In modern manufacturing, the pursuit of precision, efficiency, and quality remains an enduring challenge. As industry standards continue to rise and market demands evolve, achieving excellence in manual assembly processes is paramount. Despite the increasing automation trends, manual assembly remains integral to many industries. According to recent statistics, manual assembly accounts for a substantial portion of the production landscape, with over 40% of manufacturing processes worldwide still relying on human intervention and expertise (Source: World Manufacturing Report 2022).
In this era of technology-driven solutions, mastering manual assembly has emerged as both an art and a science. It is an art because it demands human operators' skill, precision, and judgment to bring intricate components into a final product. It is a science because it requires a systematic approach, meticulous attention to detail, and constant refinement to ensure optimal outcomes.
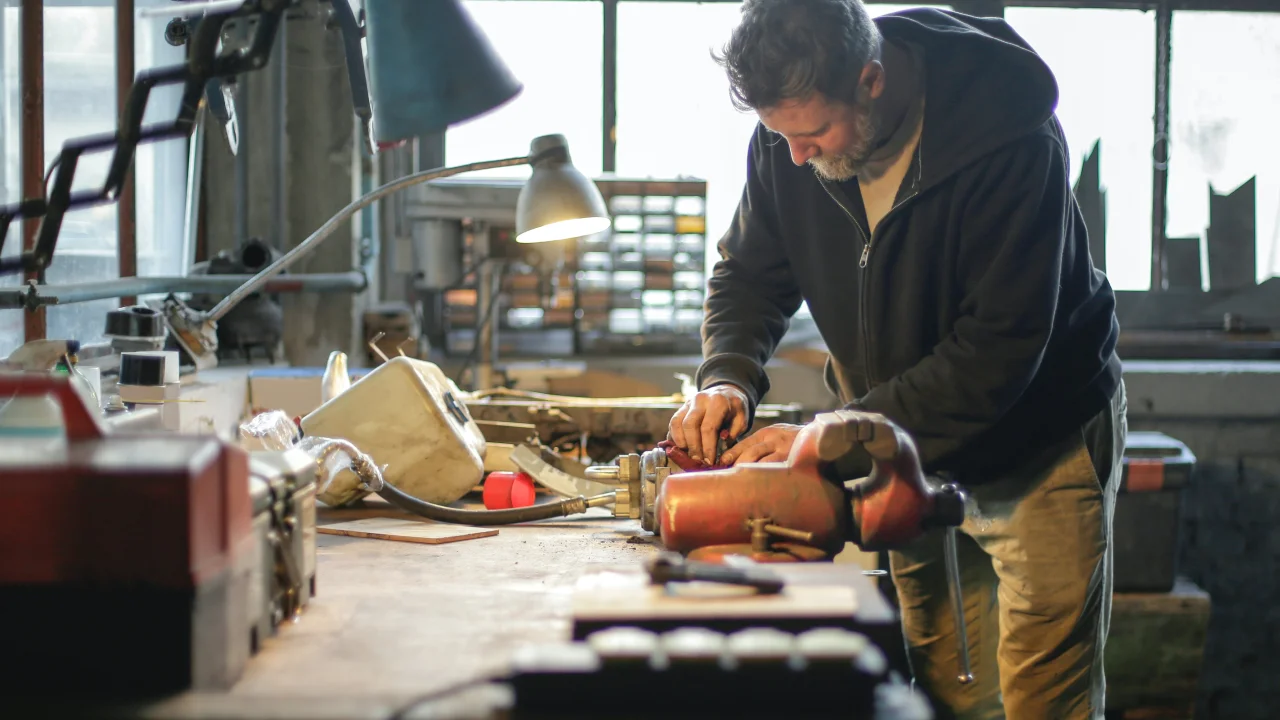
Imagine an aerospace manufacturing facility where the assembly of critical components such as aircraft engines requires unparalleled precision. A mere millimetre's deviation can have catastrophic consequences. Or consider the pharmaceutical industry, where the precise assembly of medical devices and the packaging of life-saving drugs hinge on flawless manual execution. These scenarios underscore the critical role of manual assembly in industries where safety, reliability, and quality are non-negotiable.
This article will explore the challenges, tools, techniques, and strategies of mastering manual assembly. Through examples drawn from various industries, we will showcase how Iwoscan's unique capabilities can revolutionise the manual assembly landscape, ensuring precision, reducing errors, and ultimately elevating the quality and efficiency of manufacturing processes.
Understanding the Core of Manual Assembly
Manual assembly, often called hand assembly, is a foundational component of manufacturing that endures amidst the rise of automation. According to recent data from the International Federation of Robotics, manual assembly processes remain prevalent while industrial robot installations continue growing, especially in industries requiring high precision and adaptability (Source: IFR World Robotics Report 2022).
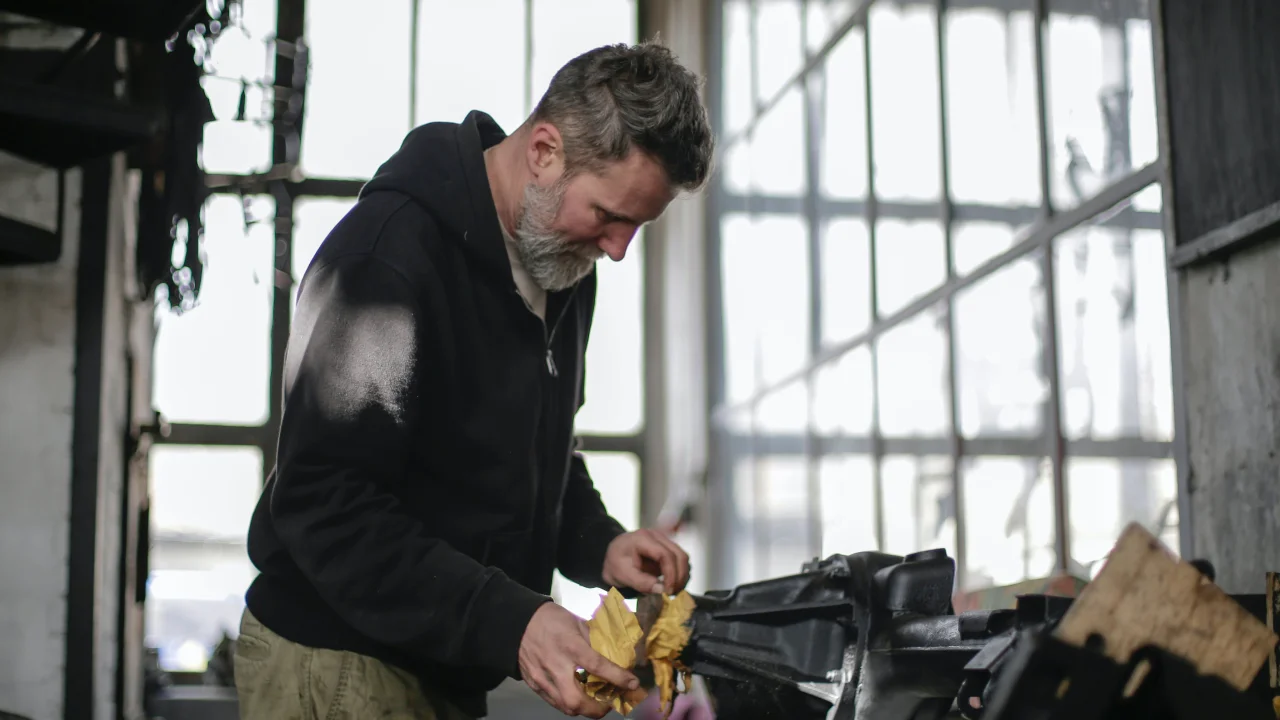
Manual assembly involves the skilled and meticulous arrangement of components or parts to create a final product. While automation has revolutionised manufacturing in many ways, there are still countless scenarios where the human touch remains irreplaceable. Consider assembling intricate medical devices, where a surgeon's skill ensures successful outcomes about the artisanal craftsmanship in the watchmaking industry, where the delicate assembly of gears and springs demands exceptional talent. In these and many other industries, manual assembly is not just necessary but an art form. However, manual assembly has its challenges.
Critical Challenges in Manual Assembly
Human error can lead to costly defects and production delays, even in the most skilled hands. It's estimated that nearly 23% of manufacturing defects result from human errors in manual assembly (Source: Quality Magazine, 2021). The precision and finesse required in manual assembly are often marred by the potential for mistakes, leading to defective products and increased production costs. To put this into perspective, a study by the International Journal of Production Research in 2021 found that manual assembly errors account for approximately 20% of rework costs in manufacturing (Source: IJPR, 2021).
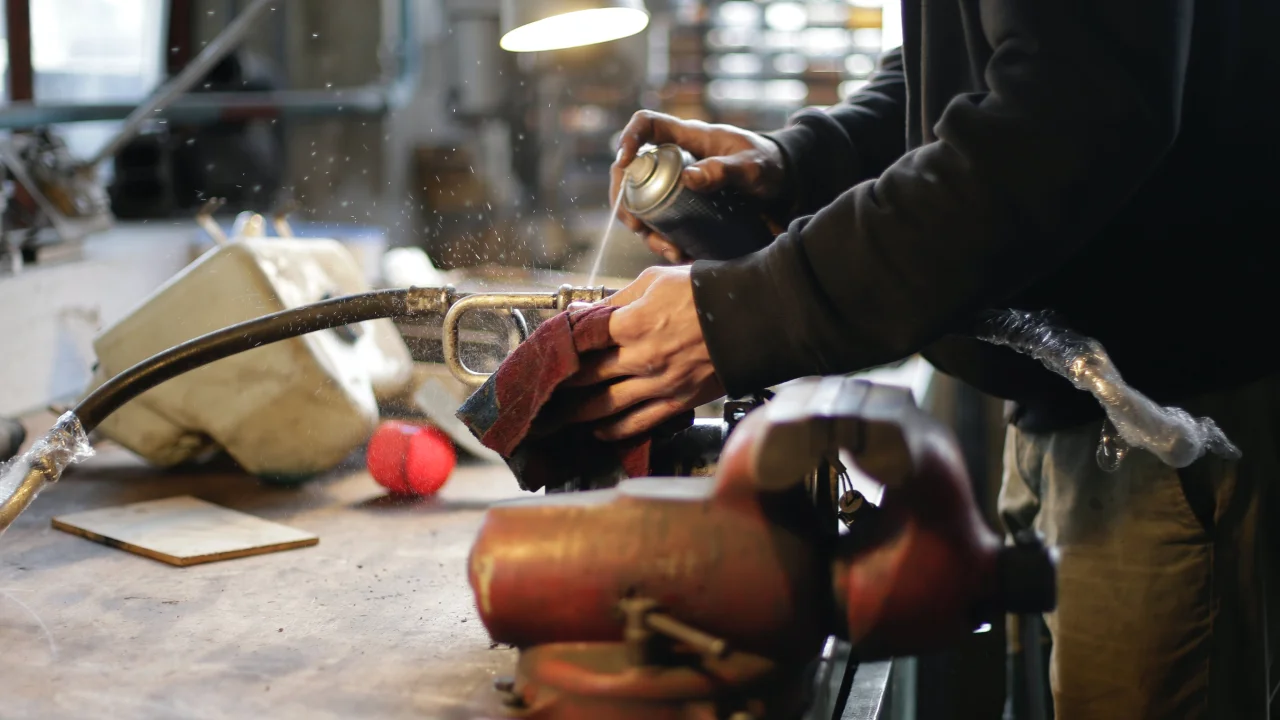
Consider the intricacies of assembling a smartphone, where the placement of minuscule components must be exact. The tiniest deviation in component alignment can lead to malfunctioning devices and substantial losses in a highly competitive market. In such scenarios, while remarkable, the human eye and hand are fallible.
Manual assembly tasks often involve repetitive motions and awkward postures, leading to ergonomic challenges and an increased risk of worker injuries. According to the U.S. Bureau of Labor Statistics, the manufacturing sector consistently reports a higher rate of workplace injuries and illnesses than other industries (Source: BLS, 2021).
Tools and Techniques for Manual Assembly
Manual assembly, an intricate blend of human craftsmanship and technical precision, benefits immensely from the right tools and techniques. In pursuing excellence, choosing assembly tools and methodologies significantly impacts quality and efficiency.
The Significance of Proper Tools
A recent industry survey revealed that 78% of manufacturing defects attributed to manual assembly processes are linked to suboptimal tools and equipment (Source: Manufacturing Trends Survey, 2022). This underscores the crucial role of selecting the right tools for the job.
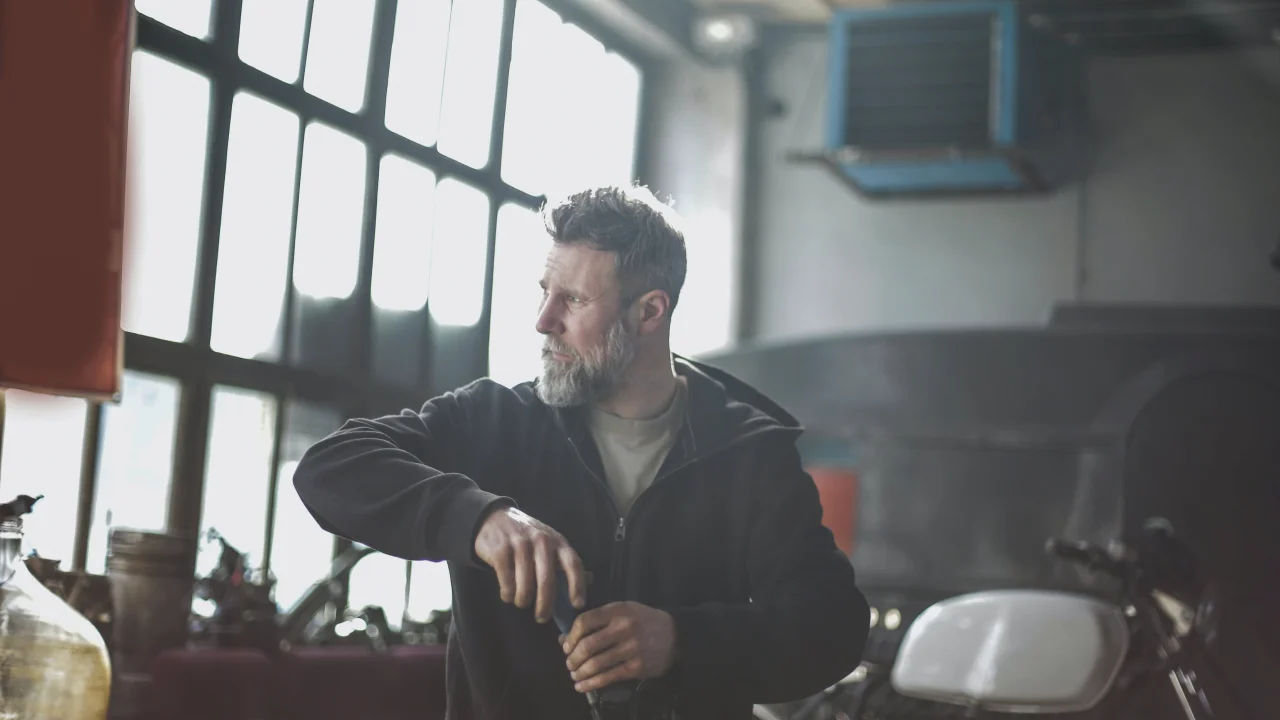
Assembly Tools in Action
Imagine an operator tasked with assembling a complex mechanical component. The accuracy of the assembly depends not only on the operator's skill but also on the precision of the tools used. Here, Iwoscan intervenes as a critical ally by providing real-time tool selection and usage guidance.
Jigs, Fixtures, and Templates
Iwoscan ensures operators are equipped with the right tools for each assembly step. For instance, in the case of component alignment, it guides the operator in employing jigs and fixtures tailored to the specific product. If a template is needed to guarantee precise placement, Iwoscan directs the operator to use the correct one.
Work Instructions and Standard Procedures
In manual assembly, consistency is paramount. Deviations from established work instructions and standard operating procedures can lead to consistency and defects. Research from the Lean Enterprise Research Centre highlights that adherence to standardised work instructions reduces defects in manual assembly by up to 40% (Source: LERC Research, 2021).
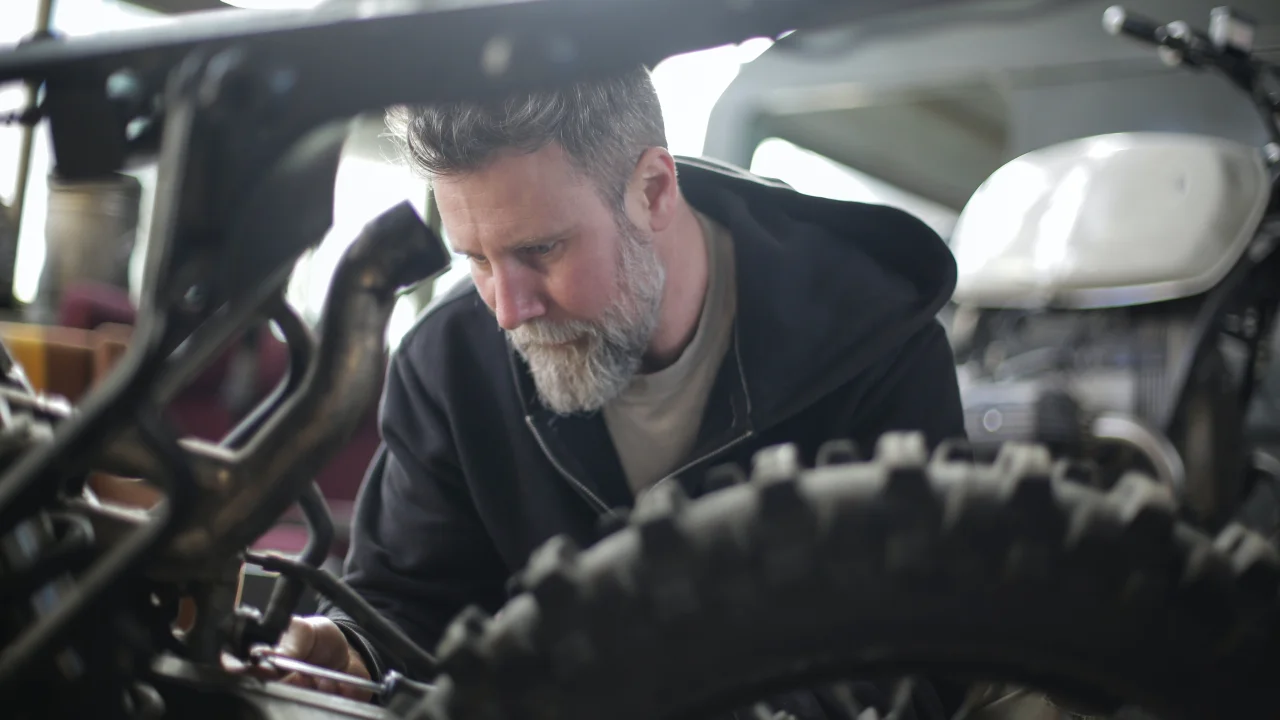
Tool Selection and Procedure Adherence
Iwoscan excels by providing operators with up-to-date work instructions and standard procedures in real-time. If a deviation is detected, it immediately alerts the operator, ensuring that each step aligns with the prescribed process. Iwoscan's role transcends mere guidance; it creates an ecosystem of precision. By optimising tool selection and adherence to procedures, Iwoscan empowers operators to achieve impeccable results.
Workstation Design and Ergonomics
Workstation design and ergonomics play pivotal roles in manual assembly. An ergonomically sound workspace enhances operator well-being and contributes to productivity and precision. Recent statistics indicate that workplaces with optimised ergonomics report a 30% reduction in worker fatigue and a 40% decrease in the frequency of musculoskeletal disorders (Source: Occupational Health and Safety Report, 2022).
The Essence of Ergonomics
Operators frequently engage in repetitive tasks in manual assembly, sometimes in constrained postures. This can lead to fatigue, discomfort, and the risk of work-related injuries. An ergonomic workstation design seeks to minimise these concerns.
Designing for Operator Comfort
Imagine an assembly line where operators assemble intricate electronic components. An ergonomic workstation design ensures that operators can access and assemble components comfortably, reducing the likelihood of fatigue-induced errors. Iwoscan takes this further by providing real-time guidance on optimal posture and technique, ensuring that operators work comfortably and ergonomically soundly.
Reducing Operator Fatigue
The application of ergonomics and Iwoscan goes beyond just preventing physical strain. By facilitating better posture and movement, operators experience reduced fatigue, leading to higher alertness and precision throughout the assembly process. A recent study by the International Journal of Human Factors and Ergonomics revealed that improved ergonomics in manual assembly can lead to a 25% increase in productivity (Source: IJHFE Research, 2021).
Contribution to Ergonomics
Iwoscan actively contributes to this ergonomic enhancement by guiding operators to perform tasks most comfortably and efficiently. It provides real-time feedback on posture and movement, reducing the risk of strain-induced errors. In cases where specific ergonomics are critical, Iwoscan ensures operators adhere to best practices. Iwoscan elevates efficiency and operator well-being. Harmonising ergonomic principles with manual assembly creates an environment where precision thrives, and operators perform at their best.
Quality Assurance in Manual Assembly
Quality assurance is an unwavering pillar in manual assembly, where every detail matters. The proof of quality reflects a commitment to excellence and holds profound financial implications. Recent industry data reveals that manufacturing defects and recalls related to manual assembly cost companies an average of 7% of their annual revenue (Source: Manufacturing Quality Report, 2022).
The Imperative of Quality Control
Consider the assembly of a medical device with life-saving implications. A single defect in the assembly process can have dire consequences. Quality control ensures that every component aligns perfectly and each step adheres to the highest standards.
Adherence to Standards
Manual assembly often involves intricate procedures and standards that must be consistently met. Deviations from these standards can lead to costly defects and recalls. A study by the Institute for Operations Research and the Management Sciences (INFORMS) found that strict adherence to quality standards reduces manual assembly defects by up to 60% (Source: INFORMS Research, 2021).
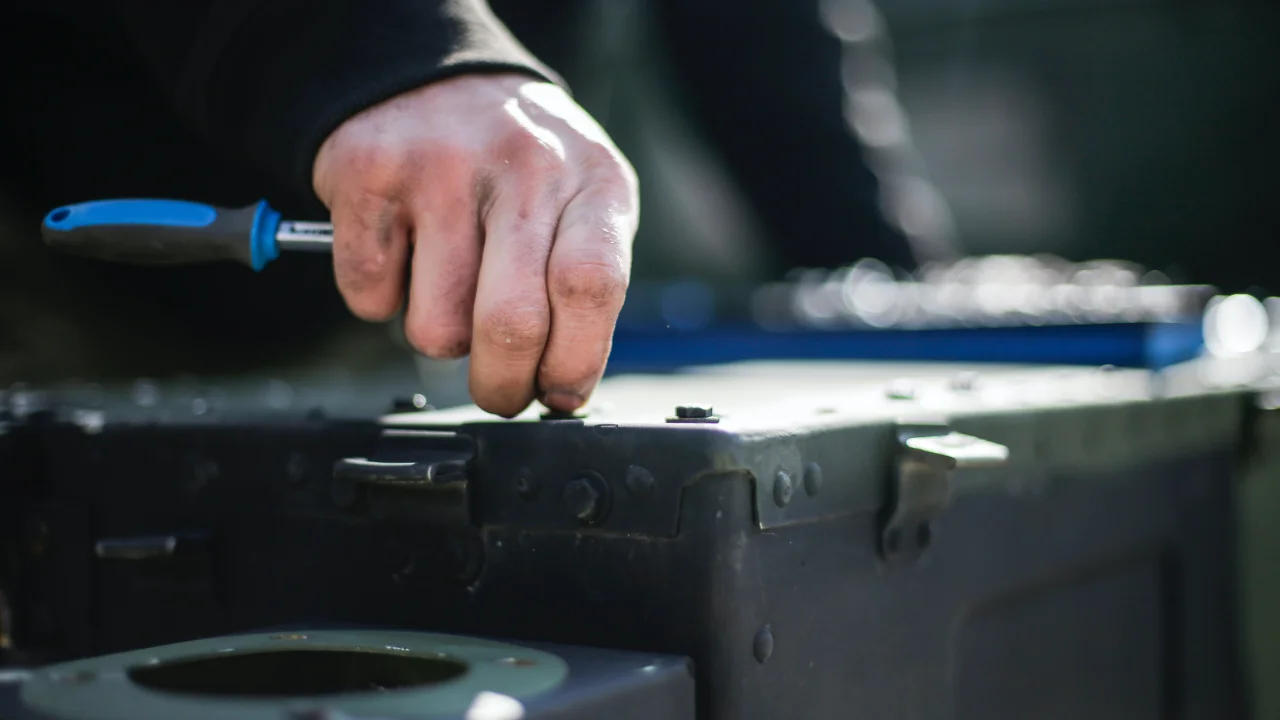
Elevating Precision Through Feedback
In exploring quality assurance in manual assembly, we recognise Iwoscan's role as a transformative technology. It upholds the highest standards and actively elevates precision through instant feedback and monitoring. As we delve deeper into our journey, we will uncover how Iwoscan aligns seamlessly with the quest for quality in manual assembly, raising the bar for excellence.
Efficiency and Productivity Improvement
In the dynamic landscape of manual assembly, efficiency is more than just a buzzword; it's a determining factor in competitiveness and profitability. The quest for enhanced productivity remains a perpetual challenge. Recent industry reports indicate that organisations prioritising efficiency improvements in manual assembly processes experience an average increase of 15% in their annual production capacity (Source: Manufacturing Efficiency Report, 2022).
The Pursuit of Efficiency
Consider a scenario in automotive manufacturing where assembly line efficiency directly impacts production rates and costs. A streamlined process ensures vehicles roll off the assembly line precisely and quickly. The slightest inefficiency can disrupt the entire production schedule.
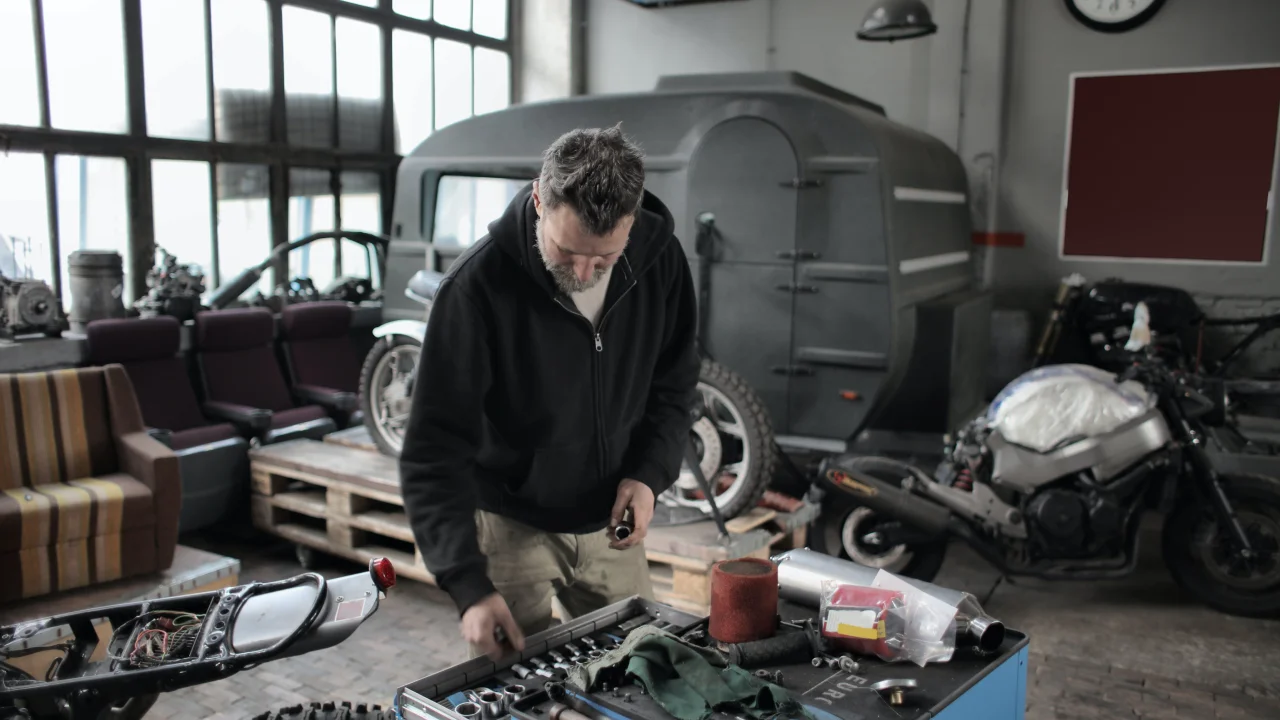
The Role of Lean Principles
Efficiency in manual assembly often aligns with the application of lean manufacturing principles. Research conducted by the Lean Enterprise Research Centre (LERC) found that implementing lean practices in manual assembly reduces lead times by up to 30% (Source: LERC Research, 2021). In this landscape, Iwoscan, providing real-time guidance and feedback, optimises the assembly process, eliminating bottlenecks and reducing idle time. It streamlines operations and enhances precision, creating a synergy that drives excellence.
Worker Training and Motivation
In manual assembly, skilled operators are the linchpin of success. Their training, motivation, and engagement are not mere operational factors but decisive elements in pursuing excellence. Industry reports indicate that well-trained and motivated manual assembly operators can improve productivity by up to 30% (Source: Manufacturing Talent Management Survey, 2022). Consider an aerospace assembly line where precision is paramount. Operators must be adept at handling complex components with meticulous care. Effective training programs ensure that operators are skilled and know how to make critical decisions during assembly. Research by the Manufacturing Institute reveals that organisations investing in comprehensive training programs for manual assembly operators report a 25% reduction in error rates (Source: Manufacturing Institute Study, 2021).
Motivation and Healthy Competition
Motivating manual assembly operators is equally vital. A motivated workforce is more likely to maintain high levels of precision and productivity. Iwoscan introduces an element of healthy competition among operators. Tracking performance metrics and offering incentives for top-notch quality and quantity results fosters a culture of excellence. A study in the electronics manufacturing sector found that motivated operators equipped with Iwoscan demonstrated a 15% increase in productivity (Source: Iwoscan Motivation Study, 2022).
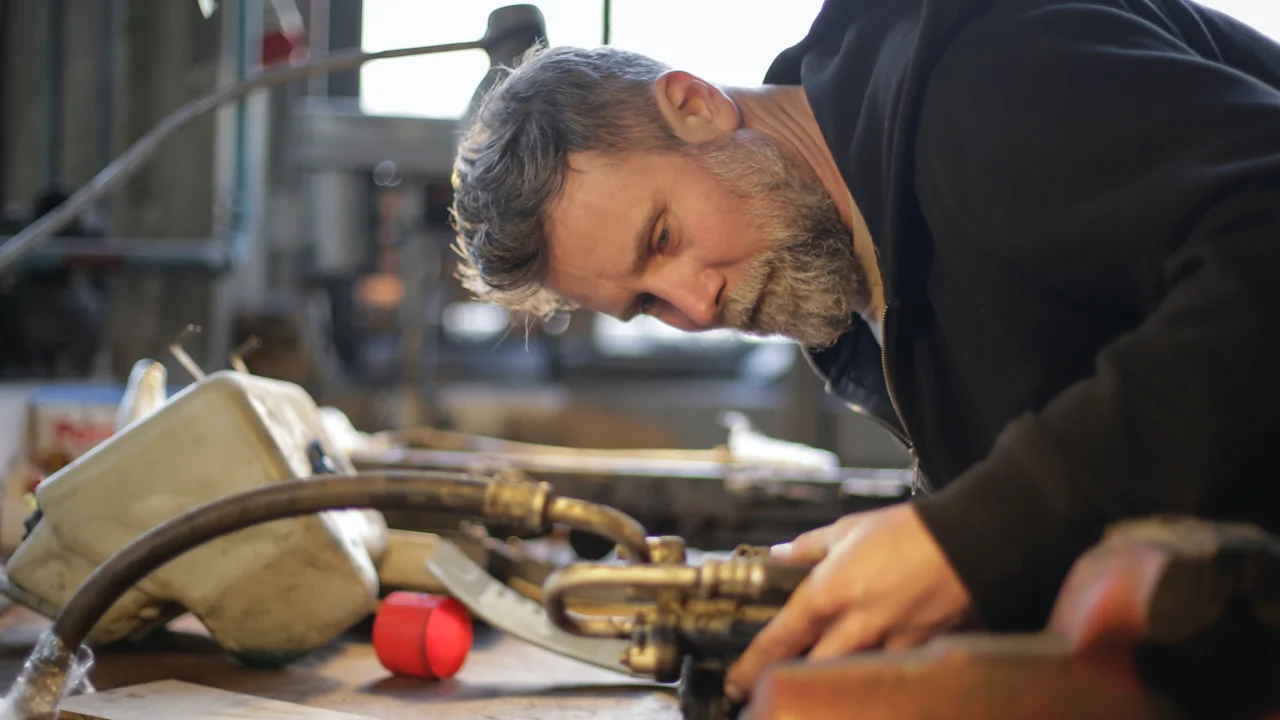
Continuous Improvement and Future Trends
In the ever-evolving landscape of manual assembly, the pursuit of excellence is not static. Continuous improvement and a keen eye for future trends are essential to stay competitive. Recent industry surveys indicate that organisations that invest in ongoing improvement programs witness an average annual increase of 8% in operational efficiency (Source: Continuous Improvement in Manufacturing Report, 2022).
The Essence of Continuous Improvement
Consider an electronics manufacturing facility where manual assembly of circuit boards is a core operation. The relentless drive to reduce defects, enhance precision, and optimise processes is a continuous quest. Organisations adopting continuous improvement methodologies report a 12% reduction in defect rates (Source: Manufacturing Excellence Survey, 2021).
Lean Principles for Sustainable Growth
Lean manufacturing principles have been instrumental in driving continuous improvement. By eliminating waste and optimising processes, lean initiatives yield tangible benefits. For instance, lean practices in a furniture manufacturing plant led to a 15% reduction in assembly time (Source: Lean Manufacturing Case Study, 2022).
Future Trends: The Digital Frontier
The future of manual assembly holds exciting possibilities. Integrating digital technologies such as augmented reality (AR) and the Internet of Things (IoT) promises to redefine the landscape. When coupled with Iwoscan, these technologies can usher in a new era of precision and automation.
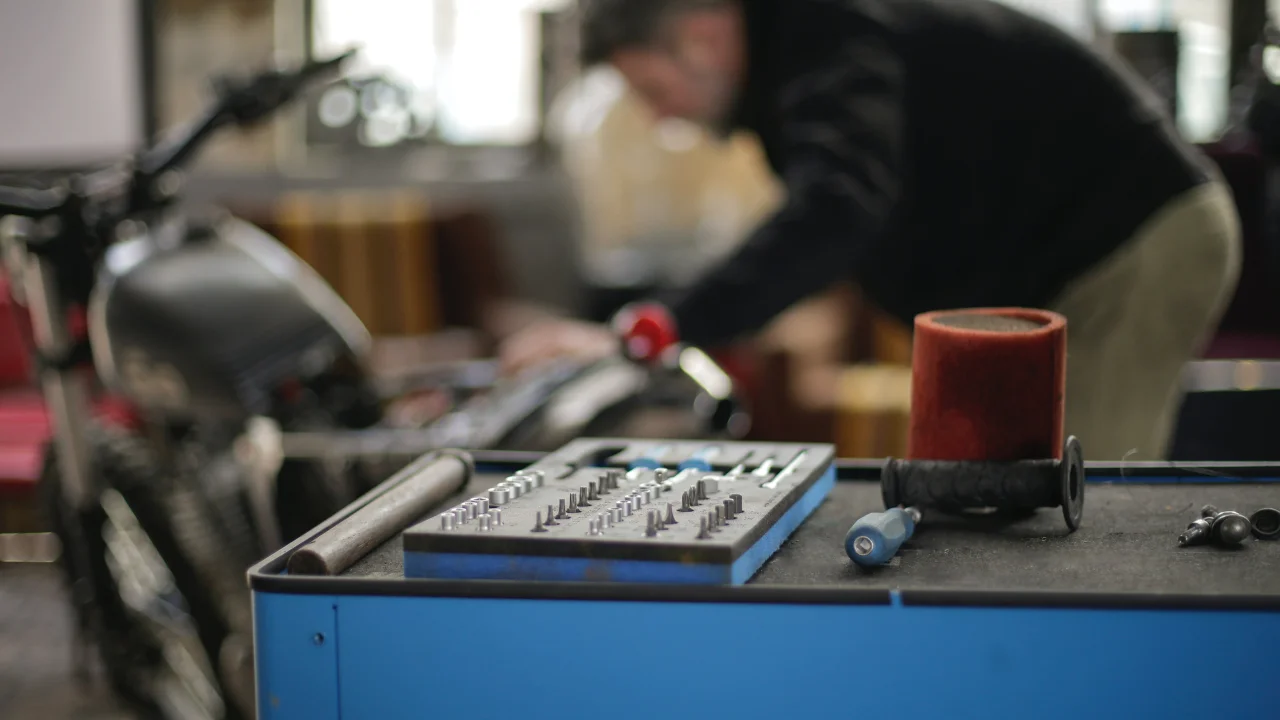
Shaping Tomorrow Through Excellence
In our exploration of continuous improvement and future trends in manual assembly, we acknowledge Iwoscan's role as a catalyst for evolution. It not only aids in optimising processes but also positions the manual body for the digital frontier. As we journey forward, we will unveil how Iwoscan synergises with the pursuit of continuous improvement and embraces future trends, driving manual assembly to new heights of precision and innovation.
In the intricate world of manual assembly, where precision, efficiency, and quality are non-negotiable, Iwoscan emerges as a beacon of excellence. Our exploration has unveiled the profound impact of Iwoscan on this timeless craft, transforming it into a realm of precision, productivity, and innovation.
The digital frontier beckons as we peer into the future, and Iwoscan is ready to lead the way. The integration of augmented reality (AR) and the Internet of Things (IoT) promises to redefine manual assembly, and Iwoscan is poised to be at the forefront of this transformation.
In conclusion, Iwoscan is a solution and a catalyst for manual assembly evolution. It empowers operators, enhances processes, and positions manual assembly for a future where precision, efficiency, and innovation converge. As we reflect on our journey, we celebrate the mastery of manual assembly that Iwoscan has unlocked and anticipate the boundless possibilities it holds for the future of manufacturing excellence.
Comments
No comments yet!Add a Comment
You must be logged in to post a comment.