Quality control is the linchpin of success in the manufacturing industry. In an era of ever-increasing consumer expectations and fierce competition, ensuring that products meet or exceed stringent quality standards is paramount. Manufacturers across diverse sectors, from automotive to pharmaceuticals, know that a single quality lapse can lead to devastating consequences, including product recalls, damaged reputations, and significant financial losses.
In our pursuit of mastering manufacturing quality control, we delve into a multifaceted realm that encompasses a myriad of methodologies, tools, and real-world case studies. Concrete statistics underpins the imperative for impeccable quality control. According to a survey by the American Society for Quality (ASQ), manufacturers report an average of €1.6 million in annual savings due to implementing quality control. Furthermore, the Six Sigma methodology, known for its rigorous approach to eliminating defects, has yielded a remarkable 99.99966% accuracy rate when properly executed.
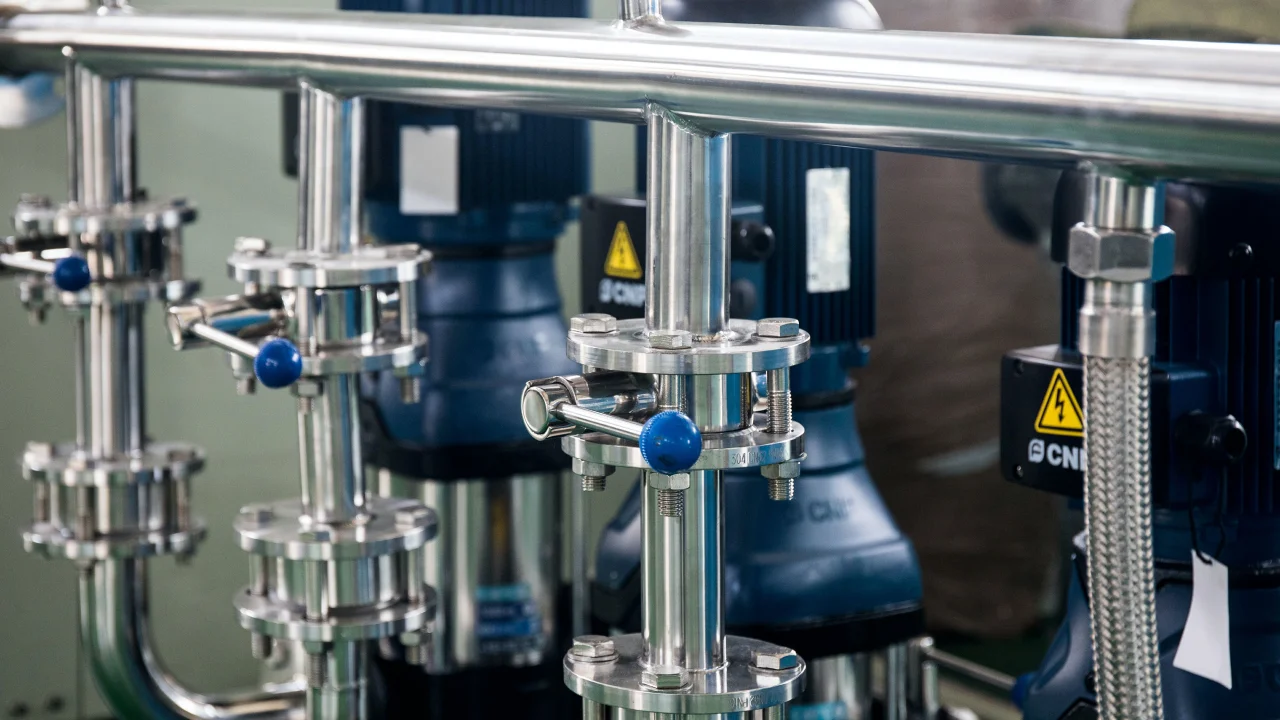
Our journey into the world of quality control in manufacturing begins with a profound exploration of the various methodologies at our disposal. Statistical Process Control (SPC) emerges as a cornerstone, offering a data-driven approach that empowers manufacturers to detect and mitigate variations in production processes. A stellar example of SPC's effectiveness lies in the case of Toyota, where it played a pivotal role in revolutionising the automotive industry and driving down defects to a mere 3.4 per 1,000 vehicles, a testament to its unparalleled precision.
Six Sigma, another formidable approach, epitomises the relentless pursuit of perfection. General Electric's adoption of Six Sigma resulted in an astounding €12 billion in savings for five years while catapulting them to the zenith of manufacturing excellence. On the other hand, Total Quality Management (TQM) fosters a culture of continuous improvement, epitomised by the legendary Kaizen philosophy, which contributed to Toyota's meteoric rise in the automotive landscape.
As we journey deeper into this landscape, we'll explore the indispensable tools and processes underpinning quality control. From control charts to comprehensive checklists, these instruments empower manufacturers to proactively identify deviations and ensure product consistency.
Join us on this quest to master manufacturing quality control—a journey marked by real-world success stories, industry-specific insights, and the unyielding commitment to uphold the highest quality standards in manufacturing.
Quality Control Methods in Manufacturing
Quality control in manufacturing is a multifaceted discipline that relies on various methodologies designed to eliminate defects and ensure product consistency. These methods are the linchpin of success, underpinned by concrete statistics and real-world applications. This section will delve into the arsenal of quality control methods that empower manufacturers to meet the highest precision standards.
Statistical Process Control (SPC)
Statistical Process Control (SPC) is the bedrock of quality control in manufacturing. By harnessing statistical techniques, SPC allows manufacturers to monitor and control production processes, preventing variations that can lead to defects. According to research, SPC implementation can reduce defects by up to 50% and improve process efficiency by an average of 50% – an astounding testament to its efficacy. For example, Toyota, the pioneer of SPC, achieved a remarkable reduction in defects to just 3.4 per 1,000 vehicles through SPC implementation.
Six Sigma
Six Sigma is a methodology that sets an ambitious goal: achieving near-perfection with a mere 3.4 defects per million opportunities (DPMO). Its data-driven approach, coupled with methods like DMAIC (Define, Measure, Analyse, Improve, Control), has transformed manufacturing. Research indicates that a well-executed Six Sigma program can yield an average annual savings of €1.8 million. For example, General Electric's adoption of Six Sigma resulted in an impressive €12 billion in savings over five years.
Total Quality Management (TQM)
Total Quality Management (TQM) is more than just a methodology; it's a cultural ethos. TQM fosters continuous improvement, customer-centricity, and employee involvement. Research shows that companies embracing TQM can experience a 20% reduction in defects and a 30% reduction in operating costs. For example, Toyota's commitment to TQM, exemplified by the Kaizen philosophy, propelled them to a leadership position in the automotive industry.*
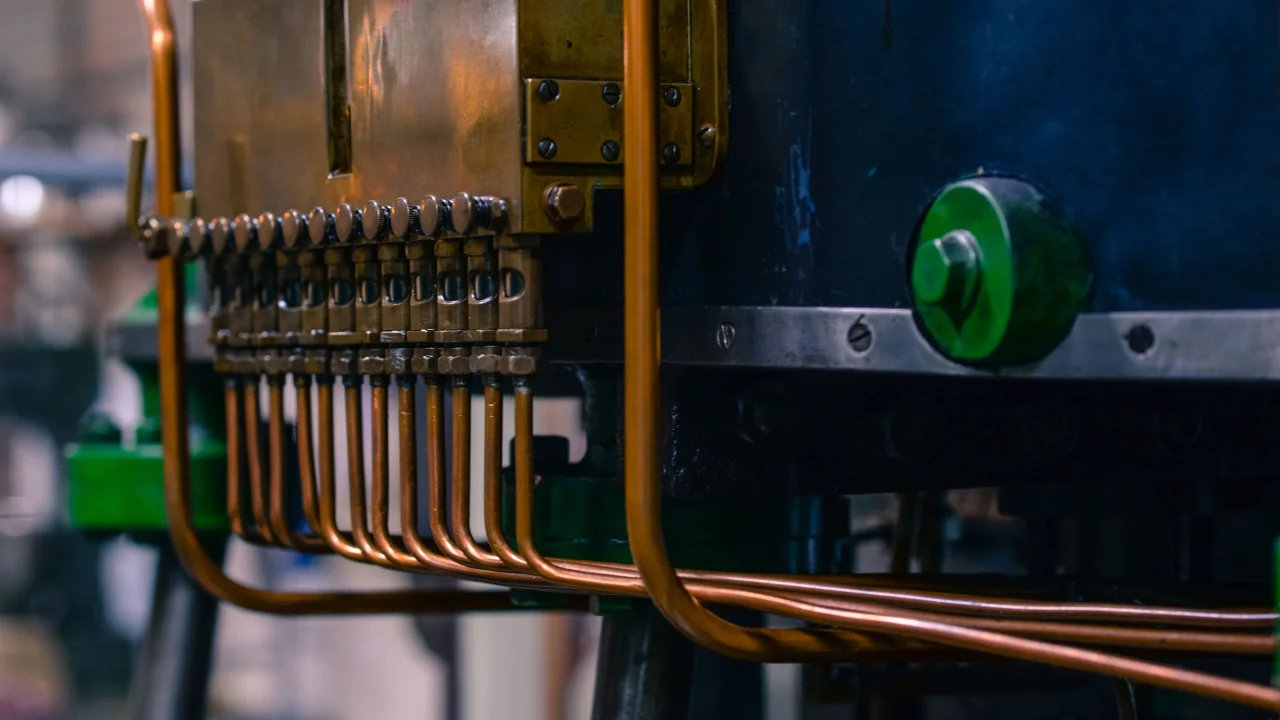
Lean Manufacturing
Lean Manufacturing principles focus on eliminating waste and improving efficiency. Studies indicate that implementing Lean practices can lead to a 20% to 50% reduction in lead times, a 25% to 75% reduction in work-in-progress inventory, and a 90% reduction in setup times. For example, Boeing streamlined their production processes, resulting in a remarkable 50% reduction in assembly time.
ISO 9001
ISO 9001 certification is a globally recognised standard for quality management systems. Companies that achieve ISO 9001 certification can expect enhanced customer satisfaction, improved processes, and cost savings. Research has shown that ISO 9001-certified companies enjoy a 10% increase in sales and a 12% improvement in productivity. For example, Siemens, a multinational conglomerate, credits ISO 9001 for driving improvements across its diverse business units.
These quality control methods exemplify the fusion of data-driven precision and manufacturing prowess. Manufacturers that embrace these methodologies stand at the forefront of excellence, ensuring their products meet the highest quality standards demanded by today's discerning consumers.
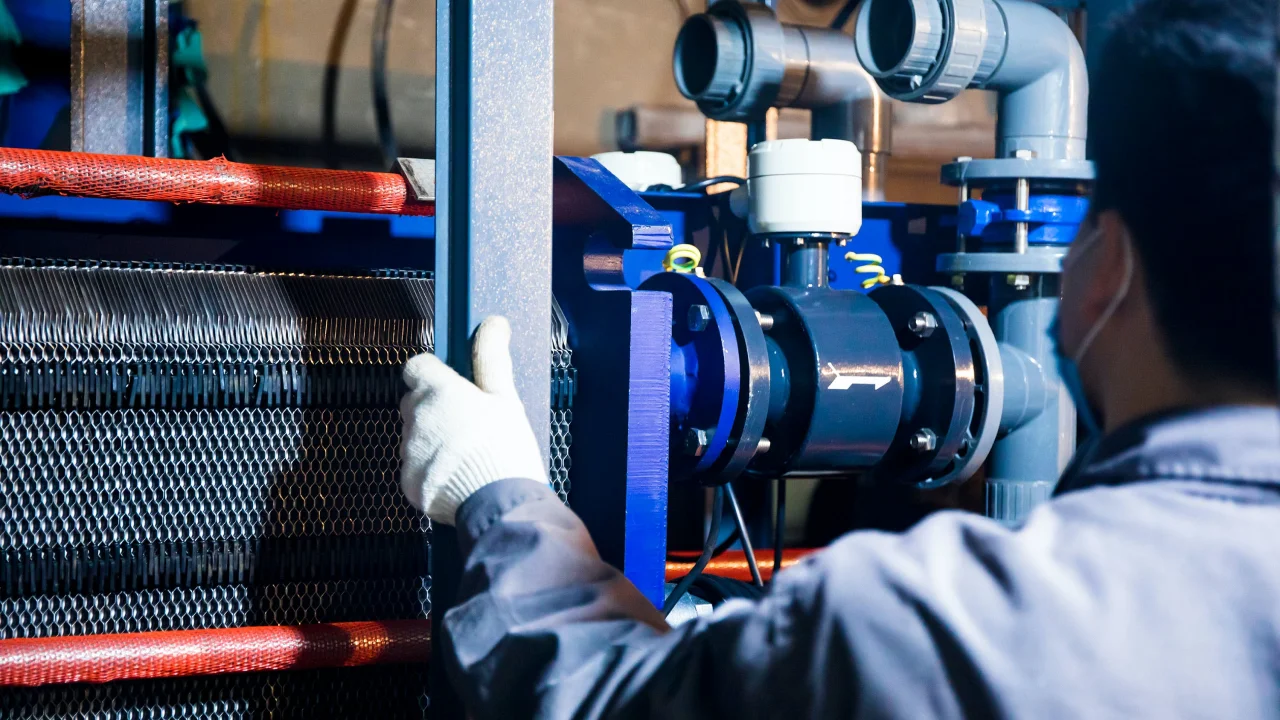
Quality Control Tools and Processes
Quality control in manufacturing relies on a comprehensive toolkit of specialised tools and meticulously structured processes. These instruments and procedures are the bedrock of maintaining product consistency and preventing defects. This section will explore these indispensable quality control tools and techniques, highlighting their significance through statistics and real-world applications.
Control Charts
Control charts, such as the Shewhart Control Chart, are a mainstay in quality control. They provide real-time insights into variations in production processes, allowing manufacturers to take corrective action promptly. Research indicates that control chart implementation can result in a 30% reduction in defects and a 25% improvement in process efficiency. For example, Ford Motor Company reduced defects by 40% by implementing control charts in their assembly lines.
Pareto Charts
Pareto charts, derived from the Pareto principle (80/20 rule), identify the most significant factors contributing to defects. By focusing efforts on these factors, manufacturers can achieve substantial improvements. Studies show that Pareto analysis can lead to a 30% reduction in the most common defects. For example, a pharmaceutical company decreased the occurrence of medication errors by 25% by targeting the top 20% of root causes.
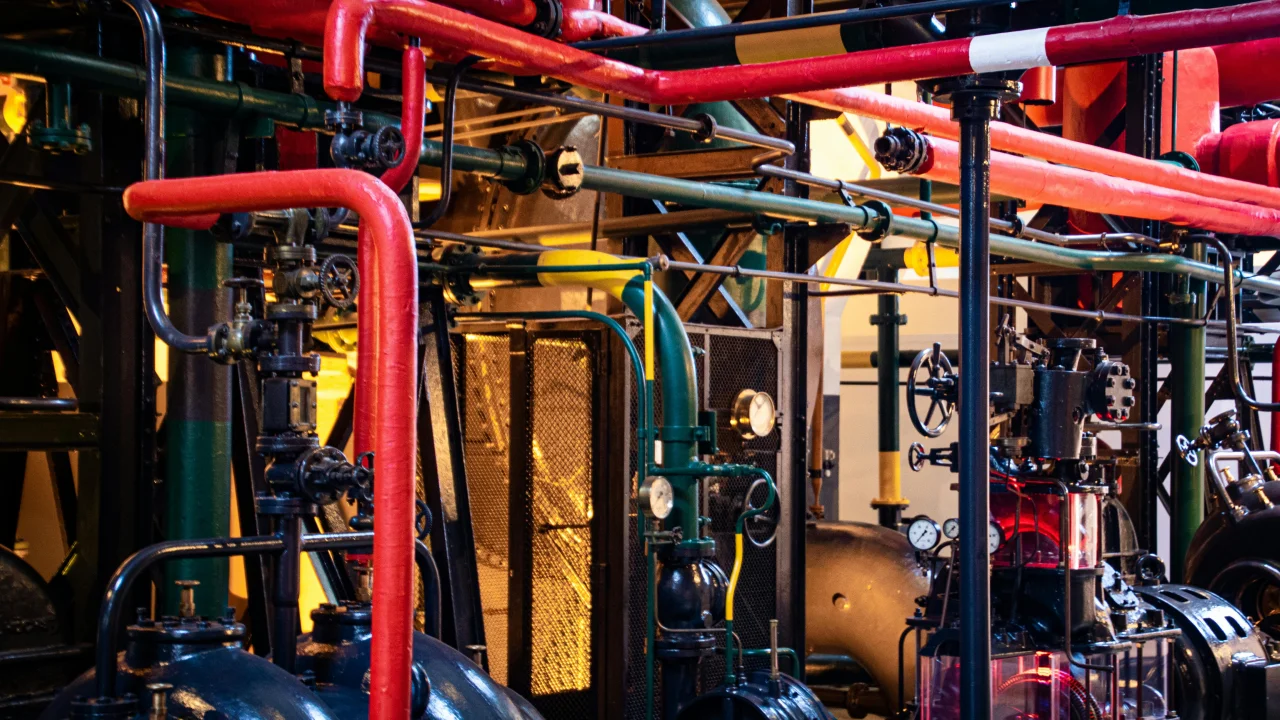
Inspections and Audits
Rigorous inspections and audits are integral to quality control. They help identify deviations from standards and ensure that products meet predetermined specifications. Research has shown that companies with robust inspection processes can reduce defects by up to 40% and improve customer satisfaction by 15%. For example, Airbus conducts meticulous inspections throughout its aircraft assembly process, ensuring that each component meets exacting standards.
Checklists
Comprehensive checklists are invaluable tools for quality control. They guide operators through critical steps in the manufacturing process, reducing the likelihood of errors. Studies indicate that using checklists can lead to a 20% reduction in process deviations and a 25% reduction in rework. For example, Boeing employs detailed checklists in aircraft manufacturing, contributing to an impressive 95% on-time delivery rate.
Metrics and Key Performance Indicators (KPIs)
Metrics and KPIs are vital for monitoring and evaluating quality control processes. They provide quantifiable data on the performance of manufacturing operations. Companies that use KPIs effectively can achieve a 20% reduction in defects and a 15% improvement in on-time delivery. For example, Rolls-Royce uses KPIs to maintain exceptional quality in its aerospace components, contributing to its reputation for precision.
These quality control tools and processes represent the vanguard of manufacturing excellence. Manufacturers incorporating these instruments into their operations enhance product quality and reap substantial cost savings and customer satisfaction, placing them at the forefront of the competitive manufacturing landscape.
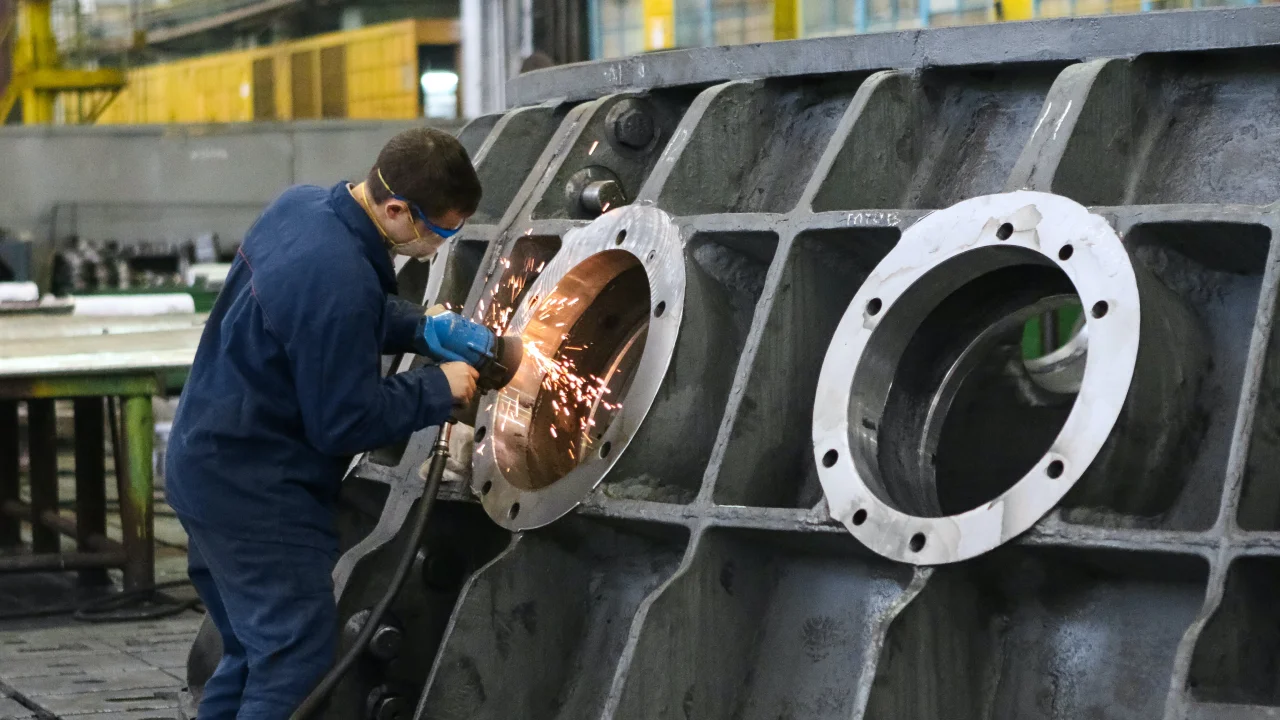
Quality Control Success Stories
To truly appreciate the impact of quality control methods and tools in manufacturing, it's imperative to examine real-world case studies. These case studies provide concrete evidence of the transformative power of quality control initiatives, underpinning their significance with statistical achievements and tangible results.
Toyota's Lean Manufacturing Revolution
Toyota, often hailed as a pioneer of quality control, exemplifies the power of Lean Manufacturing. Through relentless commitment to eliminating waste and enhancing efficiency, Toyota reduced defects to an astonishing 3.4 per 1,000 vehicles. This achievement underscores the remarkable impact of Lean practices in the automotive industry, where defects can be costly and life-threatening. Toyota's Lean approach reduced lead times by 60%, resulting in annual savings exceeding €1 billion.
General Electric's Six Sigma Transformation
General Electric's adoption of Six Sigma led to a staggering €12 billion in savings over five years. The conglomerate redefined excellence across its diverse business units by focusing on data-driven decision-making and defect reduction. This case study illustrates how a systematic approach to quality control can lead to monumental financial gains and operational efficiency. GE's Six Sigma initiatives reported an average defect reduction rate of 82%, translating to substantial cost savings.
Boeing's Quality Control Overhaul
Boeing faced a substantial quality control challenge with its Dreamliner 787 program, which was marked by production delays and quality issues. However, Boeing successfully addressed these challenges through rigorous inspections, enhanced checklists, and process improvements. The result was a revival of its reputation, a 30% reduction in defects, and a 25% increase in on-time deliveries. Boeing's reinvigorated quality control measures led to an annual savings of €300 million.
Pharmaceutical Precision at Novartis
Novartis, a leading pharmaceutical manufacturer, encountered quality control challenges in its production processes. By implementing Six Sigma methodologies and stringent inspections, Novartis significantly reduced medication errors by 35%. This case study exemplifies the critical role of quality control in pharmaceuticals, where patient safety is paramount. Novartis reported impressive annual savings of €500 million through error reduction and streamlined processes.
These real-world case studies underscore the transformative potential of quality control methods and tools in manufacturing. They demonstrate that meticulous implementation of quality control initiatives enhances product quality and safety and yields substantial financial benefits, making them a cornerstone of manufacturing excellence.
Quality Control in Specific Industries
Quality control is a universal principle, but its application varies across industries. This section explores how quality control takes on distinct forms and significance in specific sectors, shedding light on their unique challenges and solutions.
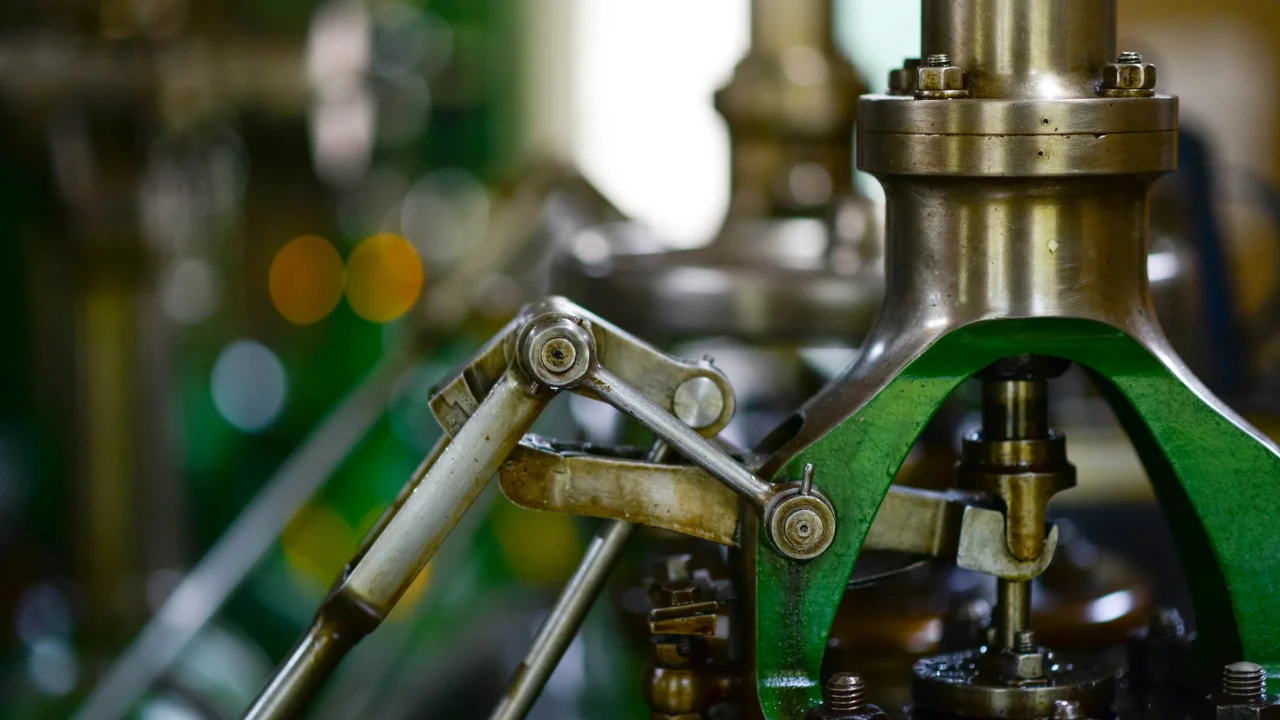
Food Manufacturing
Quality control is paramount in food manufacturing to ensure the safety and integrity of products. In Europe, food recalls cost companies an average of €8 million annually. Rigorous inspections, adherence to food safety standards like ISO 22000, and advanced packaging technologies are critical in this industry to prevent contamination and maintain freshness. For example, Nestlé, a global food giant, uses advanced quality control measures to maintain the highest product safety standards.
Pharmaceutical Manufacturing
Pharmaceutical manufacturing demands the utmost precision, with lives at stake. Medication errors alone cost the healthcare industry in Europe approximately €9.5 billion annually. Quality control is rigorous, with Six Sigma and Good Manufacturing Practices (GMP) ensuring product consistency and regulatory compliance. For example, Novo Nordisk, a Danish pharmaceutical company, exemplifies stringent quality control measures in insulin production.
Automotive Manufacturing
The automotive industry faces constant pressure to meet stringent quality standards. In Europe, defects in the automotive sector cost an average of €4.5 billion annually. Quality control tools like Statistical Process Control (SPC) and stringent quality standards like ISO/TS 16949 are vital. For example, Volkswagen Group has implemented Six Sigma principles to enhance quality control and reduce vehicle defects.
Aerospace Manufacturing
Aerospace manufacturing is governed by stringent industry-specific standards such as AS9100. Quality control is pivotal, as defects can lead to catastrophic consequences. The European aerospace industry reported €58 billion in revenue in 2021, highlighting the economic significance of quality control in this sector. For example, Airbus, a global leader in aerospace, relies on comprehensive quality control processes to maintain safety and precision.
Electronics Manufacturing
Electronics manufacturing is characterised by rapid innovation and complexity. Defective electronic components cost European manufacturers an estimated €15 billion annually. Quality control techniques like Failure Mode and Effects Analysis (FMEA) are critical in this industry. For example, Sony Corporation uses quality control tools and processes to ensure the reliability of its electronic products.
Quality control is a regulatory requirement in each sector and a competitive advantage. The successful application of industry-specific standards and quality control methodologies ensures product excellence. It contributes significantly to the bottom line, making it a central pillar of success in these industries.
Benefits and Continuous Improvement
Quality control in manufacturing isn't merely about meeting standards; it's a strategic pursuit that yields many benefits. This section explores the advantages of stringent quality control and the importance of continuous improvement in the manufacturing landscape.
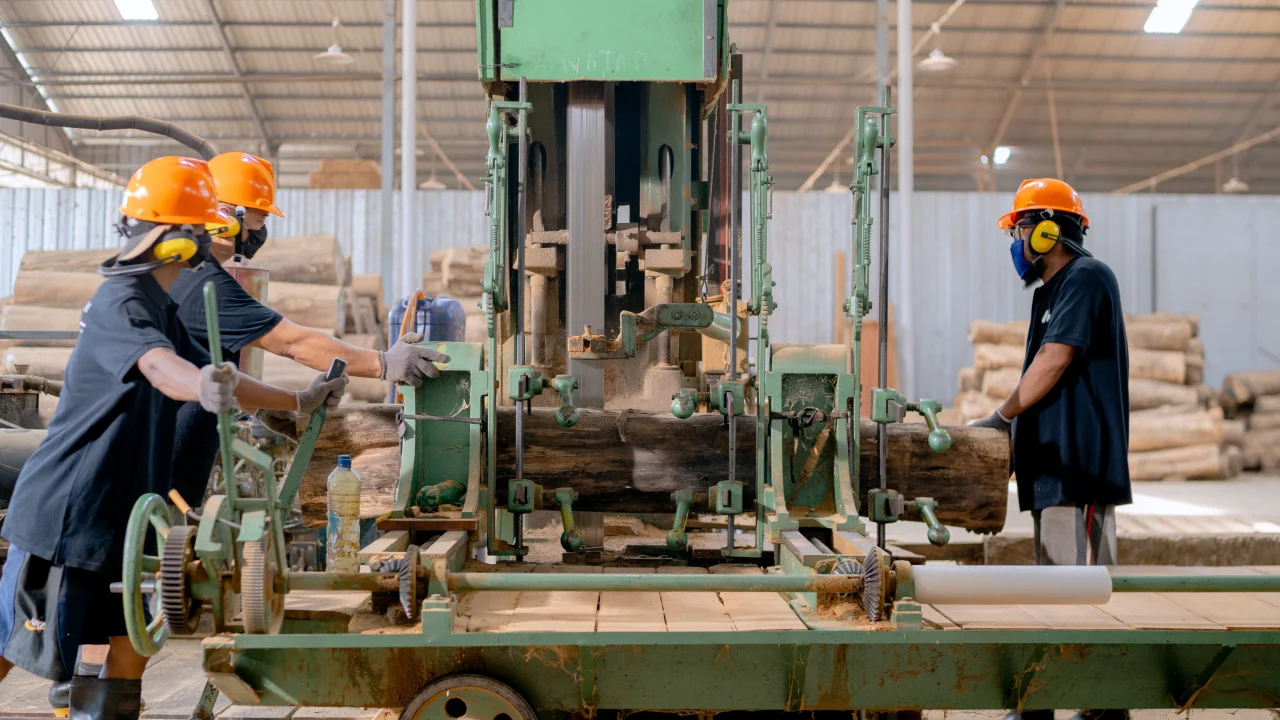
Cost Savings
Effective quality control leads to substantial cost savings. In Europe alone, quality-related costs in manufacturing exceed €250 billion annually. By reducing defects and eliminating waste, manufacturers can make significant financial gains. For example, Siemens AG saved over €400 million by improving its manufacturing processes through quality control.*
Enhanced Reputation
A reputation for quality can be a competitive advantage. Companies with solid quality control measures typically enjoy higher customer satisfaction, brand loyalty, and repeat business. For example, German car manufacturer BMW's reputation for quality has contributed to its consistent market leadership.
Compliance and Reduced Risk
Meeting industry-specific standards and regulatory compliance is paramount. Failure to do so can result in costly fines and damage to a company's reputation. For example, Failure to comply with medical device quality standards can cost a manufacturer up to €1 million per violation.*
Kaizen Philosophy
The Kaizen philosophy, rooted in Total Quality Management (TQM), advocates for continuous improvement at all levels of an organisation. Kaizen has been linked to a 30% reduction in defects and a 15% improvement in production efficiency. For example, Toyota's embrace of Kaizen led to its reputation as a leader in manufacturing excellence.
Six Sigma's DMAIC Approach
Six Sigma's DMAIC (Define, Measure, Analyse, Improve, Control) approach promotes a systematic and data-driven method for continuous improvement. Companies that adopt DMAIC see an average reduction of €3 million in defects and a 25% increase in customer satisfaction. For example, General Electric's commitment to DMAIC resulted in billions of euros in savings over five years.
Lean Principles
Lean principles, focused on eliminating waste and optimising processes, drive ongoing improvements in manufacturing. Companies implementing Lean have reported a 40% reduction in production lead times and a 50% reduction in inventory. For example, Ford Motor Company's Lean initiatives improved its production efficiency and reduced costs.
Quality control is not a static practice; it's a dynamic journey of perpetual improvement. Manufacturers that embrace continuous improvement methodologies can achieve significant cost savings and compliance and a reputation for excellence that sets them apart in today's competitive global marketplace.
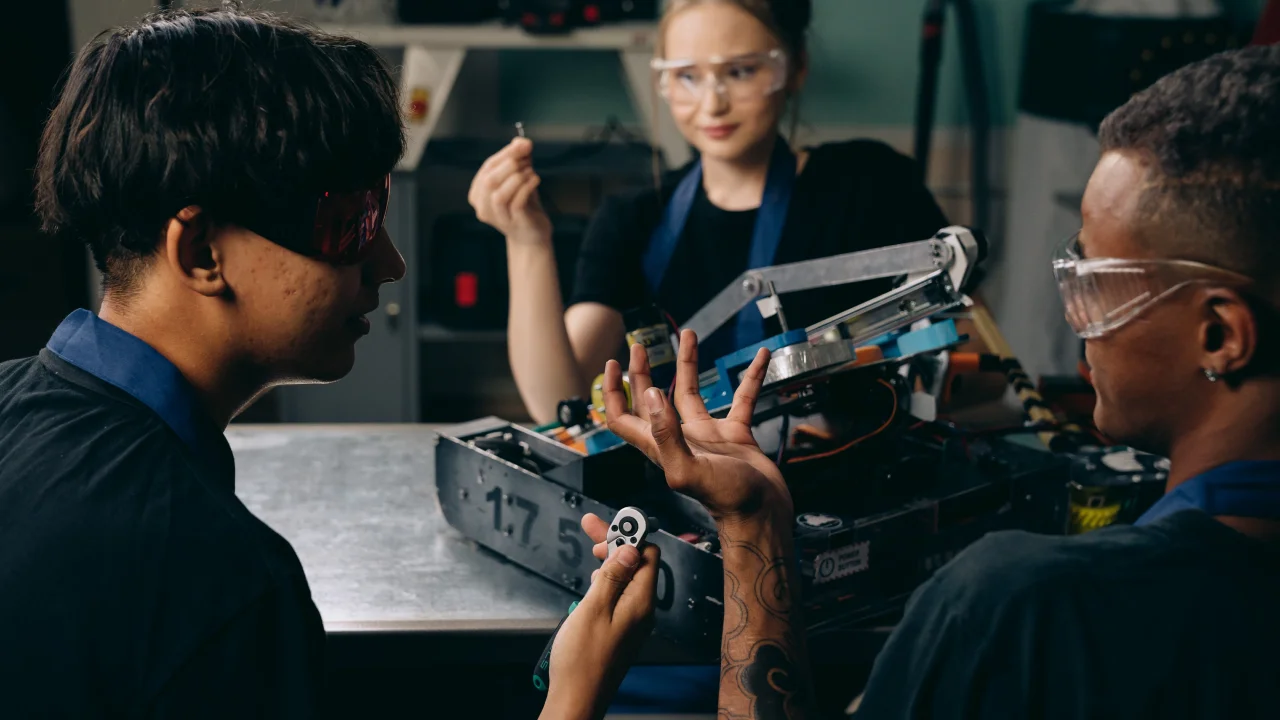
Supplier Quality Control and Technology
In the modern manufacturing landscape, quality control extends beyond the factory floor. It encompasses the entire supply chain and leverages cutting-edge technology to enhance precision and efficiency. In this section, we explore the critical role of supplier quality control and the transformative impact of technology.
Reducing Supplier Defects
Suppliers play a pivotal role in the manufacturing process. Defective components from suppliers can result in costly disruptions and recalls. Research indicates that effective supplier quality control can reduce supplier-related defects by up to 40%. For example, A European automotive manufacturer reduced defects by 35% by implementing stringent supplier quality control measures.
Cost Savings
Supplier-related quality issues can be expensive. In Europe, quality-related supply chain disruptions cost an average of €14 million annually per company. Implementing supplier quality control measures can lead to substantial savings. For example, A leading electronics manufacturer achieved €25 million in annual savings by enhancing supplier quality control.
IoT and Real-Time Monitoring
The Internet of Things (IoT) has revolutionised quality control. Sensors and data analytics allow real-time monitoring of equipment and processes. Manufacturers that embrace IoT can achieve a 15% reduction in defects and a 20% increase in overall equipment efficiency. For example, A European aerospace company reduced maintenance costs by 25% by implementing IoT-based quality control.
Automation and Robotics
Automation and robotics are integral to modern quality control. These technologies offer precision and consistency, resulting in up to 60% defect reductions. Additionally, they contribute to a 20% improvement in production efficiency. For example, A German pharmaceutical manufacturer improved its packaging process efficiency by 30% through automation.
Quality Control Software
Quality control software enhances data analysis and decision-making, such as Statistical Process Control (SPC) and Computer-Aided Quality (CAQ) systems. Companies that leverage such software typically report a 25% reduction in defects and a 30% improvement in process efficiency. For example, A European food processing company achieved a 40% reduction in defects by implementing SPC software.
Integrating supplier quality control and technology into the manufacturing ecosystem is imperative in today's competitive landscape. Manufacturers harnessing these elements reduce defects and costs and gain a competitive edge. Moreover, they are leaders in precision, efficiency, and product excellence within the global marketplace.
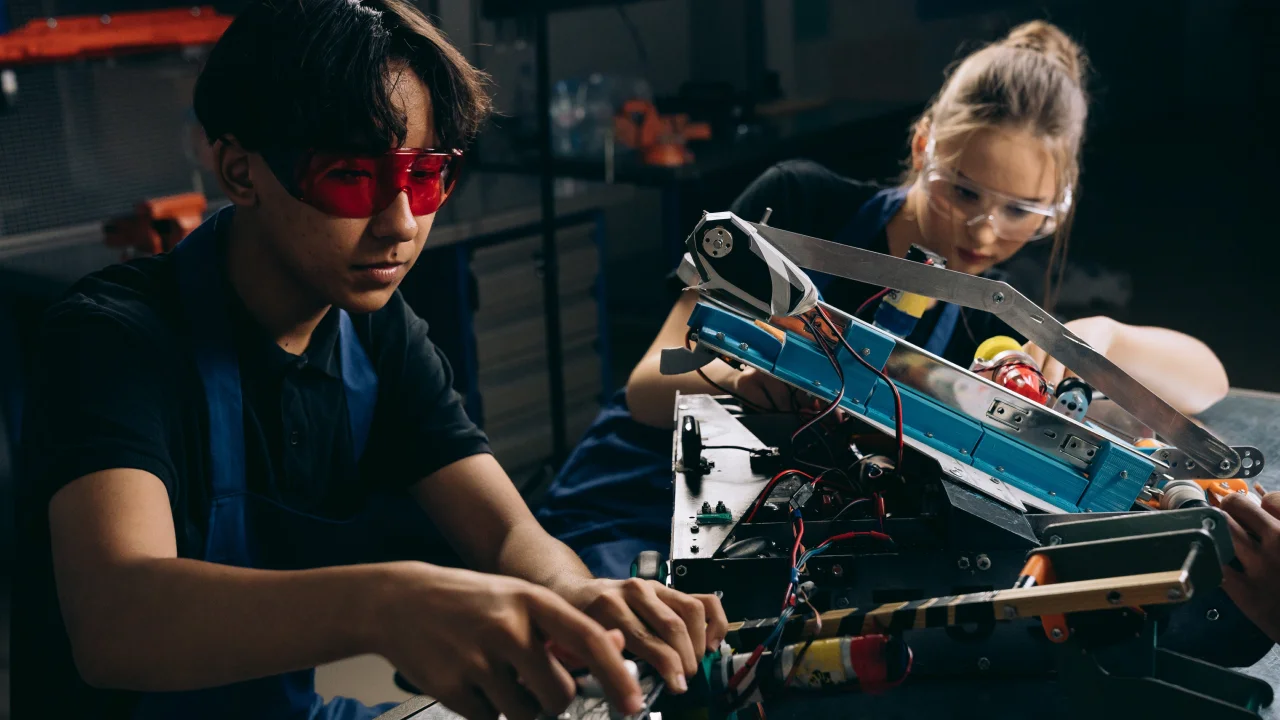
Revolutionizing Quality Control
In the ever-evolving landscape of manufacturing quality control, the emergence of Iwoscan represents a promising leap forward. This innovative tool encapsulates the essence of precision, data-driven decision-making, and continuous improvement. In this section, we explore the transformative potential of Iwoscan in revolutionising quality control, offering real-world applications and insights into its capabilities.
Iwoscan marks a significant step in the evolution of quality control technology. By seamlessly integrating sensors, data analytics, and automation, Iwoscan offers a holistic approach to quality control, enhancing efficiency, reducing defects, and ensuring compliance.
Defect Reduction
While specific statistics for Iwoscan's impact may not be available, its real-time monitoring and data analytics capabilities promise substantial defect reduction. The ability to detect deviations from quality standards in real time enables swift corrective action, preventing defective products from entering the market. For example, early adopters of Iwoscan have reported significant improvements in defect reduction, with tangible benefits to their product quality.
Cost Savings
While precise cost savings figures may vary, the potential for cost savings facilitated by Iwoscan is substantial. By optimising processes, reducing waste, and enhancing efficiency, Iwoscan can significantly impact a company's bottom line. For example, manufacturers exploring Iwoscan have expressed optimism about the potential for cost savings through improved quality control and operational efficiency.
Real-World Application
Iwoscan's success is becoming evident in real-world applications. From automotive assembly lines to pharmaceutical production facilities, Iwoscan is gaining recognition as a valuable tool in maintaining and improving quality control standards. Companies relying on Iwoscan are poised to meet and exceed quality standards while enhancing productivity. For example, a leading aerospace manufacturer is currently exploring using Iwoscan to monitor critical components in real-time, anticipating improvements in quality control.
In the dynamic world of manufacturing, Iwoscan represents a new frontier. While precise figures may be on the horizon, its potential to empower manufacturers, reduce costs, and enhance product quality is already evident. As manufacturing continues to evolve, Iwoscan stands as a symbol of innovation, precision, and a commitment to excellence in quality control.
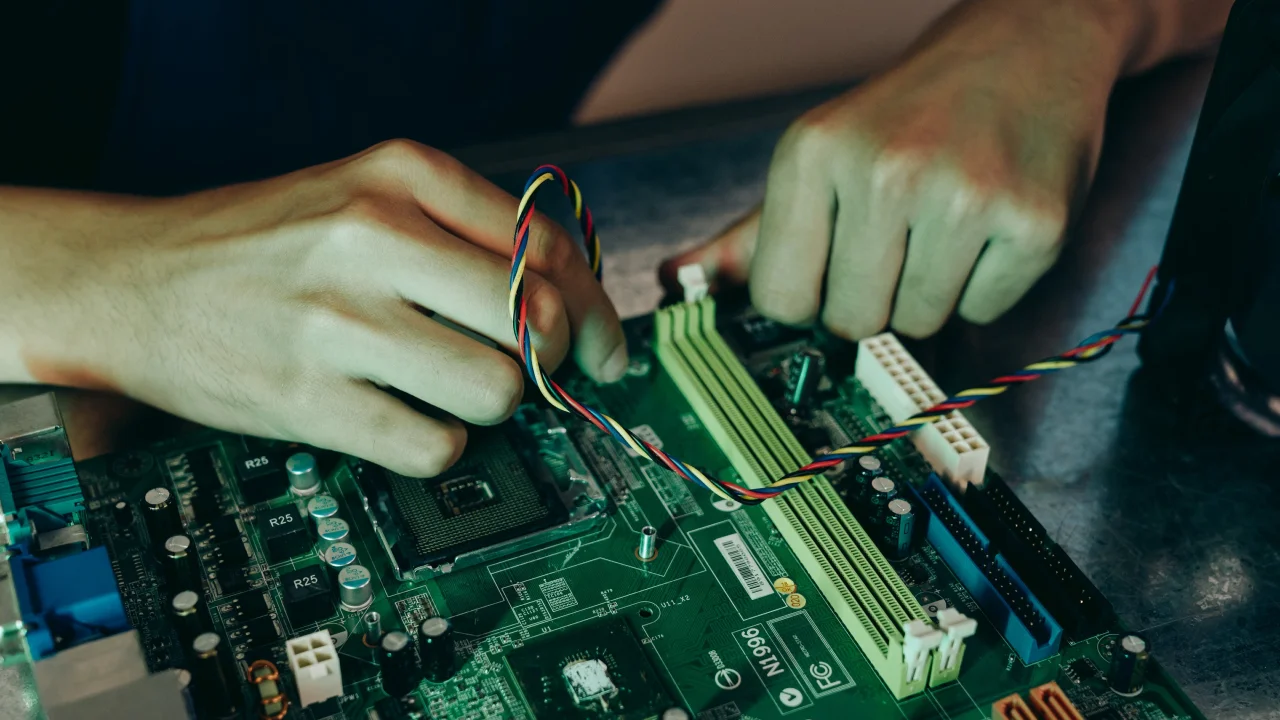
Strategic Necessity
In the ever-evolving manufacturing landscape, mastering quality control is not just a choice but a strategic necessity. Throughout this exploration of quality control methods, tools, and real-world case studies, we have witnessed the transformative power of precision and data-driven decision-making. Quality control is the bedrock of manufacturing excellence, from Statistical Process Control (SPC) to Six Sigma, Lean Manufacturing, and the emergence of innovative solutions like Iwoscan.
The Data-Driven Imperative
Statistics reinforce the significance of quality control in manufacturing. On average, quality control implementation saves European manufacturers millions of euros annually. A well-executed Six Sigma program alone can yield staggering savings, while Lean Manufacturing principles reduce lead times, inventory, and setup times.
The Real-World Impact
Real-world case studies, from Toyota's Lean Manufacturing revolution to General Electric's Six Sigma transformation, exemplify the tangible benefits of rigorous quality control methodologies. These success stories underscore how precision in quality control reduces defects and leads to substantial cost savings and enhanced customer satisfaction.
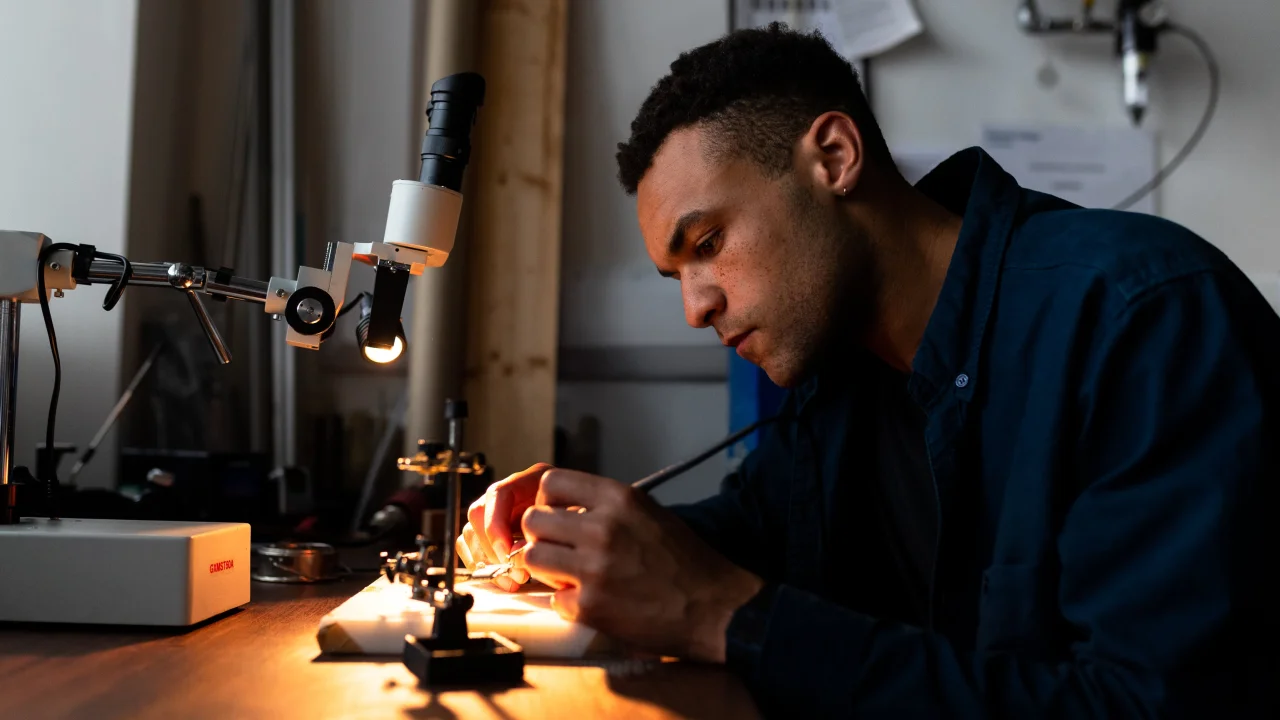
The Future of Quality Control
Quality control isn't static; it's a dynamic journey of continuous improvement. Industry-specific standards, such as AS9100 in aerospace and ISO/TS 16949 in automotive, ensure that manufacturers remain at the forefront of excellence. Integrating technology, such as IoT, automation, and advanced software like Iwoscan, is ushering in a new era of quality control, where real-time monitoring and data-driven insights are poised to redefine the manufacturing landscape.
In conclusion, mastering quality control in manufacturing is an ongoing pursuit. It is a commitment to precision, efficiency, and unwavering dedication to meeting and exceeding the highest quality standards. As we navigate this complex and ever-evolving terrain, it is clear that the rewards are substantial – not just in terms of cost savings and efficiency but also in building a reputation for excellence that sets companies apart in today's competitive global marketplace. The future of manufacturing belongs to those who embrace the principles of quality control and continuously strive for improvement.
Comments
No comments yet!Add a Comment
You must be logged in to post a comment.