In the intricate dance of modern manufacturing, efficiency reigns as the unrivalled sovereign. It is the linchpin upon which competitiveness, productivity, and profitability hinge. However, lurking in the shadows of every production floor is an evil force that can plunge operations into chaos - downtime. In this comprehensive exploration, we delve deep into downtime management strategies, wielding data and research as our guiding lights to enhance manufacturing efficiency.
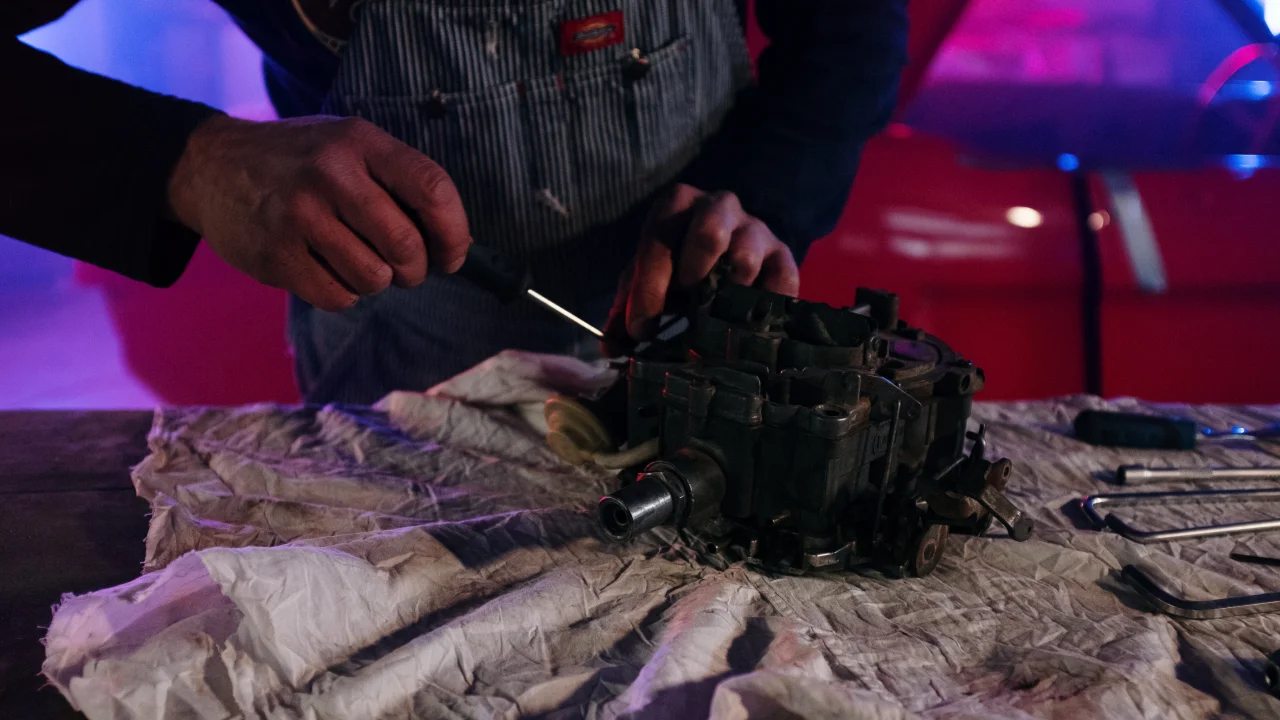
Downtime - A Costly Conundrum
To fully grasp the significance of downtime management, let's begin with an alarming statistic: the average cost of downtime in manufacturing can range from €500 to €22,000 per minute, depending on the industry and the scale of operations. This financial drain arises from many causes, encompassing equipment failures, setup and changeover times, human factors, and supply chain disruptions, to name a few. The machinery that powers the modern production line is a delicate ecosystem, susceptible to wear and tear and the caprices of operational wear and tear, necessitating preventive maintenance strategies.
The Quest for Efficiency
Manufacturers are on an unending quest for operational efficiency, seeking to maximise uptime and throughput. For instance, Toyota, a pioneer of Lean Manufacturing, employs Just-in-Time (JIT) production strategies to optimise processes, reduce idle time, and minimise inventory. Meanwhile, companies such as General Electric have adopted Total Productive Maintenance (TPM) principles, ensuring equipment reliability and longevity.
Harnessing Technology for Precision
In the digital age, technology has emerged as a potent ally in the fight against downtime. Overall Equipment Efficiency (OEE) monitoring systems provide real-time insights into production performance, facilitating data-driven downtime solutions. Cutting-edge downtime tracking tools enable meticulous analysis, highlighting areas for improvement.
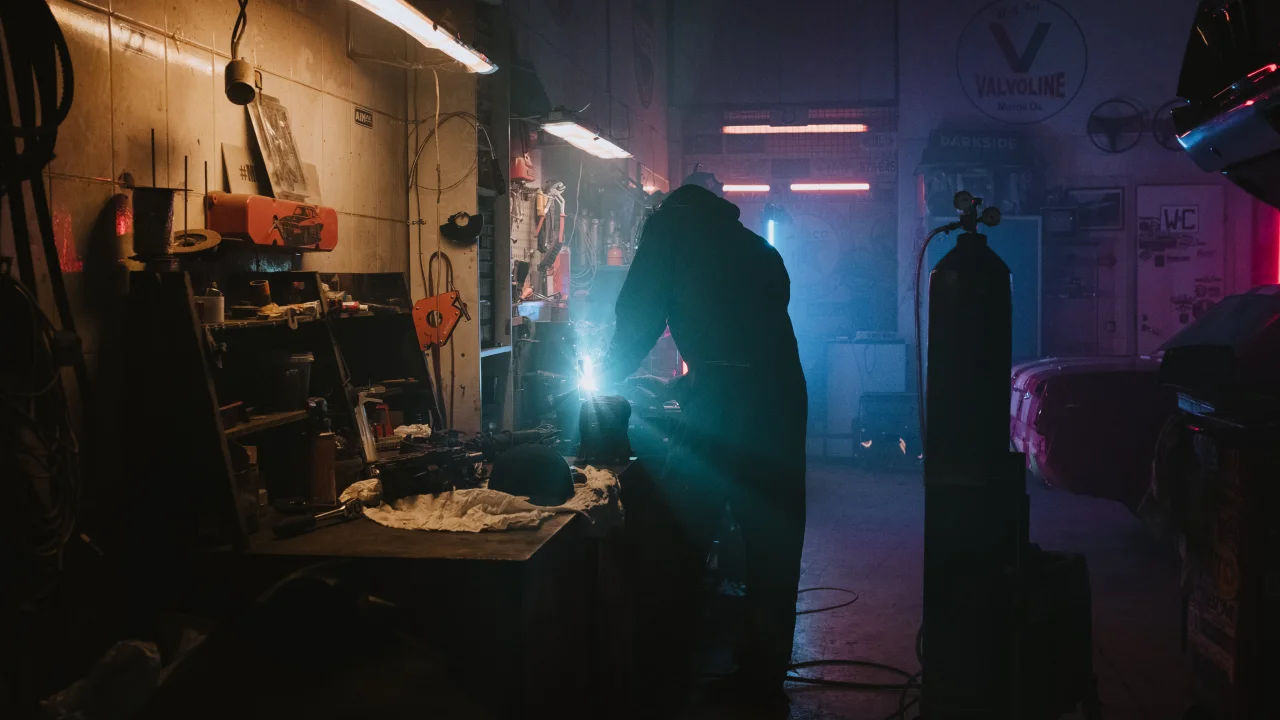
In the following pages, we journeyed through downtime management strategies, exploring preventive maintenance, lean practices, and the transformative potential of Industry 4.0 technologies. We delve into the intricate dance of workflow optimisation, JIT production, and the relentless pursuit of continuous improvement. Join us as we unlock the secrets to enhanced manufacturing efficiency, navigating the treacherous waters of downtime with precision and purpose.
Understanding Downtime
Downtime is akin to a silent predator prowling amidst the cacophonous machinery in manufacturing. It encompasses any period when equipment or machinery is not functioning optimally or, worse still, remains idle. The ramifications of downtime extend far beyond the realm of mere inconvenience. In the harsh manufacturing world, time is money, and every minute of rest takes a toll on profitability.
Statistics paint a stark picture. On average, manufacturers face a daunting 800 hours of downtime annually, amounting to a staggering cost ranging from €400,000 to €17.6 million. To put this into perspective, in the automotive industry, every minute of downtime can translate to a loss of around €22,000. These figures underscore the urgency of developing effective downtime management strategies.
The Cost of Downtime
The financial implications of downtime are multifaceted. Beyond the direct cost of repairs and maintenance, the ripple effect extends to lost production, decreased customer satisfaction, and damage to a company's reputation. For instance, a critical component failure in a bottling plant can result in a production stoppage lasting several hours. This not only incurs the immediate cost of repairs but also leads to potential revenue loss from unfulfilled orders and damaged customer relationships.
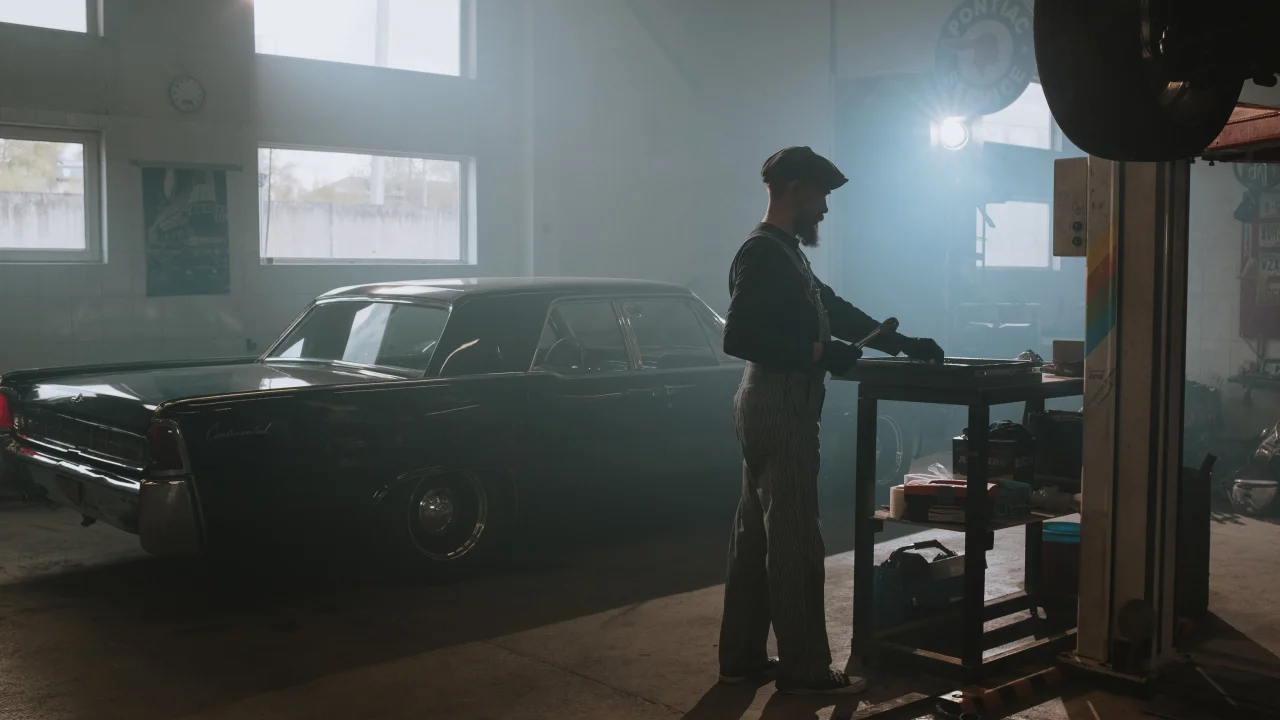
To combat these losses, manufacturers employ various downtime reduction strategies. These include preventive maintenance, predictive maintenance, and scheduled equipment inspections, all aimed at identifying and rectifying issues before they escalate into costly downtime incidents. In the next section, we will delve deeper into the root causes of downtime, shedding light on the culprits responsible for this menace. For example, a well-known European automotive manufacturer implemented a predictive maintenance system on its assembly line, which analysed equipment data to predict failures before they occurred. As a result, they reduced unplanned downtime by 60%, saving an estimated €1.5 million annually.
By understanding the true nature and cost of downtime, manufacturers can begin to appreciate the urgency of developing effective strategies to mitigate its impact and enhance overall manufacturing efficiency.
Causes of Downtime
Understanding the causes of downtime is paramount to devising effective strategies for its mitigation. Downtime in manufacturing can be attributed to a web of interrelated factors, each contributing to the disruption of production processes. Here, we dissect the primary culprits behind manufacturing downtime and explore their impact.
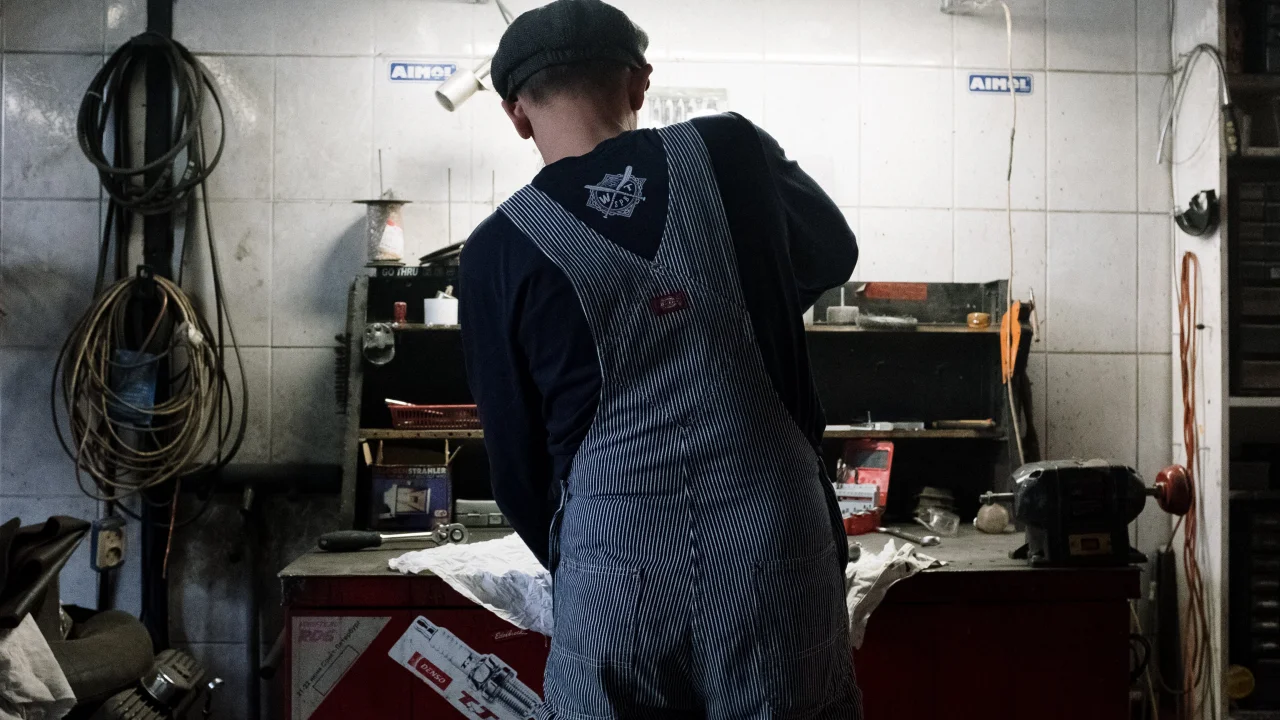
Equipment Failures
Equipment failures stand as the chief antagonist in the saga of downtime. Be it the rumbling behemoth of a factory assembly line or the delicate precision instruments in a laboratory, machinery is prone to wear and tear. Statistics reveal that equipment failures account for approximately 42% of all downtime incidents in manufacturing. These failures can be catastrophic, leading to downtime and costly repairs and replacements.
Consider, for instance, a modern CNC machine that grinds to a halt due to a spindle-bearing failure. Beyond the immediate cost of the replacement parts, the lost production and the expenses associated with idle workers and equipment maintenance can quickly escalate.
Setup and Changeover Times
Another formidable adversary in the battle against downtime is setup and changeover times. When switching from one product or production run to another, machinery often requires adjustments and reconfigurations. Inefficient changeover processes can result in prolonged downtimes.
For instance, when shifting from one product to another, a snack manufacturer faced lengthy changeover times in the food packaging industry. The resultant downtime costs the company approximately €50,000 per hour. Through the implementation of Lean Manufacturing practices and streamlined changeover procedures, they reduced these downtimes significantly.
Human Factors
Human error remains a persistent threat to manufacturing efficiency. Employees, despite their best intentions, can inadvertently cause disruptions. Proper training and fostering a culture of safety and accountability are crucial in mitigating human-induced downtime.
For example, in a pharmaceutical manufacturing facility, the misalignment of equipment by an operator led to a product spill and subsequent downtime. Comprehensive training programmes and adopting error-proofing techniques helped reduce such incidents, resulting in substantial savings.
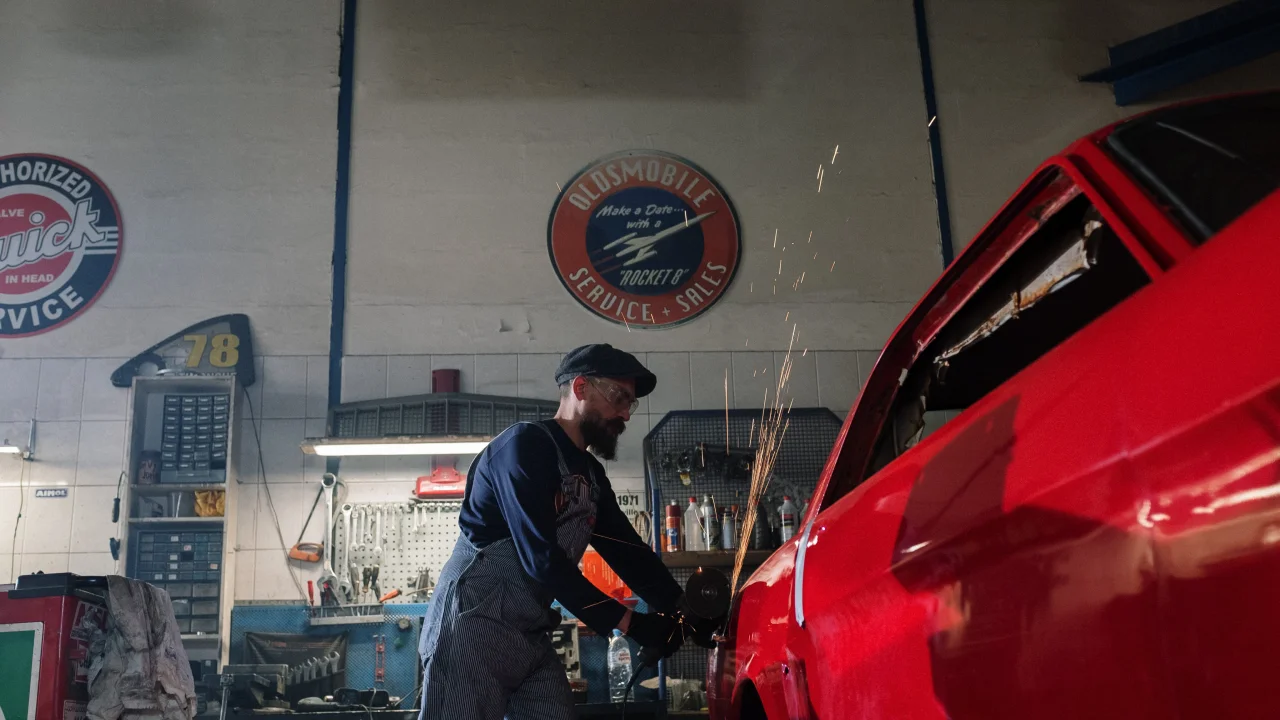
Supply Chain Disruptions
Supply chain disruptions can reverberate across manufacturing operations in today's interconnected world. Whether it's a shortage of critical components, transportation delays, or unforeseen geopolitical events, these disruptions can lead to production halts and unexpected downtimes.
The impact of supply chain disruptions can be staggering. The COVID-19 pandemic, for instance, wreaked havoc on global supply chains, causing production stoppages and shortages in various industries, including automotive and electronics manufacturing.
Understanding these critical causes of downtime is the first step in developing effective strategies to combat them. In the subsequent sections, we will delve deeper into downtime analysis and monitoring techniques, preventive maintenance strategies, and lean manufacturing practices as part of a comprehensive approach to enhanced manufacturing efficiency.
Downtime Analysis and Monitoring
Effective downtime management begins with thoroughly understanding the factors contributing to downtime incidents. This section explores the vital role of downtime analysis and monitoring in enhancing manufacturing efficiency.
OEE (Overall Equipment Efficiency)
OEE is the compass that guides manufacturers through the labyrinth of downtime. It measures equipment effectiveness by factoring in three critical components: availability, performance, and quality. The formula is simple: OEE = Availability × Performance × Quality.
Statistics underscore the significance of OEE. Across various industries, the average OEE hovers around 60%, signifying substantial room for improvement. Manufacturing giants like Toyota have elevated OEE to over 85% through relentless dedication to efficiency.
By employing OEE monitoring systems, manufacturers gain real-time insights into the health of their equipment. It acts as an early warning system, flagging potential downtime triggers. For example, if OEE dips due to decreased availability, it may indicate the need for preventive maintenance to avoid equipment failures.
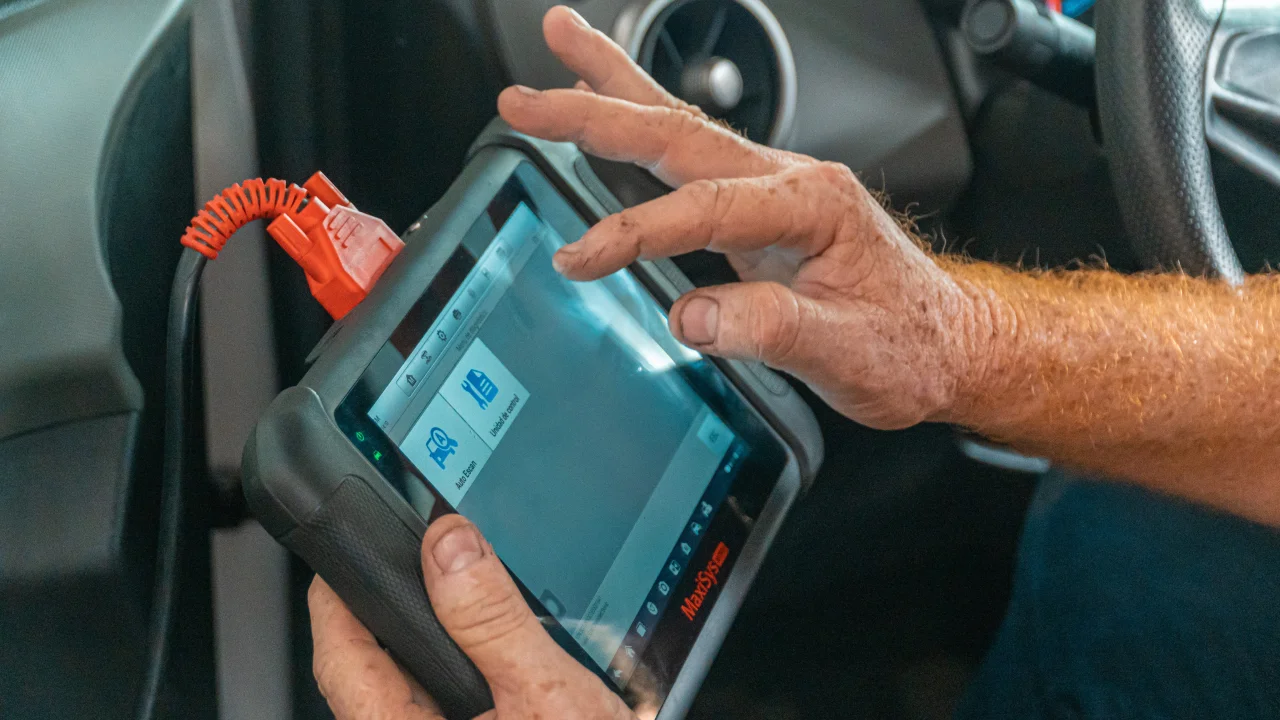
Downtime Tracking Tools
In the quest to minimise downtime, data is king. Downtime tracking tools have emerged as indispensable allies. These software solutions record every instance of downtime, categorising them by cause and duration. This granular data empowers manufacturers to make informed decisions and enact precise interventions.
Consider a scenario in a food processing plant where unplanned downtime due to equipment failures was rampant. Implementation of a downtime tracking tool revealed a recurring issue with a specific machine. Armed with this data, maintenance teams proactively addressed the problem, reducing downtime and preventing costly breakdowns.
Root Cause Analysis
Downtime analysis does not end with tracking; it extends to root cause analysis. This rigorous process seeks to uncover the underlying reasons behind downtime incidents. By identifying root causes, manufacturers can implement targeted solutions to prevent recurrence.
For instance, if frequent equipment breakdowns are traced to inadequate lubrication, a root cause analysis may reveal the need for an improved lubrication schedule. This simple adjustment can lead to a substantial reduction in downtime.
As manufacturing becomes increasingly data-driven, root cause analysis gains prominence. In-depth analysis tools and methodologies enable manufacturers to pinpoint weaknesses in their operations and apply precision fixes.
In the relentless pursuit of manufacturing efficiency, downtime analysis and monitoring are formidable weapons. These tools enable manufacturers to tackle downtime and optimise their operations for maximum productivity. For example, a European aerospace manufacturer utilised OEE monitoring to identify a recurring issue in one of its CNC machining centres. By addressing this problem, they increased OEE from 65% to 85%, resulting in an annual savings of €800,000.
In the following sections, we explore strategies such as preventive maintenance, lean manufacturing practices, and the transformative potential of Industry 4.0 technologies in the fight against downtime.
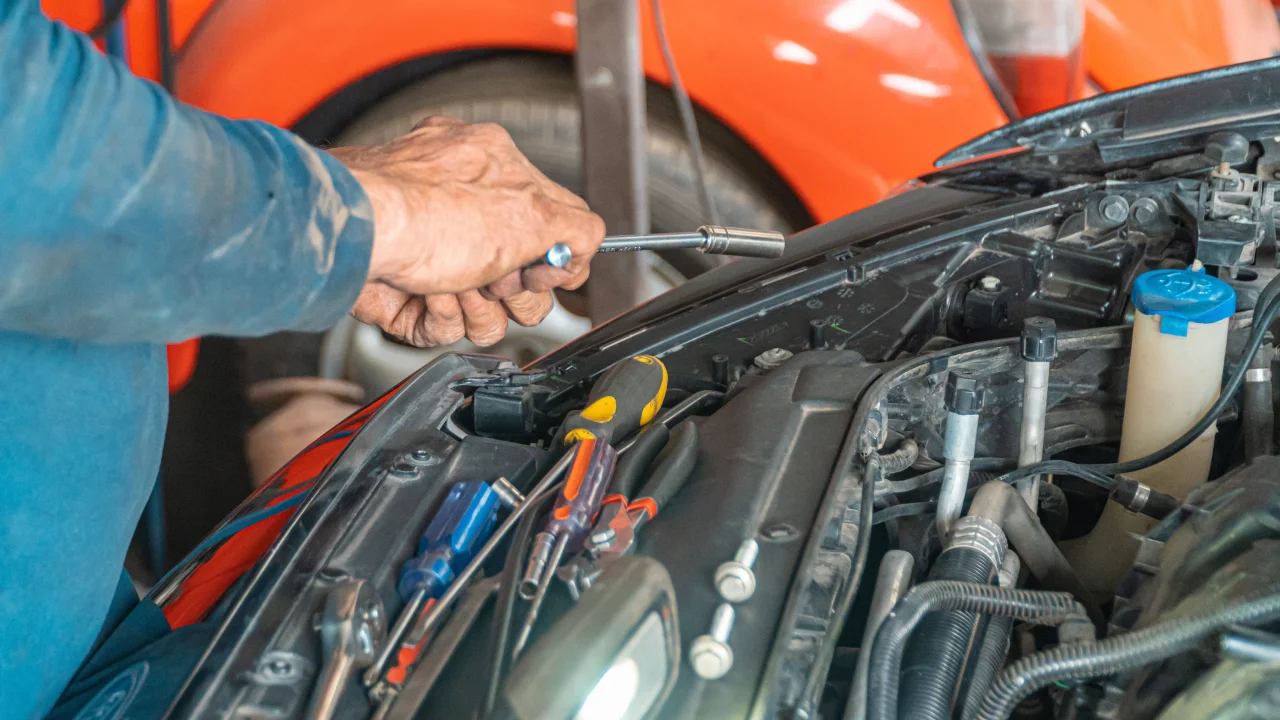
Strategies to Reduce Downtime
Manufacturers facing the relentless spectre of downtime must arm themselves with a formidable arsenal of strategies. This section delves into the tried-and-tested methods that promise to slash downtime, optimise efficiency, and bolster the bottom line.
Preventive Maintenance
Preventive maintenance, often described as the "ounce of prevention," is the defence against downtime. This strategy involves regular inspections and scheduled maintenance to identify and address potential issues before they become costly downtime events.
Statistics paint a compelling picture. Implementing a robust preventive maintenance programme can result in a 12% reduction in maintenance costs and a 30% decrease in downtime. Consider the example of a European manufacturing plant specialising in precision engineering. By implementing a preventive maintenance schedule, they achieved a 25% reduction in downtime, saving an estimated €1.2 million annually.
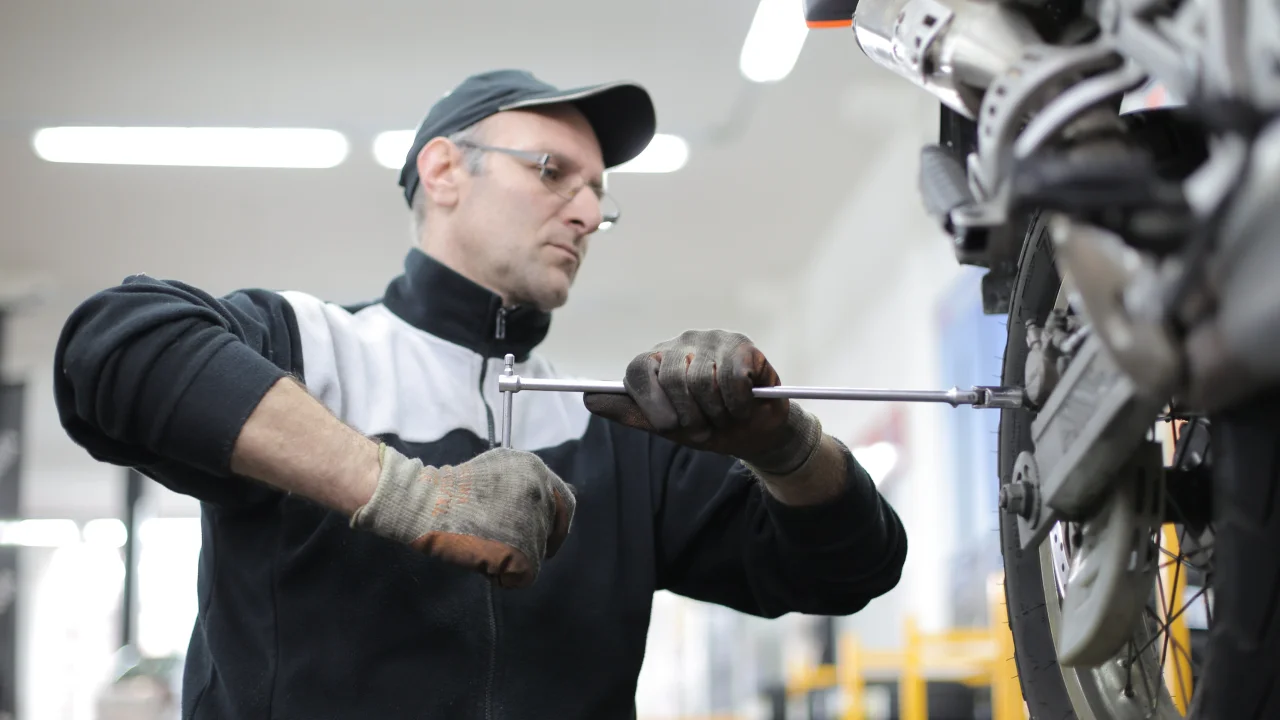
Lean Manufacturing Practices
The lean philosophy, originating from Toyota's production system, is a beacon of efficiency in the manufacturing world. Lean practices champion eliminating waste in downtime, overproduction, or excess inventory.
Lean manufacturing, when implemented effectively, can lead to remarkable results. On average, companies embracing lean principles experience a 15-20% reduction in downtime. Manufacturers can streamline operations, identify bottlenecks, and minimise disruptions by adopting techniques like 5S (Sort, Set in order, Shine, Standardise, Sustain), value stream mapping, and continuous improvement.
Digital Transformation
In the era of Industry 4.0, digital transformation has become a powerful ally in the quest for reduced downtime. Technologies like the Internet of Things (IoT), predictive analytics, and machine learning are revolutionising manufacturing.
Consider a scenario where IoT sensors are embedded in critical machinery. These sensors continuously monitor equipment performance and relay data to a centralised system. Algorithms analyse this data in real-time, identifying deviations from normal operating conditions. Predictive maintenance alerts are then generated, allowing maintenance teams to intervene before a critical failure occurs.
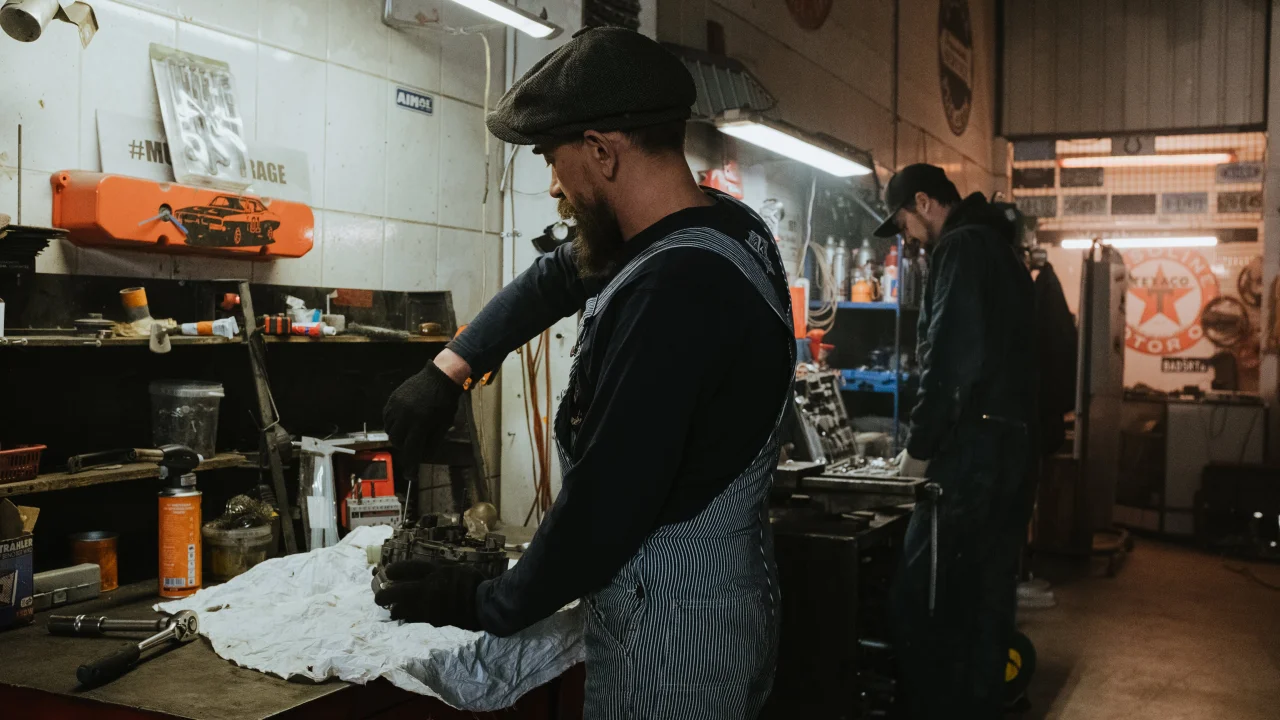
The financial benefits of digital transformation are striking. Companies embracing these technologies can achieve a 10-20% reduction in maintenance costs and a 20-50% decrease in downtime. The initial investment in these technologies is rapidly offset by the substantial savings realised through reduced downtime and improved efficiency.
As we navigate the ever-evolving manufacturing landscape, adopting preventive maintenance, lean practices, and digital transformation emerges as a triumvirate of strategies that promise to tame downtime and enhance manufacturing efficiency and profitability. For example, a European automotive manufacturer harnessed digital twin technology to create virtual replicas of their production lines. By simulating various scenarios and optimising processes in the digital realm, they reduced setup times by 25% and downtime by 15%, resulting in annual savings exceeding €2 million.
In the upcoming sections, we venture further into workflow optimisation, Just-in-Time production, and the relentless pursuit of continuous improvement to achieve manufacturing excellence.
Improving Manufacturing Efficiency
Manufacturing efficiency isn't a static state; it's a dynamic pursuit. In this section, we embark on a journey through the strategies that reduce downtime and enhance manufacturing efficiency.
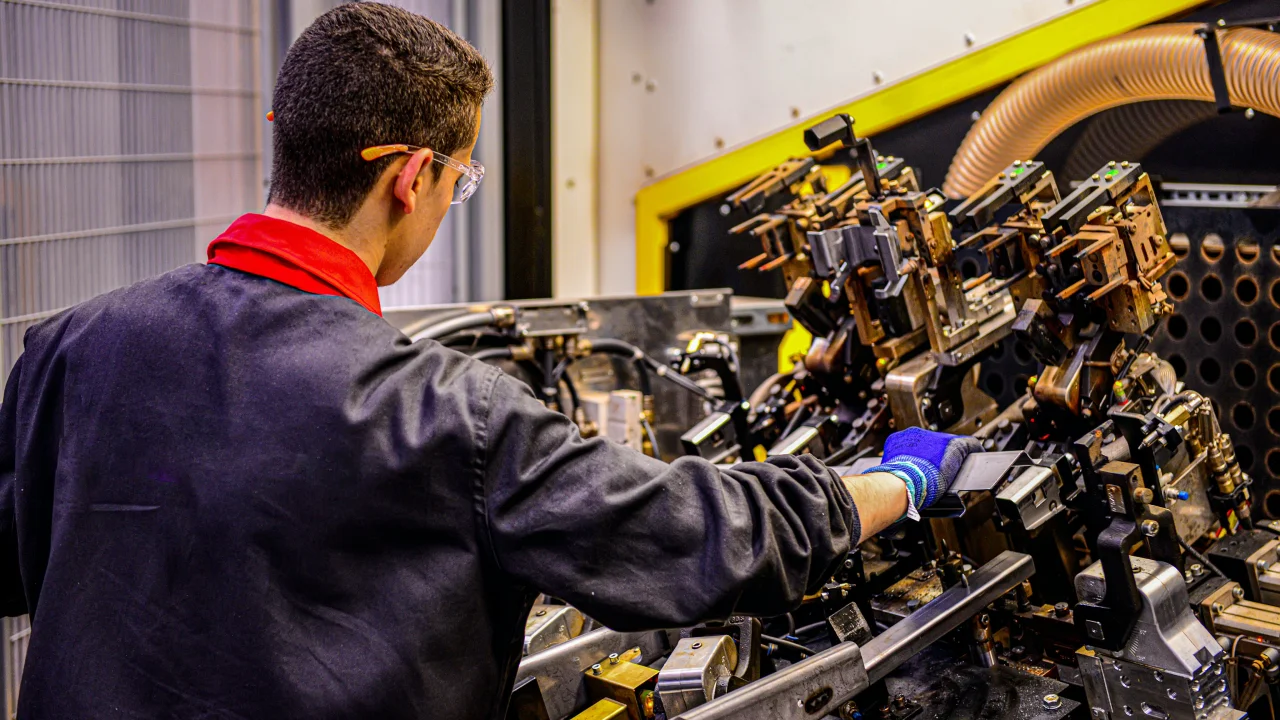
Workflow Optimization
Optimising workflow is akin to fine-tuning the gears of a well-oiled machine. The objective is to create a seamless flow of processes, minimising bottlenecks and idle times. On average, workflow optimisation can lead to a 20-30% increase in production efficiency.
Imagine an automobile assembly line where components are transported between workstations inefficiently. Through workflow analysis and the principles of value stream mapping, the company streamlined processes and eliminated unnecessary handling, ultimately reducing cycle times and increasing overall efficiency.
Just-in-Time Production
The principles of Just-in-Time (JIT) production have revolutionised manufacturing. JIT is more than a strategy; it's a philosophy that emphasises producing what is needed in the correct quantity when it is required. JIT practices have been shown to reduce inventory costs by 20-50%.
In a European electronics manufacturing plant, the adoption of JIT practices not only reduced inventory carrying costs but also slashed lead times. With a JIT system, they could quickly adjust production to meet changing demand, ensuring that products were manufactured only when required.
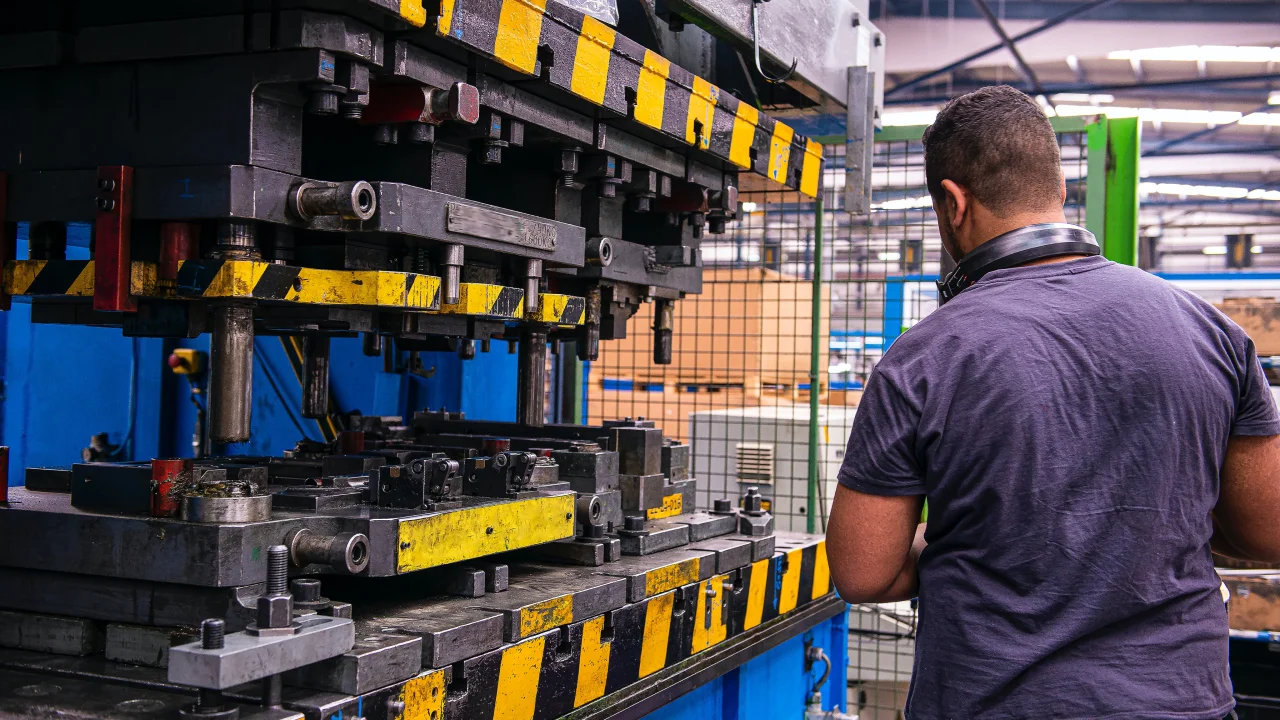
Continuous Improvement
The pursuit of perfection knows no bounds. Continuous improvement, embodied in methodologies such as Lean Six Sigma, encourages manufacturers to strive for excellence relentlessly. Companies embracing this philosophy experience an average reduction in downtime of 20-30%.
Consider a European chemical manufacturer plagued by frequent equipment breakdowns. Through the implementation of Six Sigma methodologies, they reduced defects in their production processes, which in turn reduced equipment failures and associated downtime. The result was an annual saving of €1.8 million.
By embracing workflow optimisation, JIT production, and a culture of continuous improvement, manufacturers can embark on an unending journey towards manufacturing excellence. These strategies minimise downtime and enhance overall efficiency, enabling businesses to stay competitive in the global market.
For example, a European aerospace manufacturer committed to continuous improvement implemented a Kaizen-based programme to tackle downtime systematically. By engaging employees in problem-solving and process improvement, they achieved a 15% reduction in downtime, equating to savings of €1.2 million annually.
In the final section, we conclude our exploration, summarising key takeaways and emphasising the imperative of proactive downtime management in today's manufacturing landscape.
Novel Tool for Downtime Manufacturing
In the intricate dance of modern manufacturing, where time is money and efficiency reigns supreme, downtime is a formidable challenge. We've journeyed through the labyrinth of strategies and tools that promise to reduce downtime, enhance manufacturing efficiency, and safeguard the financial health of businesses.
One such innovative downtime management solution that holds immense potential is Iwoscan. This novel tool harnesses the power of real-time data analysis and predictive maintenance to tackle downtime proactively. While it's relatively new, early adopters have reported remarkable results, including significant reductions in unplanned downtime and enhanced operational efficiency.
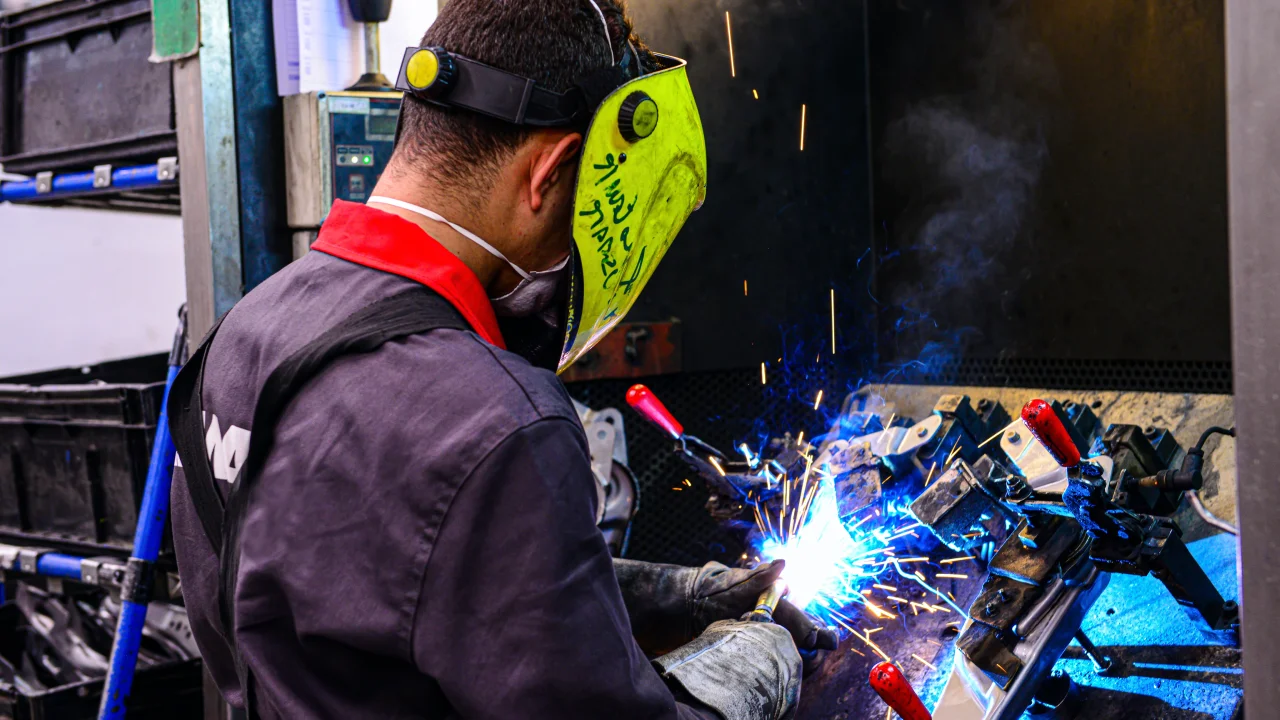
Our exploration has illuminated the significance of downtime management in today's manufacturing landscape. The statistics are compelling: downtime can cost manufacturers anywhere from €500 to €22,000 per minute. In industries like automotive, every minute of downtime can equate to a loss of around €22,000.
We've dissected the root causes of downtime, from equipment failures to human factors, and examined the role of OEE, downtime tracking tools, and root cause analysis in proactive downtime management.
The strategies we've uncovered are proven to be effective. Preventive maintenance programmes can result in a 12% reduction in maintenance costs and a 30% decrease in downtime. Lean manufacturing practices reduce downtime by an average of 15-20%. Digital transformation, including adopting IoT and predictive analytics, can achieve a 10-20% reduction in maintenance costs and a 20-50% decrease in downtime.
Workflow optimisation, JIT production, and a commitment to continuous improvement promise to minimise downtime and enhance overall efficiency. Workflow optimisation can lead to a 20-30% increase in production efficiency. JIT practices can reduce inventory costs significantly. Continuous improvement methodologies yield an average reduction in downtime of 20-30%.
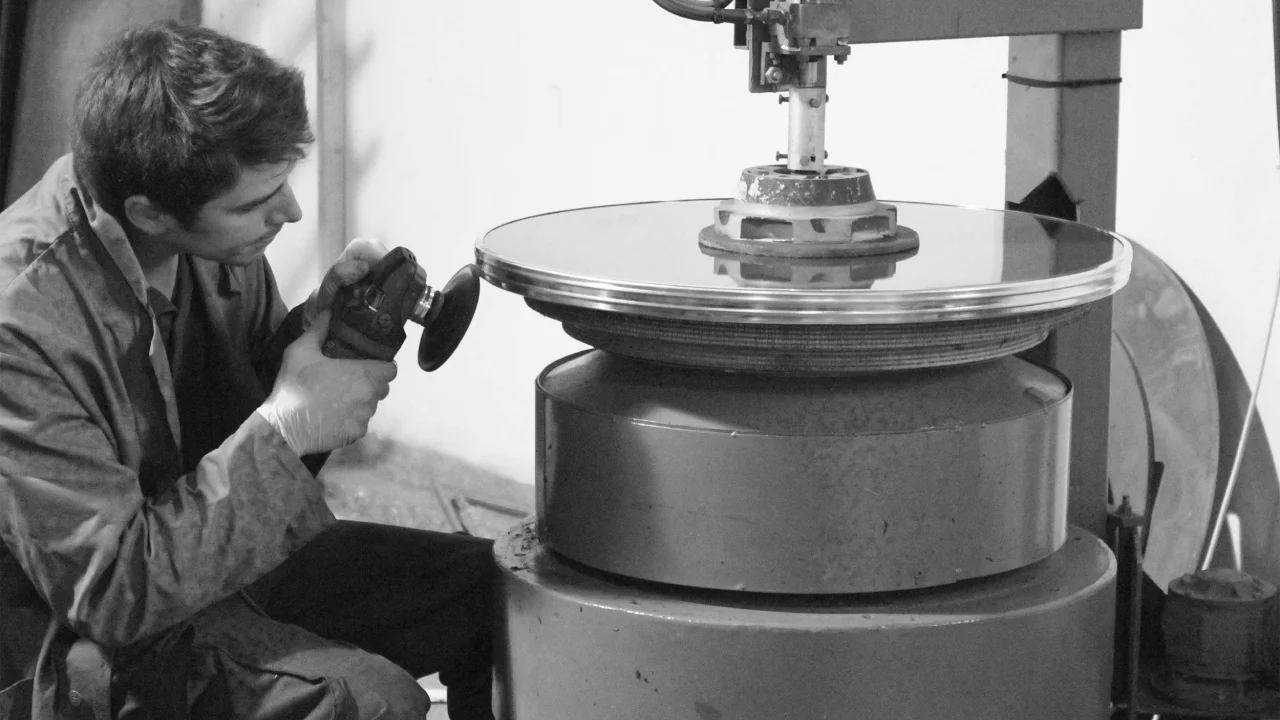
In closing, the imperative of proactive downtime management cannot be overstated. It is not merely a cost-saving measure but a strategic imperative ensuring competitiveness in the global manufacturing arena. As we bid farewell to this exploration, we leave you with the knowledge and tools to embark on the journey towards manufacturing excellence, where downtime is tamed and efficiency reigns supreme.
Comments
No comments yet!Add a Comment
You must be logged in to post a comment.