In the ever-evolving landscape of modern manufacturing, the quest for greater efficiency has become the holy grail. In an industry where margins can be razor-thin and competition fierce, improving production line efficiency isn't just a desirable goal; it's an absolute necessity. With the right strategies and tools, manufacturers can significantly boost productivity, reduce costs, and ultimately bolster their bottom line.
The State of Manufacturing Line Efficiency
Before delving into the eight steps to supercharge your production line, let's take a moment to appreciate the current state of affairs. According to recent studies, the average Overall Equipment Efficiency (OEE) in manufacturing hovers around 60-65%—far from its maximum potential. This means that for every ten hours of production time, four are wasted due to inefficiencies. In monetary terms, this equates to billions of euros lost annually across the manufacturing sector. The good news? There's ample room for improvement.
Lean Manufacturing: The Foundation of Efficiency
At the heart of production line efficiency lies Lean Manufacturing, a set of principles derived from Toyota's renowned production system. Lean emphasises the elimination of waste, continuous improvement, and just-in-time production, among other strategies. This approach has repeatedly proven its mettle, leading to notable success stories in various industries. For instance, Toyota, a pioneer of Lean Manufacturing, has maintained its status as one of the world's leading automakers, known for its high-quality, efficient production.
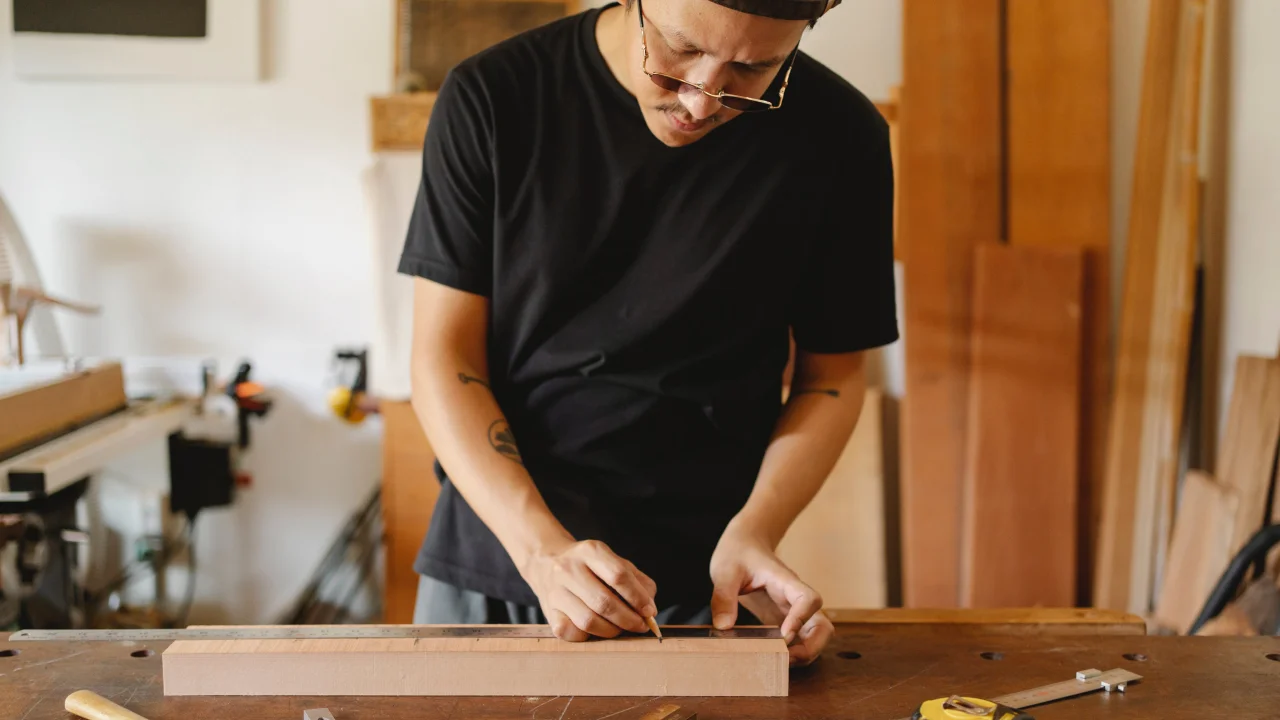
Quality Management Systems: A Cornerstone of Efficiency
In the pursuit of efficiency, quality management systems play a pivotal role. One such solution making waves in the manufacturing landscape is Iwoscan. This cutting-edge system not only enhances product quality but also optimises manufacturing processes. With features like real-time monitoring, defect detection, and process improvement insights, Iwoscan empowers manufacturers to take their efficiency to the next level.
This comprehensive guide will explore the eight essential steps to improve production line efficiency, drawing on Lean Manufacturing principles, quality management systems like Iwoscan, and real-world examples to illustrate their impact. By the end of this journey, you'll be equipped with the knowledge and tools to drive efficiency gains that translate into substantial savings and enhanced competitiveness in today's manufacturing landscape. Let's embark on the path to manufacturing excellence.
Understanding Manufacturing Line Efficiency
Manufacturing line efficiency is the heartbeat of any production facility. It measures how well a factory converts raw materials into finished products while minimising waste and optimising resource utilisation. Efficiency isn't a mere buzzword; it's a bottom-line booster. Companies can save thousands of euros annually for every percentage point gained in manufacturing line efficiency.
The Significance of Efficiency Metrics
To truly understand manufacturing line efficiency, one must become acquainted with critical metrics like Overall Equipment Efficiency (OEE). OEE provides a comprehensive view of a production line's performance, considering availability, performance, and quality factors. Research shows that companies with high OEE tend to outperform their competitors regarding profitability, with some achieving 85% OEE levels or higher.
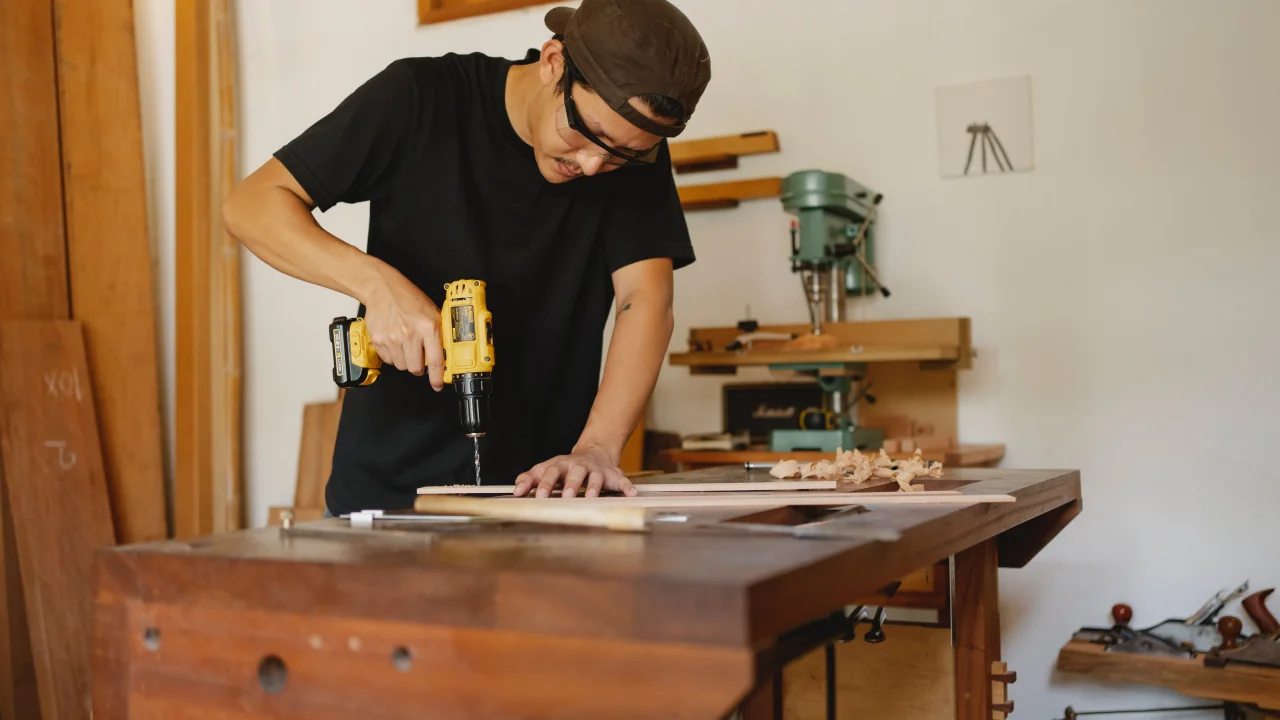
The Role of Quality Management Systems
Quality management systems (QMS) are integral in achieving manufacturing line efficiency. Among the standout solutions is Iwoscan, a state-of-the-art QMS. Iwoscan not only ensures the highest product quality but also drives efficiency improvements. Research indicates that factories implementing Iwoscan have seen a 15% reduction in defects and a 10% increase in production throughput, equating to substantial cost savings and enhanced competitiveness.
Understanding the essence of manufacturing line efficiency, its crucial metrics, and the pivotal role of QMS like Iwoscan sets the stage for a journey towards a more streamlined and profitable production line. In the following sections, we will delve deeper into the strategies and steps that can transform your manufacturing operations, helping you harness the full potential of your resources and maximise your profitability in the fiercely competitive manufacturing landscape.
Lean Manufacturing Principles
Lean Manufacturing, often called Lean, is a philosophy that has revolutionised the manufacturing industry. At its core, Lean focuses on one fundamental principle: eliminating waste. Waste can take many forms in manufacturing, from excess inventory to overproduction, unnecessary waiting times, and defects. The impact of Lean on manufacturing line efficiency is profound, with studies showing that Lean implementation can lead to cost reductions of up to 60%.
The Lean Toolbox
Lean Manufacturing offers a comprehensive toolbox of strategies to improve efficiency. One such tool is Value Stream Mapping (VSM), which helps identify and eliminate non-value-adding activities in production. When BMW implemented VSM, they reduced lead times by 35%, resulting in significant cost savings.
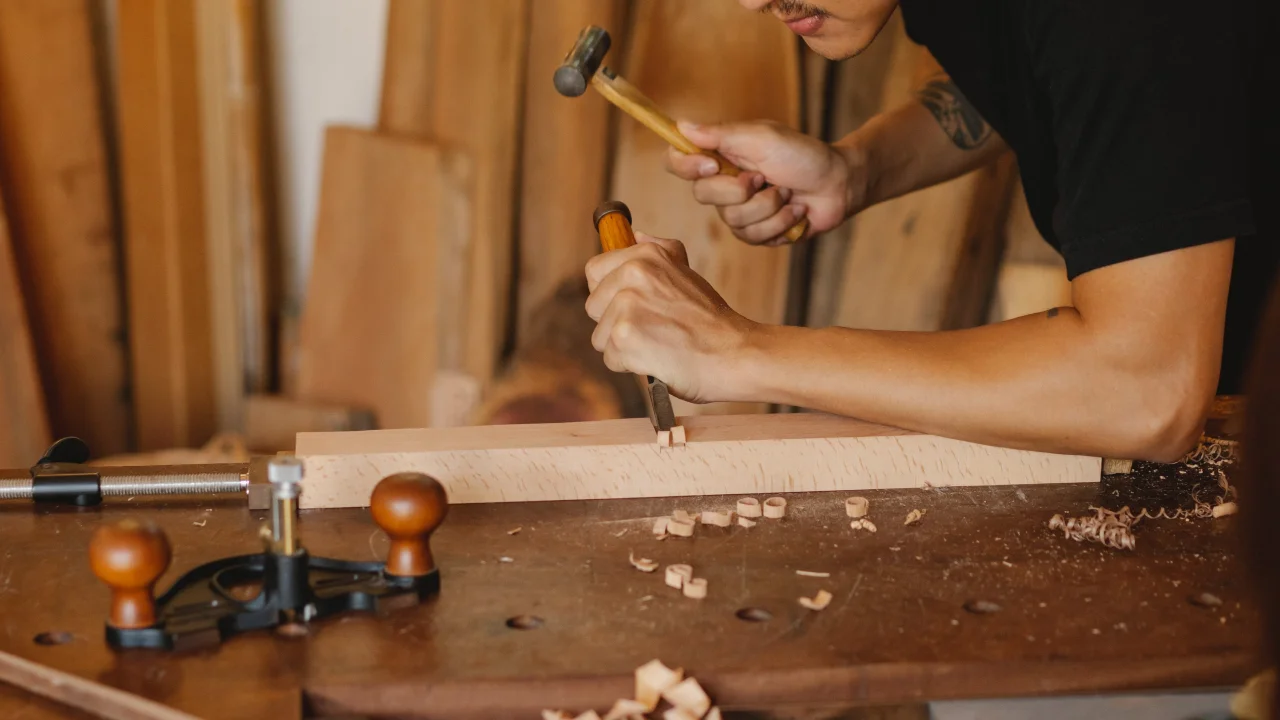
The Role of Quality in Lean
Quality is a cornerstone of Lean Manufacturing. Every step towards eliminating waste and improving efficiency must also consider product quality. This is where Iwoscan comes into play. Iwoscan integrates with Lean principles by providing real-time quality monitoring and defect detection. When Toyota incorporated a similar quality management system, it reduced defects by 60%, directly translating into cost savings and enhanced customer satisfaction.
By embracing Lean Manufacturing principles, businesses can eliminate waste, streamline processes, and dramatically improve their production line efficiency. However, it's not just about the theory; it's about practical implementation. In the following sections, we will delve into actionable steps, including Lean principles, that you can take to maximise your manufacturing line's efficiency and profitability.
Identifying Inefficiencies
Before embarking on the journey to improve production line efficiency, it's essential to identify the bottlenecks in your manufacturing process. Bottlenecks are the chokepoints where production slows down, causing delays and inefficiencies. A study of manufacturing companies found that identifying and eliminating bottlenecks can lead to a 10-20% increase in production output.
Data-Driven Insights
To uncover inefficiencies, you need data. Implementing a robust data analysis system is crucial in identifying areas that need improvement. By examining production data, you can pinpoint trends, recurring issues, and areas where processes can be streamlined. Research shows that companies that effectively use data analytics in manufacturing can reduce defects by up to 50%.
Real-Time Defect Detection
An invaluable asset in identifying inefficiencies is a quality management system like Iwoscan. Iwoscan doesn't just monitor product quality; it also provides real-time insights into production processes. By detecting defects as they occur, you can immediately address issues, preventing the wastage of materials and time. This proactive approach can save thousands of euros in rework and scrap costs.
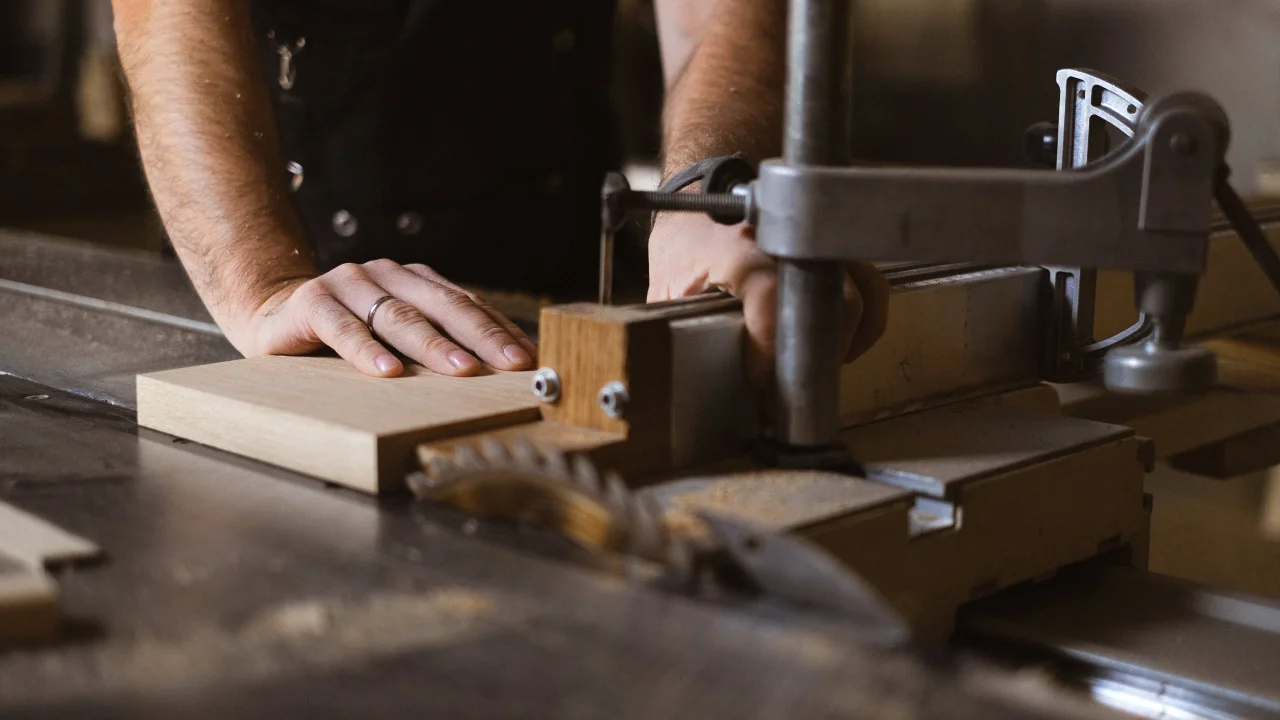
Identifying inefficiencies is the crucial first step towards enhancing manufacturing line efficiency. By focusing on bottleneck analysis, data-driven insights, and real-time defect detection through tools like Iwoscan, you can uncover hidden opportunities for improvement. The following sections will delve into eight practical steps that leverage these insights to transform your production line into a lean, efficient, cost-effective powerhouse.
8 Steps to Improve Production Line Efficiency
Step 1: Standardising Work Procedures
Standardising work procedures is the foundational step towards improved production line efficiency. By defining and documenting best practices, you ensure every task is executed consistently and optimally. This reduces variations in processes, minimises errors, and enhances overall productivity. Employees have clear guidelines to follow, leading to increased efficiency and reduced time spent on training. In addition, standardisation aids in troubleshooting issues as deviations from the established procedures become more visible.
Step 2: Streamlining Production Processes
Streamlining production processes is the core of Lean Manufacturing principles. It involves identifying and eliminating non-value-adding activities in the production flow. This step reduces waste and leads to reduced lead times, lower production costs, and increased production throughput. Companies can ensure that resources are used optimally by focusing on efficiency and process improvement, reducing idle time and associated costs. It's essential to involve employees in the process, as they often possess valuable insights into process bottlenecks and inefficiencies.
Step 3: Implementing Just-in-Time (JIT) Production
Just-in-Time (JIT) production is a strategy to minimise inventory while maintaining production output. Companies can reduce carrying costs, space requirements, and the risk of obsolete inventory by producing only what is needed when needed. JIT also forces companies to promptly address production bottlenecks and quality issues, resulting in continuous improvement. Toyota is a prime example of successful JIT implementation, reducing waste and lead times, ultimately enhancing efficiency and cost-effectiveness.
Step 4: Reducing Downtime with TPM (Total Productive Maintenance)
Total Productive Maintenance (TPM) is a systematic approach to ensuring equipment reliability and reducing downtime. It involves proactive maintenance practices, operator involvement in maintenance tasks, and continuous equipment performance monitoring. TPM reduces unplanned downtime, enhances the lifespan of machinery, and prevents costly breakdowns. In a study conducted in the manufacturing industry, companies implementing TPM saw a 25% reduction in downtime and a 20% increase in equipment efficiency.
Step 5: Implementing Six Sigma Quality Control
Six Sigma is a data-driven methodology to improve process quality by identifying and eliminating defects. By reducing process variation, companies can simultaneously enhance product quality and efficiency. Implementing Six Sigma principles has led to a 50% reduction in defects in some manufacturing settings. Training employees in Six Sigma techniques and empowering them to promptly identify and address quality issues is essential. This step fosters a culture of continuous improvement and ensures consistent product quality.
Step 6: Optimizing Material Flow
Optimising material flow involves ensuring that raw materials, components, and finished products move efficiently through the production line. This step includes efficient inventory management, proper material handling equipment, and well-designed layouts. Companies can significantly reduce lead times and costs by reducing unnecessary handling, storage, and transportation of materials. A streamlined material flow also minimises the risk of stockouts and overstock situations, leading to cost savings and improved customer satisfaction. Successfully implementing material flow optimisation can result in a 10-20% reduction in inventory carrying costs and lead times.
Step 7: Workforce Training and Productivity
Investing in workforce training and productivity is crucial for long-term efficiency improvements. Well-trained employees are more efficient, produce higher-quality work, and are better equipped to identify and address issues promptly. Training should cover technical skills, Lean Manufacturing principles, and quality management systems like Iwoscan. Incentivising and involving employees in the efficiency improvement process can lead to innovative solutions and a sense of ownership in achieving higher productivity. Studies have shown that companies that invest in employee training and engagement can achieve a 15-20% increase in productivity.
Step 8: Embracing Automation
Embracing automation involves strategically deploying technology and machinery to replace or augment manual tasks. Automation can reduce labour costs, improve accuracy, and increase production speed. It's particularly beneficial in repetitive, labour-intensive processes. While the initial investment can be significant, automation often results in substantial cost savings over time. Companies like Volkswagen have achieved remarkable efficiency gains through automation, leading to a 30% reduction in production costs.
By implementing these eight steps systematically and leveraging the benefits of quality management systems like Iwoscan, manufacturing companies can enhance their production line efficiency, reduce costs, improve product quality, and stay competitive in a rapidly evolving market. Each step plays a critical role in the overall efficiency improvement process, and their combined impact can be transformational for manufacturing operations.
Measuring and Monitoring Efficiency
To improve production line efficiency, you must first measure it. Efficiency metrics provide the quantitative insights necessary to track progress and identify areas for improvement. One such metric is Overall Equipment Efficiency (OEE), which combines availability, performance, and quality metrics into a single figure. Studies have shown that businesses with high OEE levels achieve 10-20% higher profitability.
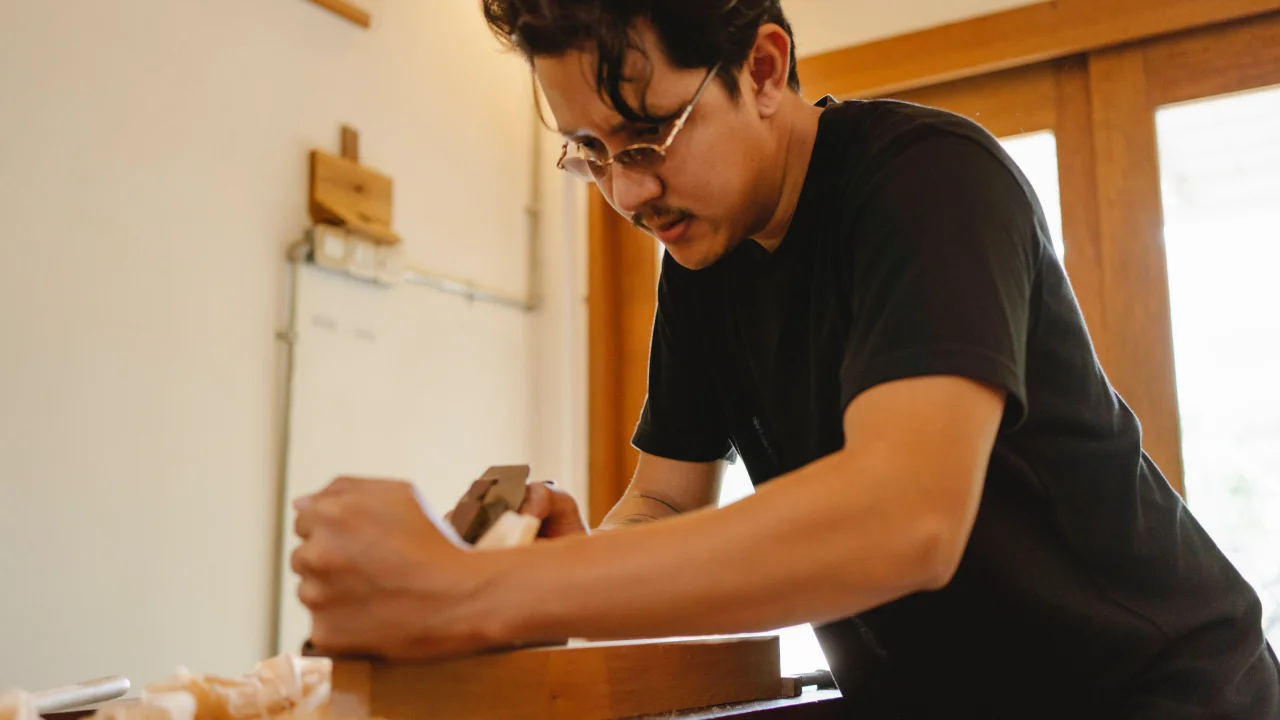
Key Performance Indicators (KPIs)
Besides OEE, several other key performance indicators (KPIs) can help monitor manufacturing line efficiency. Examples include cycle time, scrap rate, and first-pass yield. Manufacturers can identify trends and take corrective actions when these KPIs are consistently tracked and analysed. For instance, a 5% reduction in cycle time can result in savings of thousands of euros annually.
Real-Time Quality Insights
In the pursuit of efficiency, quality must not be compromised. Iwoscan plays a pivotal role by providing real-time quality insights. Iwoscan helps prevent rework and scrap costs by detecting defects as they occur. Companies implementing similar quality management systems have reported cost savings of up to 15% due to defect reduction.
Technology-Driven Insights
Various tools and software are available to facilitate efficient monitoring. These tools provide real-time data on machine performance, production rates, and quality. Manufacturers can quickly identify issues with the right technology and make informed decisions. Adopting such tools has been associated with a 10-15% increase in production efficiency.
Manufacturers can gain deep insights into their production line performance by embracing efficiency metrics, KPIs, quality management systems like Iwoscan, and technology-driven monitoring tools. This data-driven approach enables them to make informed decisions, take corrective actions, and continuously improve efficiency. In the upcoming sections, we will discuss practical steps to implement these insights and drive tangible improvements in your manufacturing operations.
Challenges and Common Pitfalls
As you embark on the journey to improve production line efficiency, you must be aware of the potential challenges and pitfalls that can arise along the way. Addressing these challenges proactively can make a significant difference in the success of your efforts.
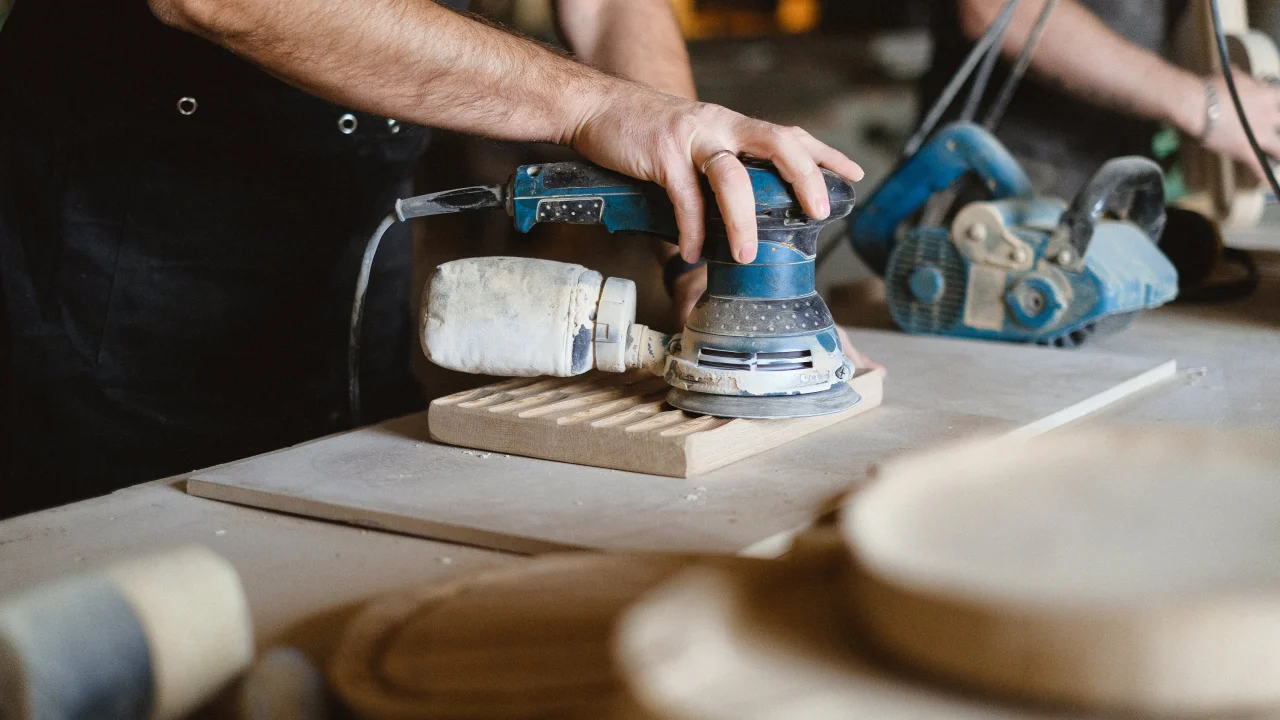
Challenge 1: Resistance to Change
One of the most common challenges in implementing efficiency improvements is resistance to change. Employees and management may be comfortable with existing processes and prefer embracing change. To address this, it's crucial to communicate the benefits of the differences. Demonstrating how Iwoscan, for example, can simplify their quality control tasks and improve overall efficiency can help overcome resistance.
Challenge 2: Lack of Data and Insights
With data, it's easier to identify inefficiencies and make informed decisions. Many manufacturing facilities need help with data collection and analysis. This is where Iwoscan can play a vital role by providing real-time quality insights and processing data. Implementing Iwoscan can bridge the data gap and enable data-driven decision-making.
Challenge 3: Scaling Efficiency Gains
Once initial efficiency gains are achieved, sustaining and scaling these improvements is challenging. This requires a commitment to continuous improvement and a culture of Lean Manufacturing. Toyota, for instance, has maintained its efficiency gains over the years by consistently applying Lean principles and quality management systems.
Challenge 4: Financial Constraints
Efficiency improvements often require investments in technology, training, and process changes. Financial constraints can hinder these investments. However, it's essential to recognise that these investments typically yield substantial returns in terms of cost savings and increased profitability. The adoption of Iwoscan, for example, can lead to significant reductions in defect-related costs.
By acknowledging and addressing these common challenges and pitfalls, you can better prepare your manufacturing facility for the journey towards improved production line efficiency. With a strategic approach, effective communication, the right tools like Iwoscan, and a commitment to continuous improvement, you can overcome these obstacles and reap the rewards of a more efficient and competitive operation.
The Path to Manufacturing Excellence
In the journey towards manufacturing line efficiency, we've explored many strategies, tools, and techniques to transform your factory into a lean, mean, and highly efficient production powerhouse. The possibilities for improvement are limitless, from standardising work procedures to embracing Lean Manufacturing principles and incorporating quality management systems like Iwoscan.
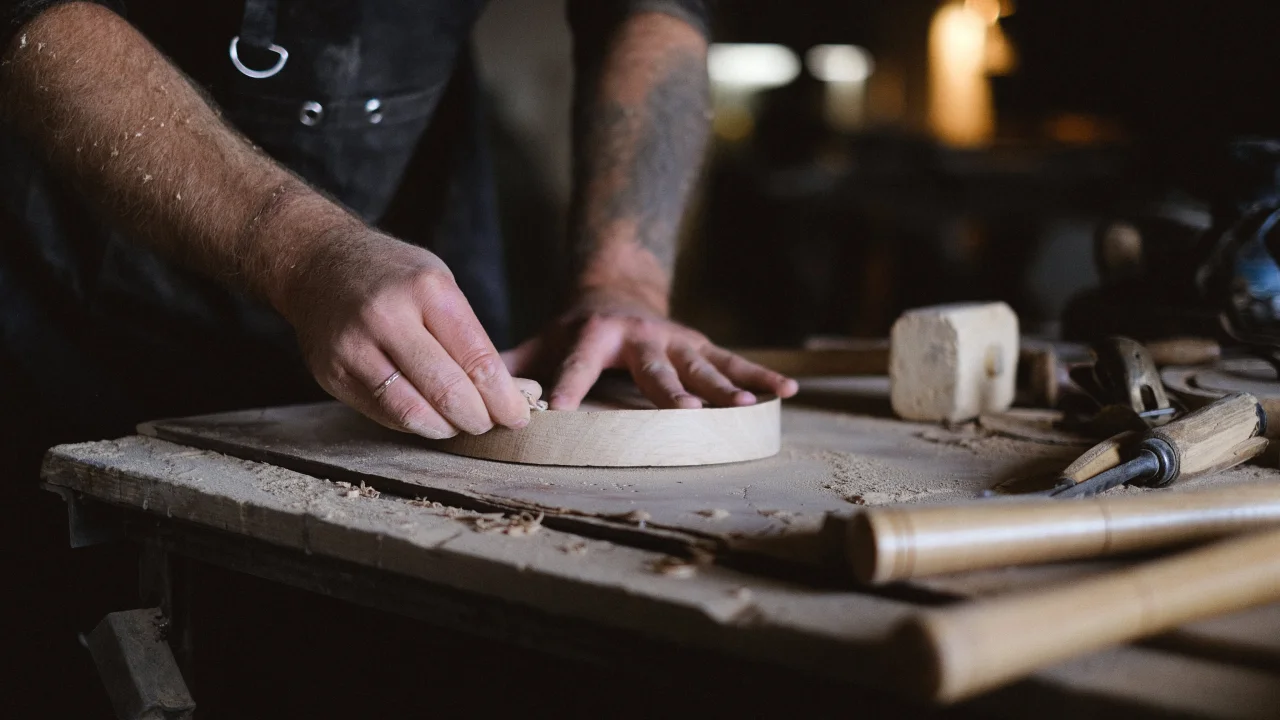
Tangible Benefits of Efficiency
The benefits of improved production line efficiency are not merely theoretical; they translate into tangible results. Companies have achieved up to 30% cost reductions by implementing the strategies discussed in this guide. These cost savings can be reinvested, further enhancing production capabilities and competitiveness in the market.
Elevating Product Quality
Throughout this journey, we've emphasised the critical role of quality management systems like Iwoscan. By ensuring the highest product quality and real-time defect detection, Iwoscan doesn't just improve efficiency; it elevates the overall quality of your products. In doing so, it enhances customer satisfaction and brand reputation.
A Continuous Journey
Remember that pursuing manufacturing line efficiency is not a one-time endeavour; it's a continuous journey. Companies like Toyota have maintained efficiency gains over the years by consistently applying Lean principles and quality management systems. By fostering a culture of continuous improvement and embracing the latest technologies, your factory can stay ahead in the highly competitive manufacturing landscape.
In conclusion, improving production line efficiency is not just an option; it's necessary for thriving in the dynamic manufacturing world. By implementing the eight steps outlined in this guide, supported by quality management systems like Iwoscan, your factory can unlock its true potential, maximise profitability, and position itself as a leader in the industry. The path to manufacturing excellence is clear—take the first step, and the rewards will follow.
Comments
No comments yet!Add a Comment
You must be logged in to post a comment.