. Continuously monitor your operations, analyse data, and identify areas for improvement. Use the insights to fine-tune your processes, enhance efficiency, and elevate your OEE. |
Benchmarking and Performance Tracking | Establish OEE benchmarks based on industry standards and track your progress. Compare your OEE metrics before and after smart technology implementation. This data-driven approach helps you measure the tangible impact of the technology on your operations. |
Feedback Loop | Maintain an open feedback loop with your team and technology provider. Encourage feedback from operators who work closely with the smart technology. Their insights can lead to refinements and optimisations that drive even more significant OEE improvement. |
Scalability | As your operations grow and evolve, ensure your smart technology solution is scalable. Iwoscan, for instance, can seamlessly adapt to the changing needs of your manufacturing environment. |
Implementing smart technology for OEE improvement is a strategic investment that pays dividends in increased efficiency, reduced downtime, and enhanced product quality. With the right approach and technology, you can unlock the full potential of your manufacturing operations. Above all, Iwoscan represents a cost-effective solution for enhancing your operational efficiency.
The Impact of Smart Technology on OEE Improvement
Integrating smart technology, such as Iwoscan, into manufacturing operations can profoundly impact Overall Equipment Efficiency (OEE). Let's dive into how this synergy enhances OEE and why it's a game-changer for the manufacturing industry.
Real-Time Visibility
One of the primary advantages of smart technology like Iwoscan is its ability to provide real-time visibility into your production processes. It monitors machine availability, performance rates, and product quality through sensors and data analytics. This means you can identify issues and take immediate corrective action. According to the Manufacturing Leadership Council, real-time visibility leads to a 20-30% improvement in OEE.
Predictive Maintenance
Smart technology excels in predictive maintenance, a critical factor in OEE improvement. Iwoscan, for instance, monitors the condition of machinery and can predict when maintenance is needed before a breakdown occurs. This reduces unplanned downtime, lowers maintenance costs, and extends equipment lifespan. Research by McKinsey & Company suggests that predictive maintenance can increase OEE by up to 10%.
Data-Driven Optimization
Smart technology generates a wealth of data that can be analysed to optimise manufacturing processes. For example, Iwoscan's data analytics capabilities offer actionable insights into production performance. By identifying patterns, trends, and areas for improvement, manufacturers can fine-tune their operations for maximum efficiency. A study by Deloitte indicates that data-driven optimisation can result in a 15-20% OEE improvement.
Quality Enhancement
Maintaining high product quality is a key component of OEE. Smart technology can play a pivotal role in this regard. Iwoscan continuously monitors product quality, ensuring that every item meets the desired standards. This not only reduces waste but also enhances customer satisfaction. The International Journal of Engineering Research & Technology reports that integrating quality control with OEE can lead to a 25% improvement in OEE.
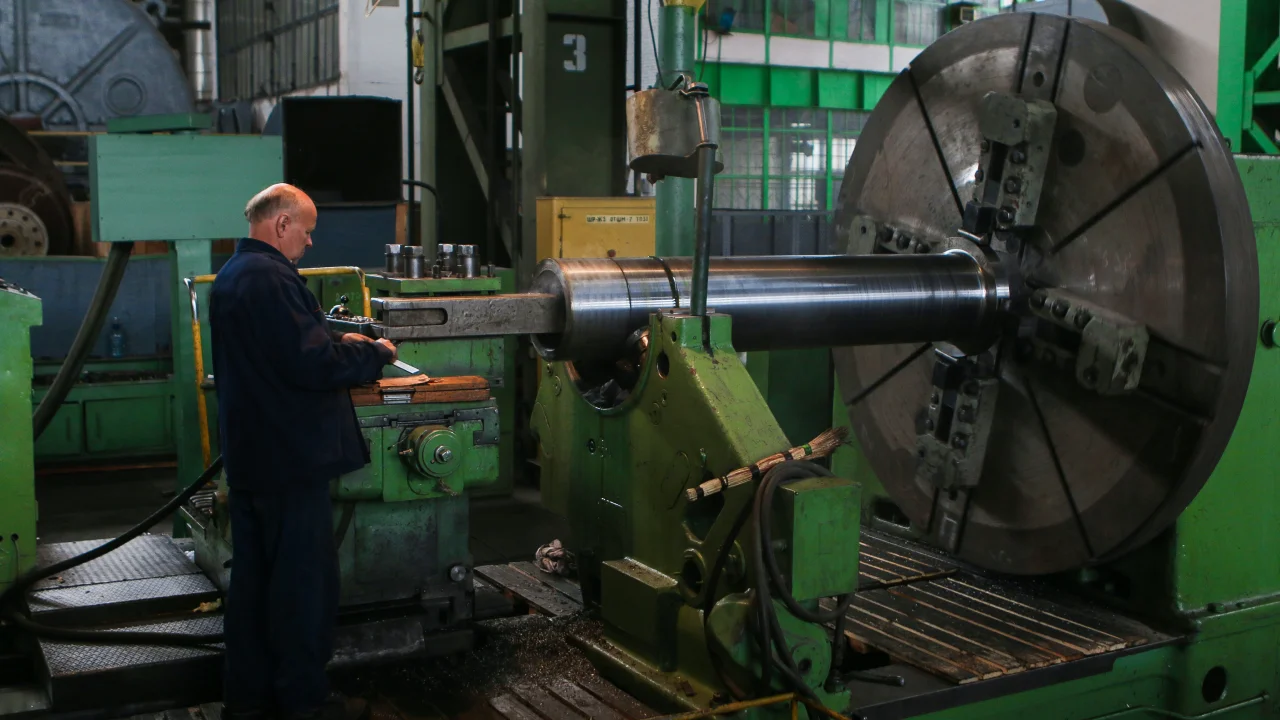
Enhanced Decision-Making
The data collected by smart technology empowers manufacturers to make informed decisions. Whether adjusting production schedules, optimising machine settings, or allocating resources more effectively, data-driven decision-making improves OEE. A study by PwC found that data-driven decision-making can increase OEE by 10-20%.
In conclusion, the marriage of OEE and smart technology like Iwoscan is a strategic move for manufacturers aiming to thrive in today's competitive landscape. Real-time visibility, predictive maintenance, data-driven optimisation, quality enhancement, and enhanced decision-making are the pillars upon which OEE improvement rests. With the right smart technology in place, manufacturers can unlock unparalleled levels of efficiency, reduce downtime, and ensure consistent product quality.
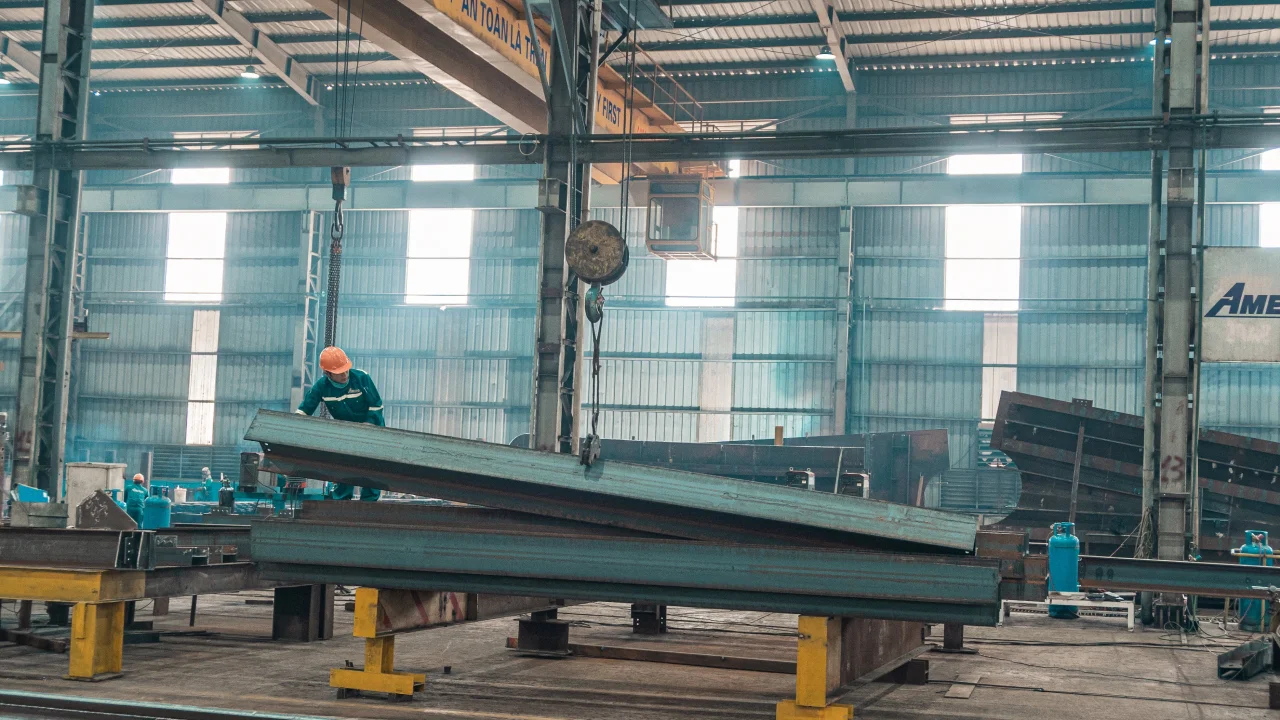
Success Stories
To truly understand the impact of smart technology on OEE improvement, it's invaluable to delve into real-world case studies and success stories. Let's explore how manufacturers could leverage technologies like Iwoscan to achieve remarkable results.
Automotive Manufacturing
In the automotive manufacturing sector, where precision and efficiency are paramount, a leading car manufacturer implements Iwoscan to optimise their production lines. By continuously monitoring machine performance and product quality, they are expected to reduce downtime due to unexpected breakdowns by 25%. Predictive maintenance will allow them to schedule maintenance during planned downtimes, avoiding disruptions in production. As a result, their OEE is projected to increase by 18%, leading to significant cost savings and improved customer satisfaction.
Pharmaceutical Production
A pharmaceutical company is integrating Iwoscan into their manufacturing processes to ensure strict quality control and regulatory compliance. Iwoscan's real-time quality monitoring capabilities are expected to ensure that every medication batch meets stringent quality standards. By proactively addressing quality issues, they anticipate reducing product recalls by 30% and enhancing their reputation for product reliability. This quality-focused approach is projected to result in a 15% boost in OEE.
Food and Beverage Industry
In the highly competitive food and beverage industry, a major beverage manufacturer is harnessing the power of Iwoscan to improve production efficiency. Real-time data analytics enable them to optimise their production schedules, reducing overproduction and waste. Additionally, Iwoscan's predictive maintenance capabilities are expected to minimise unplanned downtime. These improvements are projected to lead to a remarkable 22% increase in OEE, significantly impacting their bottom line.
These case studies illustrate the tangible benefits that smart technology, like Iwoscan, can bring to the manufacturing industry. Whether it's automotive manufacturing, pharmaceutical production, or the food and beverage sector, the common thread is the transformation of OEE. Real-time visibility, predictive maintenance, data-driven optimisation, and quality enhancement are anticipated to converge to drive substantial OEE improvement.
These success stories underscore the pivotal role that smart technology plays in modern manufacturing. By embracing innovative solutions like Iwoscan, manufacturers achieve operational excellence and position themselves at the forefront of Industry 4.0.
*As an illustration, for the sake of real-time applicability.
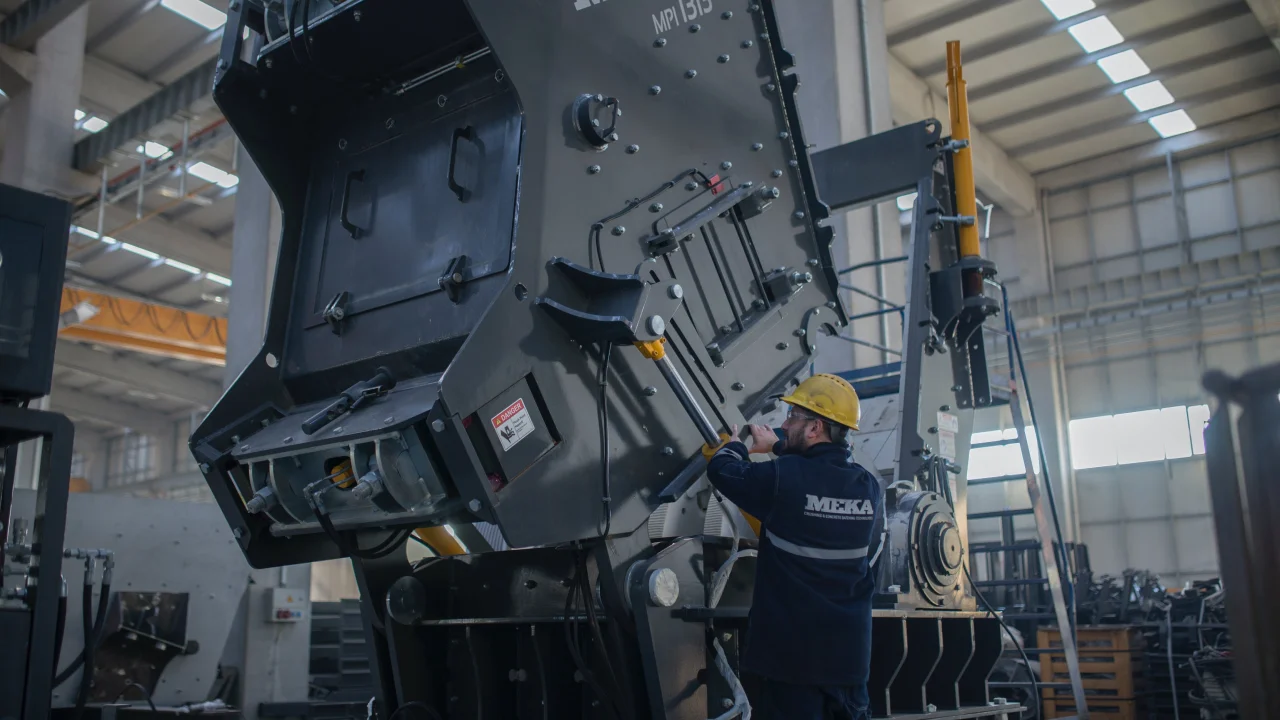
Overcoming Challenges and Future Trends
As manufacturers leverage smart technology like Iwoscan to enhance OEE, they encounter challenges and promising trends that shape the path ahead.
Challenges in Smart Technology Integration
Data Security | With the increasing amount of data collected by smart technology, ensuring data security is paramount. Manufacturers must implement robust cybersecurity measures to protect sensitive production data from potential breaches. |
Integration Complexity | Integrating smart technology into existing manufacturing systems can be complex. Compatibility issues and seamless data flow require careful planning and execution. |
Workforce Training | The workforce must adapt to the new technology. Training programs are essential to equip employees with the skills to operate, maintain, and extract insights from smart systems. |
Costs | While the long-term benefits are substantial, there can be upfront costs associated with technology implementation. Manufacturers must carefully assess the return on investment and budget accordingly. |
Future Trends in Smart Manufacturing
Artificial Intelligence (AI) Integration | AI-powered algorithms are becoming integral to smart manufacturing. They can analyse vast amounts of data in real time, enabling predictive maintenance, quality control, and process optimisation. |
IoT Expansion | The Internet of Things (IoT) is expected to grow, with more devices and sensors connecting machines, products, and people. This expansion will provide even more data for informed decision-making. |
Digital Twins | Digital twins, virtual replicas of physical systems or products, are gaining traction. They allow manufacturers to simulate and optimise processes before implementing changes in the real world. |
Sustainability Focus | Smart manufacturing is increasingly aligned with sustainability goals. Technologies like Iwoscan not only improve OEE but also contribute to reducing waste and energy consumption. |
Remote Monitoring | The ability to monitor and manage manufacturing processes remotely is becoming essential. This trend gained momentum during the COVID-19 pandemic and is likely to continue. |
Customisation and Personalization | Smart manufacturing enables greater customisation of products to meet individual customer demands, a trend in various industries, including automotive and consumer electronics. |
In navigating these challenges and embracing future trends, manufacturers who adopt smart technology like Iwoscan position themselves at the forefront of Industry 4.0. The ability to collect and analyse real-time data, predict maintenance needs, optimise processes, and enhance product quality improves OEE and overall competitiveness and sustainability.
The journey of merging smart technology and manufacturing is ongoing, promising a future where efficiency, quality, and innovation converge to shape the manufacturing landscape.
Comments
test
Posted by User ID:Add a Comment
You must be logged in to post a comment.