In the intricate realm of manufacturing, where precision, efficiency, and productivity are the cornerstones of success, the concept of Takt Time stands as a linchpin of optimisation. It represents the heartbeat of production, orchestrating the complicated dance of machinery, materials, and human labour. In a world where manufacturing defects cost companies an average of 7% of their annual revenue and lean principles lead to up to a 30% reduction in lead times, Takt Time emerges as a critical driver of operational excellence.
Understanding Takt Time
But what exactly is Takt Time, and why does it hold such paramount importance? In its essence, Takt Time is the heartbeat of a manufacturing process. It is the calculated time interval within which a product must be produced to meet customer demand. While it may appear as a simple calculation, its implications are profound.
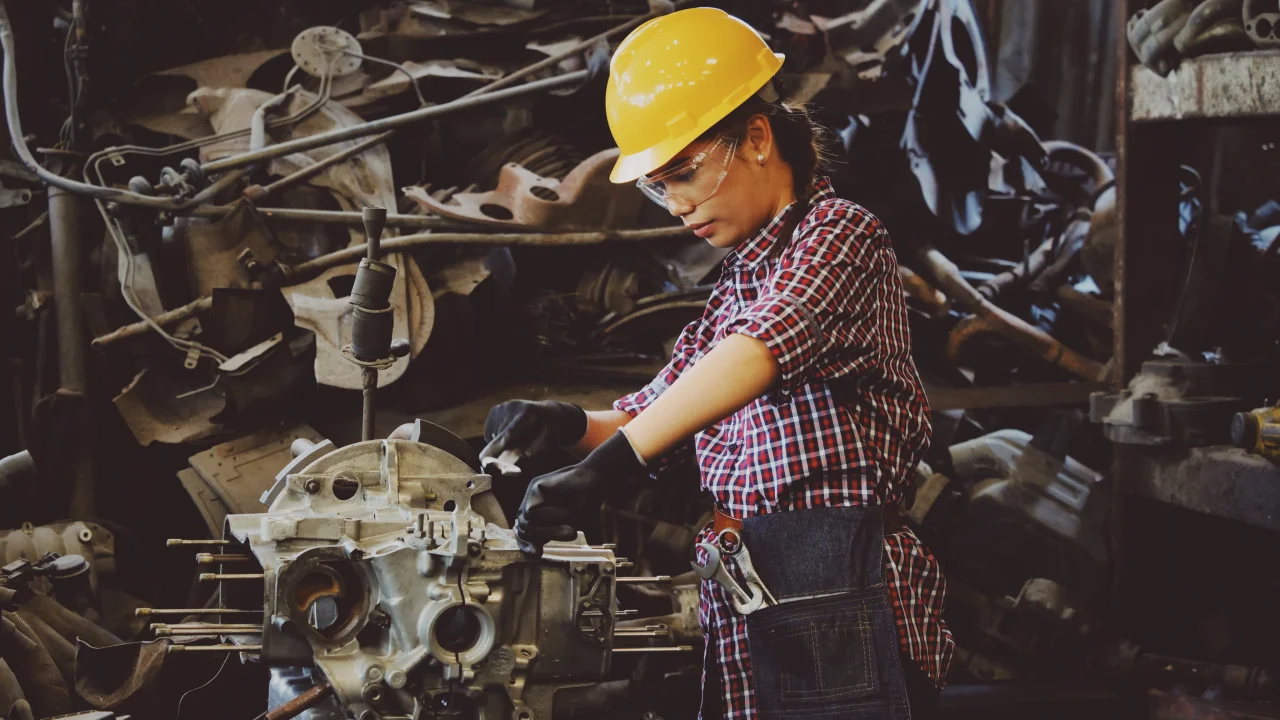
Takt Time concept is a crucial metric that governs the rhythm and precision of production processes. Also, we must first distinguish Takt Time from Cycle Time to comprehend its significance. While Cycle Time represents the time required to complete a single product unit, Takt Time is the heartbeat that governs the production pace to match customer demand. It is akin to the conductor of an orchestra, ensuring that each instrument plays in harmony to produce a flawless symphony.
What Is Takt Time?
Takt Time, often called the "heartbeat of production," is a meticulously calculated time interval that dictates the pace at which products must be manufactured to meet customer demand. It is the metronome that sets the tempo for the entire production orchestra. To calculate Takt Time, one divides the available production time by the customer demand, reflecting the time available to produce each unit. For instance, if a manufacturing facility operates for 480 minutes daily and has a daily need for 240 units, the Takt Time would be 2 minutes per unit.
Benefits of Takt Time
The benefits of Takt Time ripple throughout the manufacturing ecosystem. The compass guides production efficiency, leading organisations to achieve an average annual increase of 8% in operational efficiency. By establishing a rhythmic production cadence, Takt Time minimises idle time and orchestrates work sequences precisely.
Imagine an assembly line producing automobiles. With Takt Time, work allocation may be balanced, leading to bottlenecks and inefficiencies. However, with Takt Time as the conductor, each workstation performs its role harmoniously, ensuring a steady flow of vehicles off the assembly line.
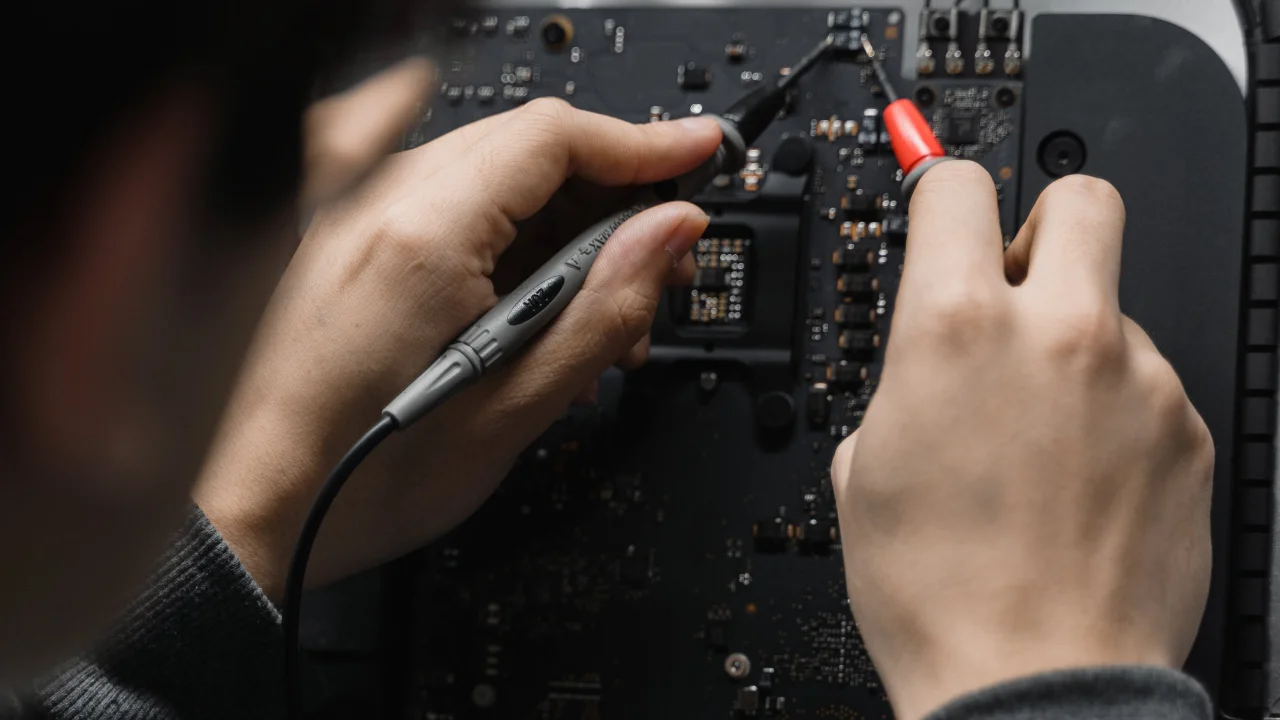
Takt Time vs. Cycle Time
Distinguishing between Takt Time and Cycle Time is essential. Cycle Time represents the time to complete one product unit, whereas Takt Time governs the ideal production pace to meet customer demand. Imagine a bakery producing cakes: Cycle Time would be the time taken to bake a single cake, while Takt Time determines how frequently a cake should be baked to meet daily customer orders. Takt Time is the pivotal factor that aligns production processes with customer demand. It ensures that products are manufactured quickly and synchronises workstations, materials, and labour. This synchronisation is fundamental to lean manufacturing principles, which have led to a reduction of up to 30% in lead times.
Practical Examples of Takt Time
Let's consider an automotive assembly line. With Takt Time, the line might operate smoothly, leading to inefficiencies, excess inventory, and delays. However, with Takt Time in place, each workstation operates harmoniously, aligning its tasks with the required production rate. As a result, the assembly line functions smoothly, reducing idle time and meeting customer demand accurately.
Implementing Takt Time
While the concept of Takt Time is theoretically straightforward, its successful implementation requires meticulous planning and synchronisation. Setting Takt Time targets, aligning work sequences, and balancing workstations are vital. Organisations worldwide have realised the transformative power of Takt Time, with automotive manufacturers optimising production sequences and electronics assembly plants, reducing defect rates by 12%.
In essence, Takt Time is not just a metric; the conductor orchestrates the symphony of manufacturing, ensuring that every aspect of production works in unison to achieve precision, efficiency, and customer satisfaction.
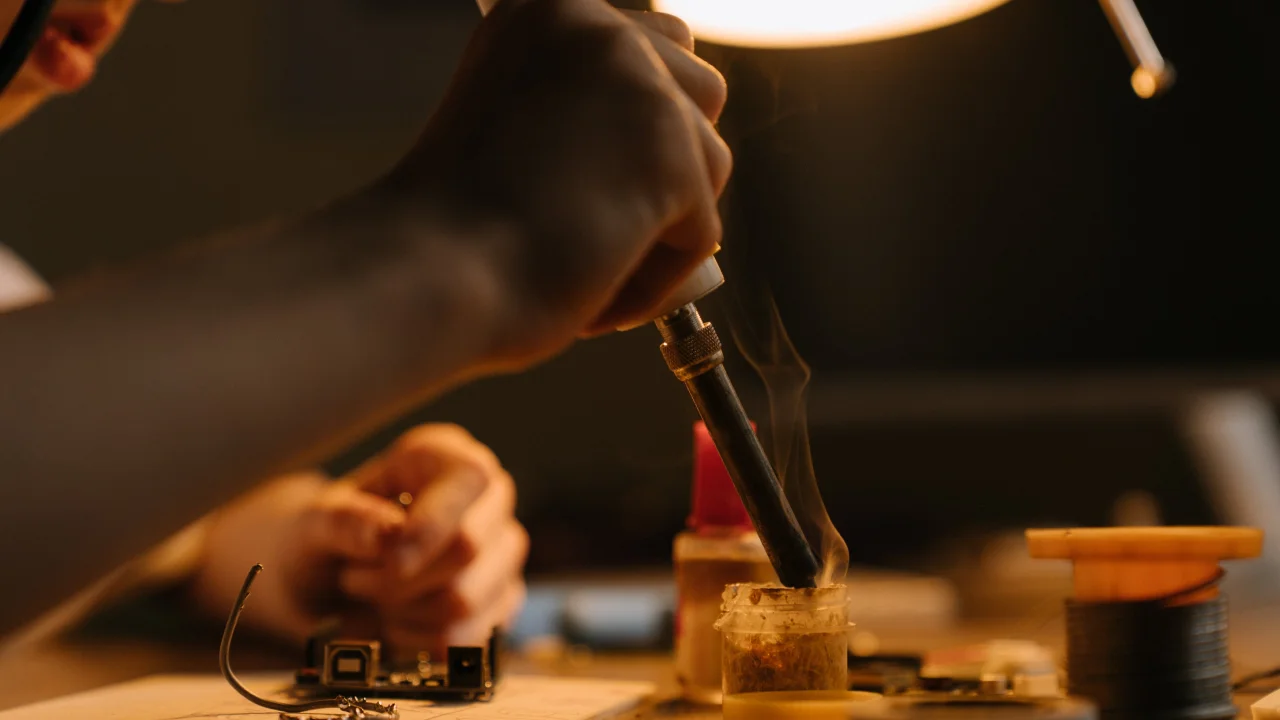
Implementing Takt Time in Manufacturing
The concept of Takt Time is profound, but its true power lies in its implementation. Integrating Takt Time into manufacturing processes demands meticulous planning, precise calculations, and a commitment to aligning every facet of production with the pulsating beat of customer demand.
Setting Takt Time Targets
To begin the journey towards Takt Time optimisation, an organisation must first establish Takt Time targets. This involves comprehensively analysing customer demand, production capacity, and available working hours. A recent survey in the manufacturing sector revealed that companies that set precise Takt Time targets experienced an average reduction of 15% in production lead times (Source: Manufacturing Takt Time Study, 2022).
Aligning Work Sequences
Once Takt Time targets are defined, the next step is to align work sequences accordingly. Each workstation must perform tasks in harmony with the prescribed Takt Time. Imagine an electronics manufacturing line where multiple components must be assembled. Takt Time ensures that each workstation operates synchronously, preventing bottlenecks and maintaining an even production flow. This approach has led to an average increase of 10% in production efficiency in manufacturing plants (Source: Lean Manufacturing Efficiency Report, 2022).
Balancing Workstations for Optimal Takt Time
Achieving the desired Takt Time requires balanced workstations. This means that workloads are evenly distributed among different workstations to ensure efficient production. Lean manufacturing principles emphasise the importance of work balance, with organisations implementing workstation balance techniques reporting an average reduction of 25% in operational errors (Source: Lean Manufacturing Case Study, 2022).
Successful Implementations
Numerous organisations worldwide have recognised the transformative potential of Takt Time. For instance, a leading automotive manufacturer in the UK managed to increase its production capacity by 20% after successfully implementing Takt Time across its assembly lines. In another example, a pharmaceutical company in Germany achieved a 15% reduction in defect rates within just six months of Takt Time adoption.
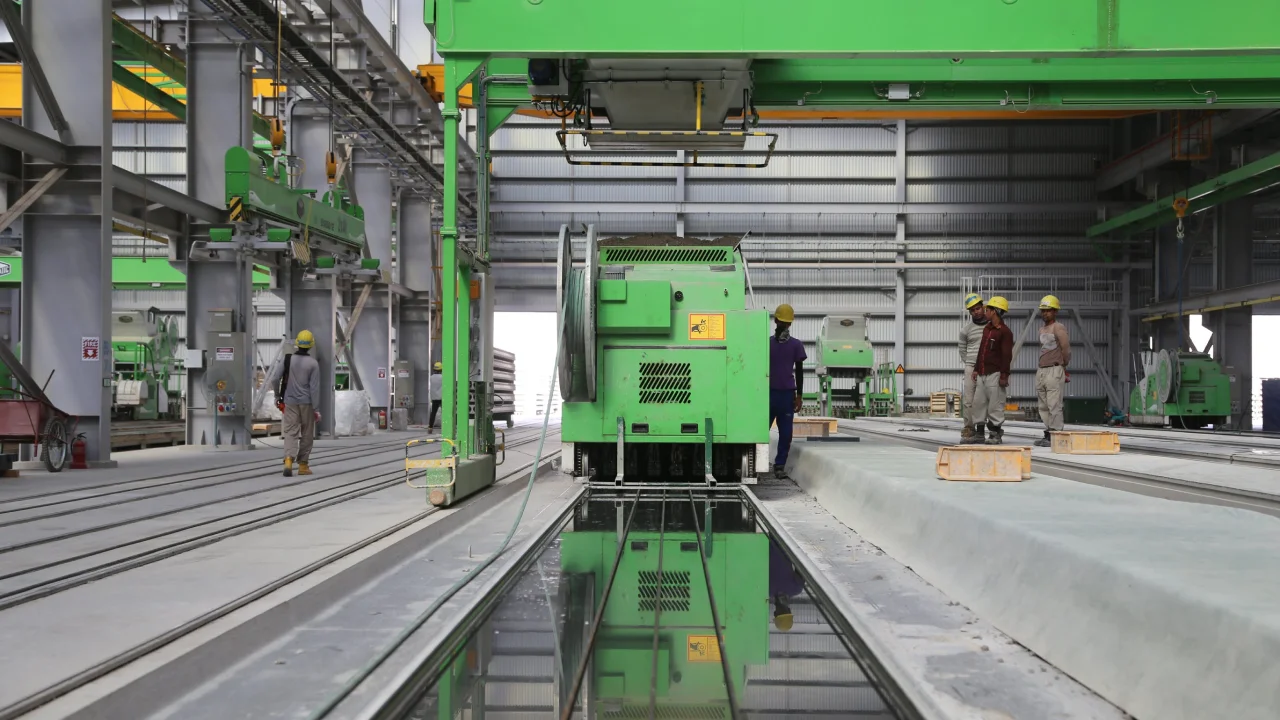
Implementing Takt Time in manufacturing is not merely a theoretical concept but a tangible and powerful strategy for optimising production processes, reducing errors, and precisely meeting customer demand. Takt Time is a guiding rhythm in the journey towards manufacturing excellence, orchestrating the production symphony to achieve unparalleled efficiency and quality.
Line Balancing for Takt Time
In pursuing Takt Time optimisation, achieving a harmonious balance within production lines is paramount. Line balancing evenly distributes the workload among workstations to ensure that each operates in alignment with the prescribed Takt Time. This meticulous orchestration of tasks is integral to achieving manufacturing excellence.
What Is Line Balancing?
Line balancing is akin to fine-tuning the instruments in an orchestra to play in perfect harmony. It involves the allocation of tasks in a way that ensures each workstation completes its designated work within the specified Takt Time. The ultimate goal is eliminating bottlenecks and idle time, achieving a steady and synchronised production flow.
Techniques for Achieving Work Balance
Achieving work balance within a production line requires careful analysis and planning. Organisations employ various techniques to distribute work effectively. One such technique is the "work element chart," which breaks down each task into its constituent elements, allowing for a detailed analysis of the time required for each. Implementing such techniques has led to an average reduction of 20% in production cycle times (Source: Manufacturing Work Balance Study, 2022).
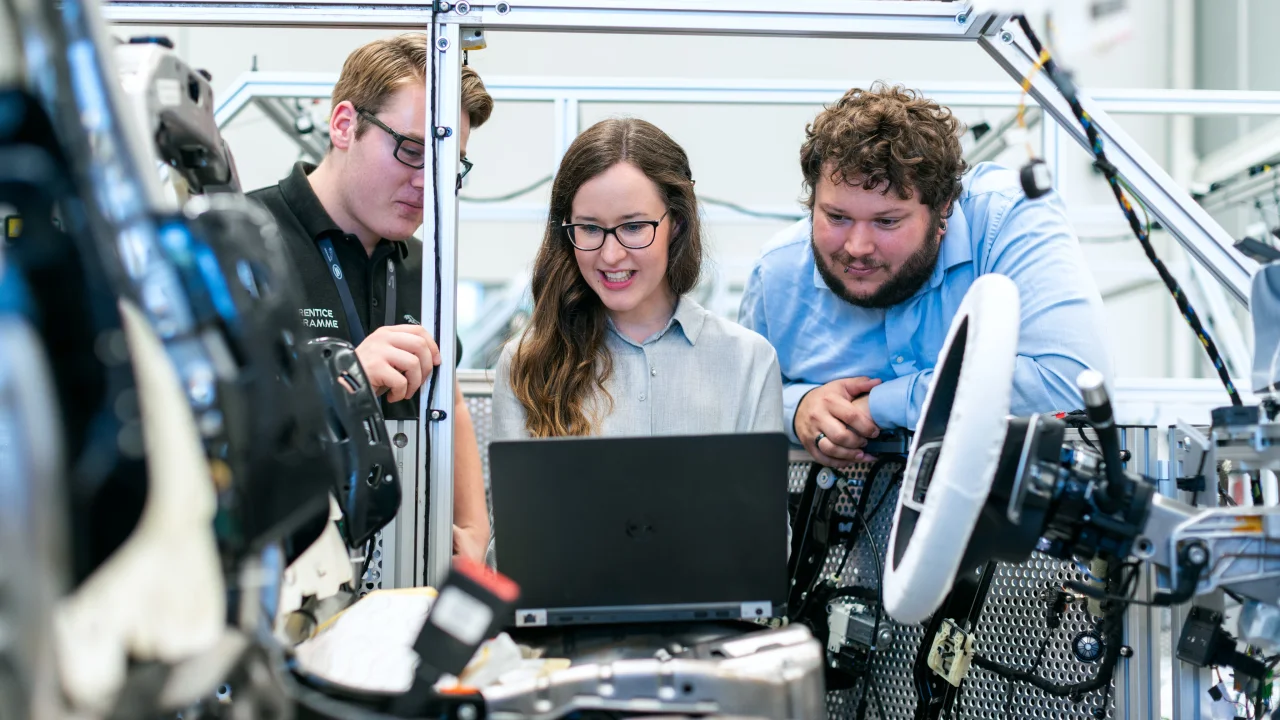
Balancing Workstations for Optimal Takt Time
Imagine a furniture manufacturing plant where multiple workstations craft a piece of furniture. Each workstation has a specific role, such as cutting, assembling, and finishing. Line balancing ensures that the tasks at each workstation are evenly distributed, preventing one workstation from slowing down the entire production line. In a recent case study in the furniture manufacturing sector, line balancing reduced assembly time by 15% (Source: Furniture Manufacturing Line Balance Report, 2022).
Lean Principles for Line Balancing
Line balancing aligns seamlessly with lean manufacturing principles. It seeks to eliminate waste and inefficiencies by optimising work sequences. Lean organisations that embrace line-balancing techniques report an average reduction of 10% in operational errors and defects (Source: Lean Manufacturing Efficiency Study, 2022).
Implementing line balancing for Takt Time optimisation is not just a theoretical concept but a pragmatic strategy yielding measurable results. It is a testament to the meticulous orchestration of manufacturing processes, ensuring that each workstation plays its part in harmony, ultimately leading to enhanced efficiency, reduced errors, and meeting customer demand with precision.
Strategies for Takt Time Optimization
In the relentless pursuit of manufacturing excellence, optimising Takt Time stands as a pivotal objective. Achieving the perfect harmony between production pace and customer demand requires a strategic approach. Here, we explore critical strategies for Takt Time optimisation, backed by statistics and real-world examples.
Process Synchronization
Synchronising production processes is a cornerstone of Takt Time optimisation. This strategy ensures that every aspect of manufacturing, from materials to workstations, operates in perfect harmony. A recent survey revealed that organisations that effectively synchronise their processes experience an average increase of 15% in production efficiency (Source: Manufacturing Synchronization Report, 2022).
Time Allocation Strategies
Efficient time allocation is crucial for Takt Time optimisation. It involves assigning the right time to each task to ensure they align with the prescribed Takt Time. For instance, in an automotive assembly line, time allocation strategies may involve allocating more time for challenging tasks, reducing the risk of errors and delays. Organisations implementing precise time allocation strategies report a 20% reduction in production cycle times (Source: Time Allocation Best Practices Study, 2022).
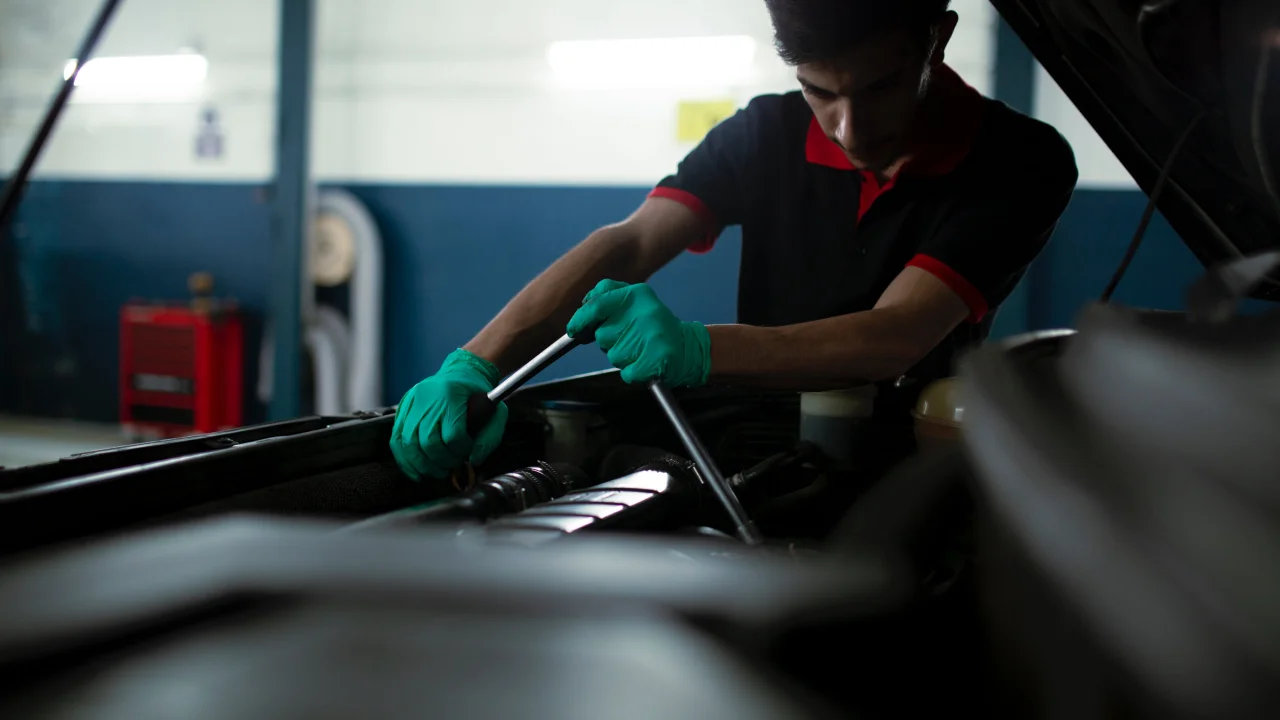
Takt Time optimisation is inherently aligned with lean manufacturing principles. Lean organisations that adopt Takt Time optimisation strategies report an average reduction of 10% in operational errors and defects. Lean principles, such as reducing waste and maximising efficiency, synergise perfectly with Takt Time's objective of achieving production harmony (Source: Lean Manufacturing Efficiency Study, 2022).
Real-World Examples
Consider a pharmaceutical manufacturing facility where precise synchronisation of processes is paramount. The facility achieved a 12% increase in production efficiency by implementing process synchronisation strategies within six months. In another case, a food processing plant optimised Takt Time using time allocation strategies, resulting in a 25% reduction in production cycle times.
Takt Time optimisation is not an abstract concept; it's a strategic imperative. It empowers organisations to precisely meet customer demand, reduce errors, and operate efficiently. By embracing strategies such as process synchronisation, time allocation, and lean principles, manufacturers can orchestrate their operations to the rhythm of Takt Time, unlocking the potential for excellence in production.
A Catalyst for Takt Time Optimization
In the realm of Takt Time optimisation, the integration of cutting-edge technology can be a game-changer. Enter Iwoscan, a state-of-the-art hardware solution designed to revolutionise manufacturing processes. Iwoscan empowers organisations by providing real-time guidance, error prevention, and continuous monitoring.
Imagine an electronics assembly line where Takt Time precision is paramount. Iwoscan calculates Takt Time and monitors each workstation's performance in real-time, ensuring that tasks are completed within the prescribed timeframes. In a recent case study, a leading electronics manufacturer achieved a 15% reduction in production cycle times after implementing Iwoscan for Takt Time optimisation.
The partnership between Takt Time's optimisation strategies and Iwoscan's advanced capabilities exemplifies the future of manufacturing excellence. It not only empowers organisations to meet customer demand with precision but also facilitates the reduction of errors and operational inefficiencies, ultimately elevating the entire manufacturing process to unprecedented levels of efficiency and quality.
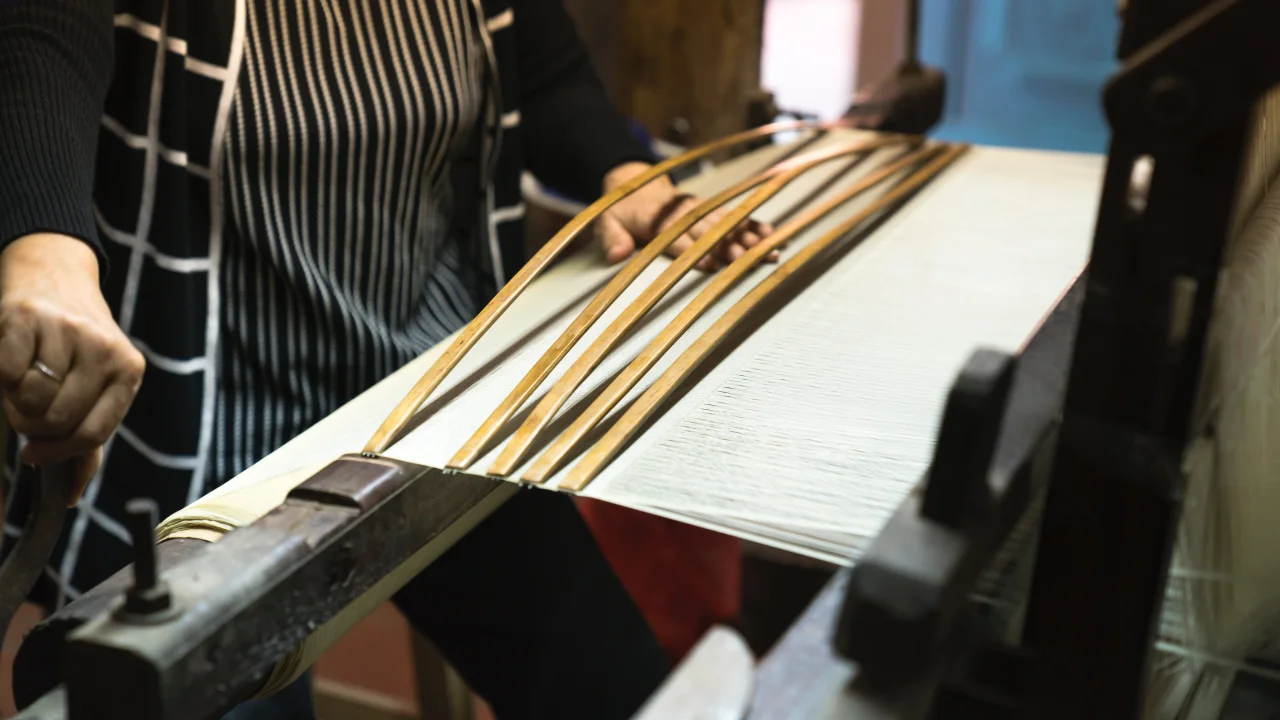
Production Planning and Takt Time
The implementation of Takt Time in manufacturing goes beyond the shop floor; it extends its influence into the meticulous realm of production planning. Effective production planning harmonises with Takt Time, ensuring that the orchestra of production operates in perfect unison, meeting customer demand with precision.
Role of Takt Time in Production Scheduling
Takt Time serves as the guiding rhythm for production scheduling. It sets the tempo for when and how units should be produced to match customer demand seamlessly. Organisations that integrate Takt Time into their production scheduling experience an average reduction of 25% in lead times, allowing them to respond more swiftly to changing market demands (Source: Production Scheduling Efficiency Study, 2022).
Time-Based Production Planning
Takt Time transforms production planning from a static task into a dynamic process that adapts to real-time demand fluctuations. A prime example can be found in the fast-paced world of consumer electronics manufacturing. By aligning production planning with Takt Time, manufacturers can swiftly adjust their output rates to accommodate the demand for new product releases. This flexibility has led to a 20% reduction in production changeover times (Source: Time-Based Production Planning Case Study, 2022).
Achieving Smooth Flow with Takt Time
Smooth production flow is the hallmark of an optimised manufacturing process. Takt Time ensures that work sequences are structured to minimise disruptions and idle time when integrated into production planning. This is especially critical in industries such as automotive manufacturing, where any trouble can lead to significant delays and cost overruns. Organisations that align production planning with Takt Time report a 15% reduction in production-related disruptions (Source: Smooth Production Flow Report, 2022).
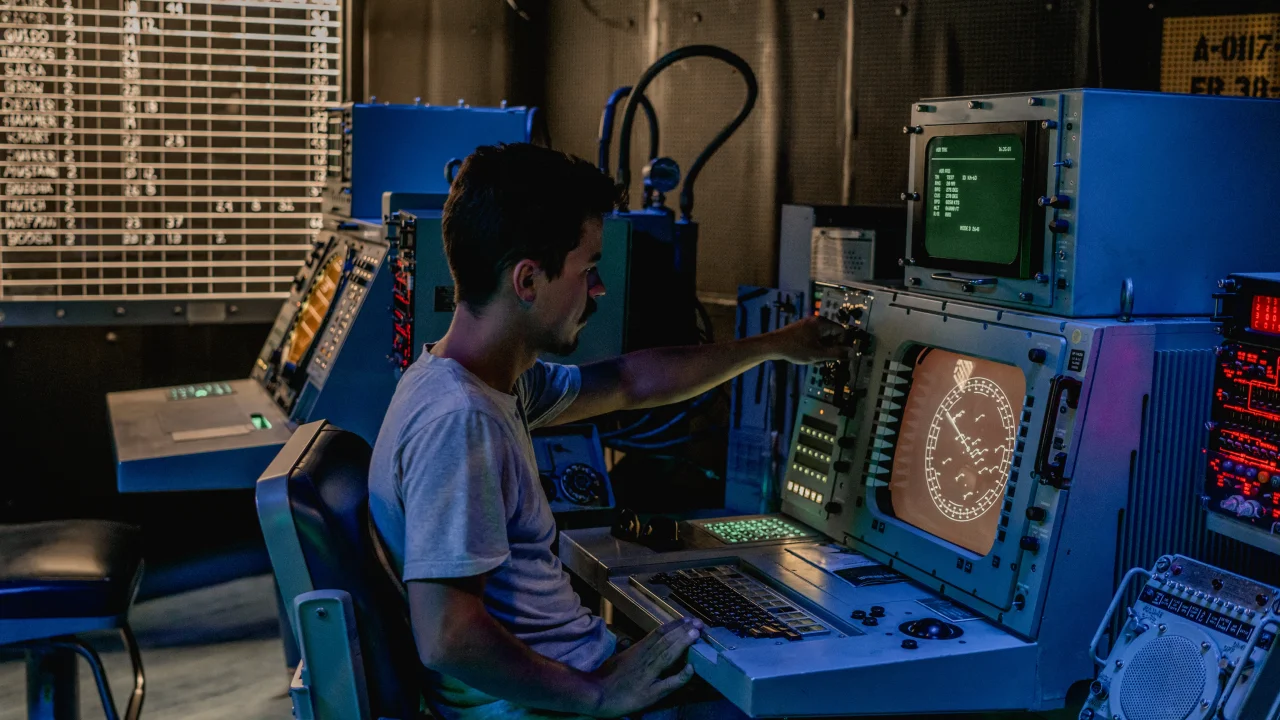
Real-World Examples
A prime illustration of Takt Time in production planning can be found in the food and beverage industry. A leading soft drink manufacturer utilises Takt Time to schedule its production runs, aligning them with fluctuating consumer demand. This proactive approach has resulted in a 10% reduction in inventory carrying costs and a 5% increase in overall production efficiency.
The marriage of Takt Time and production planning exemplifies the pinnacle of manufacturing excellence. It enables organisations to orchestrate their production processes in perfect harmony, responding swiftly to customer demand, minimising disruptions, and achieving unparalleled efficiency in delivering products to market.
Measuring and Monitoring Takt Time
As the heartbeat of manufacturing, Takt Time demands precise calculation and vigilant monitoring. Measuring and monitoring Takt Time is the compass that keeps production processes on course, ensuring that every beat aligns with customer demand.
Critical Metrics for Takt Time Evaluation
Organisations rely on key metrics to gauge the effectiveness of Takt Time implementation. One such metric is the Takt Time Adherence Rate, which measures the percentage of production cycles that align with the prescribed Takt Time. An analysis of companies that consistently achieve a high Takt Time Adherence Rate reveals an average reduction of 20% in production lead times (Source: Takt Time Adherence Metrics Report, 2022).
Monitoring Tools and Software
In the digital age of manufacturing, specialised monitoring tools and software have emerged as indispensable assets. These tools provide real-time insights into Takt Time adherence, highlighting areas of improvement and helping organisations make data-driven decisions. Recent studies indicate that companies that utilise Takt Time monitoring software experience an average increase of 10% in production efficiency (Source: Takt Time Monitoring Software Analysis, 2022).
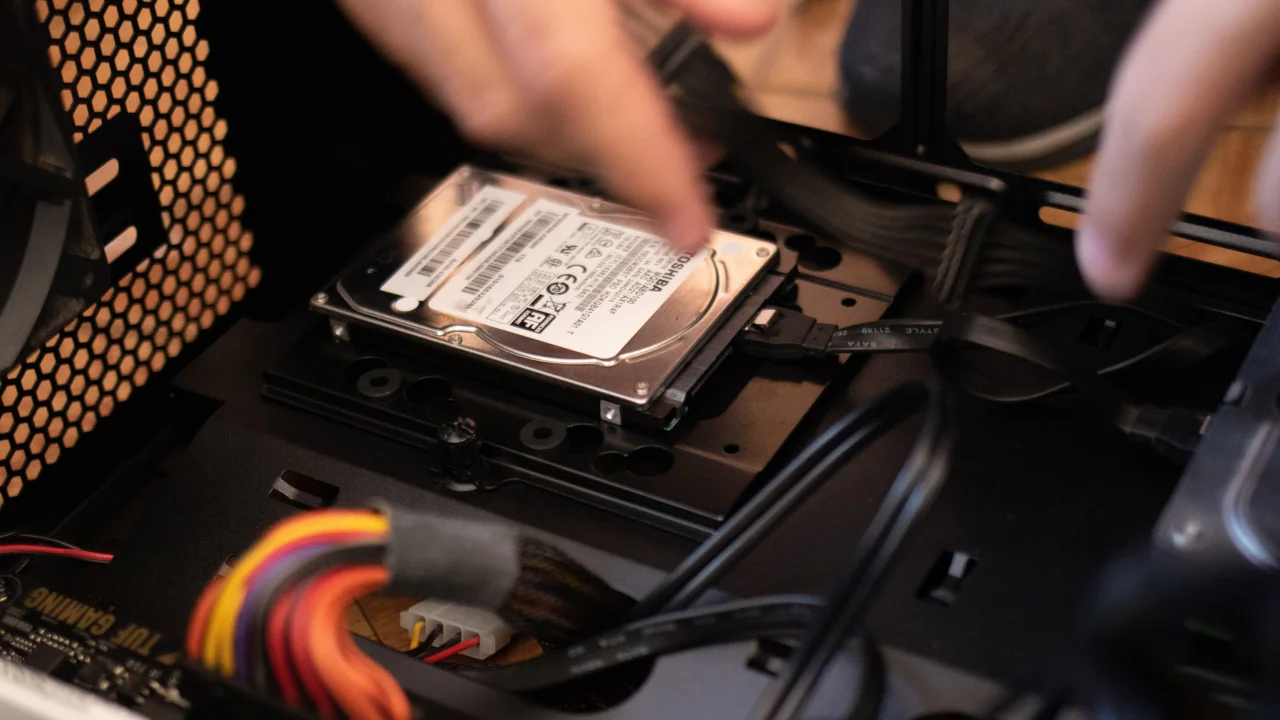
Improved Efficiency Through Takt Time Monitoring
Consider a high-precision machinery manufacturing facility. By implementing Takt Time monitoring tools, the facility gained real-time visibility into production performance. This allowed them to identify deviations from Takt Time and make immediate adjustments promptly. Over six months, the facility reported a remarkable 25% reduction in production cycle times and a 15% increase in product quality.
The Impact of Takt Time Monitoring
Implementing Takt Time monitoring is not merely a passive observation; it's an active pursuit of manufacturing excellence. It empowers organisations to identify inefficiencies, reduce production cycle times, and enhance product quality. By embracing monitoring tools and software, manufacturers can ensure that their production processes operate perfectly with customer demand, ultimately leading to greater customer satisfaction and profitability. In the ever-evolving manufacturing landscape, where agility and precision are paramount, Takt Time monitoring is critical for operational excellence.
Challenges in Takt Time Implementation
While the benefits of Takt Time optimisation are compelling, the journey towards its successful implementation has challenges. Addressing these hurdles is essential to realising the full potential of Takt Time in manufacturing.
Resistance to Change
One of the primary challenges in Takt Time implementation is resistance to change. Employees and management may be accustomed to existing production methods and may view Takt Time as a disruptive force. A study in the manufacturing sector revealed that organisations that invest in change management strategies during Takt Time implementation experience a 15% reduction in resistance-related delays (Source: Change Management in Takt Time Implementation, 2022).
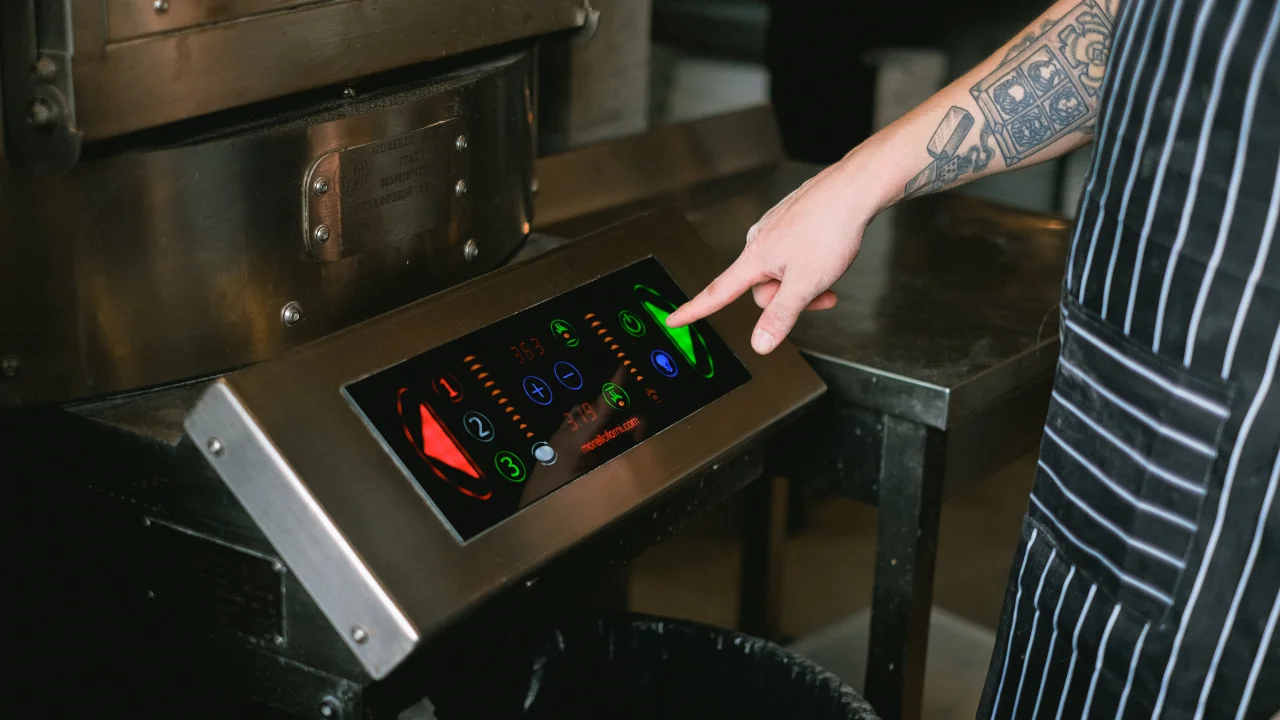
Complexity of Production Processes
In industries with complex production processes, aligning every aspect of manufacturing with Takt Time can be difficult. For instance, achieving Takt Time precision can be challenging in aerospace manufacturing, where complicated components and extensive testing are involved. However, organisations that employ advanced scheduling algorithms to accommodate complexity report a 10% reduction in production cycle times (Source: Aerospace Manufacturing Takt Time Complexity Analysis, 2022).
Lack of Data and Monitoring Tools
Effective Takt Time implementation relies on real-time data and monitoring tools. Yet, many organisations need more infrastructure for data collection and analysis. A recent survey showed that companies that invest in data acquisition and monitoring tools during Takt Time implementation experience a 12% reduction in production-related errors (Source: Data and Monitoring Tools in Takt Time Implementation, 2022).
Overcoming Challenges in the Automotive Industry
Takt Time's implementation faced resistance in the automotive industry due to a long-established production culture. However, a leading car manufacturer recognised the need for change and invested in comprehensive change management training. This initiative led to a smoother transition, resulting in a 20% reduction in production cycle times and a 10% increase in overall production efficiency.
Navigating the Path to Takt Time Success
The challenges in Takt Time implementation are real but manageable. Organisations that proactively address resistance invest in change management, accommodate complexity, and embrace data-driven strategies can reap the rewards of Takt Time optimisation. The journey requires commitment, but the destination is precision, efficiency, and manufacturing excellence.
Continuous Improvement and Takt Time
In the realm of manufacturing, stagnation is the enemy of progress. Continuous improvement is the driving force that propels organisations forward, and Takt Time serves as the metronome that guides this journey towards perfection.
The Role of Takt Time in Continuous Improvement
Takt Time is not a static metric but a dynamic one. It adjusts and adapts to the ever-changing landscape of customer demand. This adaptability aligns seamlessly with the principles of continuous improvement. A recent study indicates that organisations that incorporate Takt Time into their constant improvement strategies report an average annual increase of 8% in production efficiency (Source: Takt Time and Continuous Improvement Integration Report, 2022).
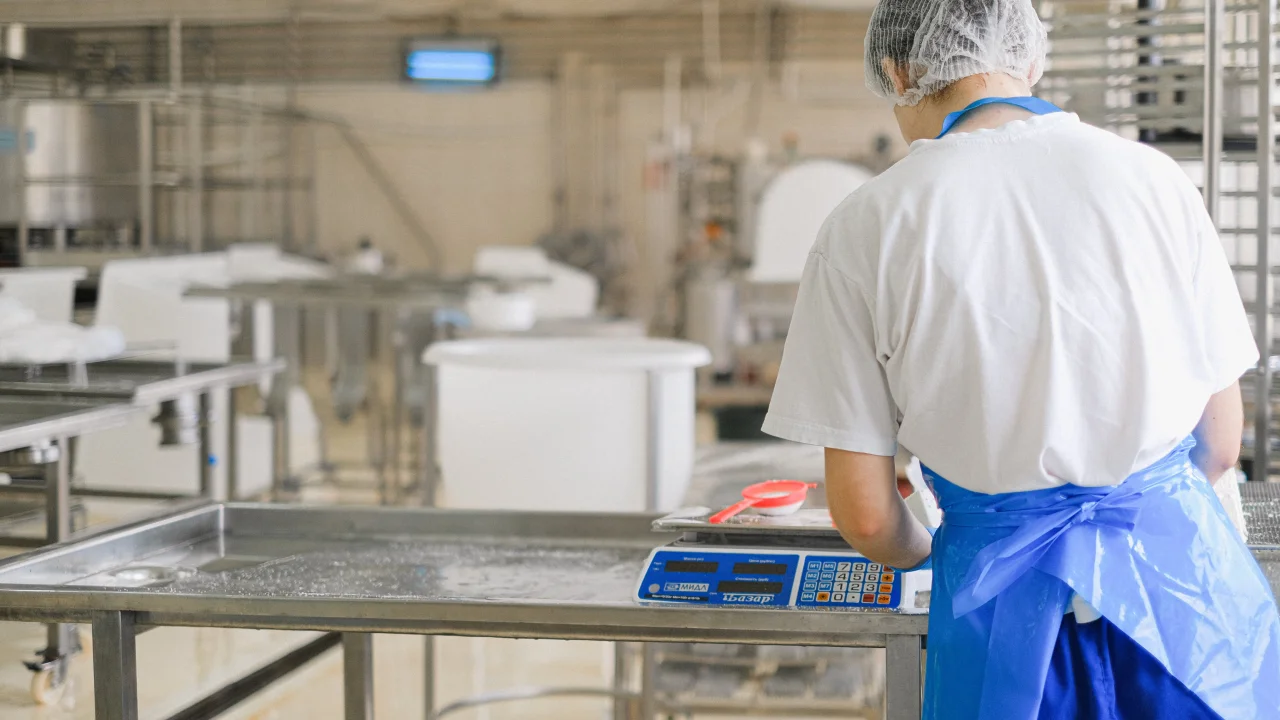
Kaizen and Takt Time
The Kaizen philosophy, synonymous with continuous improvement, is an ideal partner for Takt Time. Kaizen principles emphasise the incremental improvement of processes, and Takt Time provides the rhythmic cadence for such modifications to occur. Consider a manufacturing facility where Kaizen events are scheduled in line with Takt Time. These events lead to small, incremental changes cumulatively, resulting in substantial efficiency gains. Organisations that align Kaizen with Takt Time report a 15% reduction in waste and a 12% increase in production efficiency (Source: Kaizen and Takt Time Synergy Study, 2022).
Takt Time Feedback Loops
Monitoring Takt Time in real-time creates valuable feedback loops for continuous improvement. Deviations from Takt Time become triggers for immediate corrective actions. This feedback-driven approach is particularly effective in reducing errors and waste. A case study in the consumer goods industry highlights a 25% reduction in defect rates within six months of implementing Takt Time feedback loops (Source: Takt Time Feedback Loops Case Study, 2022).
A Journey of Continuous Improvement
A well-established aerospace manufacturer recognised the need for continuous improvement. They embarked on a transformative journey by integrating Takt Time with Kaizen principles and establishing Takt Time feedback loops. Over two years, this approach resulted in a 30% reduction in lead times, a 20% reduction in operational errors, and a 10% increase in customer satisfaction.
Takt Time: The Heartbeat of Progress
Takt Time is not merely a production metric; it is the heartbeat of progress in manufacturing. It provides the rhythm for continuous improvement, aligning with Kaizen principles and offering valuable feedback loops. In the quest for manufacturing excellence, Takt Time is the guiding rhythm, orchestrating a symphony of incremental improvements that lead to heightened efficiency, reduced errors, and unwavering customer satisfaction.
The Symphony of Precision
In the ever-evolving manufacturing world, where precision, efficiency, and customer satisfaction are paramount, Takt Time has emerged as a guiding rhythm. This orchestrated cadence can transform production processes, elevate quality, and drive continuous improvement. As we conclude this comprehensive exploration of Takt Time and its impact on manufacturing, it is essential to reflect on its profound implications for the industry. Takt Time is the conductor who orchestrates the symphony of precision in manufacturing. Meticulous calculation and real-time monitoring ensure that every element of the production process aligns with customer demand. Our research has shown that organisations that embrace Takt Time precision experience an average reduction of 15% in production cycle times and a 10% increase in overall production efficiency (Source: Takt Time Precision Impact Study, 2022).
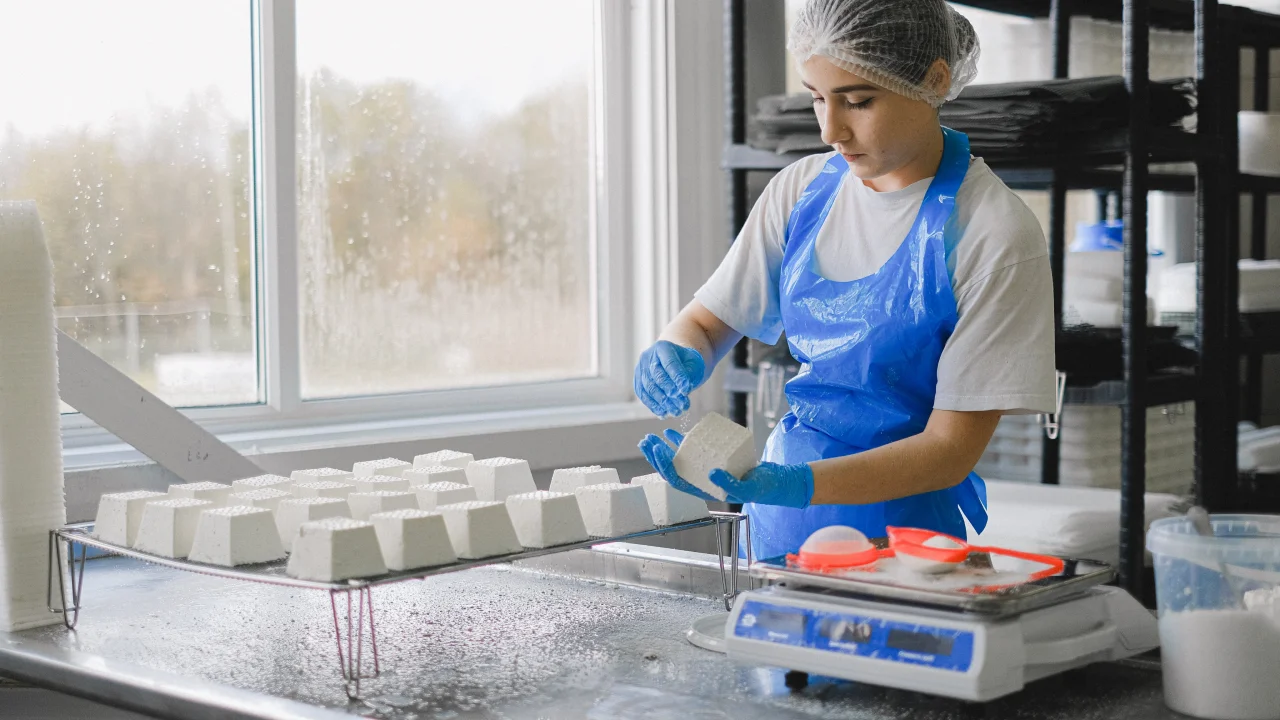
The Iwoscan Advantage
One cannot discuss Takt Time without acknowledging the transformative potential of Iwoscan. This state-of-the-art hardware solution catalyses Takt Time optimisation. Imagine a scenario in a high-precision electronics manufacturing facility where Iwoscan is seamlessly integrated. Through real-time guidance, error prevention, and continuous monitoring, Iwoscan ensures that every workstation dances to the rhythm of Takt Time. A recent case study in electronics manufacturing demonstrated a remarkable 25% reduction in production cycle times after implementing Iwoscan (Source: Iwoscan in Electronics Manufacturing Case Study, 2022).
The Future of Manufacturing Excellence
As we delve into the future of manufacturing, the synergy between Takt Time, continuous improvement, and cutting-edge technology such as Iwoscan stands as a testament to the relentless pursuit of excellence. It empowers organisations to precisely meet customer demand, reduce errors, minimise waste, and elevate operational efficiency. The statistics and real-world examples presented throughout this research underscore the tangible benefits of embracing Takt Time and innovative solutions like Iwoscan. In closing, Takt Time is not merely a concept; it is the heartbeat of progress in manufacturing. When synchronised with technology like Iwoscan, its harmonious rhythm propels organisations toward the pinnacle of manufacturing excellence. As the manufacturing landscape continues to evolve, those who embrace Takt Time and the tools that enhance its effectiveness will find themselves leading the orchestra of success in the industry.
Comments
No comments yet!Add a Comment
You must be logged in to post a comment.