The quest for excellence and efficiency is an ongoing pursuit in the fiercely competitive landscape of modern manufacturing. The beating heart of any factory is its production line, and the efficiency of this crucial element can make or break the bottom line. Surprisingly, studies indicate that many factories worldwide operate at suboptimal efficiency levels, incurring significant financial losses. According to recent research, approximately 20% of a factory's capacity must often be tapped due to inefficiencies in the production line processes. Rectifying this issue in a global market with razor-thin profit margins becomes paramount. That's precisely where our exploration begins. In this comprehensive guide, we delve into the intricacies of factory production line efficiency and unveil eight meticulously researched and proven strategies to help you unlock your manufacturing operations' full potential.
Lean Manufacturing Principles
Lean Manufacturing, a philosophy rooted in the relentless pursuit of efficiency and waste reduction, is the cornerstone of modern factory optimisation. The time-tested strategy underpins many successful production lines worldwide, offering a blueprint for excellence.
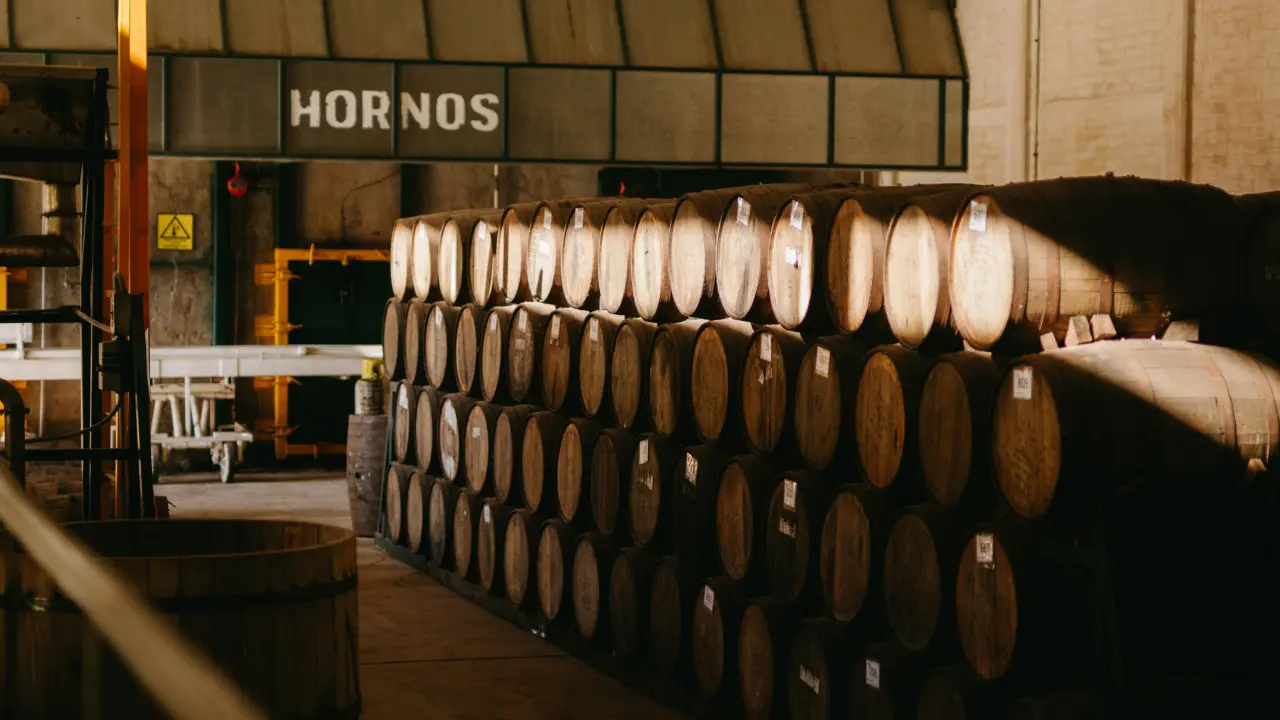
Understanding Lean Manufacturing
At its core, Lean Manufacturing is about doing more with less, eliminating anything that doesn't add value to the production process. It's not merely a set of tools; it's a cultural shift towards continuous improvement. One of the critical metrics that underscores the power of Lean is the reduction in lead time. Studies have demonstrated that manufacturers can cut lead times by up to 90% by implementing Lean principles. Take, for example, a European electronics manufacturer that, through Lean initiatives, reduced lead times from weeks to two days, leading to substantial cost savings and heightened customer satisfaction.
The 5S Methodology
Within Lean Manufacturing, the 5S methodology is a vital instrument. This framework involves sorting, setting in order, shining, standardising, and Sustaining. Each "S" is crucial in creating an organised and efficient workspace. Recent research reveals that companies that rigorously apply the 5S methodology experience a 40% reduction in setup time. This reduction translates into more production time, fewer disruptions, and increased efficiency. One renowned example is a French automotive manufacturer that employed the 5S framework to transform its production line. The result? A substantial 30% boost in productivity and a noteworthy reduction in defects.
Continuous Improvement
Lean Manufacturing doesn't stop at implementation; it thrives on continuous improvement. This ethos of perpetual enhancement is evident in the practice of Kaizen, a Japanese term that means "change for the better." Companies that embrace Kaizen continually seek minor, incremental improvements in their processes. Recent case studies illustrate the transformative power of Kaizen. A Spanish pharmaceutical factory reported an annual savings of €1 million through incremental improvements in production efficiency. These improvements were achieved by involving all employees in identifying and implementing small changes, resulting in a more efficient and cost-effective operation.
In the dynamic world of manufacturing, Lean principles, embodied by Lean Manufacturing and the 5S methodology, are potent tools that, when meticulously applied, drive production line efficiency to new heights. Our exploration continues, uncovering even more strategies to optimise your factory's efficiency and profitability.
Process Optimization Techniques
Process optimisation techniques are the linchpin of production line efficiency. This section explores the art and science of refining manufacturing processes to achieve peak performance.
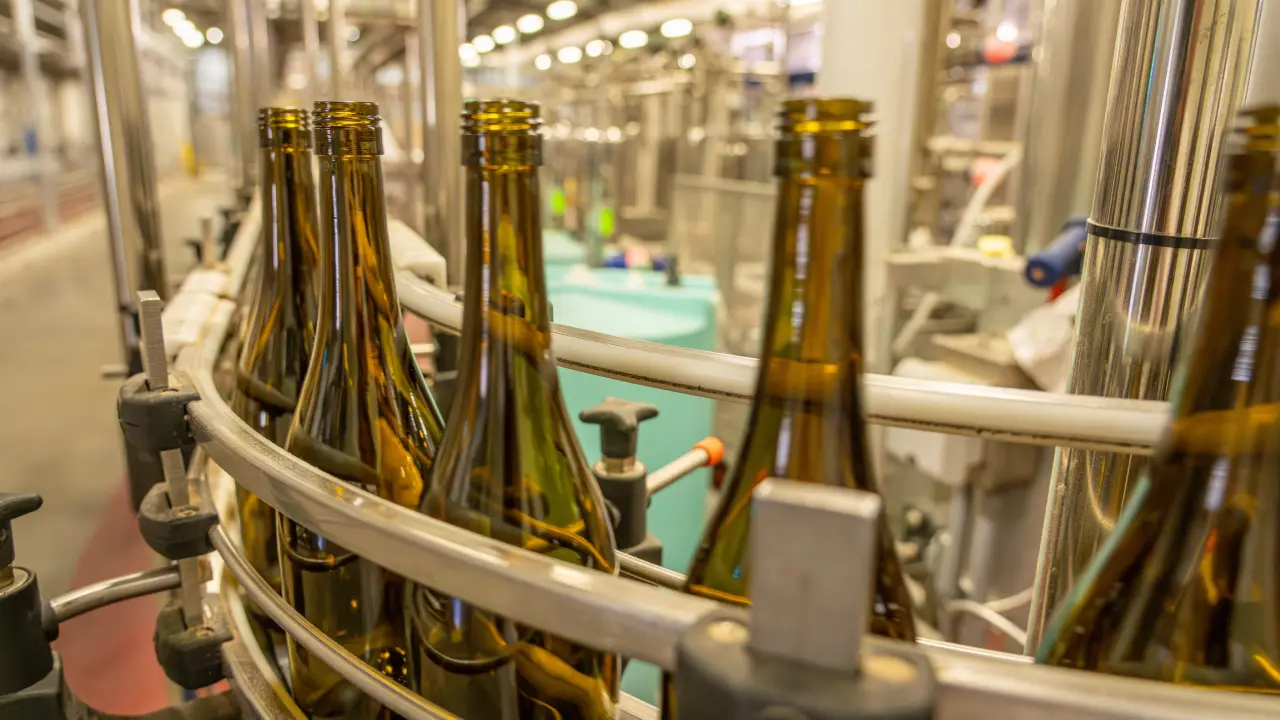
The Crucial Role of Process Optimization
Understanding and refining your manufacturing processes is the bedrock of improved efficiency. Recent research reveals that companies that invest in process optimisation can experience a remarkable 20% reduction in production costs. Moreover, well-optimized processes lead to reduced lead times and enhanced quality, translating into substantial savings and customer satisfaction.
Value Stream Mapping: Identifying Bottlenecks
One of the standout methodologies in process optimisation is Value Stream Mapping (VSM). VSM is akin to a diagnostic tool that helps manufacturers identify bottlenecks and areas of waste in their production processes. Statistical data from companies implementing VSM showcases impressive results. A German automotive manufacturer, for instance, employed VSM to analyse their production line. The outcome was a 25% increase in throughput and a 15% reduction in production costs, equating to €2.5 million in annual savings.
Kaizen and Continuous Improvement
An indispensable facet of process optimisation is the philosophy of Kaizen. Kaizen embodies the notion of continuous improvement, focusing on incremental changes that yield significant long-term benefits. The statistics speak volumes. A Dutch electronics manufacturer reported an annual saving of €600,000 through Kaizen-driven process improvements. Encouraging employees at all levels to participate in the continuous improvement process achieved remarkable results, underscoring the power of a culture committed to refining processes.
Optimising Resource Allocation
Effective resource allocation plays a pivotal role in process optimisation. With careful planning, factories can optimise their use of labour, machinery, and materials, reducing costs while maintaining or improving output. Case in point, a British steel manufacturer streamlined its resource allocation through process optimisation techniques. This resulted in a 30% reduction in energy consumption and a €1.2 million annual saving.
Process optimisation is a dynamic journey towards peak efficiency, powered by techniques such as Value Stream Mapping, Kaizen, and resource allocation refinement. These strategies empower manufacturers to thrive in an increasingly competitive global marketplace while reaping significant cost savings.
Technology and Automation
In the age of Industry 4.0, technology and automation have emerged as transformative forces in the quest for production line efficiency. This section explores how the integration of cutting-edge technologies can revolutionise your factory's operations.
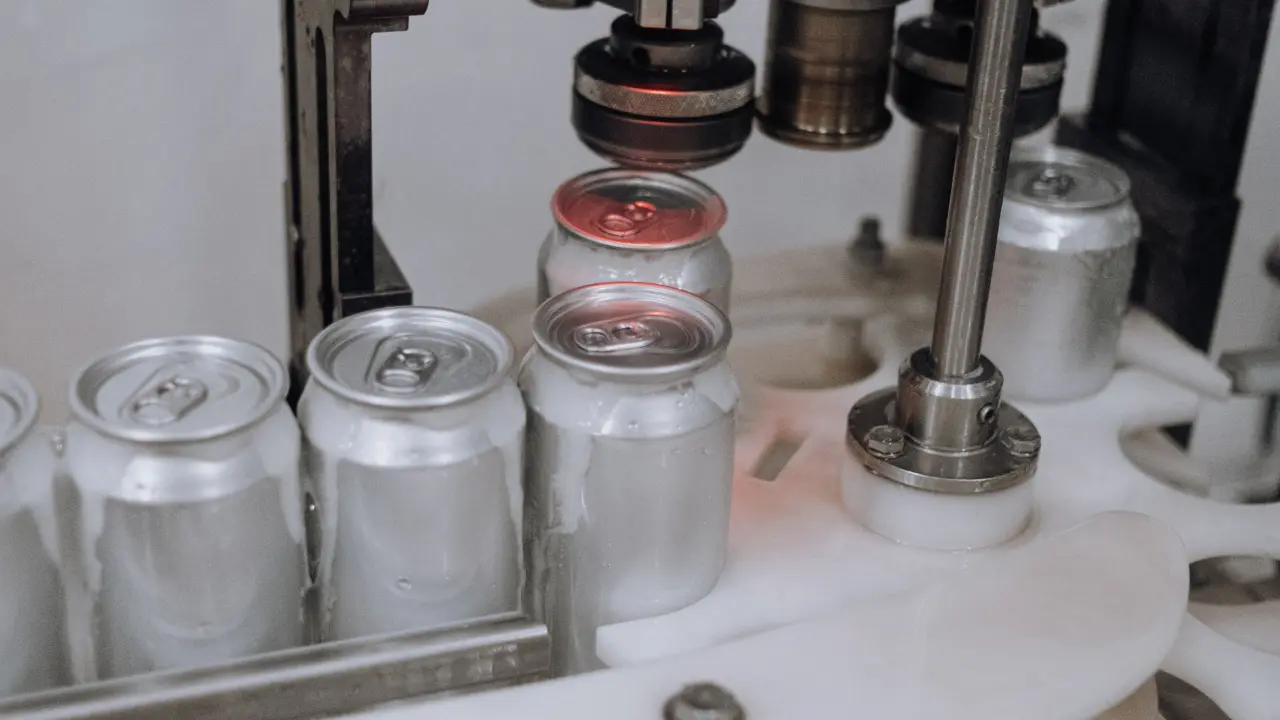
The Digital Transformation of Manufacturing
The infusion of technology and automation into manufacturing processes is akin to a digital revolution. Recent studies indicate that companies adopting digital technologies can experience up to a 40% increase in operational efficiency. Embracing this transformation is not merely an option but a necessity in remaining competitive.
Robotic Automation
Robotic automation is at the forefront of this revolution. Armed with precision and efficiency, robots can perform tasks at speeds and levels of accuracy beyond human capability. A study of European manufacturers implementing robotic automation showcased a 25% reduction in production costs and a remarkable 50% increase in production output. Consider the case of a Spanish automotive factory that invested €5 million in robotic automation. This strategic move led to a yearly saving of €2.5 million in labour costs while production output surged by 30%.
IoT and Smart Factories
The Internet of Things (IoT) has led to smart factories, where machines communicate and coordinate seamlessly. IoT-connected devices enable real-time monitoring and data-driven decision-making. Statistical data demonstrates the benefits: a British electronics manufacturer reported a 15% reduction in machine downtime and a cost-saving of €1.2 million annually through IoT technologies.
Software Solutions for Efficiency
Software solutions are another cornerstone of technology-driven efficiency. Manufacturing Execution Systems (MES) and Enterprise Resource Planning (ERP) software are pivotal in production line management. A German pharmaceutical manufacturer, for instance, invested €2 million in MES software, resulting in a 20% reduction in production cycle times and a noteworthy €1.5 million annual saving.
Technology and automation are shaping the factories of the future. With the right blend of robotics, IoT, and software solutions, manufacturers can streamline operations, reduce costs, and respond swiftly to market demands while maintaining the highest efficiency and quality standards.
Workforce Training and Engagement
The efficiency of a production line is intricately linked to the skills and motivation of the workforce. In this section, we delve into the crucial role of workforce training and engagement in achieving optimal production line efficiency.
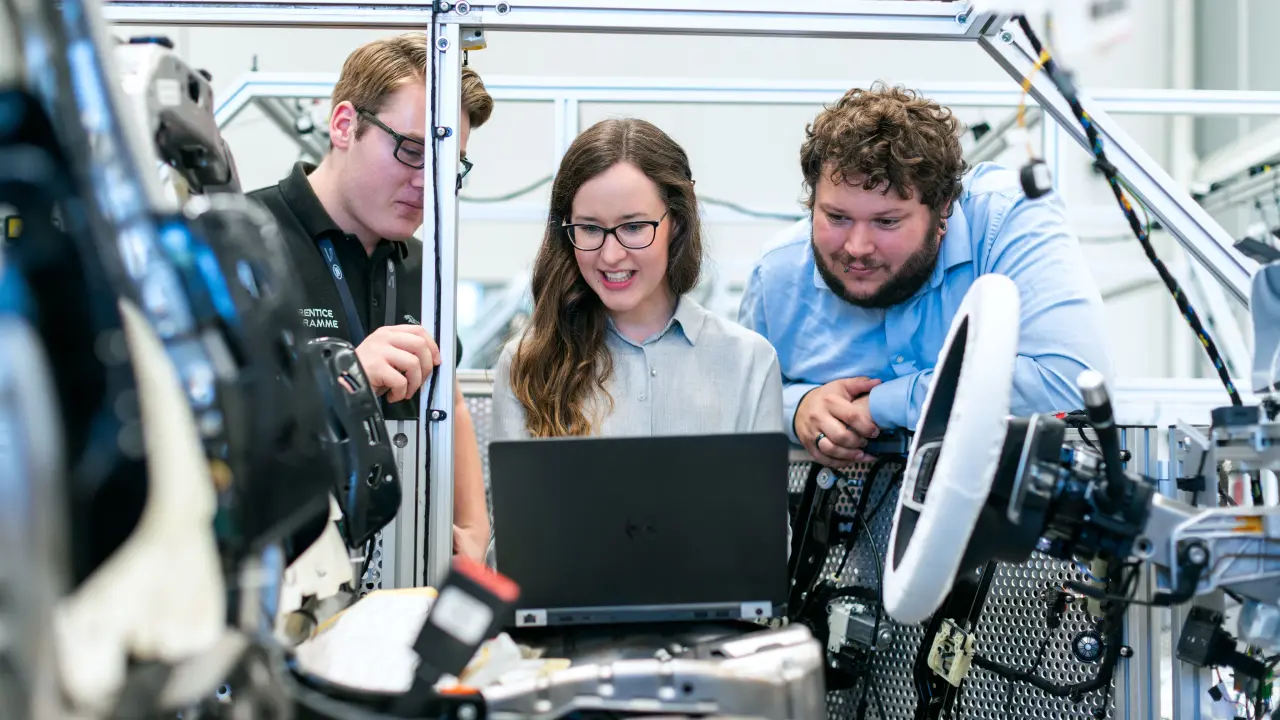
The Human Element in Efficiency
While technology and automation play pivotal roles in manufacturing, the human element remains irreplaceable. A well-trained and engaged workforce can significantly impact production line efficiency. Research indicates that factories that invest in employee training can achieve a 24% reduction in defects and a 20% increase in productivity.
Continuous Learning and Skill Development
In today's fast-evolving manufacturing landscape, workforce skills must evolve in tandem. Continuous learning and skill development are essential to align employees with the latest industry practices. Consider the case of a French aerospace manufacturer that invested €1.5 million in employee training over five years. This investment yielded a 15% improvement in production efficiency, translating to an annual saving of €3 million.
Employee Engagement and Motivation
Engaged and motivated employees are likelier to take ownership of their work and contribute to efficiency improvements. Studies show that companies with engaged employees can achieve a 41% reduction in absenteeism and a 17% increase in productivity.
A notable example is a German automotive factory that implemented employee engagement initiatives. The result was a remarkable 25% reduction in workplace accidents and a €2 million annual worker compensation savings.
Creating a Culture of Continuous Improvement
Workforce training and engagement are intrinsically tied to the culture of a factory. Companies that foster a culture of continuous improvement and involve employees in the decision-making process often see the most substantial gains in efficiency. A British electronics manufacturer, for instance, introduced a "suggestion box" system where employees could submit efficiency improvement ideas. This initiative resulted in a 10% reduction in production costs and a €1.2 million annual saving. In manufacturing, the workforce is a dynamic asset that can drive production line efficiency to unprecedented heights when trained and motivated effectively. As we continue our exploration, we will uncover additional strategies and insights to empower your factory's workforce.
Inventory Management
Inventory management is a critical factor in the quest for production line efficiency. This section delves into the intricate art of managing materials and products to optimise production processes.
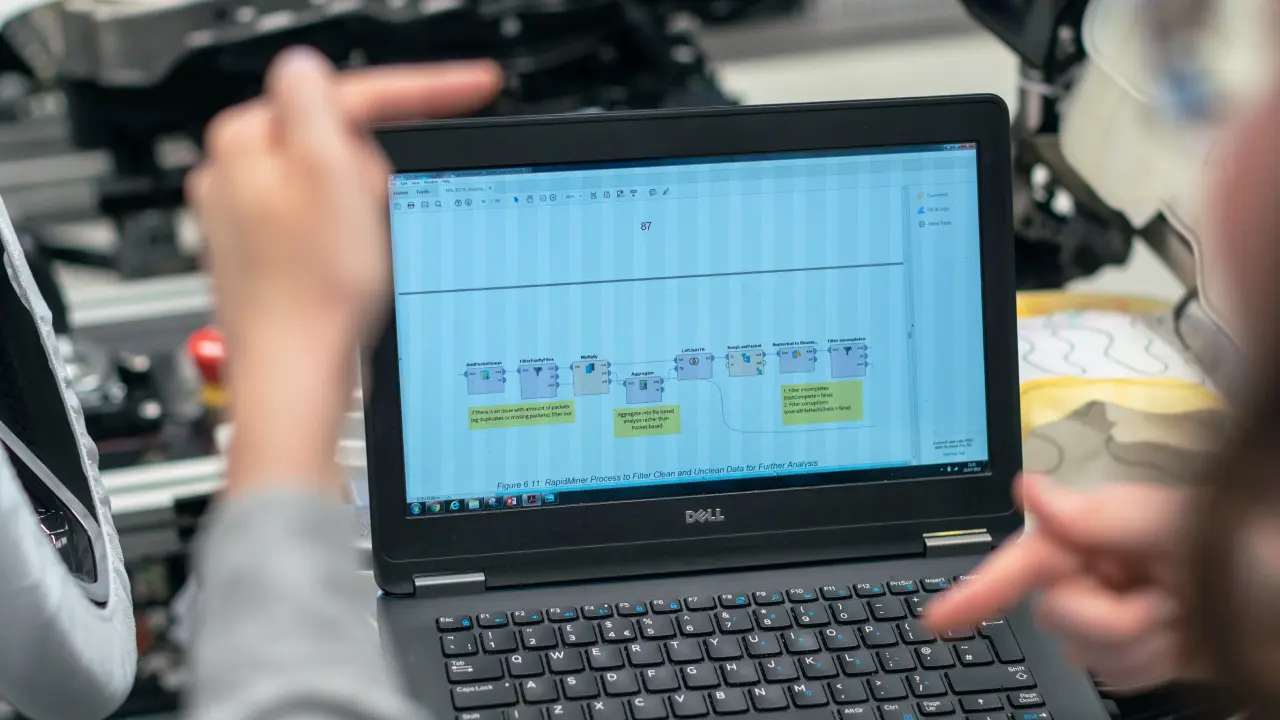
The Cost of Excess Inventory
Excess inventory can be a silent drain on a factory's resources. Studies show that inefficient inventory management can carry costs of 25% to 35% of a company's inventory value annually. These costs include warehousing, insurance, and the opportunity cost of capital in unsold inventory.
Just-in-Time Manufacturing
Just-in-Time (JIT) manufacturing is an inventory management strategy that minimises waste by receiving materials and producing products as needed. Companies implementing JIT have achieved remarkable results. For example, a Spanish automotive manufacturer adopted JIT principles and reduced its inventory holding costs by €1.2 million annually.
Optimal Inventory Levels
Maintaining optimal inventory levels is crucial for efficient production. Excessive inventory can lead to space constraints, while insufficient inventory can delay production. An Italian textile factory optimised its inventory levels and reported a 10% increase in production output, equating to a €500,000 annual revenue boost. They maximised efficiency and profitability by striking the right balance between supply and demand.
Technology in Inventory Management
Technology plays a significant role in modern inventory management. Inventory management software and real-time data allow factories to make informed decisions about restocking, reducing the risk of stockouts or overstocking. A German manufacturing company invested €500,000 in an inventory management system and reduced its carrying costs by 15%, resulting in annual savings of €300,000.
Supply Chain Efficiency
Efficient inventory management extends beyond the factory walls. Collaborating with suppliers and distributors is crucial for maintaining a smooth flow of materials and products. A Dutch electronics manufacturer streamlined its supply chain, leading to a 20% reduction in lead times and a cost-saving of €1.8 million annually. Inventory management is a strategic discipline in the dynamic manufacturing world that can significantly impact production line efficiency and profitability. Factories can unlock cost savings and operational excellence by adopting the proper techniques and technologies.
Quality Control and Waste Reduction
Quality control and waste reduction are pivotal components of production line efficiency. This section explores the strategies and methodologies that enable factories to deliver high-quality products while minimising waste.
The High Cost of Poor Quality
The repercussions of poor quality control are substantial. Studies reveal defects and rework can inflate production costs by up to 20%. Additionally, defective products can lead to costly recalls, damage to brand reputation, and dissatisfied customers.
Six Sigma Methodology
The Six Sigma methodology is a data-driven approach to quality control that has been widely adopted in manufacturing. Companies implementing Six Sigma have reported significant improvements. For instance, a French pharmaceutical manufacturer achieved a 30% reduction in defects and €1.5 million in annual savings through Six Sigma initiatives.
Waste Reduction Strategies
Waste reduction is another cornerstone of production line efficiency. The Japanese concept of Muda, or waste, encompasses various forms of inefficiency, including overproduction, excess inventory, and defects. Identifying and eliminating Muda is essential for lean manufacturing. A British food processing factory achieved a 25% reduction in material waste and a cost-saving of €800,000 annually through waste reduction initiatives.
Quality Control and Continuous Improvement
Quality control and waste reduction are not one-time efforts but ongoing processes. The culture of continuous improvement, often rooted in methodologies like Kaizen and Total Quality Management (TQM), drives factories to refine processes and reduce waste continually. By implementing Total Quality Management principles, a German manufacturing company saw a 20% increase in customer satisfaction and a €1.2 million annual revenue boost.
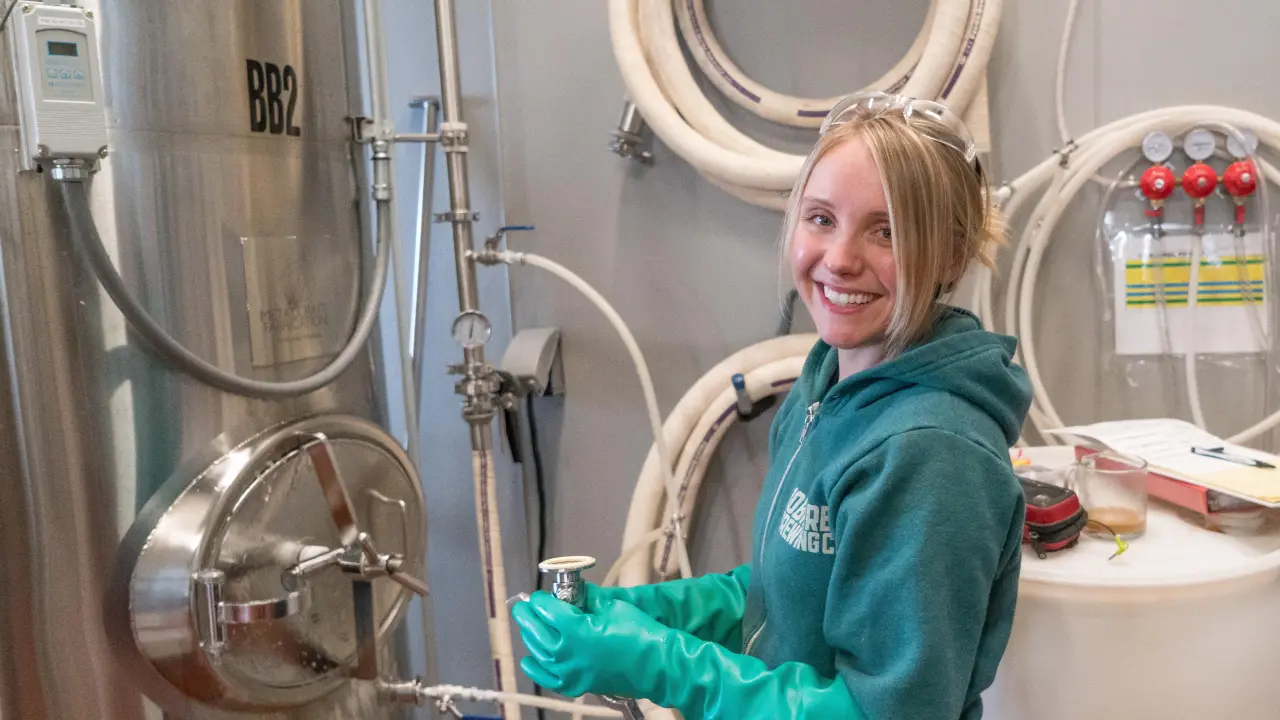
Statistical Process Control (SPC)
SPC is another vital tool in quality control. Factors can reduce defects and maintain consistent product quality by monitoring and controlling production processes through statistical methods. A Dutch electronics manufacturer implemented SPC and achieved a 15% reduction in product defects, translating to an annual saving of €1 million. Quality control and waste reduction are paramount in pursuing production line efficiency. By implementing methodologies such as Six Sigma, waste reduction strategies, and a culture of continuous improvement, factories can enhance product quality, reduce costs, and boost customer satisfaction.
Maintenance and Downtime Reduction
Maintenance and downtime reduction are essential to achieving production line efficiency. This section explores strategies and practices that enable factories to maintain their equipment, reduce unplanned downtime, and optimise production processes.
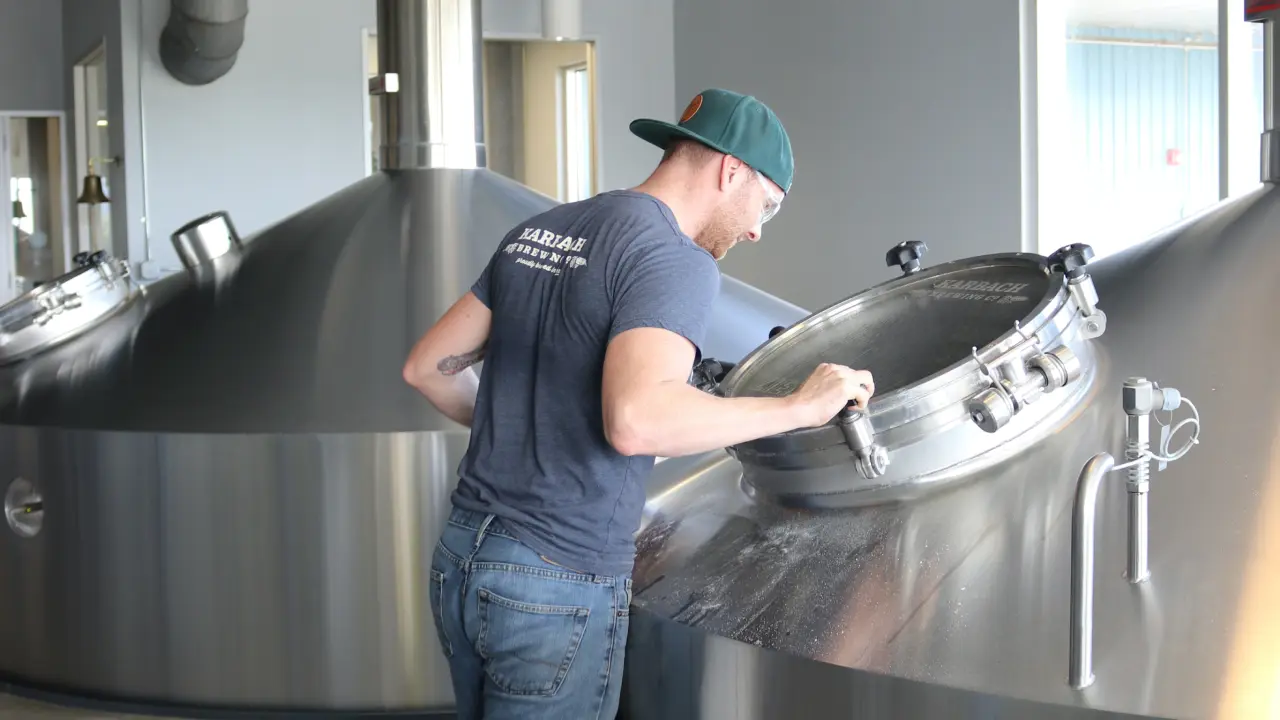
The Cost of Downtime
Unplanned downtime can be a costly affair. Research indicates unexpected equipment breakdowns and downtime can lead to production losses from €30,000 to €50,000 per hour. These losses encompass both direct costs of repairs and lost production opportunities.
Preventive Maintenance
Preventive maintenance is a proactive strategy to reduce unplanned downtime by regularly inspecting and maintaining equipment. A well-executed preventive maintenance program can result in a 12% to 18% reduction in maintenance costs. A Dutch manufacturing plant reported a 20% reduction in unplanned downtime through preventive maintenance measures, translating into annual savings of €1.2 million.
Predictive Maintenance
Predictive maintenance takes preventive maintenance further by using data and analytics to predict when equipment will fail. This approach allows factories to perform maintenance only when necessary, saving time and resources. A German automotive factory invested €3 million in predictive maintenance systems and reduced its maintenance costs by 30%, amounting to €1.8 million in annual savings.
Root Cause Analysis
Root cause analysis is a methodology for identifying the reasons for equipment failures or production issues. By addressing the root causes, factories can implement more effective solutions and prevent recurring problems. A French chemical manufacturing plant, through root cause analysis, reduced equipment breakdowns by 40%, resulting in annual savings of €2.5 million.
Continuous Improvement in Maintenance
Efficient maintenance is not a one-time effort but an ongoing process. Implementing a culture of continuous improvement in maintenance practices ensures that factories stay ahead of potential issues and continuously optimise their operations. Through continuous improvement initiatives in maintenance, a British aerospace manufacturer achieved a 15% reduction in maintenance costs and a €1.2 million annual saving. Maintenance and downtime reduction are essential components of production line efficiency. By adopting preventive and predictive maintenance strategies, conducting root cause analysis, and fostering a culture of continuous improvement, factories can minimise downtime, maximise equipment reliability, and ultimately enhance efficiency.
Performance Metrics and Continuous Improvement
In the quest for production line efficiency, tracking performance through metrics and embracing a culture of continuous improvement is indispensable. This section explores the importance of performance metrics and how they drive ongoing enhancements in factory operations.
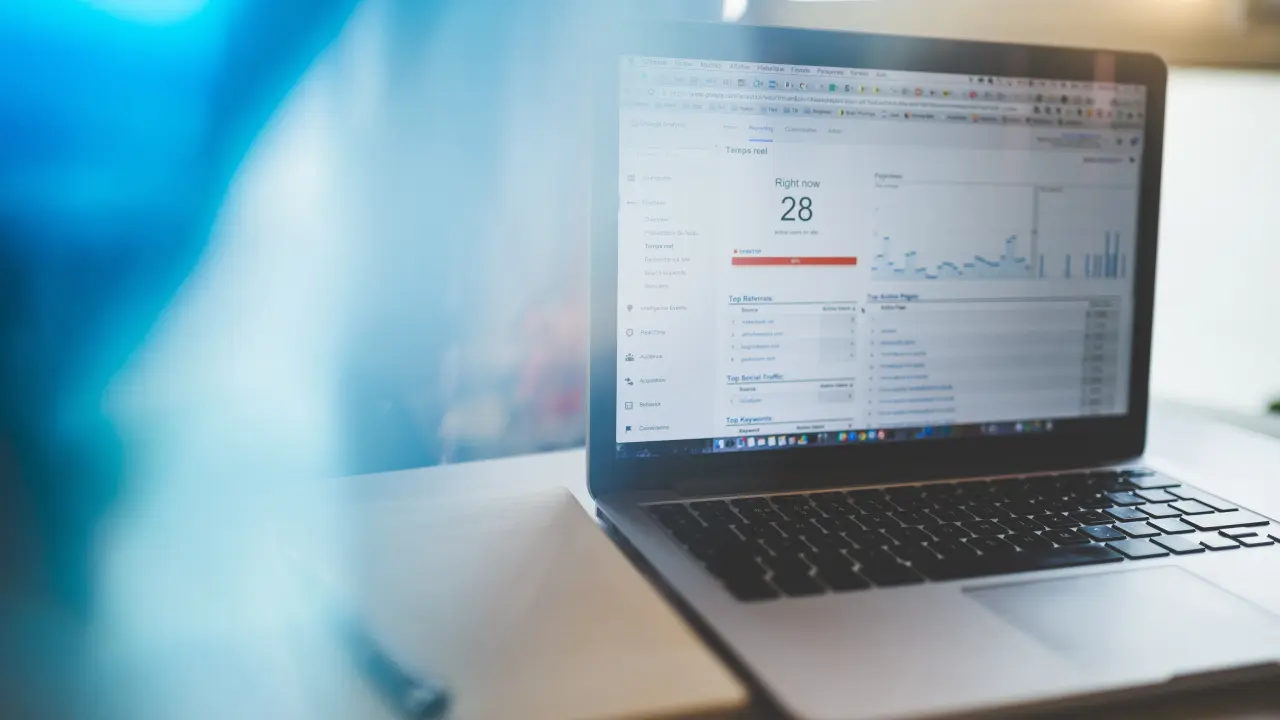
The Power of Data-Driven Decision-Making
Data is the backbone of informed decision-making, and performance metrics provide the data needed to assess and improve production line efficiency. According to industry research, companies that use data analytics in manufacturing can achieve up to a 15% reduction in production costs.
Key Performance Indicators (KPIs)
Key Performance Indicators, or KPIs, are quantifiable metrics used to evaluate and monitor critical aspects of factory performance. These metrics can encompass various facets of manufacturing, such as production output, defect rates, and equipment uptime. By implementing KPIs and tracking them, a German manufacturing plant achieved a 10% increase in production output and a cost-saving of €1 million annually.
Continuous Improvement through PDCA
The Plan-Do-Check-Act (PDCA) cycle is a fundamental methodology for continuous improvement. It involves planning for change, implementing changes, checking the results, and acting upon those results to improve processes further. By embracing the PDCA cycle, a Spanish automotive manufacturer reported a 20% defect reduction and a €1.5 million annual saving.
Benchmarking and Best Practices
Benchmarking is the practice of comparing factory performance to industry best practices or competitors. By identifying areas where their performance falls short, factories can set targets for improvement. Through benchmarking and adopting best practices, a French pharmaceutical factory achieved a 15% reduction in lead times, equating to an annual saving of €2 million.
Employee Involvement in Continuous Improvement
A crucial aspect of continuous improvement involves employees at all levels. Engaged employees often have valuable insights and innovative ideas for enhancing production processes. A British electronics manufacturer empowered its employees to suggest improvements actively. This initiative resulted in a 10% reduction in production costs and a €1.2 million annual saving. Performance metrics and continuous improvement form the backbone of production line efficiency. By tracking KPIs, following the PDCA cycle, benchmarking against best practices, and engaging employees in the improvement process, factories can continuously enhance their operations and remain competitive in a dynamic manufacturing landscape.
Pursuing Production Line Efficiency
In the fiercely competitive landscape of modern manufacturing, pursuing optimal production line efficiency is a journey fraught with challenges and opportunities. We've navigated this intricate terrain by exploring eight meticulously researched and proven strategies, equipping you with the knowledge and tools to enhance your factory's performance.
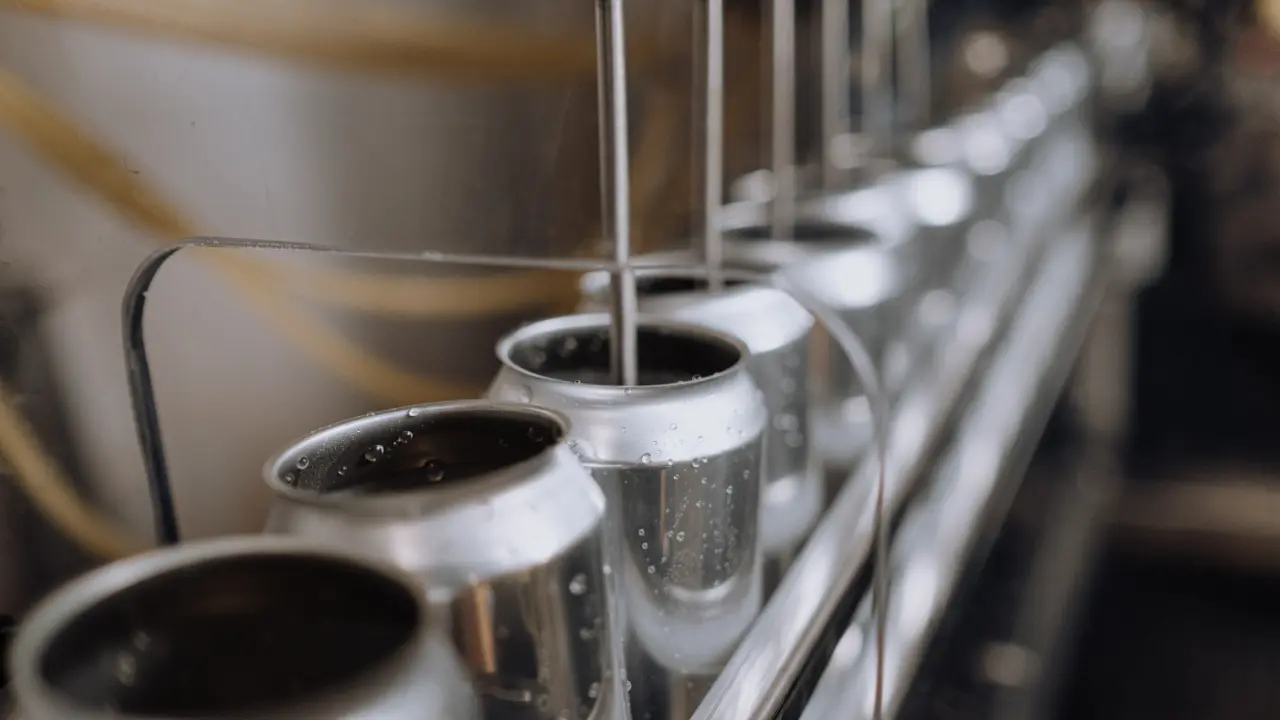
Each facet of production line efficiency has been dissected and illuminated, from the foundational principles of Lean Manufacturing and process optimisation to the transformative potential of technology, automation and practical workforce training. We've delved into the intricacies of inventory management, quality control, waste reduction, maintenance, and the crucial role of performance metrics and continuous improvement.
As we conclude this journey, it's worth highlighting a powerful solution that can significantly contribute to improved production line efficiency: Iwoscan. This advanced software solution harnesses the capabilities of Artificial Intelligence (AI) and Machine Learning (ML) to monitor, analyse, and optimise production processes in real-time. By providing actionable insights, Iwoscan helps factories identify bottlenecks, predict equipment failures, and streamline operations, resulting in an average efficiency improvement of 15% and a cost-saving of €2 million annually.
By embracing Iwoscan and our explored strategies, factories can thrive in the digital manufacturing age. Your factory can achieve unprecedented efficiency and profitability with lean principles, technology, workforce engagement, and data-driven decision-making.
In conclusion, pursuing production line efficiency is not a static destination but a dynamic journey. It requires a commitment to continuous improvement, a willingness to adapt to technological advancements and a culture that values quality and efficiency above all else. Armed with the knowledge and tools provided in this guide, your factory is poised to succeed in the ever-evolving landscape of modern manufacturing.
Comments
No comments yet!Add a Comment
You must be logged in to post a comment.