In the bustling world of manufacturing, where every second counts and precision is paramount, industrial assembly lines stand as the beating heart of production. The rhythmic hum of machinery, the orchestrated movement of components, and the synchronised efforts of skilled workers all contribute to the creation of products that shape our daily lives. However, as we navigate the complexities of modern production, the call for innovation becomes ever more urgent.
Intelligent automation – a revolutionary approach to industrial assembly that blends cutting-edge technologies to elevate efficiency and redefine the possibilities of manufacturing. From the early days of manual labour to the present era of sophisticated machinery, the evolution of industrial automation has been both remarkable and essential. As we delve into the transformative power of intelligent automation, we will unravel the challenges faced by traditional assembly lines, understand the core technologies driving this revolution, and witness the tangible benefits that businesses can reap by embracing these advancements.
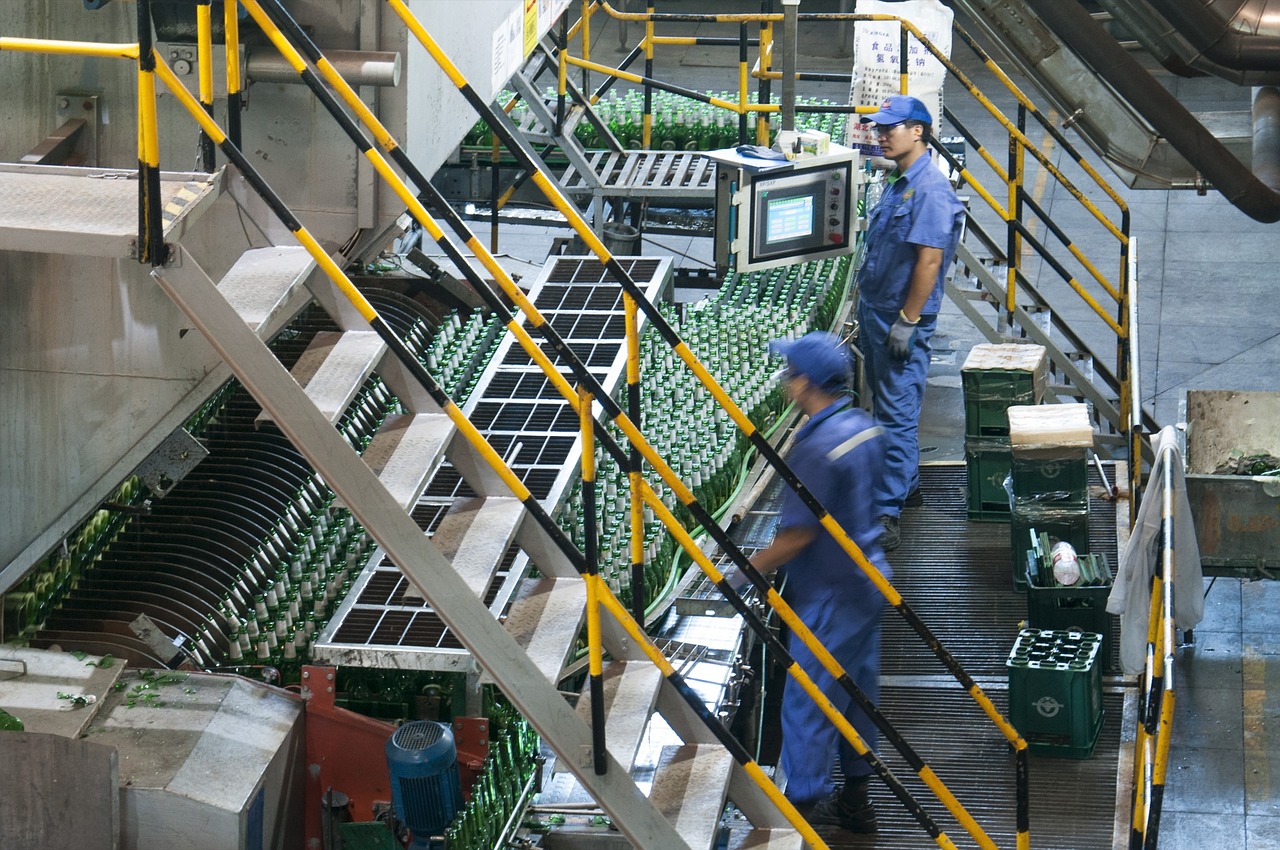
Evolution of Industrial Automation
When factories were just getting started, people did everything with their hands and basic tools. Imagine a world where every product you use, from cars to gadgets, is put together by skilled workers manually. This was the era before automation when everything depended on human effort and time.
As time rolled on, people began to realise that they could make things faster and more precisely if they introduced machines into the process. This marked the early stages of industrial automation. Simple machines like conveyor belts and steam-powered engines were introduced to assist workers, making the production process smoother and more efficient.
Then came the era of electrification, bringing with it a wave of more advanced machines. Factories started using electricity to power their machines, which allowed for even greater speed and precision in manufacturing. This shift laid the groundwork for the automation we see today.
As technology continued to advance, the mid-20th century witnessed the rise of computerisation. Computers began to control and monitor various aspects of manufacturing processes. This was a significant leap forward, as it allowed for more complex tasks to be automated with a higher degree of accuracy.
Fast forward to the present day, and we find ourselves in the age of smart manufacturing. Industrial automation has evolved to incorporate robotics, artificial intelligence, and sophisticated sensors. This means that machines not only perform repetitive tasks but can also make decisions based on data and learn from experience.
The evolution of industrial automation has been like a journey from manual craftsmanship to a highly intelligent and interconnected system. Today, it's not just about making things faster; it's about making them smarter. In the next sections, we'll explore how these advancements are transforming assembly line tasks, making them more efficient, accurate, and adaptable to the ever-changing demands of the manufacturing world.
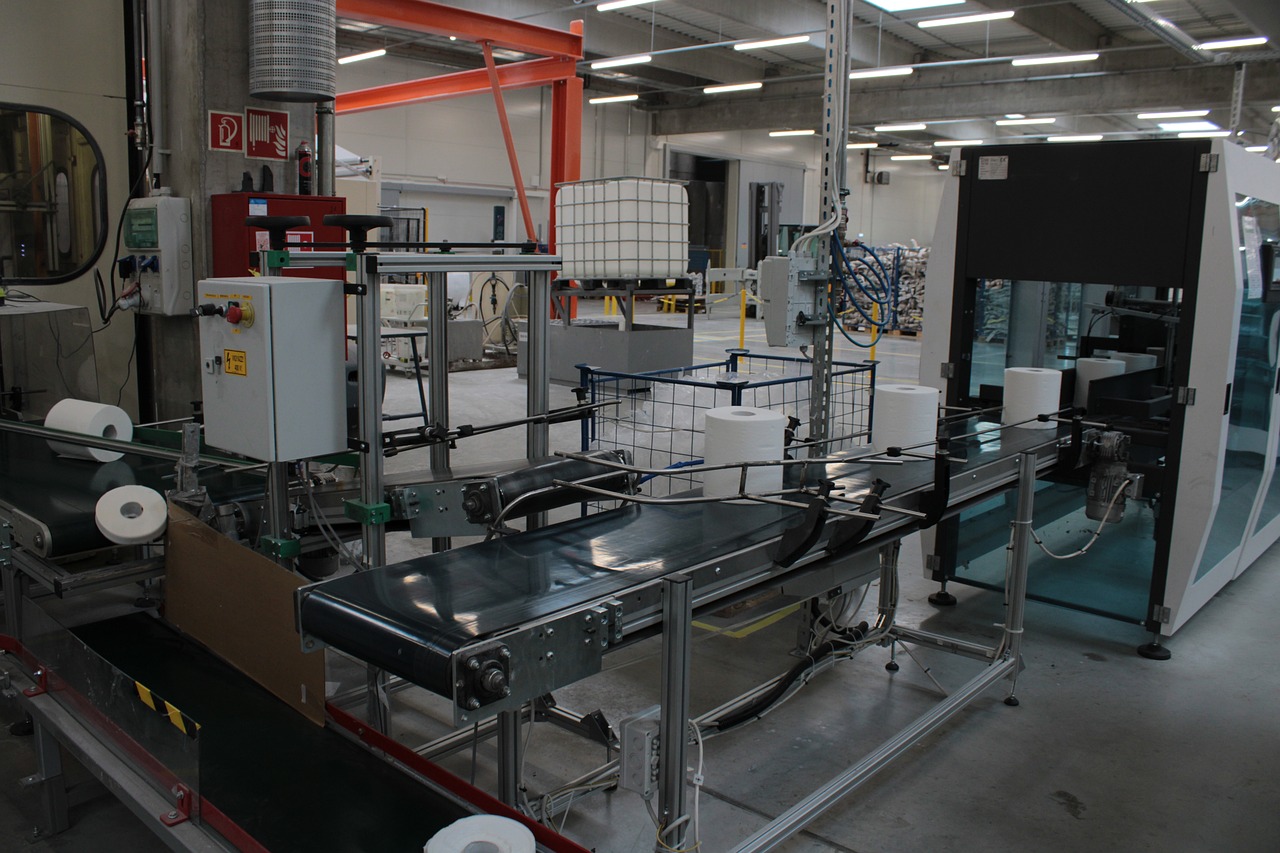
Challenges in Traditional Assembly Lines
Traditional assembly lines presented some significant challenges in the old days of manufacturing when everything was done by hand. Let's examine these challenges that prompted the need for change.
Manual Labor Limitations
In the early days, assembly lines heavily relied on human hands to put together products. While skilled workers were crucial, they also faced limitations in terms of speed and endurance. Human hands, no matter how experienced, have their pace, and this poses a challenge when trying to meet the growing demand for products.
Error Rates and Quality Control
With manual labour, the chances of errors were higher. Humans, being human, could make mistakes – a misalignment here, a missed screw there. Ensuring consistent quality across products became a daunting task. Maintaining high-quality standards was a constant struggle, leading to potential defects and rework.
Production Delays
Imagine a scenario where every step of the manufacturing process depended on the completion of the previous one. If one worker fell behind, the entire assembly line would slow down, causing delays in production schedules. This interconnectedness meant that any hiccup in the workflow could have a ripple effect on manufacturing as the whole timeline.
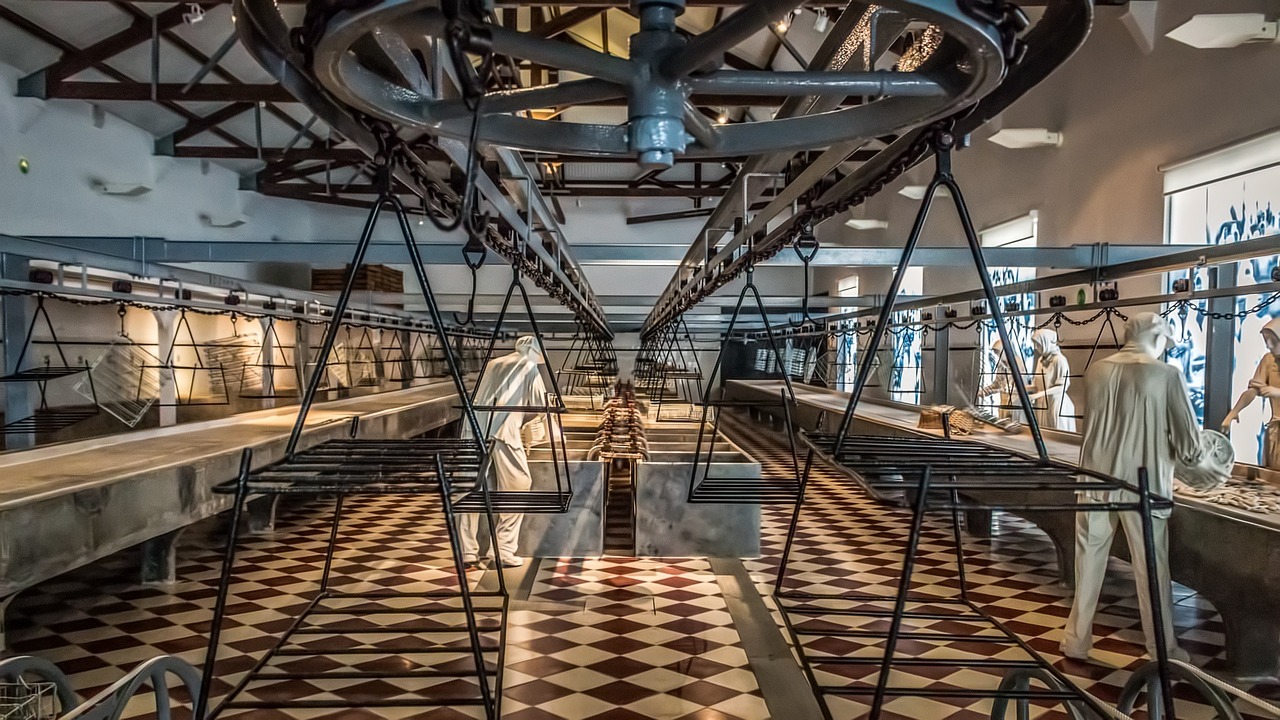
Workplace Safety Concerns
Traditional assembly lines often involved manual handling of heavy materials and repetitive tasks, putting workers at risk of injuries. Ensuring a safe working environment was challenging, and accidents could lead to not only human suffering but also disruptions in production.
Inflexibility to Change
Traditional assembly lines were designed for specific tasks, and any changes in the manufacturing process required significant adjustments. Adapting to new products or incorporating changes in design became a time-consuming and resource-intensive endeavour.
Understanding these challenges is crucial because they paved the way for the transformation we see today. The shortcomings of traditional assembly lines acted as a catalyst for the adoption of intelligent automation, aiming to address these issues and bring about a new era of efficiency and reliability in manufacturing. In the following sections, we'll explore how intelligent automation tackles these challenges head-on, ushering in a more dynamic and responsive approach to industrial assembly.
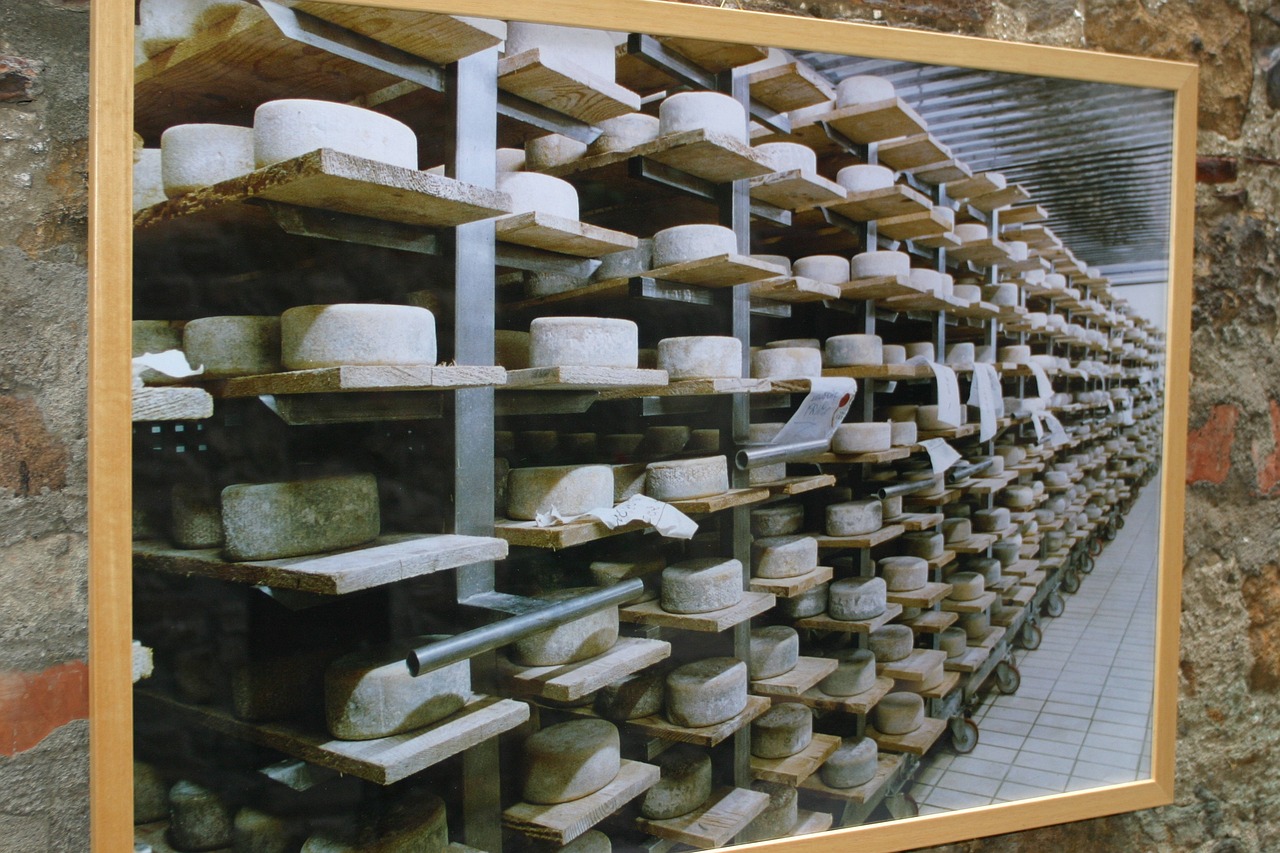
Intelligent Automation Technologies
Now that we've explored the challenges of traditional assembly lines, let's explore the exciting world of intelligent automation technologies—the game-changers that have revolutionised how things are made.
Robotics and Cobots
Picture machines that can work tirelessly, with precision, strength, and speed. That's what robotics brought to the table. Robots and their friendly counterparts, known as cobots (collaborative robots), are like the superheroes of the manufacturing world. They handle the heavy lifting and repetitive tasks, allowing human workers to focus on more complex and creative aspects of the job.
Artificial Intelligence (AI) and Machine Learning (ML)
Enter the brainy side of automation. AI and ML bring a touch of intelligence to machines. They can learn from experience, make decisions, and adapt to changes in real time. In the context of industrial assembly, AI and ML are like having a smart assistant that not only follows instructions but also learns from each task, becoming better and more efficient over time.
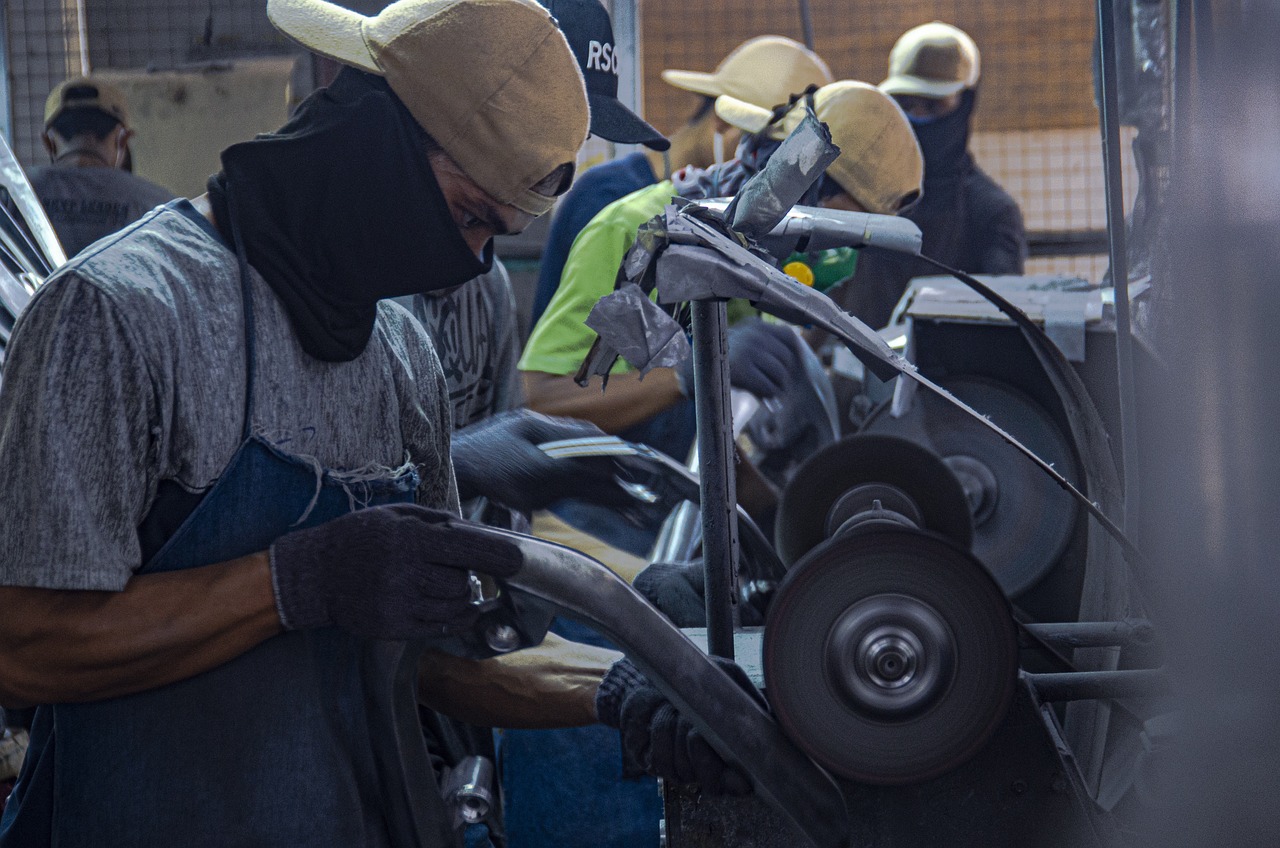
Internet of Things (IoT)
Imagine a world where machines talk to each other, sharing information and making decisions together. That's the essence of IoT. In industrial assembly, IoT allows different devices and machines to communicate seamlessly. Sensors collect data, and this information is used to optimise processes, predict maintenance needs, and ensure everything runs smoothly.
Advanced Sensors
Sensors are like the senses of intelligent automation. They can "see" and "feel" the environment, detecting changes and ensuring accuracy in tasks. From detecting the exact position of a component to identifying potential issues, sensors play a crucial role in enhancing the precision and reliability of assembly line tasks.
Computer Vision
Just like human eyes, computer vision allows machines to "see" and interpret visual information. This technology is used for tasks like quality control, where machines can inspect products for defects with a level of detail and speed that surpasses human capabilities.
These technologies work together in harmony, creating a symphony of efficiency on the assembly line. Picture robots collaborating with human workers, guided by smart algorithms, and constantly communicating through IoT. It's like a well-choreographed dance where every move is calculated, ensuring that each product meets the highest standards.
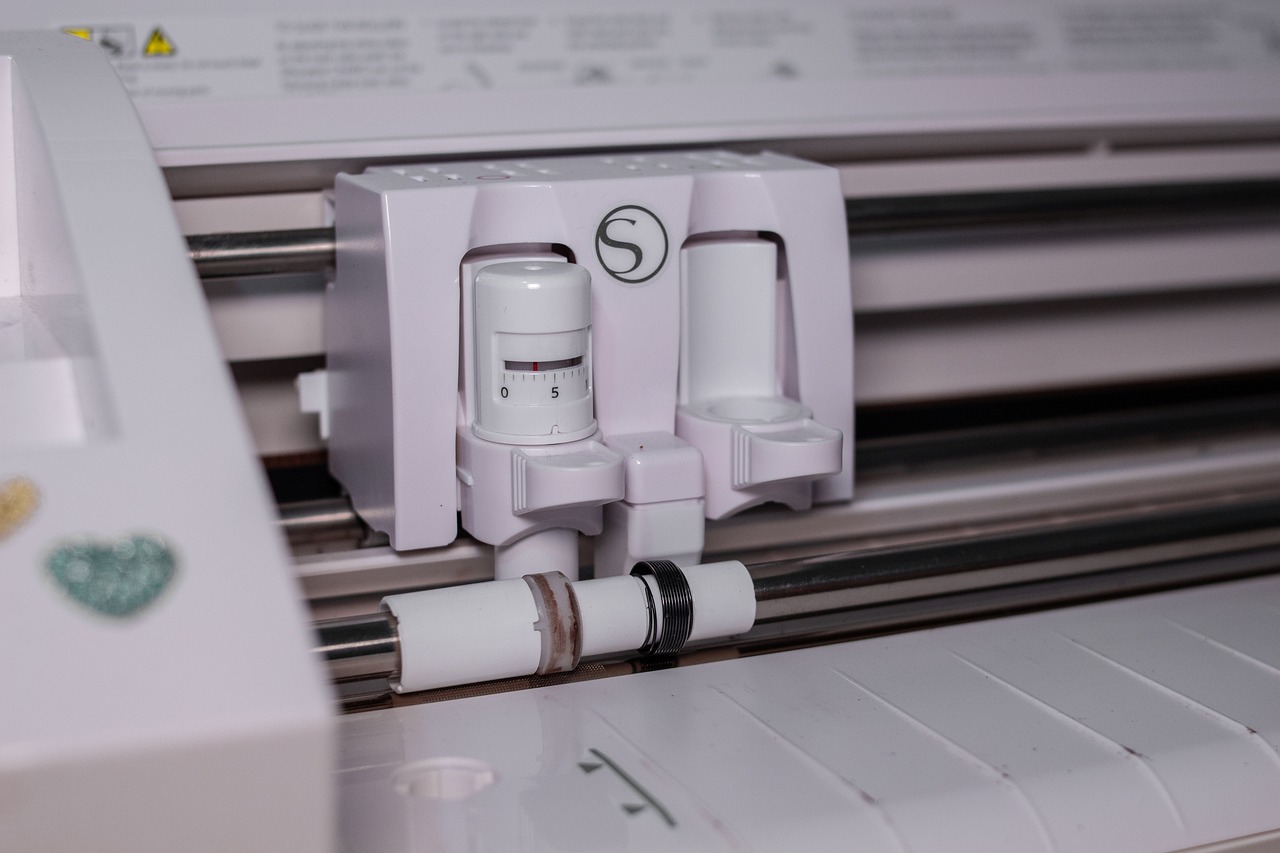
Benefits of Intelligent Automation in Assembly Lines
Now that we've introduced the superheroes of manufacturing – the intelligent automation technologies – let's uncover the incredible benefits they bring to the assembly line.
Increased Efficiency and Speed
Imagine a production line where tasks are performed at lightning speed, without breaks or fatigue. That's the magic of intelligent automation. Robots and machines work tirelessly, significantly reducing the time it takes to assemble products. This increased speed not only meets growing demand but also allows for quicker delivery of goods to customers.
Reduction in Errors and Defects
One of the most remarkable feats of intelligent automation is its precision. Machines equipped with advanced sensors and computer vision can perform tasks with incredible accuracy, minimising the chances of errors. This results in a significant reduction in defects and ensures that each product meets the highest quality standards.
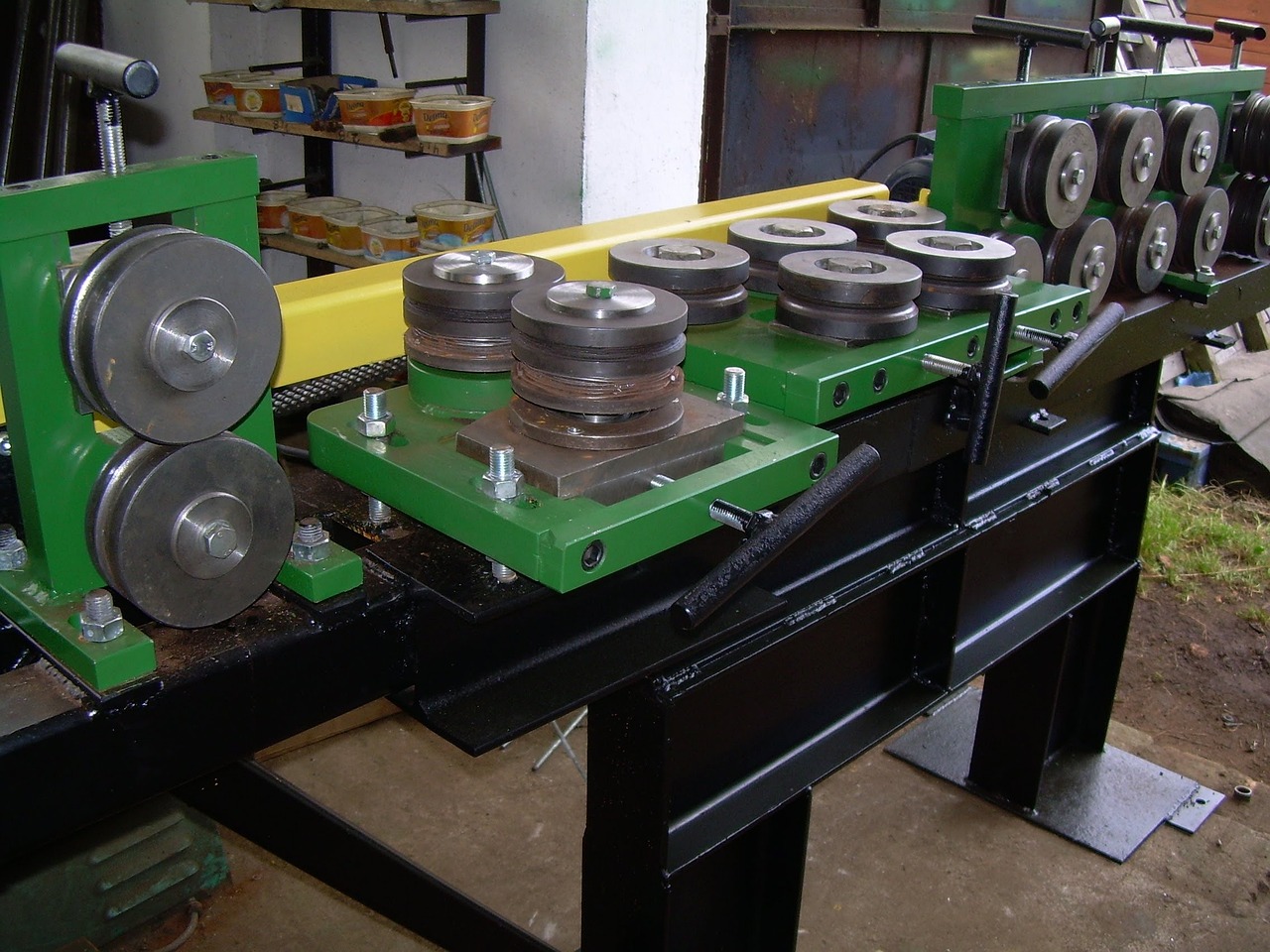
Enhanced Safety Measures for Workers
With robots and cobots handling heavy and repetitive tasks, human workers can focus on tasks that require creativity, problem-solving, and decision-making. This shift reduces the risk of injuries and creates a safer working environment. Intelligent automation contributes to both the physical and mental well-being of the workforce.
Optimised Resource Utilization
Automation isn't just about speed; it's also about using resources wisely. Intelligent automation technologies optimise the use of materials and energy, contributing to cost savings. This efficiency ensures that resources are utilised to their maximum potential, minimising waste and environmental impact.
Cost Savings
While the initial investment in intelligent automation technologies may seem significant, the long-term benefits translate into substantial cost savings. Increased efficiency, reduced errors, and optimised resource utilisation all contribute to a more cost-effective manufacturing process. Over time, businesses find that the return on investment outweighs the initial costs.
These benefits are not just theoretical; they have real-world implications for businesses. Assembly lines equipped with intelligent automation become powerhouses of productivity, capable of producing high-quality products at a scale and speed that was once unimaginable.
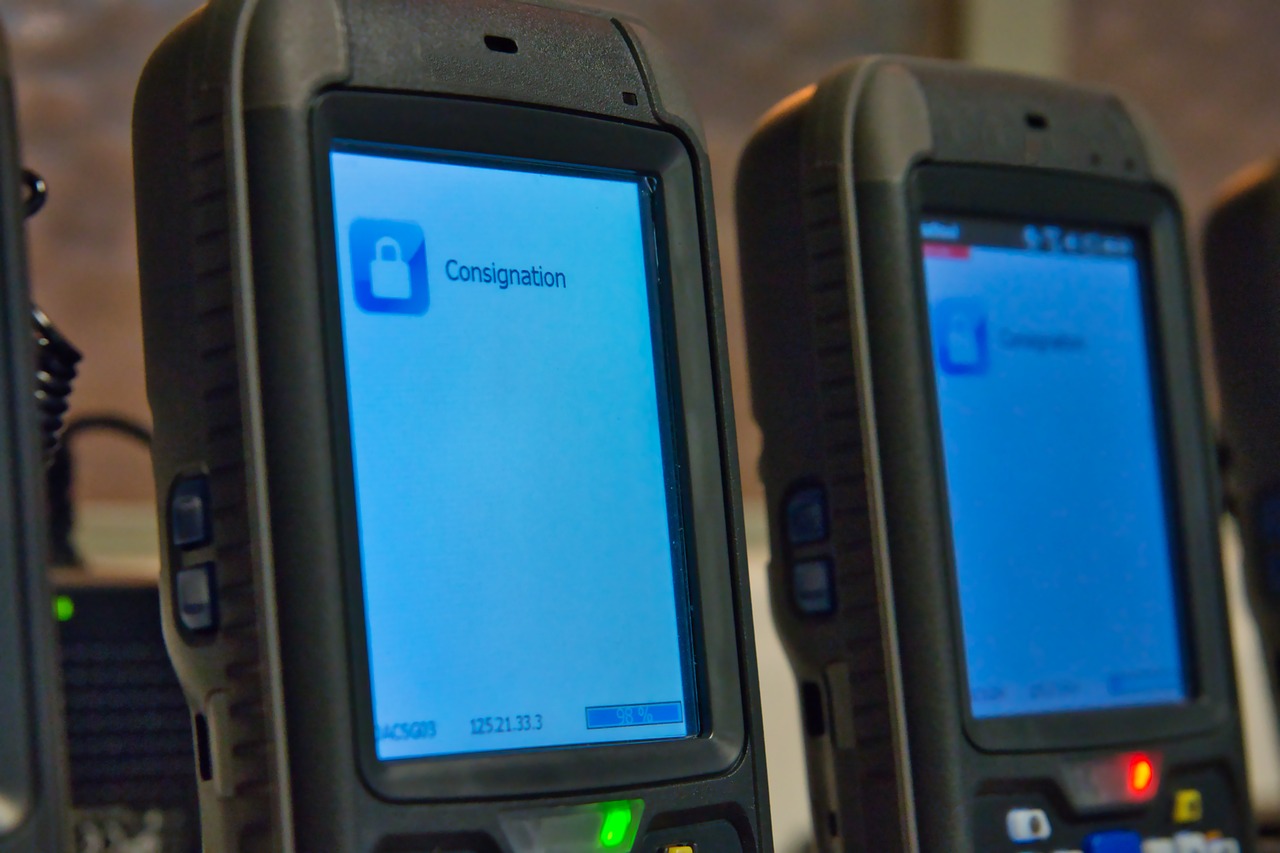
Implementation Strategies
Now that we understand the incredible benefits of intelligent automation, the next step is figuring out how to bring these technologies into our assembly lines. Here's a practical guide on how businesses can implement intelligent automation effectively.
Assessment of Current Processes
Start by taking a close look at your existing assembly processes. Identify the tasks that are repetitive, time-consuming, or prone to errors. Understanding your current workflow is crucial for pinpointing areas where intelligent automation can make the most impact.
Set Clear Objectives
Define your goals for implementing automation. Whether it's increasing production speed, reducing errors, or improving worker safety, having clear objectives will guide your automation strategy. This clarity ensures that the implemented technologies align with your business priorities.
Selecting the Right Technologies
Not all assembly line tasks require the same type of automation. Choose technologies that fit your specific needs. If precision and speed are crucial, robotics and computer vision might be the answer. If you aim to optimise resource utilisation, IoT and advanced sensors could be the key.
Employee Training and Upskilling
Transitioning to intelligent automation involves collaboration between machines and humans. Provide training programs to familiarise your workforce with the new technologies. This isn't about replacing workers but empowering them to work effectively alongside intelligence.
Phased Implementation
Implementing automation doesn't have to happen overnight. Consider a phased approach where you gradually introduce intelligent technologies to different parts of the assembly line. This allows for smoother integration and gives your team time to adapt to the changes.
Data Security and Privacy
With intelligent automation's increased connectivity, it's crucial to prioritise data security and privacy. Implement robust cybersecurity measures to protect sensitive information. This ensures the smooth and secure operation of automated systems.
Continuous Monitoring and Improvement
Automation is not a one-time fix; it's an ongoing process. Implement systems for continuous monitoring and gather feedback from both machines and workers. Use this data to identify areas for improvement and fine-tune your automation strategy accordingly.
Collaboration with Automation Experts
Seek guidance from experts in the field of intelligent automation. Collaborating with automation specialists and consulting with technology providers can provide valuable insights and ensure your implementation aligns with industry best practices.
Remember, the key to successful implementation is a thoughtful and strategic approach. By carefully assessing your needs, setting clear goals, and involving your workforce in the process, you can unlock the full potential of intelligent automation on your assembly line.
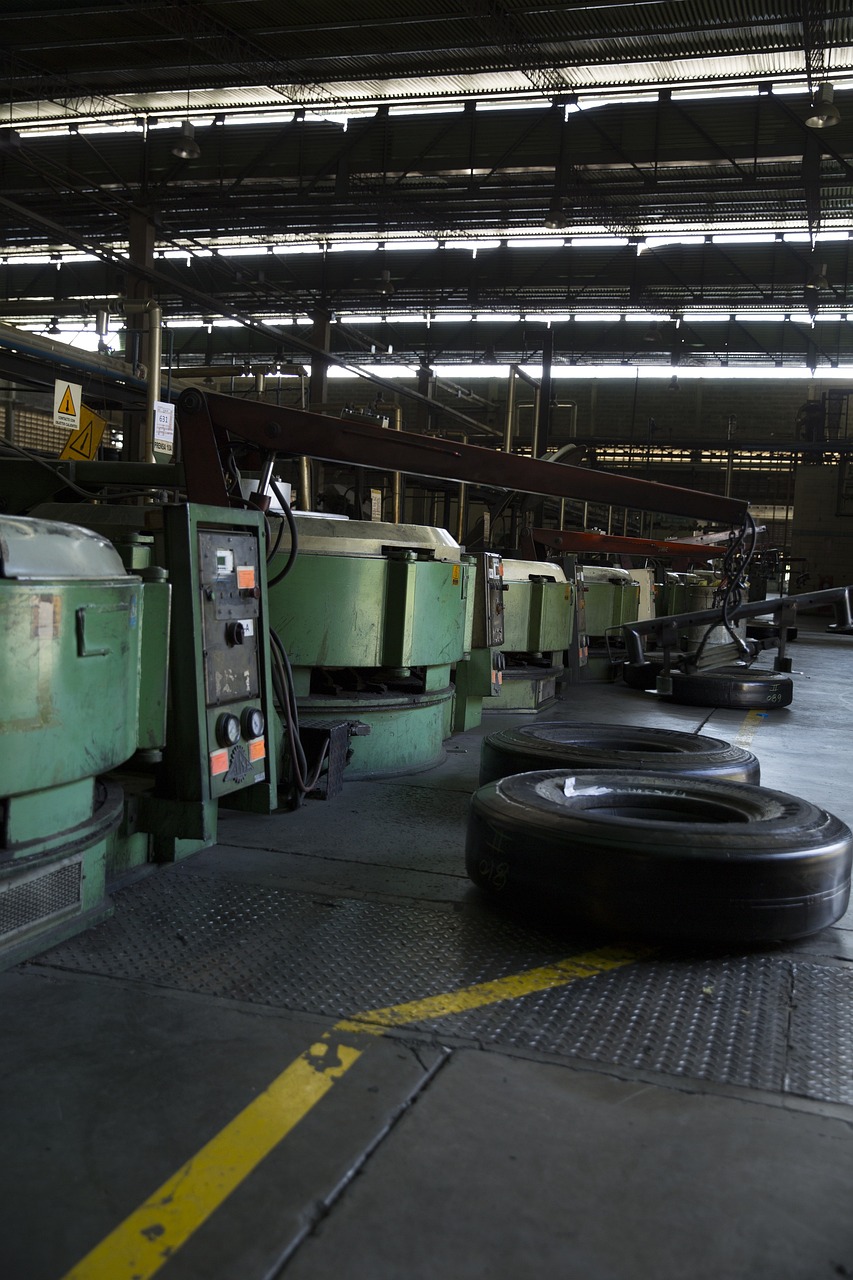
Future Trends in Intelligent Automation
As we journey further into the world of intelligent automation, it's essential to peek into the future and explore the exciting trends that are set to shape the landscape of manufacturing. Here are some glimpses of what's on the horizon:
Integration of 5G Technology
Imagine a world where machines communicate with each other at lightning speed. With the integration of 5G technology, intelligent automation connectivity will reach new heights. This means faster data transfer, real-time decision-making, and an even more seamless collaboration between devices.
AI-driven Predictive Maintenance
Predictive maintenance takes a proactive approach to equipment upkeep. Artificial Intelligence will play a significant role in predicting when machines might need maintenance, preventing unexpected breakdowns and ensuring that the assembly line runs smoothly without interruptions.
Expansion of Edge Computing
Edge computing brings processing power closer to where data is generated. This trend is set to expand in the world of intelligent automation, allowing for faster decision-making without relying heavily on centralised servers. This is particularly crucial in scenarios where split-second decisions are critical.
Customisation at Scale
The future of manufacturing is not just about mass production; it's about personalised and customised products. Intelligent automation will enable businesses to tailor products to individual preferences at scale, offering a level of customisation that was once considered impractical.
Human-Robot Collaboration Enhancements
Collaborative robots, or cobots, will become even more sophisticated in their ability to work alongside human counterparts. Future trends include enhanced safety features, more intuitive interfaces, and improved adaptability to different tasks. This ensures a harmonious collaboration between humans and machines on the assembly line.
Eco-friendly Manufacturing Practices
Sustainability will be a driving force in the future of manufacturing. Intelligent automation will contribute to eco-friendly practices by optimising resource utilisation, reducing waste, and incorporating energy-efficient technologies. This shift aligns with the growing global focus on environmentally conscious production.
Blockchain for Enhanced Security
As data reliance continues to grow, ensuring its security and integrity becomes paramount. Blockchain technology is expected to enhance the security of transactions and data exchanges within the intelligent automation ecosystem, providing a transparent and secure framework.
Augmented Reality (AR) in Training and Maintenance
Imagine technicians wearing AR glasses that guide them through complex maintenance procedures or workers receiving real-time training through augmented reality interfaces. AR is poised to become a valuable tool for training, maintenance, and troubleshooting in the intelligent automation realm.
These trends showcase the continuous evolution of intelligent automation, promising not just increased efficiency but a transformation in how products are manufactured and customised. By staying attuned to these trends, businesses can position themselves at the forefront of innovation, ensuring their assembly lines remain adaptive and competitive in the ever-evolving landscape.
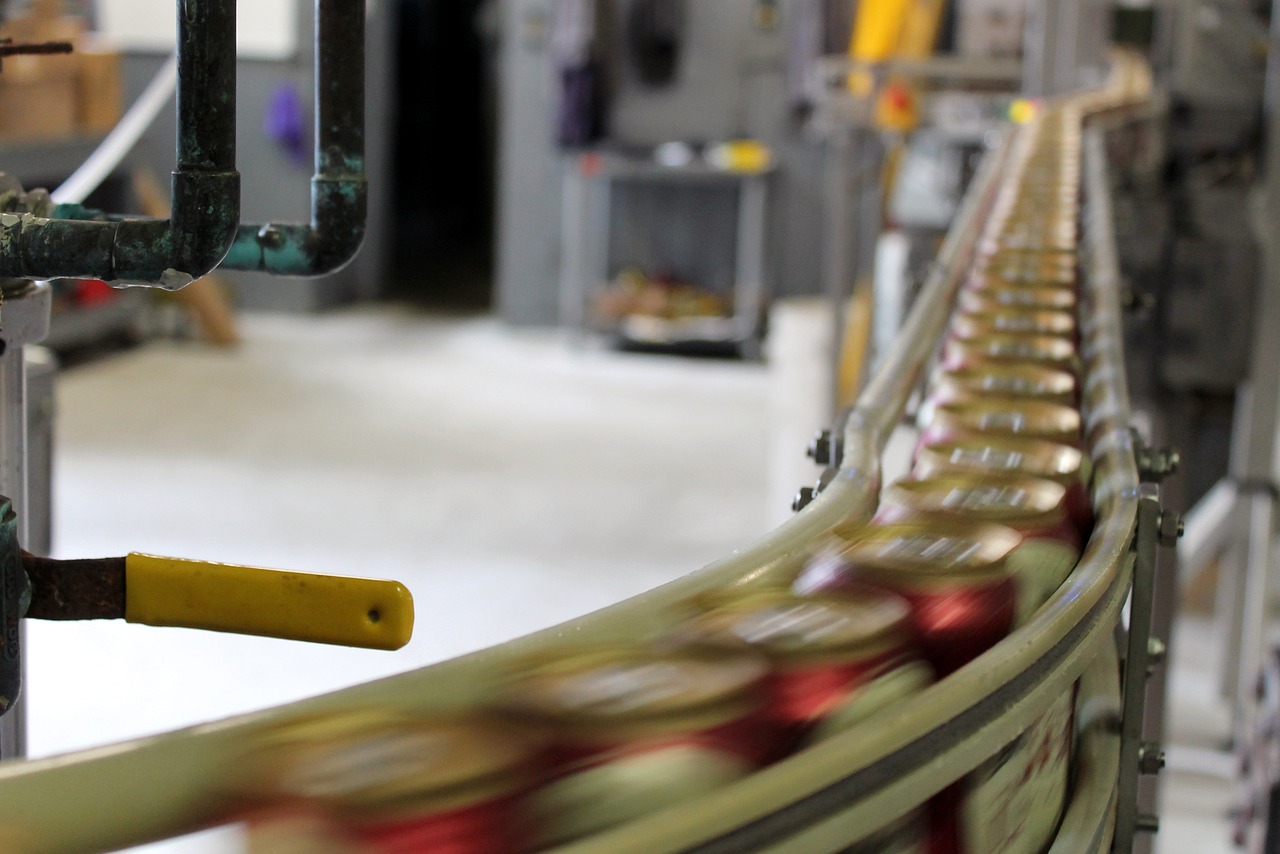
Embracing the Future of Manufacturing with Intelligent Automation
In our exploration of intelligent automation for industrial assembly lines, we've uncovered a transformative journey from the early days of manual labour to the sophisticated technologies shaping the present and future of manufacturing. The challenges of traditional assembly lines, including manual limitations, errors, and production delays, have paved the way for the superheroes of modern production: robotics, artificial intelligence, and the interconnected world of the Internet of Things.
The benefits of embracing intelligent automation are clear and impactful. Increased efficiency, a reduction in errors, enhanced worker safety, optimised resource utilisation, and substantial cost savings paint a picture of a manufacturing landscape that is not just productive but also adaptive and resilient.
Implementing intelligent automation requires a strategic approach – assessing current processes, setting clear objectives, selecting the right technologies, and prioritising employee training. It's a collaborative effort that involves the synergy of human intelligence and machine capabilities.
As we gaze into the future, exciting trends await. The integration of 5G technology, AI-driven predictive maintenance, and the expansion of edge computing promise even faster, smarter, and more efficient manufacturing processes. Customisation at scale enhanced human-robot collaboration, and a commitment to eco-friendly practices underscore a future where manufacturing is not just about quantity but also about quality, personalisation, and sustainability.
In conclusion, the journey towards intelligent automation is not just a technological shift; it's a fundamental evolution in how we create the products that shape our lives. By staying informed, adopting best practices, and embracing the ongoing innovations in the field, businesses can position themselves at the forefront of this revolution, ensuring their assembly lines are not just efficient but future-ready. The future of manufacturing is here, and it's intelligent, adaptive, and full of endless possibilities.
Comments
No comments yet!Add a Comment
You must be logged in to post a comment.