Iwoweight is an integral component of a standard quality control system, guaranteeing that every product emerging from a manual production line meets permissible weight criteria and aligns with EOL (End-of-line) test criteria. A weight outside the permissible limits during the EOL experience means the product was not manufactured correctly. This solution is pivotal in enabling manufacturers to deliver top-tier products, avoid human error, reduce fail rate, and measure performance in the production process. The repercussions of selling products with inaccurate weights (EOL are significant in manufacturing – underweight items may lead to fines or penalties, while overweight products result in costly giveaways. Iwoweight emerges as a versatile tool applicable across various industries, functioning as a potent quality assurance system.
Amidst the dynamic environment of the contemporary manufacturing sector, characterised by intense competition, prioritising quality assurance is crucial to meet evolving customer demands and align with local and global standards. Significantly, addressing the imperative to minimise or eradicate human errors from the production process is paramount. Iwoweight proves instrumental in compliance with regulations, fostering increased productivity through waste reduction, tighter tolerances, and improved product consistency. The cumulative effect is heightened efficiency, bolstered profitability and reduced rate of errors for companies implementing Iwoweight. Improve your manufacturing standards with Iwoweight and witness a transformative impact on your bottom line.
Quality Assurance and Monitoring Solution for Manual Weighing
In our era of technological marvels, it's crucial to acknowledge that automated production lines come with a hefty price tag, making them impractical and out of reach for many businesses. Investing in large machines might not be a logical or viable option for smaller manufacturers. However, the industry's demand for reliable quality assurance and monitoring tools persists. This is where Iwoweight emerges as a cost-effective and budget-friendly QA solution tailored for businesses of all sizes.
Implementing Iwoweight on a manual production line is typically driven by a blend of application requirements, specific processes, financial considerations, and the imperative of brand protection. By choosing Iwoweight, businesses ensure quality and strategically invest in their operations, aligning with their needs and the market dynamics.
Unveiling the essence of Iwoweight
In the pursuit of precision in manual weighing and packaging processes, Iwoweight emerges as an indispensable solution, revolutionising the reliability of production insights. Its innovative approach involves using a control signal to authenticate primary signals and establishing a fail-safe mechanism that guarantees the accuracy of OEE data. Iwoweight is an operator-friendly hardware tool tailored for manual packaging and quality control procedures, encompassing meticulous weight monitoring, customised sticker printing, and real-time work hour tracking.
Seamlessly interfacing with scales, Iwoweight diligently monitors EOL product weights, ensuring requirements and swiftly identifying deviations. Beyond weight monitoring, it also allows printing customised stickers and tracking real-time work hours. Iwoweight emerges as the preferred solution for minimising packaging errors, achieving cost savings, and facilitating precise task management. It offers invaluable insights into the intricacies of your business processes.
Hardware and software components
Iwoweight solution is a combination of tools:
- Industrial Counter
- Any weight range weighing scales
- Rack
- Label Printer
- BAR/QR code scanner
Retrieve and monitor real-time data from all production equipment and workspaces seamlessly, eliminating the need for additional input from line operators. This feature saves time, avoids distracting operators, and provides all the essential data to effectively address issues within a production line.
Versatile applications of Iwoweight
In the realm of overall quality control tools, Iwoweight is a steadfast assurance for manufacturers, ensuring compliance with regulations and precise product quantities. This instils confidence in manufacturers and guarantees consumers that they obtain high-quality products with all specified ingredients or parts labelled.
Iwoweight finds diverse applications in the manufacturing industry, addressing key concerns such as checking for under or overweight packages, ensuring adherence to net contents laws, and verifying the completeness of package components. From confirming the accuracy of package mixes to minimising product giveaways through precise filler adjustments, Iwoweight plays a pivotal role in enhancing efficiency and reducing waste.
Its applications include classifying products into weight zones, ensuring compliance with various standards, and facilitating pure 'net weighing' through tare/gross systems. Additionally, Iwoweight proves instrumental in measuring and reporting production line efficiency, meeting reporting standards set by regulatory bodies like USDA, FDA, OIML, FPVO, and others. Iwoweight emerges as a multifaceted tool, empowering manufacturers to uphold the highest quality and operational efficiency standards.
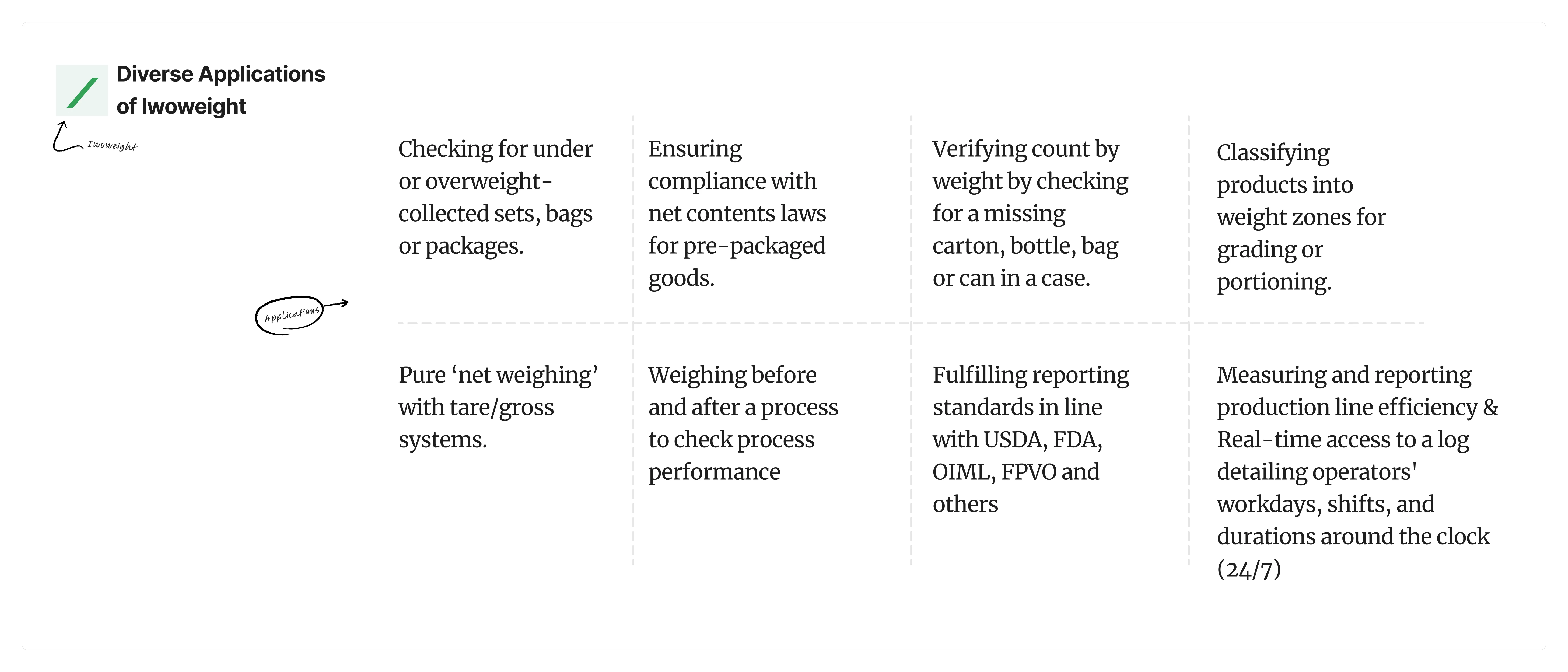
Iwoweight emerges as a dynamic solution, meticulously overseeing the weight of items during manual weighing in the production line. It goes beyond mere monitoring, employing a sophisticated system to classify objects into preset weight zones and sorting or rejecting them based on these classifications. The true power of Iwoweight lies in its ability to weigh 100% of the items on a production line, offering an unparalleled 100% overview of essential production data. This includes production counts, batch tracking, total weights, good weights, and rejected weights.
This tool is suitable for various industrial applications, mainly where cost-effective weight measurements are imperative with minimal engineering overhead. The brilliance of Iwoweight shines through when additional automated logging functions are required within the measurement framework.
Which industry stands to gain the most from Iwoweight?
Iwoweight finds its stride in diverse sectors and fields of application, serving as an ideal solution for industries ranging from Bakery and Cereal to Meat and fish, Cheese and Dairy, Fresh Produce, Frozen Produce, Snacks, Ready Meals, Pasta, Confectionery, Nuts & Dried Fruit, Granulated, Chemical, Hardware, Pharmaceutical, and even Pet & Animal Food. Assemble sets, single packages, or bags from diverse elements, including furniture assembly components, plumbing parts, and other items.
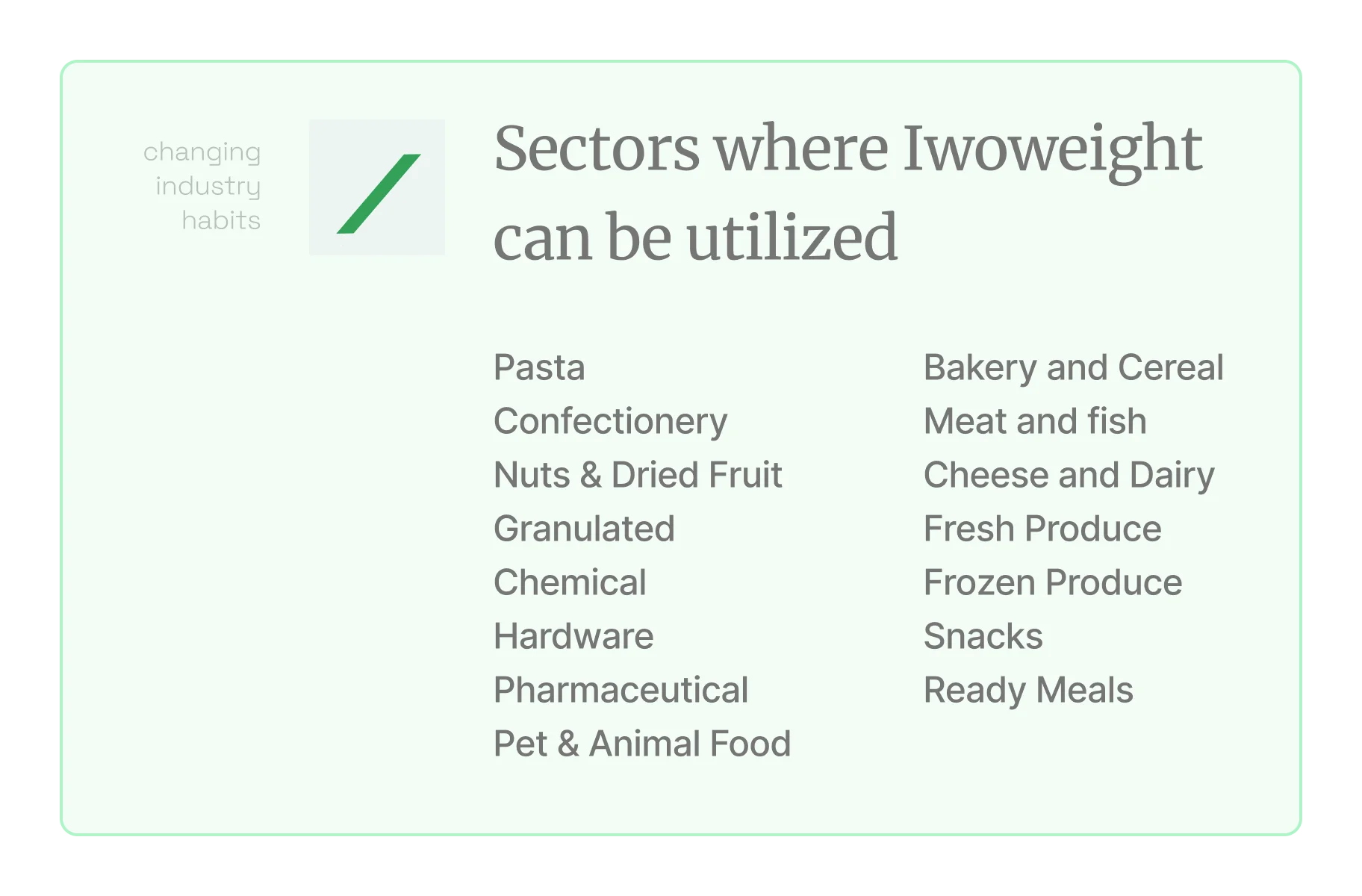
It's not just a weight monitoring system; it's a transformative force in ensuring precision, efficiency, and quality across an extensive array of manufacturing domains. Additionally, it can monitor and track workspace activities, generating labels with customised details such as operator name, date, time, company logo, and more.
What kind of items do Iwoweight typically monitor?
An Iwoweight can monitor the weighing process of almost any production line item. These can range in weight from below one gram to several hundred kilogrammes. Typical examples of check-weighed items include:
- Raw or unwrapped food products before packaging
- Pre-packed food products such as cans, glasses, wrapped products and trays
- Boxes, cartons or tubs of products (weighed to determine if papers, components, instructions or other items are missing)
- Weight-based counting of contents of bottles, bags, and packaged parts, such as cases of batteries, nappies, or drink bottles in a case
- Weighing items of different weights for future reference or billing (such as a warehouse or delivery service)
- Blister packs of products, such as tablets and capsules
- Verifying the weight of leased equipment upon its return
Insights, advantages, and benefits of Iwoweight
A key motivator behind adopting Iwoweight is aligning with government regulations and industry standards. Integrating additional weight inspection becomes a cornerstone within a comprehensive quality and process control program. Notably, the deployment of Iwoweight brings a transformative shift by automating the collection of information that was previously done manually, accomplishing the task in a fraction of the time.
In the manufacturing and packaging landscape, Iwoweight autonomously monitors the weight of every package on the line. This real-time vigilance allows immediate responses to detected issues, contributing to compliance and heightened efficiency in the production process. The result is a seamlessly integrated solution that meets regulatory requirements and optimises the manufacturing workflow for enhanced quality control and productivity.
Safeguarding customer and consumer interests
A critical facet of customer and end-consumer satisfaction hinges on manufacturers maintaining unwavering product quality. This involves mitigating the risk of producing underfilled items or supplying incomplete components. These objectives are necessary for relationships between retailers, customers, and manufacturers and open the door to potential business opportunities slipping away.
Navigating the global manufacturing landscape adds another layer of complexity, given the varying net content laws and regulations across different countries. The widely accepted OIML22 R87 standard by the International Organisation of Legal Metrology (OIML) is a benchmark for many European nations. This standard meticulously outlines acceptable deficiencies in the actual content of pre-packaged products. Meanwhile, on the local front, Weights and Measures authorities enforce specific net content laws tailored to each country.
The repercussions of non-compliance are multifaceted, ranging from spoken recommendations and warnings to legal action. Manufacturers must meet and exceed these standards to foster lasting customer relationships and avoid potential setbacks in the competitive marketplace.
Preserving brand integrity and reputation
The potency of positive product branding extends beyond a mere promise – it provides a robust assurance of safety and quality for customers. Effective branding is crucial in encouraging repeat purchases, boosting sales, and justifying premium pricing for manufacturers and retailers within the complex manufacturing environment. This includes cost reduction by preventing refunds or after-sale services and minimising post-expenditures. It is a dynamic tool extending beyond transactions, shaping perceptions, and influencing consumer choices.
A company's responsibility, however, transcends the end consumer; it extends to safeguarding the very essence of the brand and the company's reputation. Product brands are not just labels but pivotal assets demanding careful management and protection from adverse publicity. The repercussions of underweight products reaching consumers can inflict significant harm, tarnishing the organisation's brand and triggering potentially costly recalls.
In the face of customer complaints leading to investigations, robust documentation becomes a shield, providing invaluable evidence of the Iwoweight solution's correct operation. This solution, offering real-time monitoring of production processes, yield statistics, and statistical process control (SPC) trends, becomes a cornerstone for compliance, continuous improvement, and operational efficiencies. In essence, it's not just about protecting products; it's about safeguarding the very identity and prosperity of the company itself.
Optimising utilisation of finite resources
In the dynamic world of manufacturing, the accuracy of Iwoweight is not just a measure; it's a catalyst for achieving tighter production tolerances. This translates into less waste and the ability to produce more final products using the same inventory. Integrating Iwoweight becomes a cornerstone in a comprehensive program to maximise existing resources in a landscape where raw materials come with a hefty price tag. It's not just about minimising waste; it's about unlocking the full potential of every raw material and optimising the production process for enhanced efficiency and resource utilisation.
Ensure operators stay aligned with live Iwoweight feedback
Investing in Iwoweight goes beyond precision; it's about providing operators with dynamic feedback that transforms their performance. The system actively monitors operator actions, ensuring optimal performance while minimising the risks of overfills and underfills. Beyond manual packaging scenarios, Iwoweight seamlessly integrates into existing factory floor automation systems, fostering direct communication. The result is a comprehensive feedback control mechanism that ensures precision and enhances the overall operational efficiency of the manufacturing process.
Reduced false rejects, minimised rework, and decreased scrap
Incorporating a precise and well-maintained Iwoweight into your processes ensures accuracy and results in fewer products ending up in the reject bins. The implementation of tighter tolerances elevates the overall quality of the manufacturing process, effectively reducing the quantity of scrapped products and minimising the need for time-consuming rework. The meticulous refinement of zone settings further reduces false rejects, showcasing the precision of Iwoweight accuracies. It's not just about minimising waste; it's about optimising processes for heightened efficiency and quality control.
Efficient workforce operation
While spot-checking products with static scales is common, adopting in-line Iwoweight introduces a transformative shift. This eradicates potential weighing errors and significantly slashes excessive labour costs associated with static scale spot-checking. Imagine a seamless process where precision is paramount, errors are minimised, and labour-intensive tasks become a thing of the past – that's the power of in-line Iwoweight in redefining efficiency in manufacturing operations.
Enhanced overall equipment efficiency
Boosting Overall Equipment Effectiveness (OEE) hinges on refining the three key metrics: availability, performance, and quality. Achieving 100% monitoring of items through Iwoweight yields valuable insights:
- Availability - identifying process variations is crucial in preventing unexpected downtime events.
- Performance - Unleashing the full potential of your production line involves addressing reduced capacity, often caused by out-of-tune upstream devices.
- Quality - Iwoweight tightens production tolerances, minimising overfills and underfills. The result? A higher yield of satisfactory products pushes the boundaries of quality within your manufacturing processes. It's not just about monitoring; it's about strategically optimising each metric to ensure the holistic efficiency of your equipment.
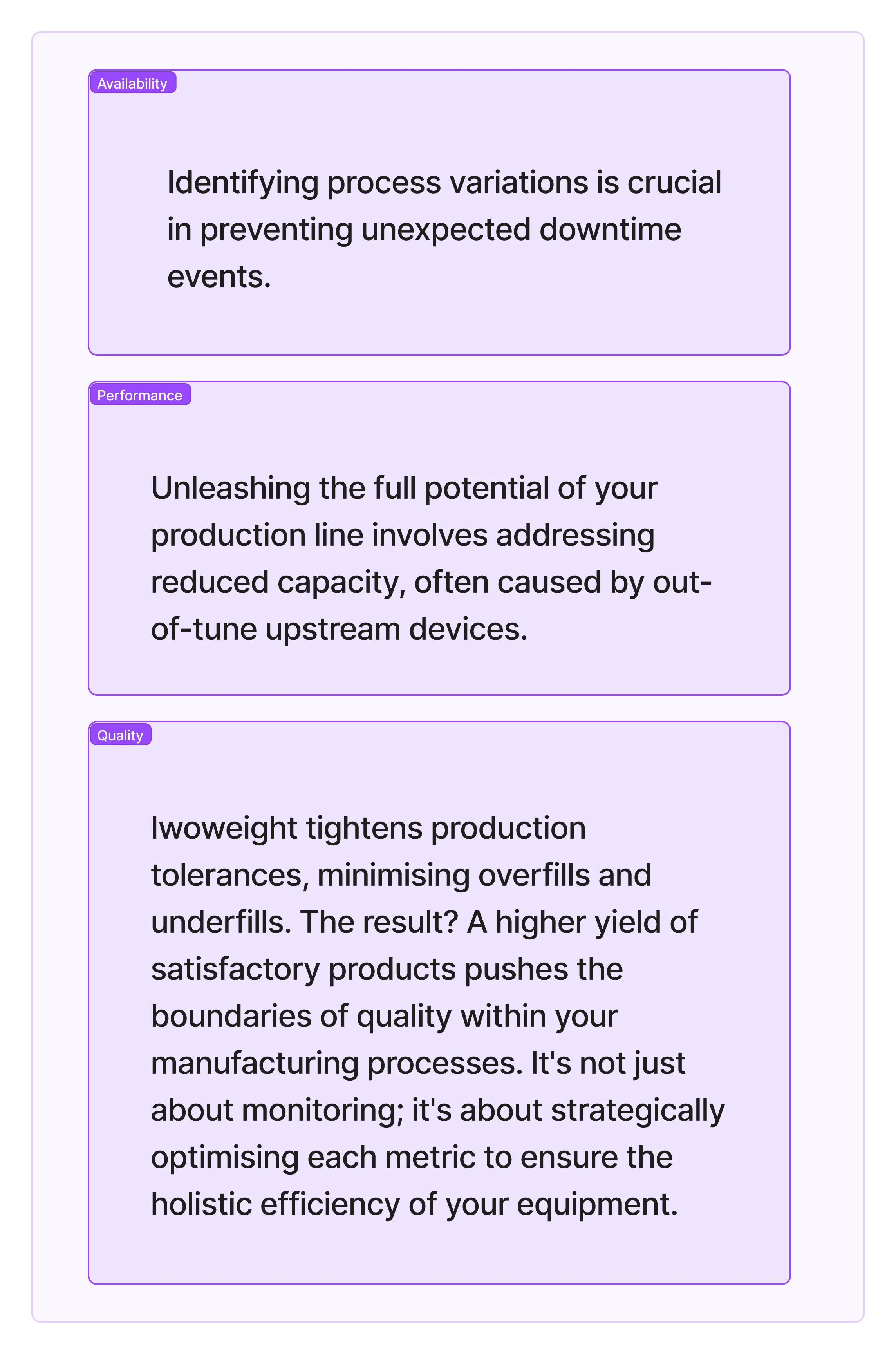
Unlocking comprehensive benefits with Iwoweight integration
Incorporating the Iwoweight weighing monitoring module into manual weighing procedures is an intelligent decision that combines advanced technology with the numerous benefits of the PLC (Programmable Logic Controller) world. This includes expandability, flexibility, software capabilities, user interface features, drives, communication interfaces, and more.
Here's a glimpse of the substantial benefits:
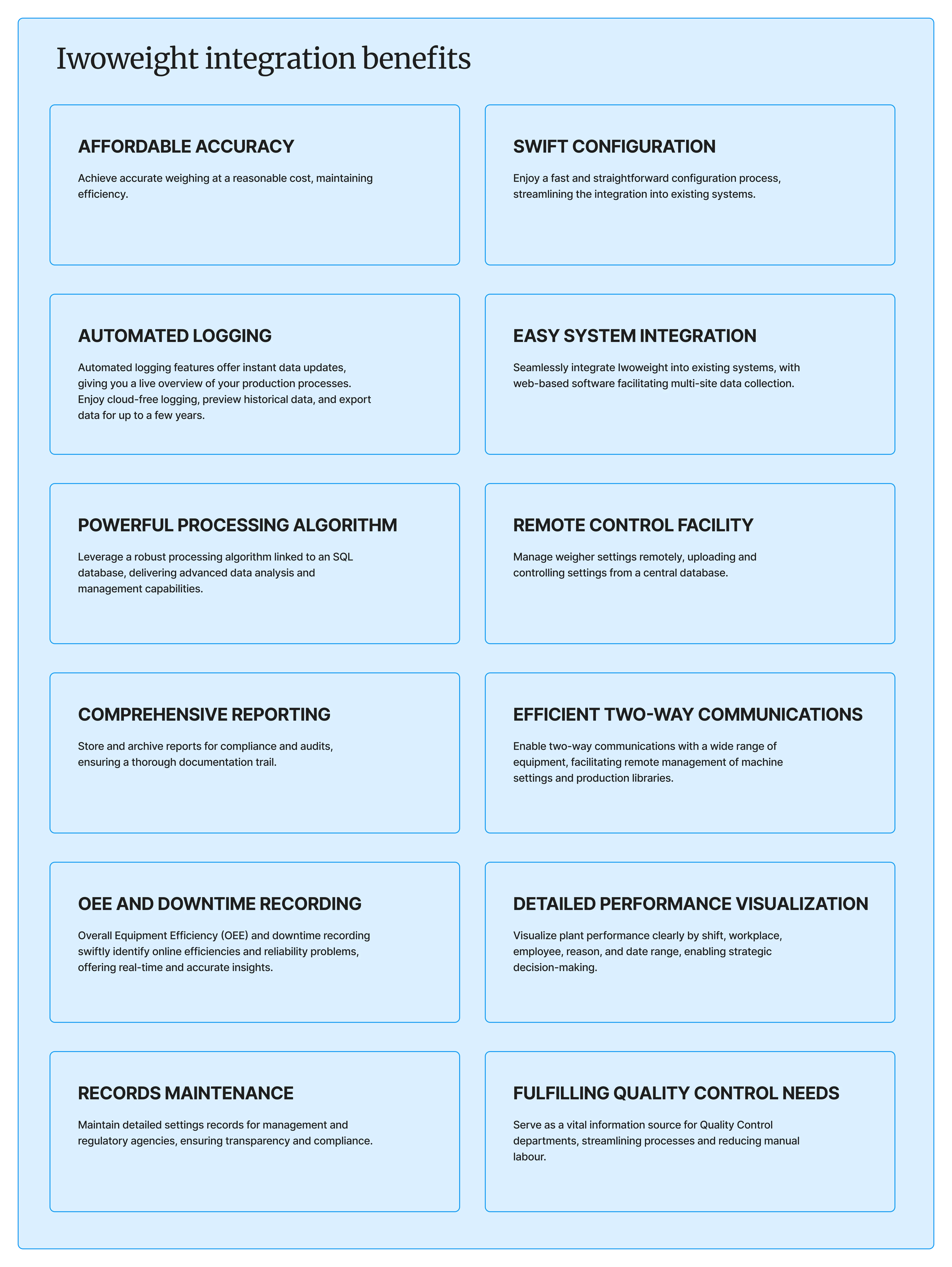
The integration of Iwoweight isn't just about precision; it's a holistic transformation that empowers manufacturing operations with efficiency, control, and adaptability.
Navigating your requirements in the Iwoweight selection
In the realm of Iwoweight systems, a diverse range caters to specific applications, providing solutions tailored to the intricacies of various tasks. On one end, low-cost, swiftly obtainable basic Iwoweights are designed for straightforward assignments. Conversely, highly sophisticated Iwoweight combination systems take charge of critical processes, exerting control over substantial sections of a production line.
Notably, most Iwoweights are bespoke creations configured to align precisely with customers' needs. These systems come equipped with specific mechanical options and software features, ensuring a seamless fit into the existing manufacturing framework. A reliable Iwoweight system supplier plays a pivotal role, offering expertise to assess and provide the optimal solution tailored to individual requirements.
For purchasers navigating the array of options, familiarity with the available choices is critical in determining the ideal Iwoweight configuration to meet their operational needs. When deciding which Iwoweight solution aligns with a particular product and production line, a strategic starting point involves thoroughly examining current processes within the manufacturing operation. Considerations should revolve around product weight, shape, size, production environment, and compliance with legal or brand requirements. It's not just about finding a solution; it's about sculpting a precise and effective tool that harmonises seamlessly with the unique demands of the manufacturing journey.
Iwoweight in action: scenario
Iwoweight, a dedicated hardware tool tailored for manual packaging and quality control, is seamlessly integrated into the operational processes at the manufacturing/packaging facility. It interfaces with scales to constantly track and record real-time package weights, ensuring precision in packaging and swiftly detecting any irregularities.
The Iwoweight system is implemented in a workspace to ensure efficient quality control during filling. The primary goal is to guarantee accurate packaging weights, prevent overfilling, and conduct comprehensive quality assessments.
Integration of Iwoweight into the workspace
The image below illustrates the seamless incorporation of the Iwoweight solution into the workspace, where operators engage with materials to craft specified products and pack them into boxes.
The Iwoweight solution comprises:
- The LightTower, available in Grey, White, Yellow, Blue, and Red, is intricately linked to each machine or workspace, offering a comprehensive view of unfolding activities across the production lines.
- A printer is responsible for generating labels/stickers containing detailed or customised information about the product.
- An industrial rack is designed to hold the tablet securely.
- Industrial tablets that visually present all the pertinent data the operator requires.
- Industrial weights transmit information directly to the tablet.
- This integrated setup ensures a cohesive and efficient workflow, empowering operators with real-time information and control over the packaging and production processes.
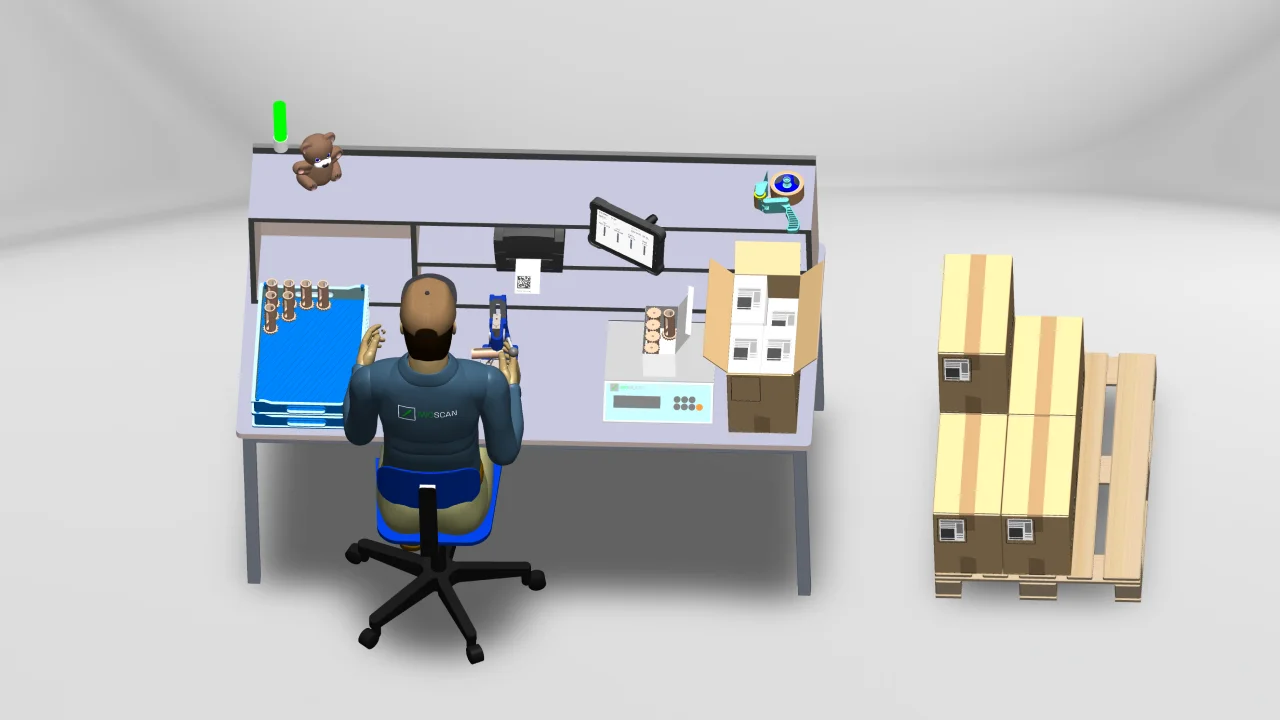
Versatility and flexibility in operation
Upon receiving materials, the Iwoweight tablet promptly displays comprehensive task instructions for the operator. One of the defining features of the system is its innate adaptability, as it seamlessly conducts completeness checks across a wide spectrum of products. What sets the Iwoweight system apart is its capacity to handle products with diverse contents without requiring additional setup.
This innovation ensures operators can effortlessly transition between tasks involving different materials and product specifications. Whether dealing with varied product compositions or adapting to changes in production requirements, the Iwoweight system stands out for its versatility, offering a user-friendly and efficient solution that streamlines operations across various scenarios. This adaptability underscores its commitment to providing a flexible platform that accommodates the dynamic demands of modern manufacturing environments without sacrificing accuracy or efficiency.

The Iwoweight system ensures meticulous weight monitoring, thorough quality control, streamlined logging processes, and adaptability to various diverse products within the packaging industry. This innovative system goes beyond weight management, offering a comprehensive suite of features that elevate operational efficiency and accuracy.
One of the key strengths of the Iwoweight system lies in its ability to conduct precise weight monitoring, ensuring that every package meets exact specifications. Simultaneously, it establishes a robust framework for comprehensive quality control, scrutinising the weight and various aspects of packaging integrity.
The system further introduces automation to the logging processes, alleviating the burden on operators and creating a reliable record of each packaging operation. This data, stored meticulously, is a valuable resource for analysis, quality audits, and continual improvement.
Notably, the Iwoweight system distinguishes itself by its adaptability to diverse products. It effortlessly accommodates product types and specification variations without requiring intricate setup adjustments. This inherent flexibility makes it a versatile solution for packaging lines dealing with a wide range of products, promoting seamless transitions and reducing downtime.
Enhancing user-friendliness, the system features a multilingual interface that caters to a diverse workforce. Operators can easily navigate through the system in their preferred language, promoting clear communication and minimising the chances of errors.
Moreover, the Iwoweight system introduces remote editing capabilities, allowing operators to make adjustments and configurations from a distance. This remote functionality adds a layer of convenience and contributes to swift adaptability to changing production requirements.
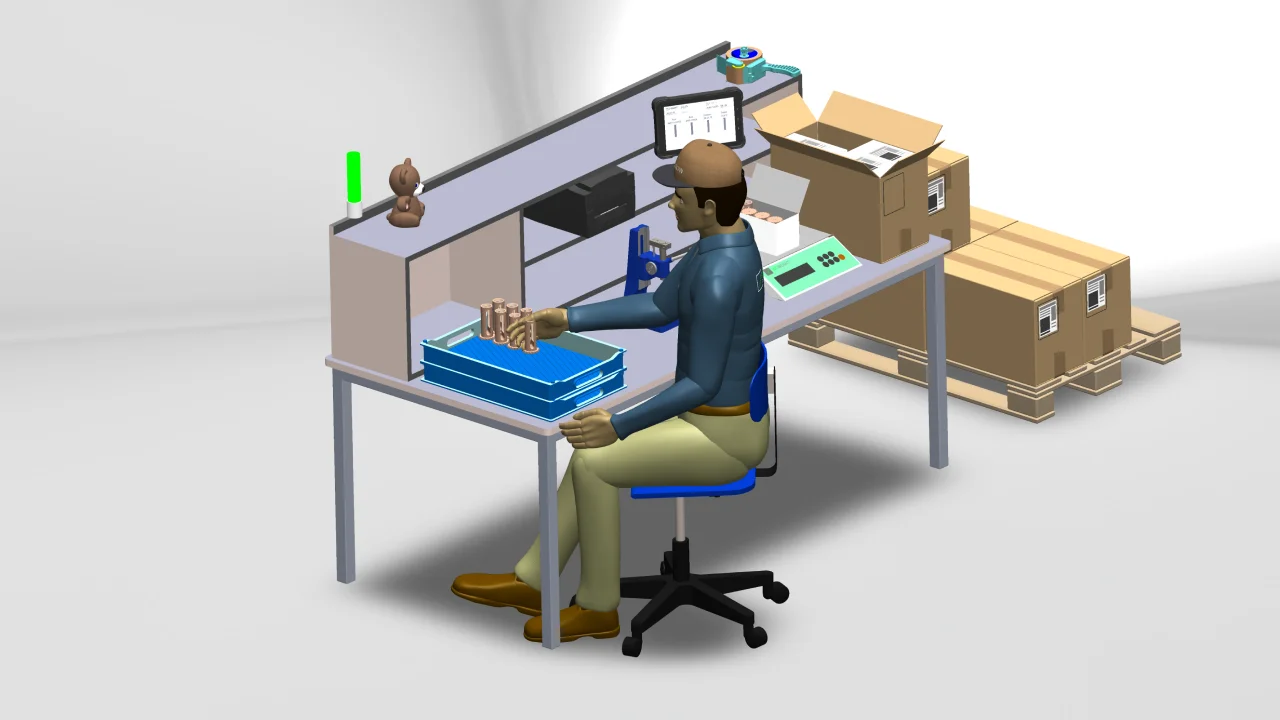
Production phase and weighing excellence with Iwoweight
In the production phase, the role of Iwoweight transcends mere weighing; it becomes the cornerstone for precision and efficiency. As materials flow into the workspace, the Iwoweight system orchestrates a seamless integration, guiding operators with explicit instructions through its intuitive tablet interface.
Iwoweight takes centre stage, monitoring package weights in real time with unparalleled accuracy.
The system's commitment to precision goes beyond the numerical values; it extends to comprehensive quality control, meticulously examining every aspect of the packaging to ensure integrity.
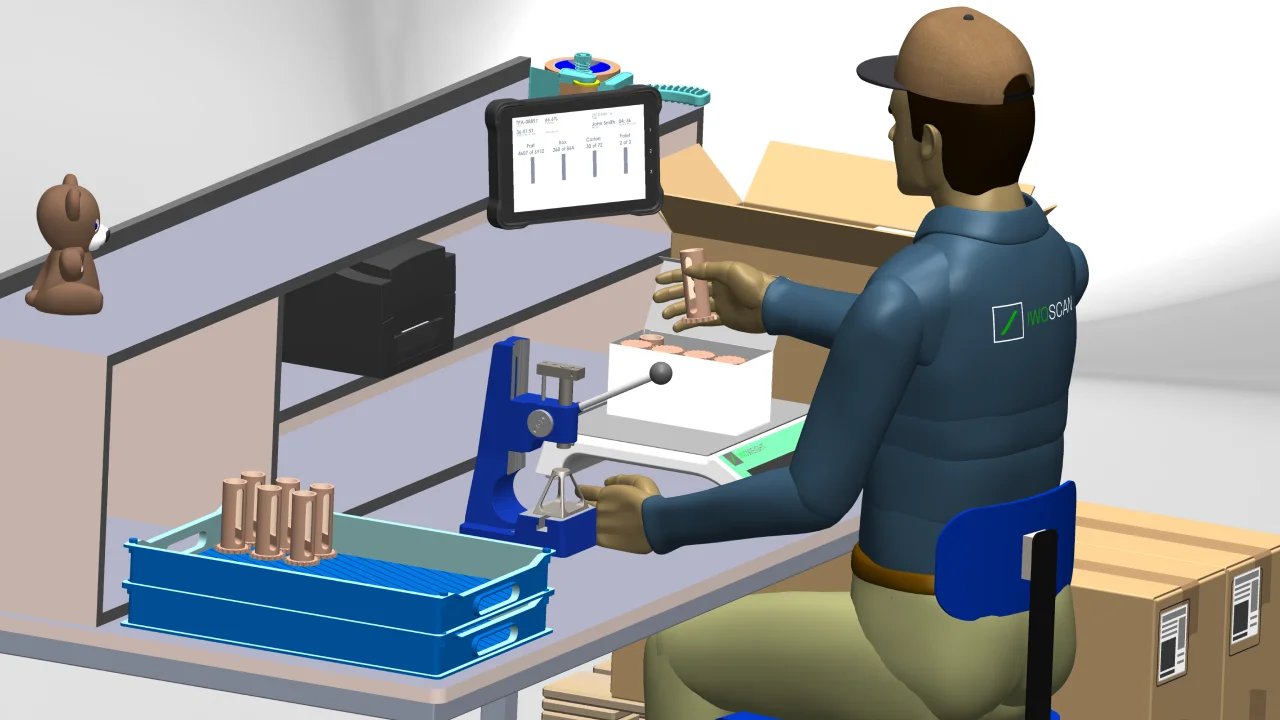
Label printing and package finalisation with Iwoweight
As the production phase progresses, the pivotal moment of label printing and package finalisation is seamlessly orchestrated by the comprehensive capabilities of the Iwoweight system. Beyond precise weighing, Iwoweight extends its influence to ensure that each package is impeccably labelled and finalised, contributing to a polished and efficient packaging process. At the heart of the label printing process, Iwoweight integrates flawlessly with a dedicated printer to generate labels/stickers that carry detailed and customisable information about the product. The precision exhibited in label printing is an extension of Iwoweight's commitment to accuracy throughout the packaging journey. These labels convey vital product information and contribute to a professional and standardised presentation.
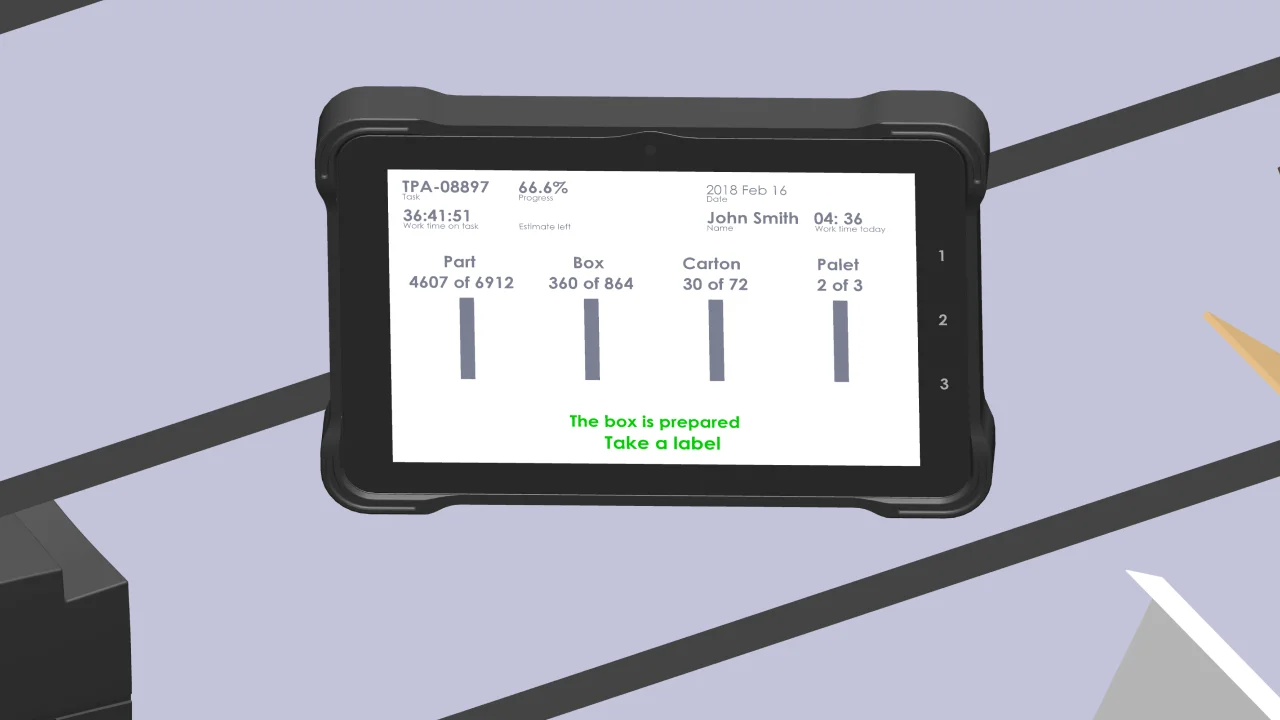
The Iwoweight system ensures that each label/sticker contains detailed, customised information relevant to the packaged product. This level of customisation is a testament to the system's versatility, accommodating diverse product lines and ensuring that end consumers receive comprehensive information about the contents within each package.
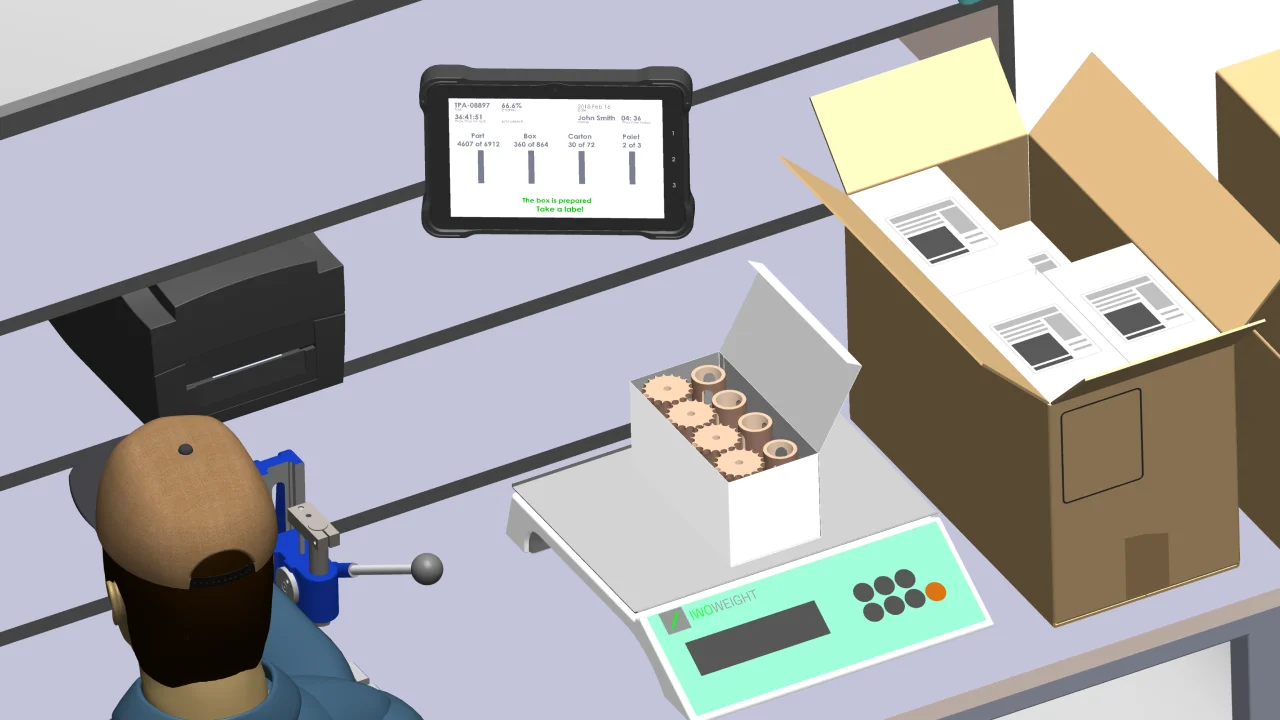
Upon packing a box, the system alerts the operator of task completion. The operator must then retrieve a sticker from the printer and affix it to the box. Subsequently, the operator places the fully packed package into a carton, and once the carton reaches full capacity, the operator positions the carton onto the pallet.
Step 1. The operator takes a sticker.
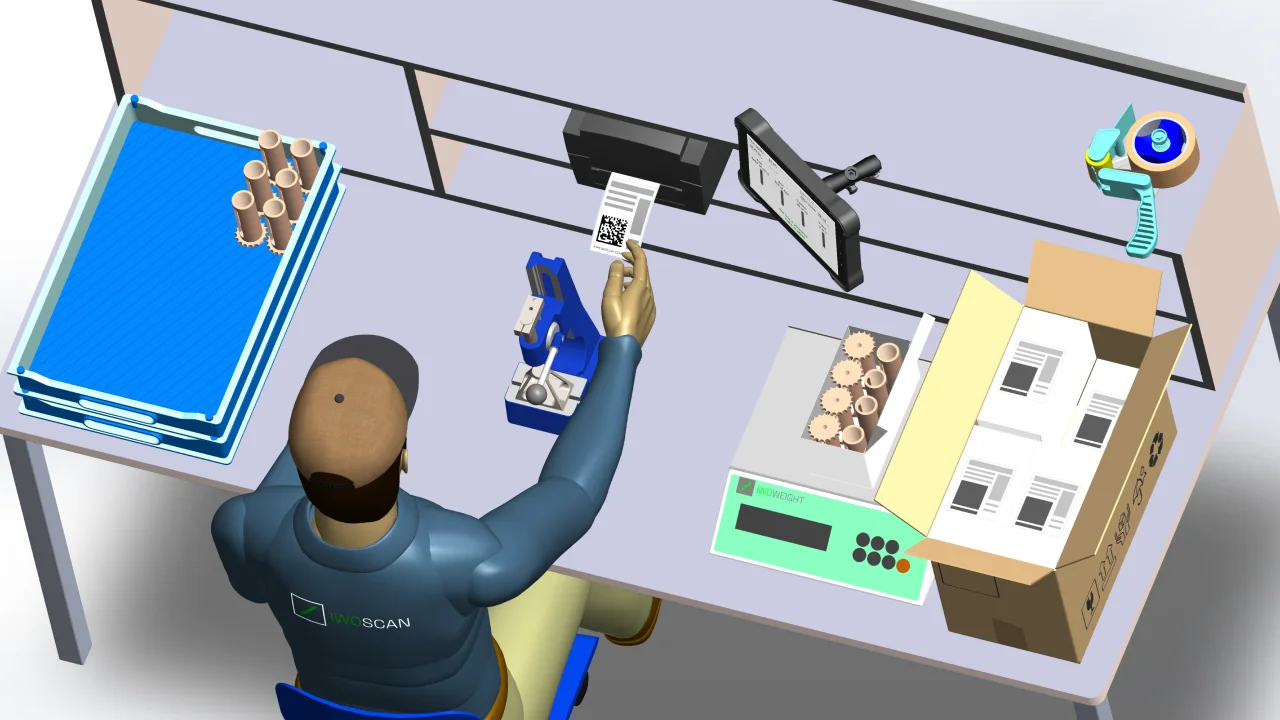
Step 2. The operator affixes the sticker onto the box.
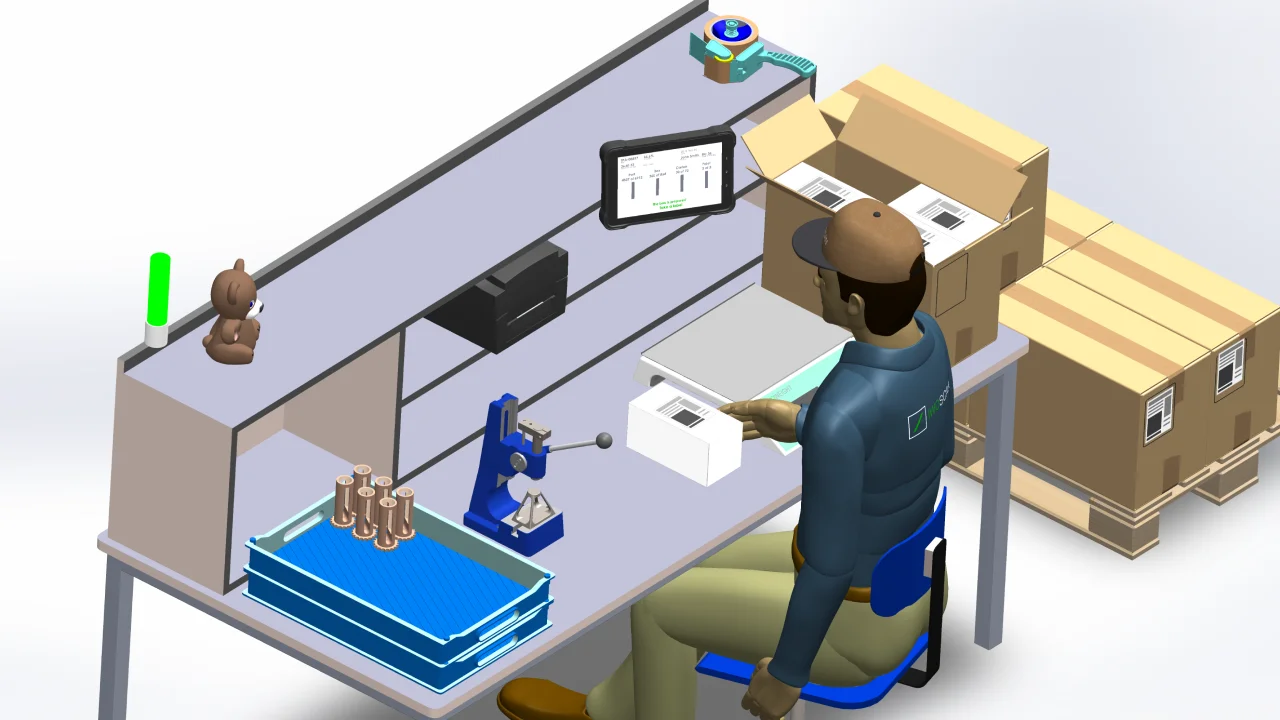
Step 3. The operator places the package into the box.
..webp)
Step 4. The operator is prepared to place the box into the carton.
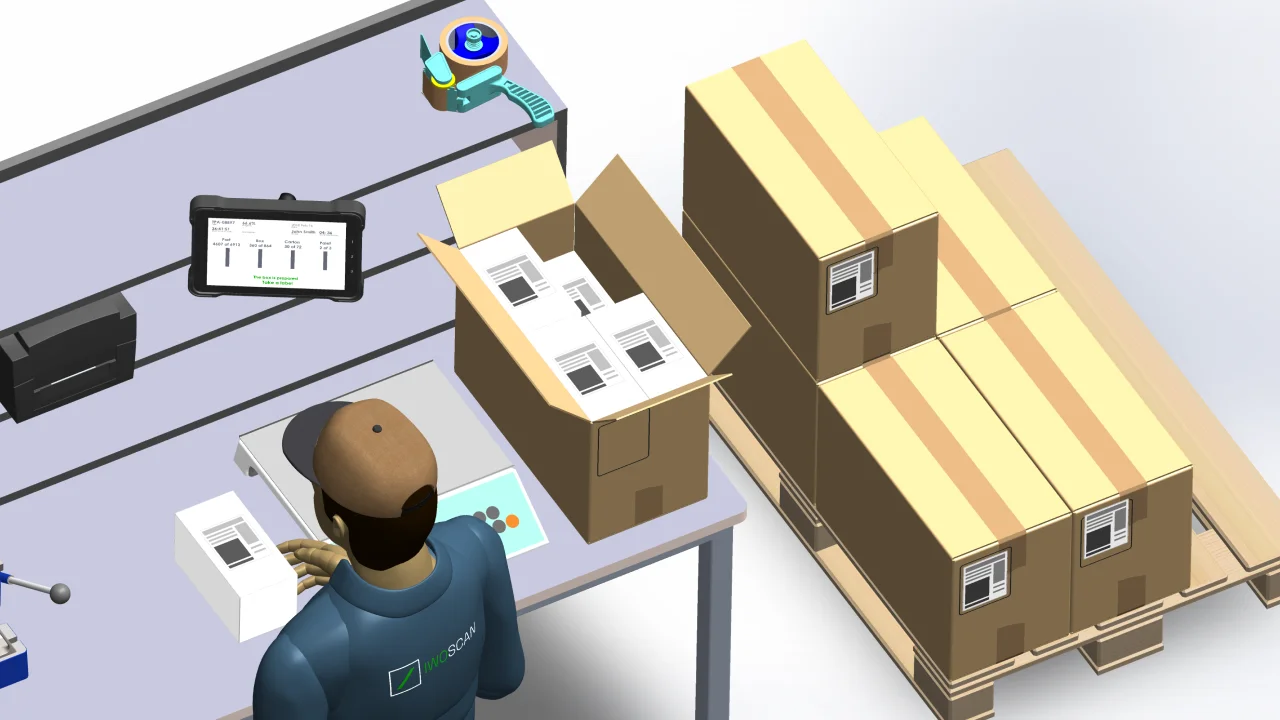
Step 5. The operator places the box inside the carton.
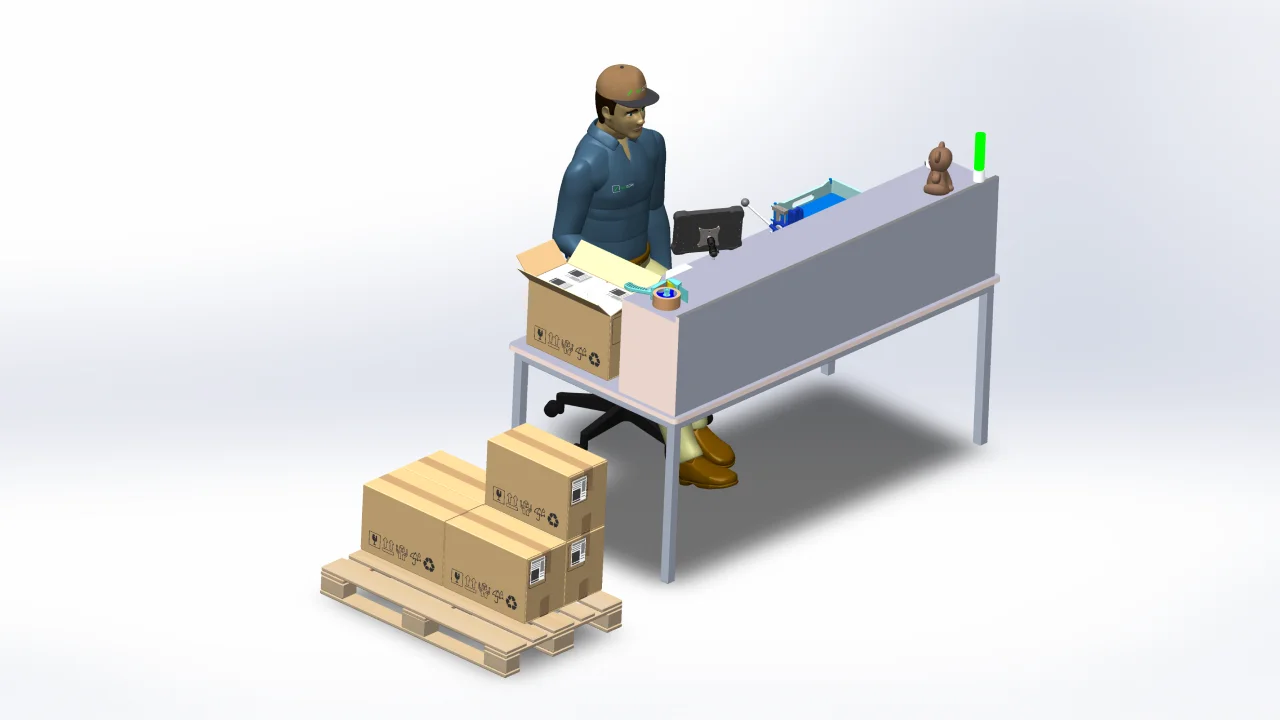
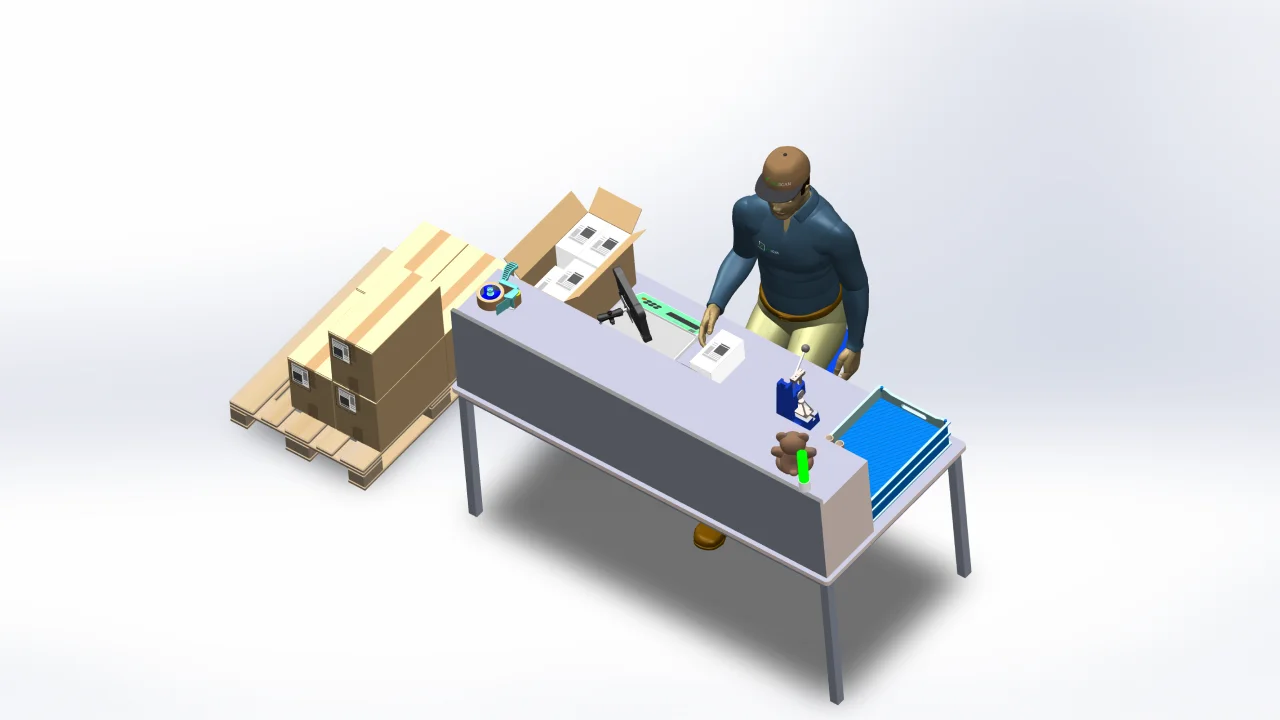
Choosing the ideal partner – exemplary service standards
Are you ready to elevate your productivity and maintain fail rate reduction? Discover the secrets to optimising your process efficiency and increasing ROI by embracing real-time remote monitoring for your process and packing line operations. Once the decision is made to invest in an Iwoweight system, ensuring its effectiveness requires attention to crucial factors:
- Accurate Installation - Guarantee the correct equipment installation to set the foundation for seamless performance.
- Empowering Operating Personnel - Provide comprehensive training to operating personnel, empowering them with the skills to harness the full potential of the Iwoweight system.
- Professional Performance Verification - Conduct meticulous performance verification to ensure the system operates efficiently.
- Holistic Support Throughout - Recognize that support extends beyond installation and initial commissioning. 'Useful Life Support' is equally vital, ensuring ongoing assistance throughout the entire working life of the Iwoweight.
- Satisfaction Assurance - A reliable Iwoweight manufacturer is committed to ensuring user satisfaction, guiding them through every system's useful life phase.
In the dynamic manufacturing landscape, the journey to excellence goes beyond mere acquisition – it's about fostering a partnership that prioritises precision, efficiency, and sustained success. Choose a partner who understands not just the technology but the unique needs of your manufacturing journey.
Harnessing the capabilities of the latest Iwoweight technology
In manufacturing, a contemporary Iwoweight surpasses its traditional role of merely weighing and sorting products. Beyond identifying non-conforming weights, the software features and options from an Iwoweight supplier empower manufacturers with heightened control over production processes. This goes beyond compliance; it's about optimising valuable resources, enhancing productivity, minimising waste, and ultimately elevating the Overall Equipment Efficiency (OEE) of the production line. It's not just a scale; it's a strategic ally in pursuing manufacturing excellence.
Comments
No comments yet!Add a Comment
You must be logged in to post a comment.