In an era where our planet faces unprecedented environmental challenges, the call for sustainable manufacturing has never been more urgent. The global manufacturing landscape stands at a crossroads where our decisions will profoundly impact the world we leave for future generations. At the heart of this transformative journey lie two inseparable cornerstones: Efficiency and Effectiveness.
Sustainable manufacturing isn't merely a buzzword but a fundamental shift in industries' operations. It's a paradigm that reimagines the very essence of production, focusing not just on profits but on a harmonious coexistence with the environment. Efficiency and effectiveness serve as guiding principles in this profound transformation.

Efficiency, in the context of sustainable manufacturing, isn't solely about maximising output while minimising input. It's a multifaceted concept encompassing reducing waste, conserving resources, and optimising energy use. An efficient manufacturing process ensures that every resource – from raw materials to energy – is utilised judiciously, leaving a minimal ecological footprint.
Effectiveness, on the other hand, is about crafting products and processes that deliver sustainable outcomes. It's about selecting eco-friendly materials, designing products with recyclability in mind, and minimising the environmental impact throughout a product's lifecycle. Effectiveness means creating lasting solutions that address not only consumers' immediate needs but also, in this blog, the planet's long-term; we will delve deep into the symbiotic relationship between efficiency and effectiveness in sustainable manufacturing. We will explore how these cornerstones drive innovation, reduce waste, and mitigate the environmental impact of production processes. We'll also examine the synergy between the two, showcasing real-world examples of companies that have harnessed their power to forge a sustainable future.
Join us on this journey through the intricate tapestry of sustainable manufacturing, where efficiency and effectiveness are not just principles but guiding lights illuminating the path towards a greener, more responsible industrial landscape. Together, we will unravel the strategies, challenges, and aspirations that define the future of manufacturing, which is efficient, environmentally conscious, and sustainable.
Sustainability is a necessity
In the ever-evolving manufacturing landscape, sustainability is no longer an option but a necessity. Sustainable manufacturing reduces environmental impact, optimises resources, enhances quality, and improves efficiency and effectiveness. In this blog post, we'll delve into the importance of efficiency and effectiveness in manufacturing and how it emerges as a sustainable solution to address the challenges faced by factories while aligning with key industry keywords.
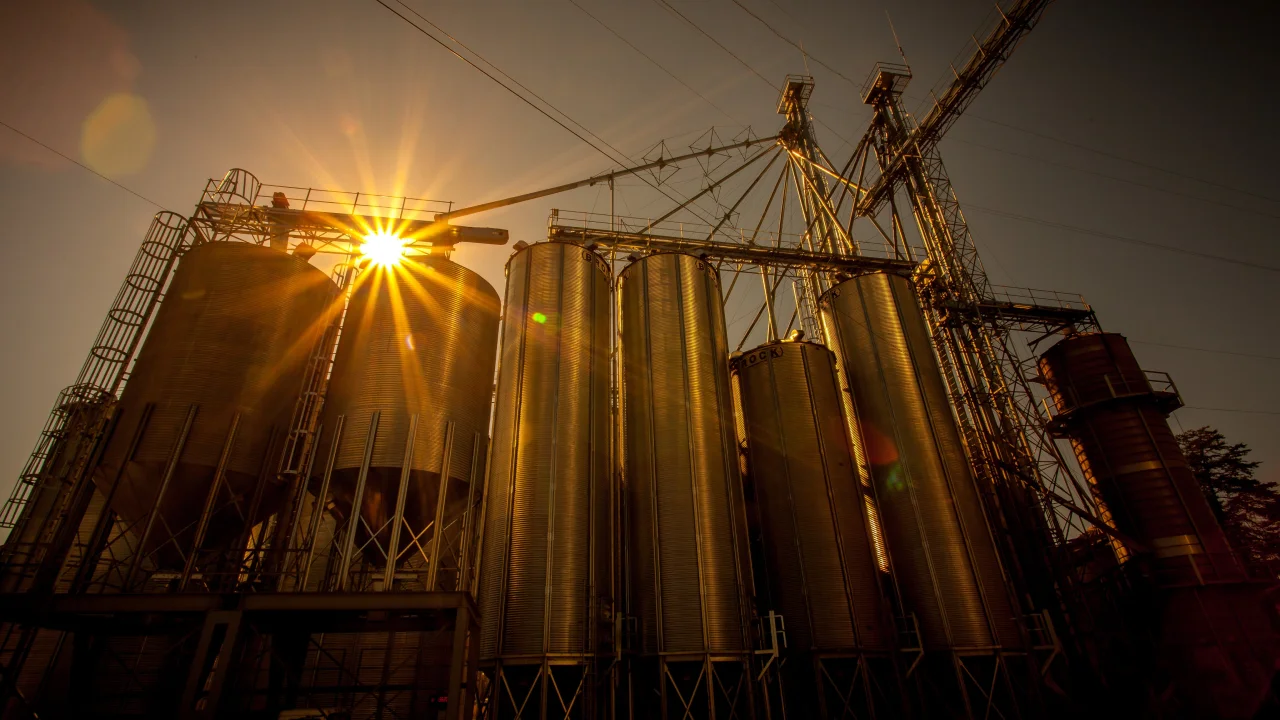
Efficiency in manufacturing refers to achieving maximum output with minimal inputs. It encompasses reducing waste, improving processes, and optimising resource utilisation. On the other hand, effectiveness involves consistently achieving the desired outcomes or quality standards. Sustainable manufacturing requires a delicate balance between these two aspects.
Quality Assurance and Control
Quality assurance and control are integral parts of sustainable manufacturing. Factories must maintain stringent quality standards to reduce defects and minimise waste. A comprehensive Quality Management System (QMS) is crucial. Iwoscan integrates seamlessly with QMS to streamline quality assurance processes and collect real-time data for immediate corrective actions.
Overall Equipment Effectiveness (OEE)
OEE is a critical metric that measures the efficiency of production equipment. It takes into account factors such as availability, performance, and quality. Iwoscan aids in OEE calculation, enabling factories to identify bottlenecks, reduce downtime, and maximise machine utilisation. This is pivotal for sustainable manufacturing.
Takt Time and Downtime Detection
Takt time ensures that production processes align with demand, preventing overproduction or underproduction. Iwoscan helps factories monitor takt time and identifies any deviations. It acts as a downtime detector, instantly flagging issues that may lead to reduced efficiency, thus ensuring optimal use of resources.
Employee Engagement and Time Management
Engaged employees are more likely to contribute to sustainable manufacturing. Iwoscan facilitates employee monitoring and employee time management, ensuring that workers are focused and productive. This employee engagement aligns with the 7 Quality Management Principles, fostering a culture of continuous improvement.
Equipment Maintenance and Defect Detection
Proactive equipment maintenance is essential for preventing unplanned downtime and defects. Iwoscan provides insights into equipment performance, helping factories schedule maintenance activities. It also aids in manufacturing defect detection and tracking, ensuring that quality remains consistent.
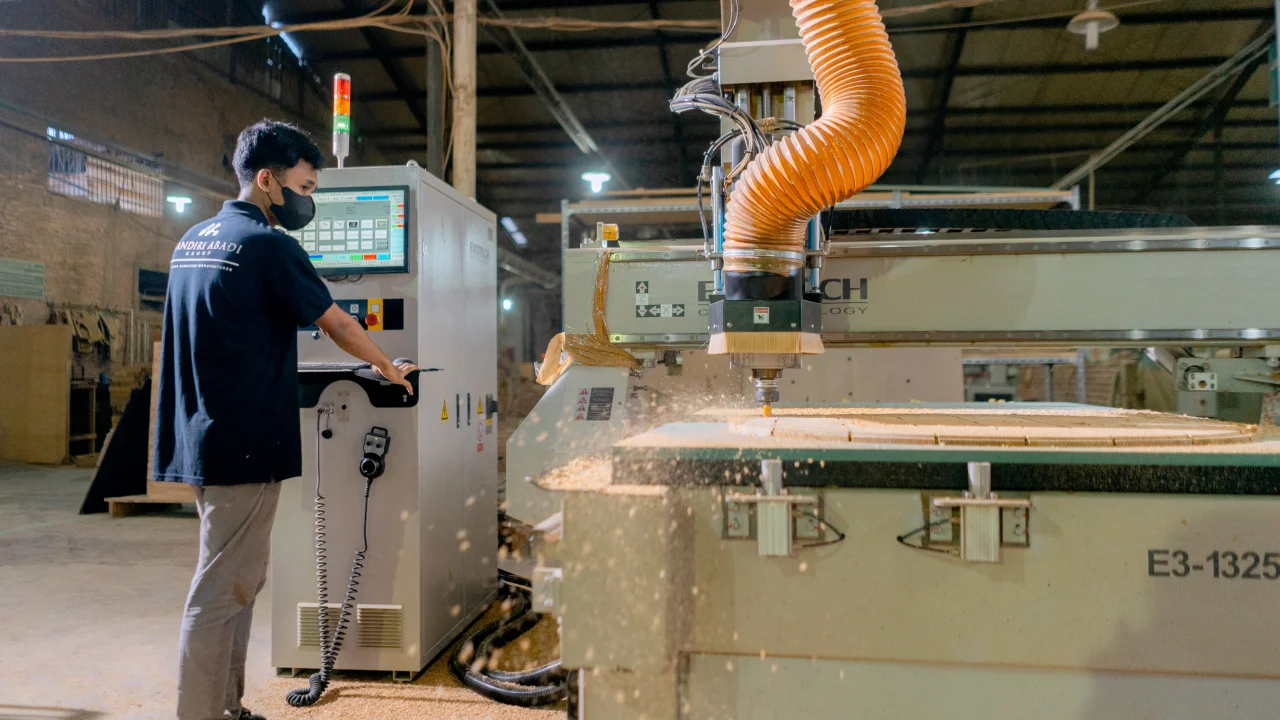
Manufacturing Line Efficiency
Efficient production lines are crucial for sustainability. Iwoscan identifies bottlenecks and inefficiencies, promoting smoother operations and higher product quality. This contributes to manufacturing line efficiency, a critical factor in sustainable manufacturing.
Iwoscan as the Sustainable Solution
Iwoscan isn't just a tool; it's a comprehensive quality management solution. It aligns with total quality management principles, ensuring factories maintain high-quality standards. Its real-time data collection and analysis capabilities empower factories to make data-driven decisions, further enhancing sustainability.
In conclusion, sustainable manufacturing isn't merely an ideal; it's an imperative for the modern factory. Efficiency, effectiveness, and quality assurance are paramount in achieving sustainability goals. Iwoscan, with its ability to address quality control and quality assurance challenges, optimise OEE, and improve overall efficiency, emerges as a solution that aligns with these goals and propels factories toward a more sustainable and prosperous future in the manufacturing landscape. Embrace Iwoscan today and embark on your journey towards sustainable manufacturing excellence.
The Significance of Sustainable Manufacturing
The significance of sustainable manufacturing cannot be overstated in a world grappling with the profound challenges of climate change, resource depletion, and environmental degradation. As industrialisation continues to shape the global landscape, the impact of manufacturing on our planet has never been more pronounced. This is precisely why sustainable manufacturing stands as a beacon of hope and a critical pillar in addressing these pressing issues.
Addressing Environmental Challenges
One of the most pressing concerns facing humanity today is the degradation of our environment. Carbon emissions, deforestation, and pollution have placed immense stress on ecosystems, leading to climate change, biodiversity loss, and the depletion of vital resources. Sustainable manufacturing presents a viable solution to mitigate these challenges. Industries can significantly reduce their negative environmental footprint. By adopting eco-friendly practices, reducing greenhouse gas emissions, and minimising waste.
Meeting Consumer Demand for Sustainability
Consumers worldwide are increasingly conscious of the product's environmental and social impact. Sustainable manufacturing aligns with consumer preferences for ethically produced, eco-friendly goods. Companies that embrace sustainably appeal to a growing market also enhance brand reputation and customer loyalty.
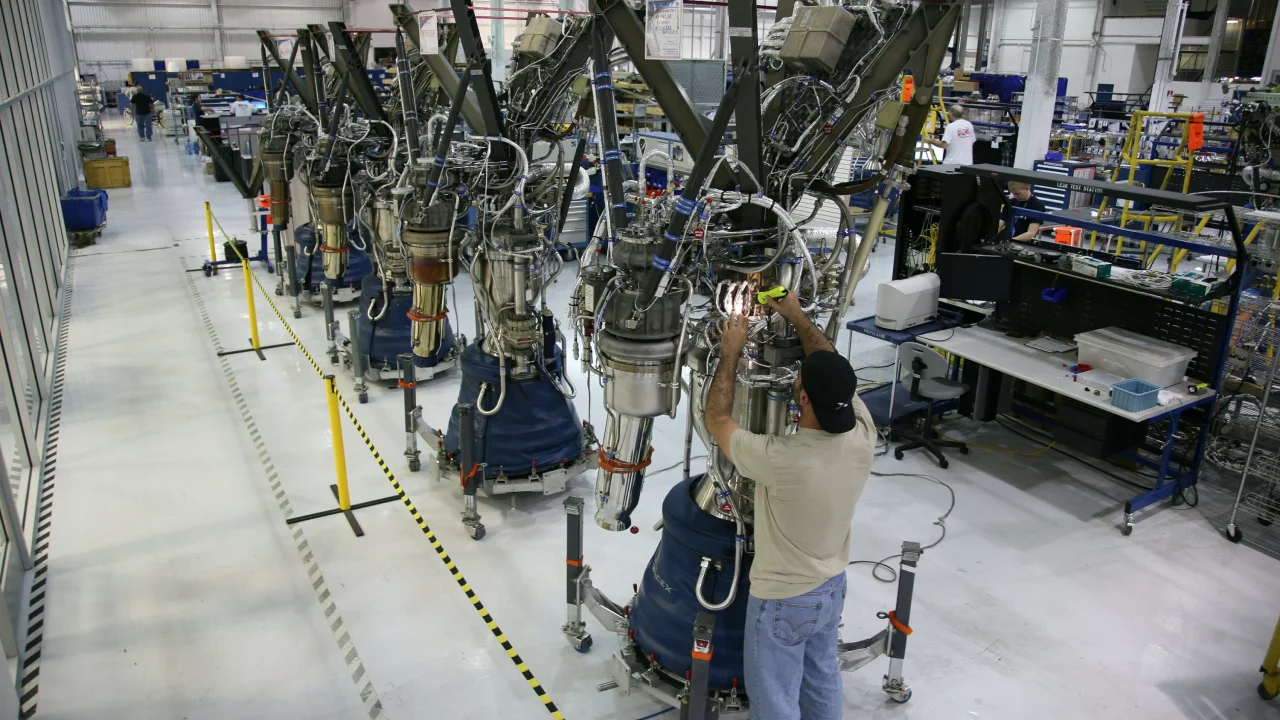
Regulatory and Legal Imperatives
Governments and international organisations are enacting stringent regulations and standards to promote sustainable practices in manufacturing. Non-compliance can result in fines, legal actions, and reputational damage. Embracing sustainable manufacturing is not just a choice but an imperative for businesses to thrive in a changing regulatory landscape.
Resource Efficiency and Cost Savings
Sustainable manufacturing isn't solely about environmental stewardship; it also makes good business sense. Efficiency measures such as waste reduction, energy optimisation, and responsible resource management translate into cost savings. By minimising resource waste, companies can improve their bottom line while reducing their ecological impact.
Long-Term Viability
The traditional, linear production model (take, make, dispose) is no longer tenable in a world with finite resources. Sustainable manufacturing, with its emphasis on circular economy principles and responsible product lifecycle management, ensures the long-term viability of industries. It enables the creation of products designed for durability, repairability, and recycling, thus reducing the need for resource-intensive replacements.
In essence, sustainable manufacturing is not a choice but a necessity. It represents a paradigm shift towards responsible, environmentally friendly, and economically viable industrial practices. In the subsequent sections of this blog post, we will delve into the key component underpinning sustainable manufacturing, focusing on the pivotal role of efficiency and effectiveness in this transformative journey.
Efficiency in Sustainable Manufacturing
Efficiency lies at the very core of sustainable manufacturing. It's not just about producing more with less; it's about reimagining the entire production process to minimise waste, maximise resource utilisation, and reduce environmental impact. In this section, we'll delve deep into the significance of efficiency in sustainable manufacturing.
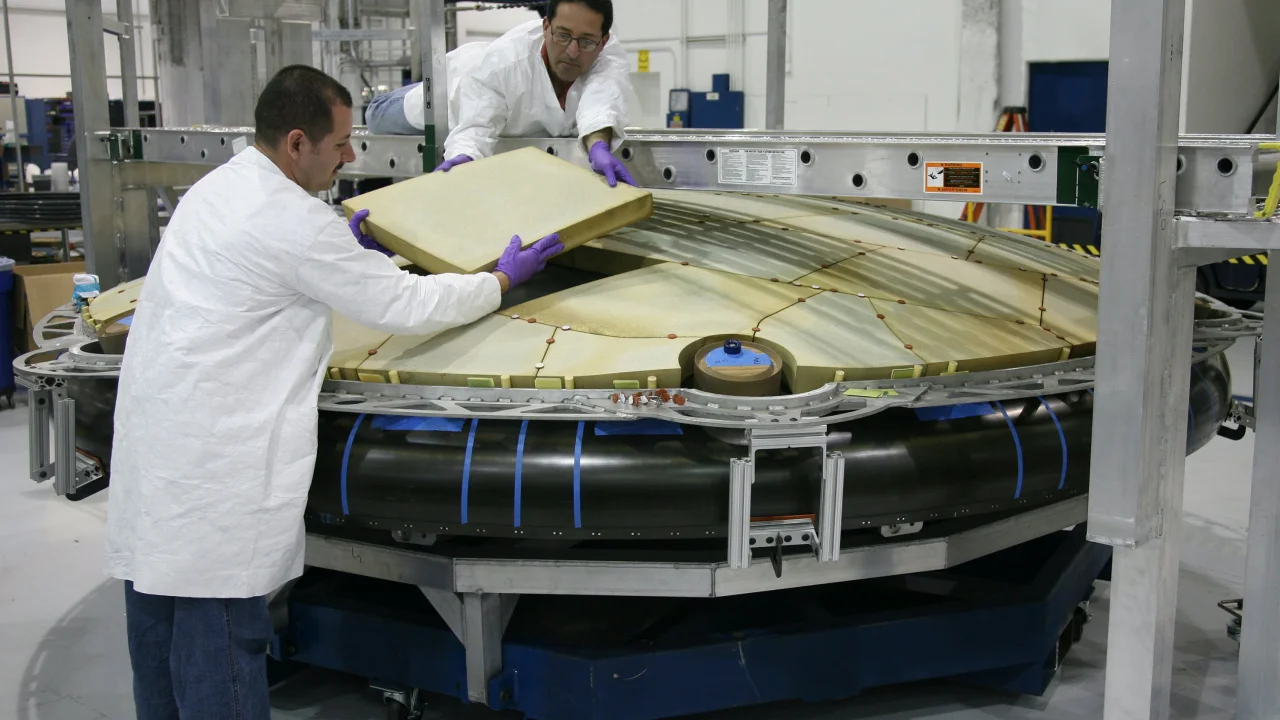
Reducing Resource Consumption
One of the primary goals of sustainable manufacturing is to reduce the consumption of finite resources such as water, raw materials, and energy. Efficiency measures like advanced manufacturing technologies, optimised supply chains, and lean production methodologies enable companies to do more with less. For instance, energy-efficient machinery consumes fewer resources while maintaining or even improving production output.
Minimising Waste Generation
Waste is not just a financial burden for businesses; it also contributes to environmental degradation. Sustainable manufacturing focuses on waste minimisation through practices like recycling, reusing, and repurposing materials. Waste reduction strategies save resources and decrease disposal costs and environmental pollution.
Lowering Carbon Footprint
Manufacturing significantly contributes to greenhouse gas emissions through energy consumption and transportation. Sustainable manufacturing employs energy-efficient technologies, renewable energy sources, and emission-reduction strategies to lower carbon footprints. By transitioning to cleaner energy sources and optimising energy use, companies can contribute substantially to climate mitigation.
Enhancing Productivity and Quality
Efficiency improvements often lead to increased productivity and product quality. When processes are streamlined, products are manufactured with fewer defects and production times are reduced. It reduces resource waste and enhances a company's competitiveness in the market.
Resource Recovery and Reuse
Efficiency is more than conserving resources and finding innovative ways to recover and reuse materials within the production cycle. Closed-loop manufacturing systems, for example, enable companies to recycle and repurpose materials, reducing the need for virgin resources and minimising waste.
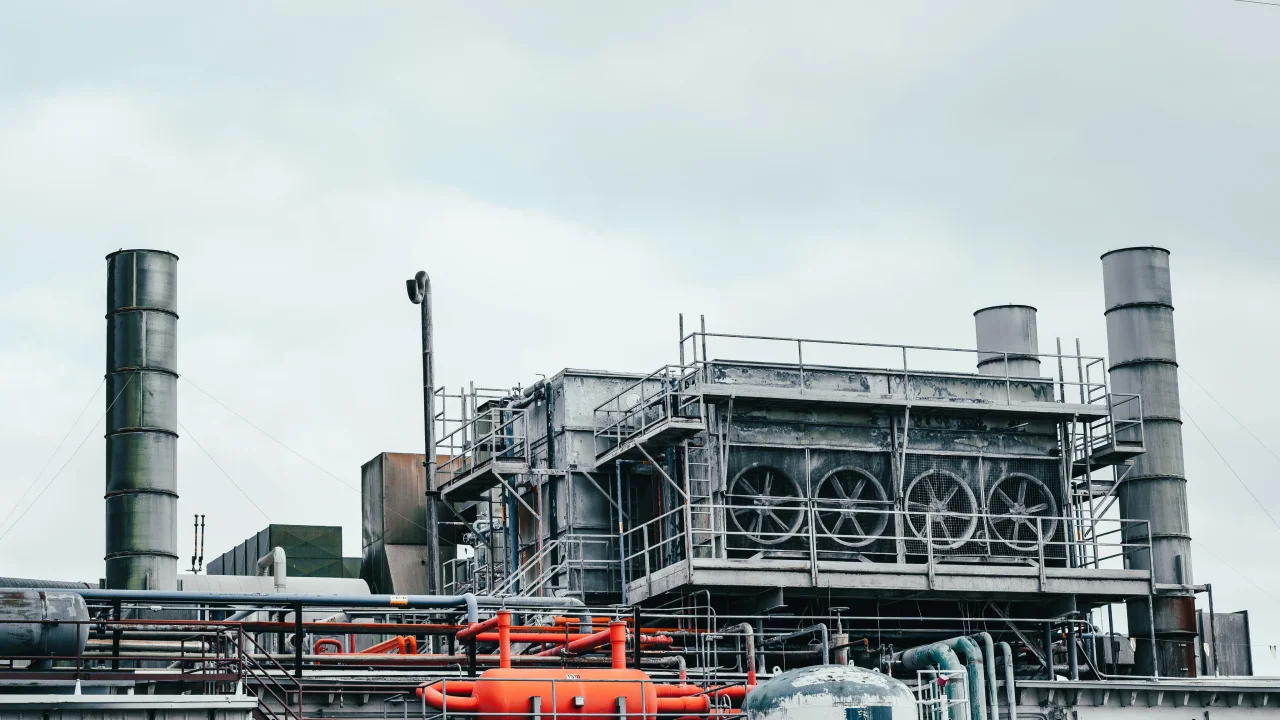
Lean Manufacturing Principles
Lean manufacturing is a cornerstone of efficiency in sustainable manufacturing. It focuses on eliminating waste in all forms, be it overproduction, excess inventory, defects, or underutilised talent. Lean principles ensure the optimisation of every production process, leading to resource savings and enhanced sustainability.
In conclusion, efficiency is not just a buzzword in sustainable manufacturing; it's a fundamental principle that drives positive change. It empowers businesses to thrive in a resource-constrained world while minimising their environmental footprint. As we move forward in this sustainable manufacturing journey, it's clear that efficiency is not an option but a necessity for creating a greener, more sustainable future. In the next section, we'll delve into the complementary concept of effectiveness and its role in sustainable manufacturing.
Effectiveness in Sustainable Manufacturing
While efficiency focuses on doing things right, effectiveness emphasises doing the right things. In sustainable manufacturing, effectiveness is pivotal in ensuring that products and processes are designed with sustainability as a core principle. In this section, we'll explore the significance of effectiveness and its role in sustainable manufacturing.
Designing for Sustainability
At the heart of effectiveness in sustainable manufacturing is product design. Effective design means creating products that serve their intended purpose and minimise environmental impact. This involves selecting eco-friendly materials, reducing hazardous substances, and designing products with recyclability and longevity. Effective design decisions influence a product's entire lifecycle, from manufacturing to disposal or recycling.
Responsible Materials Selection
Effectiveness in sustainable manufacturing extends beyond product design to the selection of materials. Companies must assess the environmental and social impacts of the materials they use. Sustainable sourcing of raw materials, including consideration of factors like ethical labour practices and fair trade, is a crucial component of effectiveness.
Minimising Environmental Footprint
Effectiveness seeks to minimise the environmental footprint of manufacturing processes. This includes reducing emissions, energy consumption, and water usage. Effective procedures are those that, when compared to conventional methods, result in significantly lower environmental impact while maintaining or improving production efficiency.
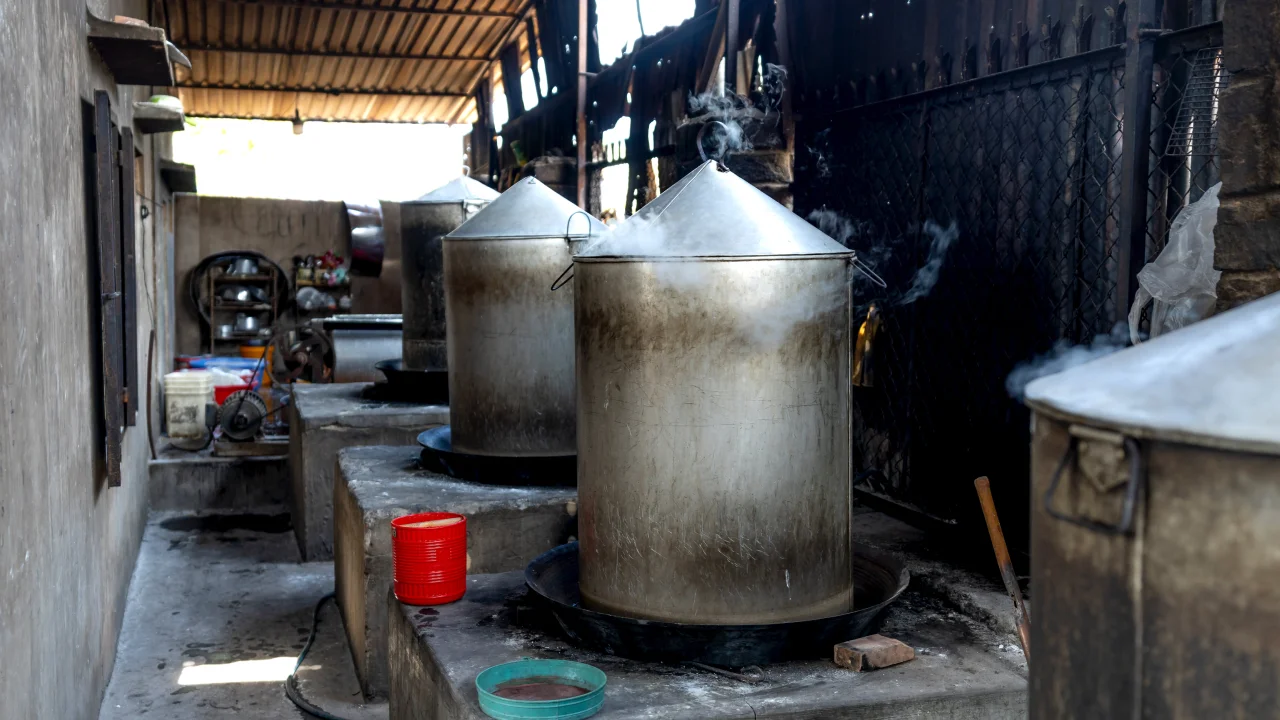
Product Lifecycle Management
Managing a product's entire lifecycle is an essential aspect of effectiveness in sustainable manufacturing. This involves planning for product reuse, recycling, or responsible disposal at the end of its useful life. By ensuring that products can be safely and efficiently dismantled or recycled, manufacturers reduce waste and contribute to a circular economy.
Circular Economy Principles
Effectiveness aligns closely with the principles of the circular economy, where products and materials are kept in use for as long as possible. This concept involves strategies like remanufacturing, refurbishing, and recycling, which reduce the demand for new raw materials and minimise waste.
Sustainable Supply Chain
Effectiveness in sustainable manufacturing extends beyond the factory floor to encompass the entire supply chain. It involves evaluating suppliers' environmental and ethical practices, promoting responsible sourcing, and collaborating with partners committed to sustainability.
Regulatory Compliance and Certifications
Companies prioritising effectiveness in sustainable manufacturing often seek certifications and compliance with sustainability standards. These certifications, such as ISO 14001 for environmental management systems, demonstrate a commitment to effective sustainability practices.
In essence, effectiveness in sustainable manufacturing is about making informed, responsible decisions at every stage of product development and production. It's about ensuring the choices align with long-term sustainability goals and contribute to a healthier planet and society. The following sections examine how efficiency and effectiveness work in synergy to create a more sustainable manufacturing landscape.
Synergy Between Efficiency and Effectiveness
Efficiency and effectiveness are not isolated concepts in sustainable manufacturing; they are intricately interwoven, creating a powerful synergy that drives positive change on multiple fronts. This section will explore the symbiotic relationship between these cornerstones and how they work together to enhance sustainability.
Waste Reduction and Resource Optimization
Efficiency measures, such as lean manufacturing and process optimisation, lead to a reduction in resource waste. When processes are streamlined, and resources are used judiciously, less material ends as waste, aligning with effectiveness principles. This waste reduction conserves resources and reduces disposal costs and environmental impact.
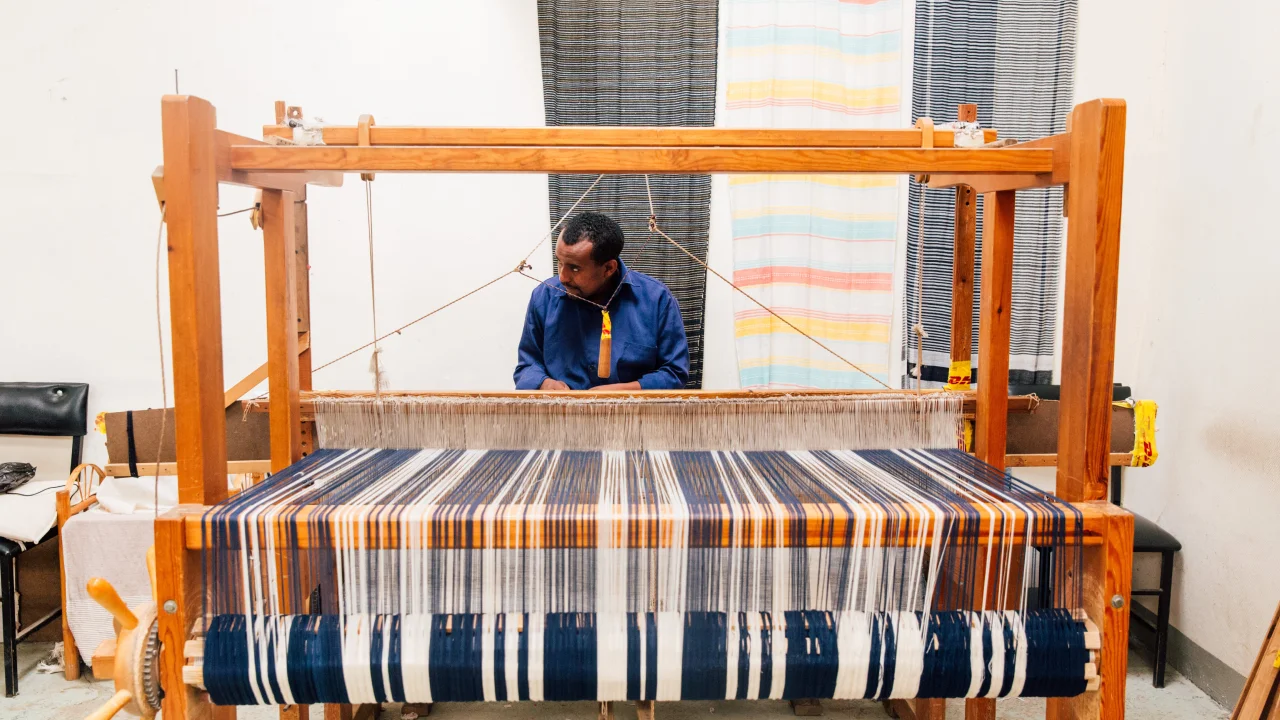
Energy Efficiency and Carbon Reduction
Efficiency strategies like energy-efficient machinery and improved process control contribute directly to carbon footprint reduction. Manufacturers can lower their greenhouse gas emissions by using less energy for the same or increased output. This aligns seamlessly with the effectiveness goal of minimising environmental impact.
Product Design and Materials Efficiency
Effective product design, emphasising eco-friendly materials and recyclability, complements efficiency by reducing the environmental footprint of products. Efficient manufacturing processes support these efforts using fewer materials and energy during production. Together, these strategies result in products that are both sustainable and resource-efficient.
Lean Manufacturing and Effective Resource Allocation
Lean manufacturing principles, which focus on eliminating waste and improving production processes, are inherently effective and efficient. Companies achieve sustainability goals by reducing excess inventory, streamlining workflows, and optimising resource allocation while improving their bottom line.
Cost Savings and Sustainability Investments
Efficiency measures often lead to cost savings, which can be reinvested in sustainability initiatives. These investments in effective sustainability practices, such as responsible materials sourcing or product design improvements, further enhance a company's environmental and social impact.
Circular Economy and Waste Reduction
The circular economy, a concept deeply rooted in effectiveness, aims to keep products and materials in use for as long as possible. Efficiency measures that reduce waste and extend the life of products align seamlessly with the circular economy's principles, creating a win-win scenario for sustainability.
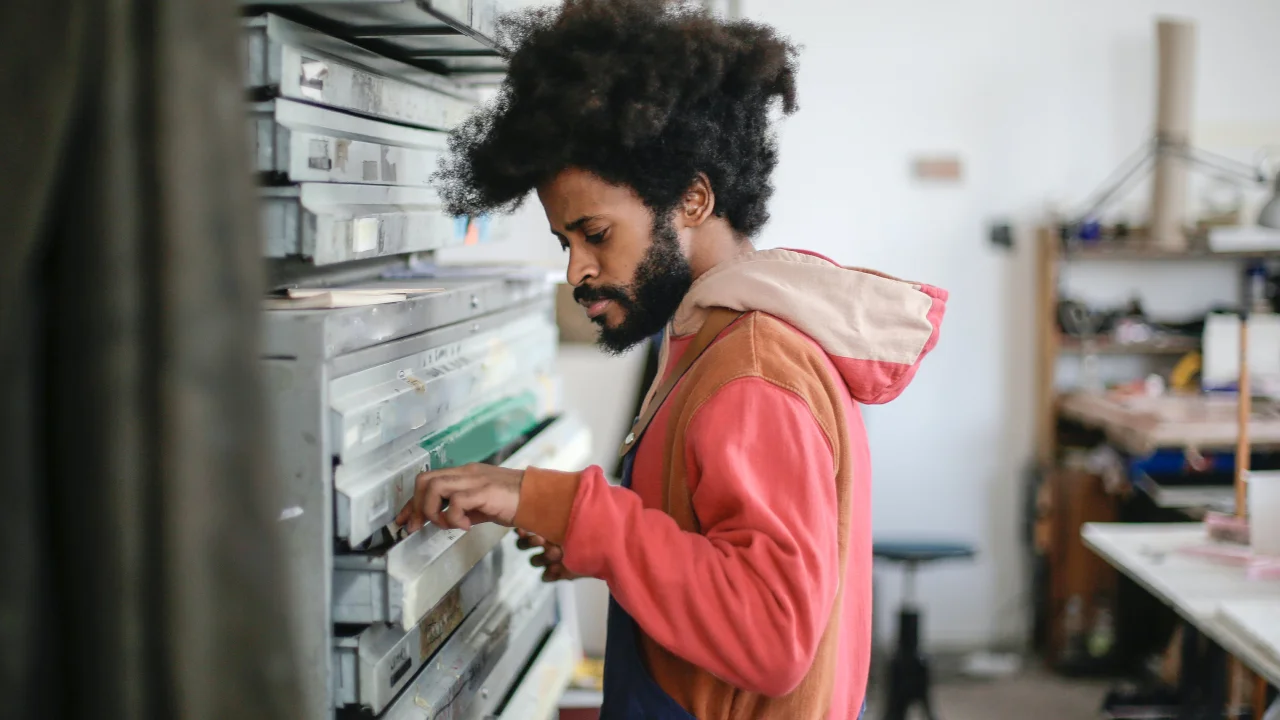
Continuous Improvement
Both efficiency and effectiveness promote a culture of continuous improvement. Both concepts are fundamental to regular assessments, data-driven decision-making, and a commitment to optimising processes and products—this ongoing pursuit of excellence results in sustainable manufacturing practices that evolve and adapt to changing circumstances.
In summary, the synergy between efficiency and effectiveness is the driving force behind sustainable manufacturing. It enables companies to navigate the complex environmental and social responsibility landscape while improving their operations and competitiveness. As we move forward, it becomes increasingly clear that these cornerstones are not just essential but inseparable in building a sustainable future for manufacturing.
Sustainable Manufacturing Metrics
In sustainable manufacturing, measurement is not just a tool for assessing performance; it's a compass guiding organisations toward their sustainability goals. Businesses must employ key metrics and indicators to manage and improve sustainable practices effectively. This section will explore the significance of sustainable manufacturing metrics and their role in driving progress.
Why Metrics Matter
Metrics serve as the foundation of any meaningful sustainability initiative. They provide a quantifiable means of tracking progress, identifying areas for improvement, and demonstrating the impact of sustainability efforts on stakeholders. With reliable metrics, sustainable manufacturing goals are attainable and easier to validate.
Key Sustainable Manufacturing Metrics
Several key metrics are central to assessing and enhancing sustainable manufacturing practices.
Energy Efficiency |
Measuring energy consumption per unit of production or product is crucial. Lowering this metric indicates improved energy efficiency and reduced environmental impact. |
Water Usage |
Monitoring water consumption and wastewater discharge helps identify water conservation and pollution prevention opportunities. |
Waste Generation and Diversion |
Measuring the amount of waste generated and the percentage diverted from landfills reveals the effectiveness of waste reduction and recycling efforts. |
Carbon Footprint |
Calculating greenhouse gas emissions associated with manufacturing processes provides insight into a company's contribution to climate change. Reduction in emissions signifies progress in carbon footprint reduction. |
Resource Utilization |
Metrics related to the efficient use of raw materials and resources, including material efficiency ratios and resource consumption per unit of output, highlight resource optimisation. |
Supply Chain Sustainability |
Assessing supplier performance, ethical sourcing, and supply chain transparency is essential for evaluating the sustainability of the entire value chain. |
Product Lifecycle Assessment (LCA) |
LCA analyses the environmental impact of a product from raw material extraction to disposal. It aids in making informed design and production decisions. |
Social Responsibility Metrics |
Metrics related to fair labour practices, worker safety, and community engagement measure a company's commitment to social responsibility. |
Data-Driven Decision-Making
Metrics provide manufacturers with actionable data. By regularly collecting and analysing data, businesses can identify inefficiencies, pinpoint areas for improvement, and make informed decisions to drive sustainability initiatives.
Benchmarking and Goal Setting
Metrics also facilitate benchmarking against industry standards and competitors. Setting measurable sustainability goals based on key metrics allows companies to track progress over time and continually raise the bar.
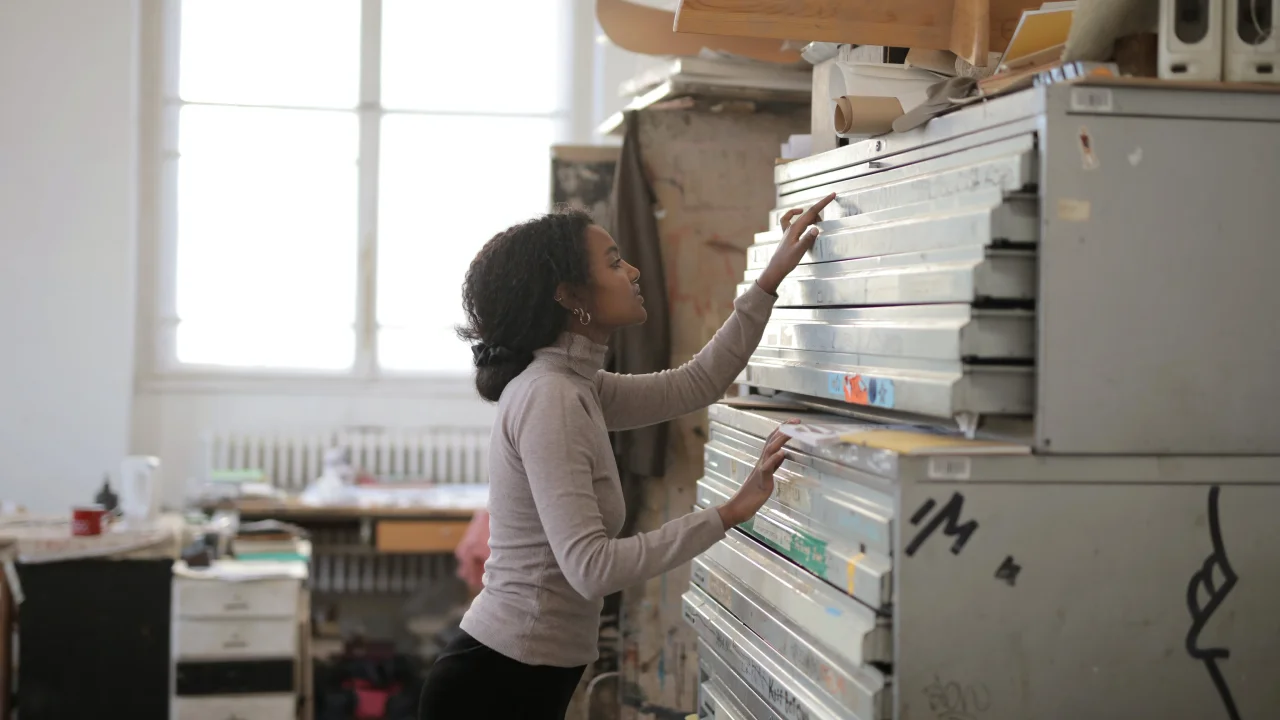
Reporting and Transparency
Transparency is increasingly important to stakeholders, including customers, investors, and regulators. Comprehensive sustainability reports, driven by robust metrics, demonstrate a company's commitment to responsible manufacturing and environmental stewardship.
In conclusion, sustainable manufacturing metrics are not just numbers on a spreadsheet but the compass guiding organisations toward a more sustainable future. They provide the means to quantify progress, identify opportunities for improvement, and align sustainable practices with business objectives. As we move forward in the quest for more responsible manufacturing, metrics will continue to play a central role in shaping the industry's path towards a greener and more sustainable future.
Strategies for Improving Efficiency and Effectiveness
Improving efficiency and effectiveness in sustainable manufacturing requires a deliberate and holistic approach. In this section, we'll explore a range of strategies that companies can employ to enhance their operations while reducing their environmental footprint and creating more sustainable products.
Embrace Lean Manufacturing Principles
Lean manufacturing is a proven strategy for enhancing efficiency and reducing waste. By identifying and eliminating non-value-added activities, optimising processes, and improving resource utilisation, companies can achieve higher efficiency while minimising costs and environmental impact. Lean principles align perfectly with sustainable manufacturing goals, making them a powerful tool for transformation.
Invest in Sustainable Technologies
Adopting cutting-edge technologies can significantly improve efficiency and effectiveness in manufacturing. Automation, robotics, and data analytics can streamline production processes, reduce errors, and enhance resource utilisation. Furthermore, integrating renewable energy sources and energy-efficient machinery can lower energy consumption and carbon emissions.
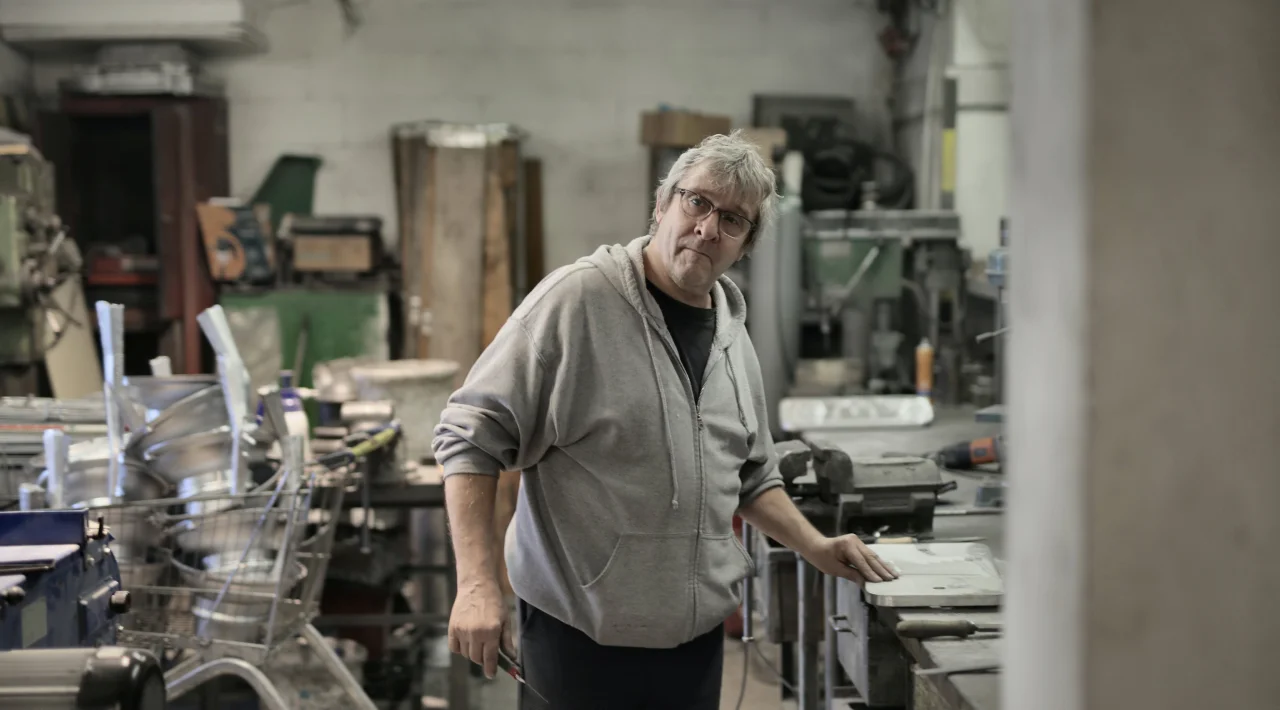
Optimise Supply Chain Management
Efficiency and effectiveness extend beyond the factory walls. Sustainable supply chain management involves assessing and improving every aspect of the supply chain, from sourcing raw materials to distributing finished products. Companies can reduce environmental impact by choosing suppliers with eco-friendly practices, optimising transportation routes, and minimising excess inventory.
Design for Sustainability
Effective product design with sustainability in mind is a powerful strategy. Companies can create more sustainable products by choosing eco-friendly materials, designing products for disassembly and recycling, and considering the entire product lifecycle. Design thinking that prioritises sustainability ensures that efficiency and effectiveness are embedded in the DNA of products.
Implement Closed-Loop Manufacturing
Closed-loop manufacturing systems aim to minimise waste by reusing and recycling materials within the production cycle. Companies can design products and processes to facilitate the recovery and reuse of materials, reducing the demand for new resources and lowering waste generation.
Invest in Employee Training and Engagement
Efficiency and effectiveness depend not solely on technology and processes but also on a skilled and engaged workforce. Investing in employee training and engagement programs can lead to a culture of continuous improvement, where employees actively contribute ideas and innovations to enhance sustainability.
Set Clear Sustainability Goals
Setting specific, measurable, and time-bound sustainability goals is essential. Companies should define their objectives for reducing resource consumption, lowering carbon emissions, and improving product sustainability. These goals serve as a roadmap for guiding efficiency and effectiveness initiatives.
Monitor and Measure Progress
Monitoring and measuring key performance indicators (KPIs) are essential to track progress. Companies should collect and analyse data related to energy use, waste generation, emissions, and other relevant metrics to identify areas for improvement.
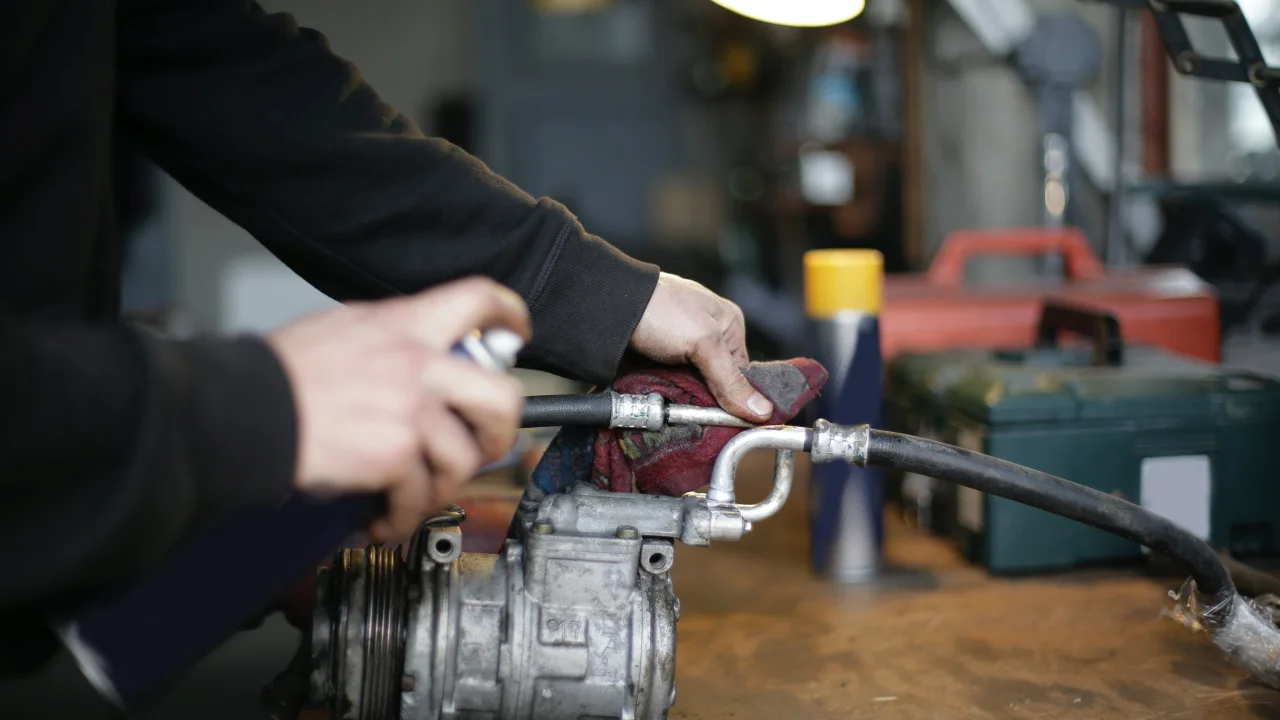
Collaborate with Stakeholders
Collaboration with stakeholders, including suppliers, customers, and industry partners, can yield valuable insights and support sustainability efforts. Working together to implement sustainable practices along the entire supply chain can amplify the impact of sustainability initiatives.
Certifications and Standards Compliance
Adhering to sustainability certifications and standards, such as ISO 14001 (environmental management) and ISO 50001 (energy management), demonstrates a commitment to efficiency and effectiveness in sustainable manufacturing. These frameworks provide guidelines for reducing environmental impact and optimising resource use.
In conclusion, improving efficiency and effectiveness in sustainable manufacturing requires a multifaceted approach encompassing technology, processes, design, and collaboration. By implementing these strategies, companies can reduce their environmental footprint, lower costs, and position themselves as leaders in responsible manufacturing practices. These efforts benefit the bottom line and contribute to a more sustainable and resilient future for the entire industry.
Challenges and Solutions
While the pursuit of efficiency and effectiveness in sustainable manufacturing offers numerous benefits, it is not without its challenges. This section explores some common obstacles companies may encounter and presents practical solutions.
Resistance to Change
Change management is crucial. It's essential to foster a culture of sustainability from top to bottom within an organisation. Engage employees in the process, provide training, and communicate sustainability benefits. Create incentives and recognition programs to motivate employees to embrace and champion sustainability initiatives.
Initial Investment Costs
Sustainable practices often require upfront technology, equipment, and employee training investments. To overcome this challenge, companies can explore financial incentives, grants, and subsidies offered by governments and industry associations to support sustainability projects. Additionally, the long-term cost savings and potential for increased market share due to sustainable initiatives should be considered.
Data Collection and Analysis
Gathering and analysing data for sustainability metrics can be complex and time-consuming. Implementing robust data management systems and software can streamline this process. Collaborate with data analysis and sustainability reporting experts to ensure accurate and insightful measurement.
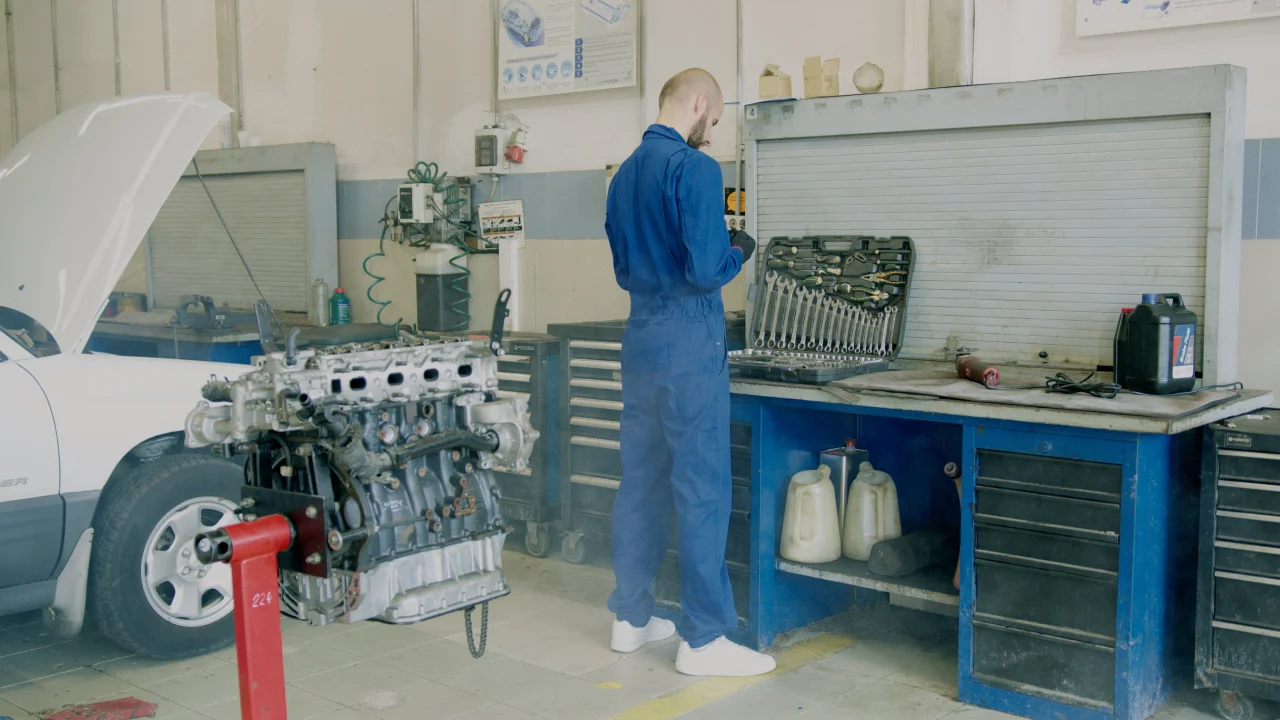
Supply Chain Complexity
Supply chains are often vast and intricate, making ensuring sustainability across all tiers challenging. Collaboration and transparency with suppliers are essential. Establish precise sustainability requirements for suppliers, conduct audits, and develop partnerships with those who align with your goals. Implement blockchain technology or digital platforms to trace and monitor the sustainability of products throughout the supply chain.
Regulatory Compliance
Keeping up with evolving sustainability regulations can take time and effort. Stay informed about changing laws and standards related to sustainable manufacturing. Invest in legal counsel or sustainability experts to ensure compliance. Engage with industry associations and participate in advocacy efforts to influence regulations positively.
Balancing Efficiency and Sustainability
Balancing efficiency and sustainability can be challenging, as optimising one aspect may negatively impact the other. Employ a systems thinking approach to assess how changes in efficiency affect sustainability and vice versa. Seek synergistic solutions that enhance efficiency and sustainability, such as energy-efficient technologies or waste-reduction strategies.
Consumer Education
Consumers often need more awareness of the environmental and social impact of products. Companies can invest in educational campaigns to inform consumers about the benefits of sustainable products and the importance of responsible consumption. Labelling products with sustainability certifications or environmental impact information can also empower consumers to make informed choices.
Technological Advancements
Technology evolves rapidly, and keeping pace with sustainable manufacturing technologies can be a challenge. Establish research and development teams dedicated to exploring emerging technologies. Collaborate with technology partners and universities to stay at the forefront of sustainable innovations.
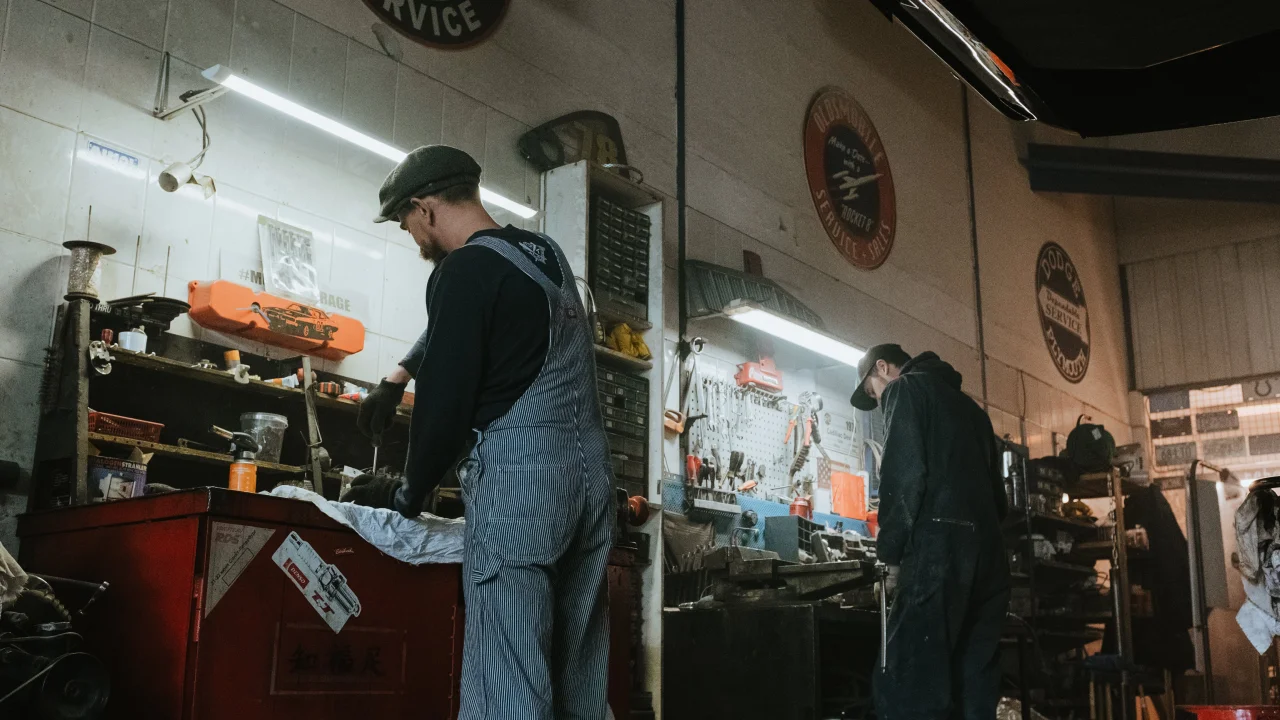
Scalability
Adapting sustainable practices for large-scale manufacturing can be complex. Start with pilot projects to test sustainability initiatives on a smaller scale before implementing them company-wide. Develop a phased sustainability plan that outlines how sustainability practices can be scaled up over time.
Short-Term vs. Long-Term Focus
Companies may prioritise short-term financial gains over long-term sustainability investments. To overcome this challenge, create a compelling business case demonstrating sustainability's long-term benefits, including cost savings, risk mitigation, and improved brand reputation. Align sustainability initiatives with the company's overall strategic objectives.
In conclusion, while there are challenges to implementing efficiency and effectiveness in sustainable manufacturing, proactive strategies and a commitment to sustainability can help companies overcome these obstacles. By addressing these challenges head-on, businesses can create a more sustainable and resilient future for themselves and the industry. Pursuing sustainable manufacturing is not without its complexities, but the rewards of environmental impact reduction, cost savings, and improved competitiveness make it a journey worth undertaking.
The Future of Sustainable Manufacturing
As we look ahead to the future of sustainable manufacturing, it is clear that this journey is not a destination but a dynamic process that will continue to evolve. Here, we explore emerging trends, technologies, and critical considerations that will shape the future landscape of sustainable manufacturing.
Integration of Advanced Technologies
The future of sustainable manufacturing is deeply intertwined with the integration of advanced technologies. Artificial intelligence (AI), the Internet of Things (IoT), and data analytics will play pivotal roles in optimising processes for both efficiency and sustainability. AI-driven predictive maintenance, for example, can help reduce equipment downtime and energy waste.
Circular Economy Adoption
The adoption of circular economy principles will become increasingly widespread. Companies will design products with longevity, repairability, and recyclability in mind. End-of-life products will be repurposed, refurbished, or remanufactured, minimising waste and resource demand.
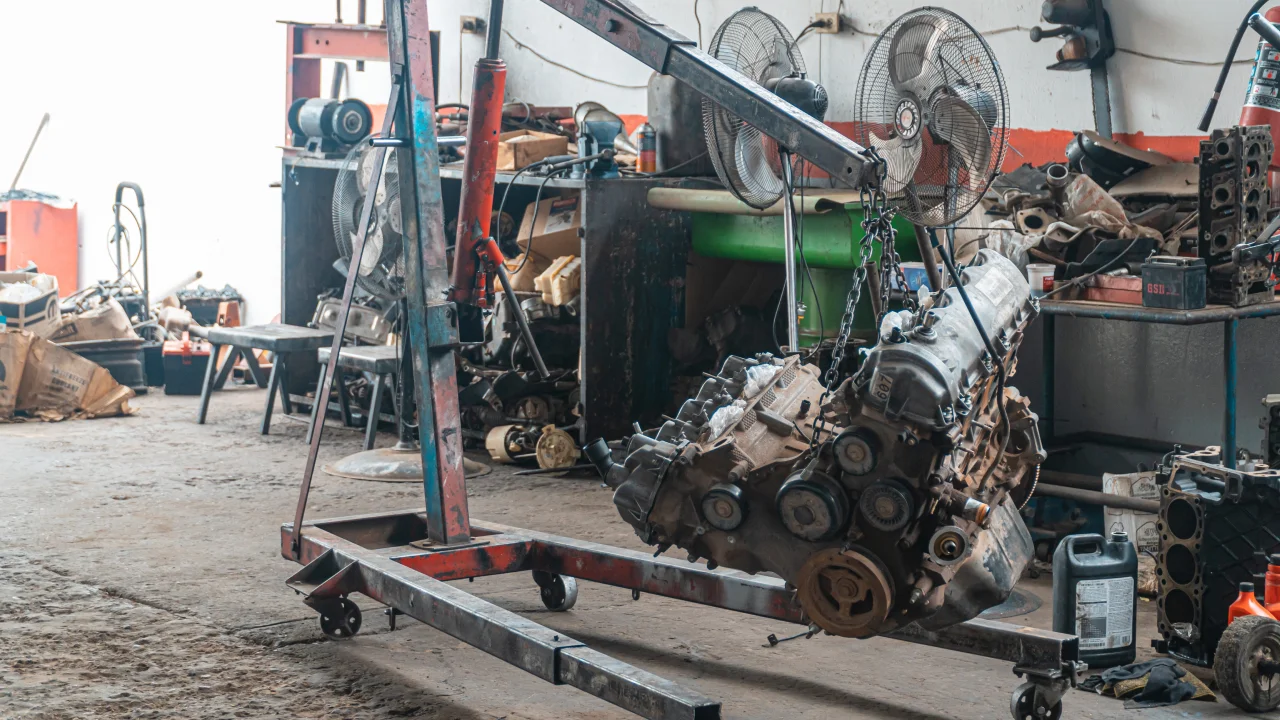
Decentralised and Clean Energy Sources
Manufacturers will continue to transition to cleaner and more sustainable energy sources. Renewable energy, including solar and wind power, will replace fossil fuels, reducing carbon emissions and dependence on finite resources. Decentralised energy systems will increase resilience and decrease transmission losses.
Sustainable Materials Innovation
Innovations in sustainable materials will revolutionise manufacturing. Bio-based materials, recycled plastics, and 3D-printed sustainable materials will gain prominence. These materials will not only reduce the environmental impact of production but also offer new design possibilities.
Digital Twins and Simulation
Digital twins, virtual replicas of physical processes, will become indispensable tools for optimising manufacturing operations. They will allow manufacturers to simulate and optimise processes before implementation, reducing resource waste and errors.
Regulatory Evolution
Regulations and standards related to sustainable manufacturing will continue to evolve. Governments worldwide will enact stricter environmental and social responsibility requirements. Companies will need to stay agile and adaptable to remain compliant and competitive.
Supply Chain Resilience
The importance of supply chain resilience will grow in the face of global disruptions. Sustainable manufacturing practices, including localised supply chains and diversified sourcing, will enhance stability and reduce environmental impacts associated with long-distance transportation.
Transparency and Traceability
Consumer demand for transparency and traceability will intensify. Technologies like blockchain will provide transparent, verifiable supply chain data, allowing consumers to make informed choices and hold companies accountable.
Social Responsibility Integration
Sustainability will encompass not only environmental but also social responsibility. Companies will prioritise fair labour practices, diversity and inclusion, and community engagement as integral components of sustainable manufacturing.
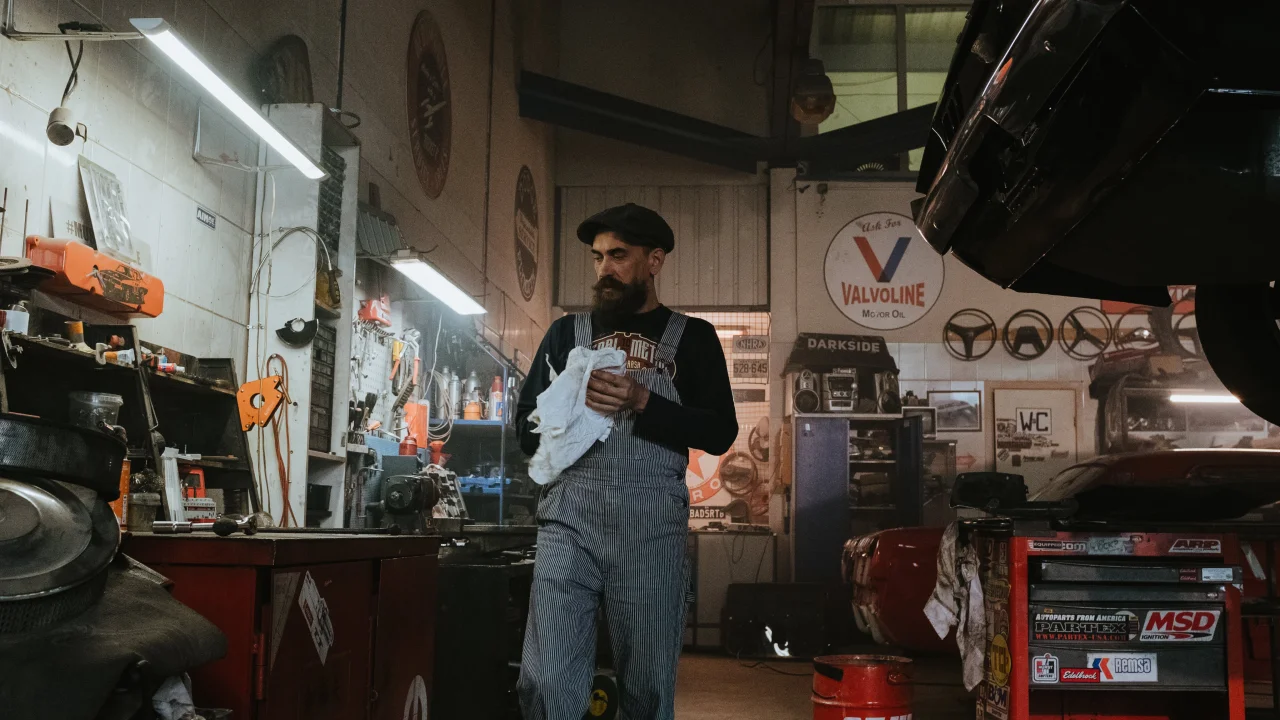
Collaboration and Industry Initiatives
Cross-industry collaboration and industry-wide initiatives will accelerate sustainable manufacturing progress. Companies will collaborate to share best practices, develop sustainability standards, and drive systemic change.
In summary, the future of sustainable manufacturing is a dynamic and promising landscape. Manufacturers can enhance competitiveness by embracing advanced technologies, circular economy principles, sustainable materials, and responsible practices, contributing to a more sustainable and resilient global economy. As sustainability becomes increasingly embedded in business strategies, it will usher in an era where efficiency, effectiveness, and environmental stewardship go hand in hand, shaping a brighter future for manufacturing and the planet.
Conclusion
Efficiency and effectiveness, as the cornerstones of sustainable manufacturing, guide industries toward a more responsible and environmentally conscious future. In this journey, we've explored the significance of these two principles, their synergy, the importance of metrics, and strategies for improvement. We've also addressed challenges and discussed the future landscape of sustainable manufacturing.
Efficiency, driven by lean principles and advanced technologies, enables companies to optimise processes, conserve resources, and reduce waste. Effectiveness focuses on sustainable design, responsible materials selection, and ethical practices, ensuring products and processes align with environmental and social goals.
The synergy between efficiency and effectiveness is powerful, allowing companies to minimise resource consumption, lower carbon footprints, and enhance product sustainability while maintaining competitiveness. Key metrics provide the compass for this journey, offering quantifiable insights to track progress and inform decision-making.
Challenges, including resistance to change, initial investment costs, and supply chain complexity, can be overcome with proactive strategies such as change management, financial incentives, and collaboration. The future of sustainable manufacturing promises integration of advanced technologies, circular economy adoption, sustainable materials innovation, and a heightened focus on social responsibility and transparency.
In conclusion, sustainable manufacturing isn't just a corporate responsibility; it's a moral obligation and a strategic imperative. By embracing efficiency and effectiveness, businesses can thrive in a world where sustainability isn't just a buzzword but a way of life. As we move forward, let's remember that the path to a more sustainable future begins with every decision, every product, and every process. It's a journey that requires commitment, innovation, and collaboration, and it's a journey that holds the promise of a better world for generations to come. Together, we can build a future where industry and ecology coexist harmoniously, efficiency and effectiveness are the guiding principles, and sustainability is the legacy we leave behind.
Comments
No comments yet!Add a Comment
You must be logged in to post a comment.